Головин С.А. Физика прочности и пластичности. Учеб. пособие. – Тула: Изд-во ТулГУ, 2006. - 192 с.
Nbsp;
Министерство образования и науки Российской Федерации
Федеральное государственное бюджетное образовательное учреждение высшего образования
«Тульский государственный университет»
Политехнический институт
Кафедра «Подъемно-транспортные машины и оборудование»
СБОРНИК МЕТОДИЧЕСКИХ УКАЗАНИЙ
К ЛАБОРАТОРНЫМ РАБОТАМ
по дисциплине
«КОНСТРУКЦИОННАЯ ПРОЧНОСТЬ»
Направление: 15.04.02 Технологические машины и оборудование
Программа: Подъемно-транспортные, строительные и дорожные машины»
Квалификация выпускника: магистр
Форма обучения: очная и заочная
Тула 2017
Методические указания к лабораторным работам составлена профессором В.С. Дроновым и обсуждена на заседании кафедры Подъемно-транспортные машины и оборудование факультета транспортных и технологических систем,
протокол № 1 от « 31 » 08 2015 г.
Зав. кафедрой В.Ю. Анцев
АННОТАЦИЯ
Лабораторные работы по дисциплине «Конструкционная прочность» имеют цель приобретения навыков проведения испытаний конструкционных материалов с определением характеристик их механических свойств при различных видах нагружения, обрабатывать и анализировать полученные результаты испытаний, а также научиться методам идентификации характера и причин разрушения по видам макроизломов образцов и натурных изделий.
|
|
Лабораторные работы носят экспериментально-исследовательский характер с получением технических показателей материалов максимально приближенных к используемым в технологических машинах.
Перечень лабораторных работ
стр | |
Введение. Дискретные модели твердых тел, физические и механические свойства материалов…………………………………………………… 1.Испытание на растяжение с определением характеристик механических свойств сталей……………………………………………………… 2. Испытание на растяжение с киносъемкой процесса локализованной текучести и разрушения в малоуглеродистой стали………………………. 3. Определение параметров изломов при хрупком, квазихрупком, вязком и усталостном разрушениях ……………………………………………… 4. Испытание на растяжение с построением диаграммы статического деформирования ……………………………………………………………... 5. Испытания на статическую трещиностойкость………………………….. 6. Определение вязкости разрушения при испытании на поперечный удар сталей разного уровня прочности в температурном интервале ……….. 7. Испытания на выносливость при многоцикловой усталости со статистическим представлением данных испытаний ………………………… | . 4 13 15 18 22 25 28 37 |
|
|
ВВЕДЕНИЕ
Дискретные модели твердых тел. Физические и механические свойства материалов
В разделе напряженное и деформированное состояние тела мы наделяли тела свойствами сплошности, однородности, изотропности и упругости – это оправдано, т.к. рассматриваются напряжения и деформации в сечениях и объемах соизмеримых с размером тела. Когда же рассматриваются процессы, связанные с пластической деформацией и разрушением, приходится обращаться к структурным составляющим деформируемого тела. Существует достаточно больное количество моделей описывающих поведение тела за пределом упругости на разных структурных уровнях: на макро-, мезо-, микро-, субмикро- и наноуровне.
В основе физического представления о прочности металлов является представление о кристаллическом их строении. Всем металлам свойствен определенный тип кристаллической решетки с определенным геометрическим расположением атомов и силам взаимодействия между ними. Наиболее часто встречаются следующие:
|
|
1) объемноцентрированная кубическая (ОЦК) – V, Cr, Feα, Nb, Mo, W и др.
2) гранецентрированная кубическая (ГЦК) – Аl, Ca, Feγ, Ni, Cu, Pb и др.
3) гексагональная плотноупакованная (ГПУ) – Be, Mg, Cd, Ti, Co, Zn, Zr и др.
Ряд металлов (Fe, Ti, Co и др.) в зависимости от температуры и давления может существовать в состояниях с различными решетками – это явление называется полиморфизмом.
Рассмотрим теперь, как осуществляется упругая и пластическая деформация (т. е. механизм упругой и пластической деформации).
Упругая деформация – есть изменение расстояния между атомами под действием внешних сил. Поэтому напряжение – есть изменение в межатомных расстояниях и может измеряться рентгеновскими методами. Очевидно, что если исключить причины, вызывающие смещение атомов, т. е. нагрузку, то они возвратятся на прежние места. Другими словами, упругая деформация не вызывает никаких последствий в материале. Чем меньшую деформацию вызывает напряжение, тем жестче материал. Следовательно, модуль упругости характеризует жесткость материала. Различают два вида модуля упругости: модуль нормальной упругости (модуль Юнга) и модуль касательной упругости (Гука). В первом случае силы стремятся оторвать атомы друг от друга, во втором — сдвинуть. Модуль Юнга (Е) в 2,5—3 раза больше модуля Гука (G). В частности, для железа Е = 2∙105 МПа, а G = 0,8∙105 МПа.
|
|
Значения модулей упругости определяются силами межатомного взаимодействия и являются константами материала. Например, модуль нормальной упругости для алюминия 0,8∙105 МПа, для железа 2∙105 МПа, молибдена 3∙10 5 МПа. Эта механическая характеристика структурно нечувствительна, т.е. термическая обработка и другие способы изменения структуры металла практически не изменяют модуля упругости. Вместе с тем повышение температуры, изменяющее межатомное расстояние снижает модуль упругости.
Пластическую деформацию кристалла можно осуществить сдвигом одной части кристалла относительно другой при этом напряжение по формуле Я.И. Френкеля (1920 г.) имеет вид
,
где G – модуль сдвига, a – межатомное расстояние в направлении скольжения, b – межплоскостное расстояние. Эта величина теоретической прочности примерно в 6 раз меньше G. К примеру, теоретический предел текучести железа равен 13000 МПа, тогда как в действительности он составляет 150 МПа, т.е. в 100 раз меньше. В чем заключается такая разница?
Структура реальных металлов существенным образом отличается от идеального кристалла нарушением геометрии кристаллической решетки различного рода дефектами. Такими дефектами являются: точечные дефекты – вакансия и межузельный атом, примесные атомы замещения и внедрения и др.; дефекты линейного типа – дислокации. Дефекты кристаллической решетки наследуются при производстве металлов (например, при кристаллизации из расплава) и при других технологиях. Чтобы понять роль дислокаций в проблеме прочности и деформации и влиянии их на свойствах металлов и сплавов, обратимся к количественной зависимости. Прочность металлов зависит от плотности дислокаций по сложному закону (рис. 1). Равновесная плотность дислокаций в отожженном металле (ρ = 106...108 см –2) соответствует минимальной прочности – σ0,2 = (10–5...10–4) G.
Рис 1. Зависимость прочности металлических материалов от плотности дефектов
Как объяснить низкую прочность (предел текучести σ0,2) реальных металлов. Рассмотрим деформирование кристалла, содержащего краевую дислокацию, при нагружении сдвигом. Краевая дислокация образуется при недостроенной кристаллографической плоскости (экстраплоскость)
![]() | ![]() | ![]() |
Рис. 2. Схема перемещения краевой дислокации
При наличии краевой дислокации сдвиг происходит в плоскости скольжения перпендикулярно линии дислокации. В результате сравнительно небольших перемещений атомов вблизи дислокации последняя под воздействием напряжения сдвига передвигается через решетку (рис. 2, а, б, в). При выходе дислокации на противоположную поверхность кристалла образуется единичная ступенька скольжения (рис. 2, в), а дислокация исчезает. Это составляет элементарный акт пластической деформации. Для перемещения дислокации методом последовательной смены когерентной связи между атомами требует значительно меньшего усилия.
Перемещение краевой дислокации похоже на перемещения ковра в результате перемещения складки (рис. 3). Длинную ковровую дорожку переместить за край бывает очень трудно, но достаточно сделать складку и перемещать эту складку – перемещение дорожки не требует больших усилий!
Рис. 3. Схема движения дислокации по аналогии с перемещением складки на ковре
При наличии нескольких параллельных плоскостей скольжения, образуется пачка полос с выходом на поверхность ступеньками и называется полосой скольжения. Такой эффект можно наблюдать, например, при растяжении образца с полированной поверхностью.
Кроме краевых дислокаций имеется другой тип – винтовая дислокация. Винтовую дислокацию отличает перемещение не в направлении сдвигающего усилия, как это осуществляется у краевой, а перемещение в перпендикулярном направлении (аналогия с антиплоским сдвигом). Дислокации не могут быть конечной длины, что противоречит кристаллическому строению, поэтому дислокация имеет очертание в виде петли, у которой части краевых и винтовых. Дислокации могут быть свободными, способными к перемещению и закрепленными.
В процессе пластической деформации, несмотря на то, что часть дислокаций выходит на поверхность, часть дислокаций противоположных знаков аннигилирует, рост плотности дислокаций растет, – это связано размножением их с ростом деформации (рис. 4).
Рис. 4. Схема генерации дислокационной петли плоским источником Франка-Рида
По механизму Франка-Рида источником дислокаций является отрезок дислокации закрепленный в точках D и D′, который под действием сдвигающих напряжений выгибается и, проходя все стадии (рис. 4, а, б, в, г, д) замыкается, образуя новую дислокацию. Такой процесс многократно повторяется. Существуют и другие механизмы генерации.
С ростом плотности дислокации при деформировании происходят реакции взаимодействия дислокаций между собой, с точечными дефектами внедрения (атмосферы Котрелла) и др. В результате происходит торможение дислокаций, скопления и оседание у препятствий, а для увеличения степени деформации требуется увеличение нагрузки.
Образование трещин. Предложены и нашли экспериментальное подтверждение различные схемы дислокационного зарождения трещин. Простейший пример – слияние нескольких краевых дислокаций в одну (сверхдислокация) образует ядро в виде зародыша клиновидной трещины. Для зарождения трещин необходима высокая локальная концентрация напряжений. Поэтому обычно трещины возникают у вершин скоплений дислокаций вблизи барьеров. Так, экстраплоскости головных краевых дислокаций в плоском скоплении у барьера могут оказаться под таким высоким давлением, что под ними образуется микротрещина (рис. 5, а).
Трещина может зародиться у барьеров при возникновении скоплений дислокаций в параллельных плоскостях скольжения (рис. 5, б). Для ОЦК-решеток не требуется наличия барьеров для дислокаций. В соответствии с правилами дислокационных реакций скольжение дислокаций <111> в пересекающихся плоскостях при их встрече дает новую а <001>с плоскостью скольжения (100). Такая дислокация представляет собой прочный барьер, тормозящий скольжение в пересекающихся плоскостях. Многократное повторение такой реакции приводит к слиянию дислокаций а<001> и, как следствие, к образованию зародышевой трещины (рис. 5, в).
Рис. 5. Схемы зарождения трещин у дислокационных скоплений
Предложена схема образования трещин внутри скоплений дислокаций при искривлении плоскостей их скольжения, что вызывает появление нормальных растягивающих напряжений (рис. 5, г). Модель реализуется после значительной пластической деформации. Для гексагональных структур возможна схема зарождения трещины в результате разрыва малоугловой границы при пластической деформации (рис. 5, д). Если в нижней части кристалла имеется барьер, а касательные напряжения значительные, то происходит разрыв дислокационной стенки (рис. 5, е). Концы стенки разойдутся, а возникающая при этом растягивающая деформация формирует трещину.
Наиболее выражен механизм зарождения коротких трещин при циклическом нагружении путем превращения тонких линий скольжения в устойчивые полосы с выступами (экструзия) и впадинами (интрузия) на поверхности металла.
При большом скоплении дислокаций у непреодолимых препятствий (включения, границы зерен и др.) зоны эти становятся не способными к пластическому деформированию и дальнейший рост напряжений ведет в этом месте к образованию микротрещин. Рост микротрещин, их объединение с последующим развитием представляет процесс разрушения, который заканчивается разделением материала на две части. Разрушение может быть хрупким или вязким.
Для хрупкого разрушения характерна острая, часто ветвящаяся трещина. Излом имеет ручьистый характер поверхности с плоскими фасетками скола (рис. 6, а). Энергия разрушения малая.
Для вязкого разрушения характерна тупая раскрывающаяся трещина с малой скоростью распространения и значительная пластическая деформация при ее продвижении. Излом имеет волокнистую поверхность с ямками и демплами (рис. 6, б). Энергия для вязкого разрушения имеет высокое значение.
Рис. 6. Схемы хрупкого – а и вязкого – б микроразрушений (сечение перпендикулярно
Поверхности излома
Методы управления прочностью и влияние условий нагружения на характеристики механических свойств
Анализ зависимости σ0,2(ρ) показывает, что повышение прочности металлов возможно либо путем снижения дефектности кристаллической решетки, либо, напротив, путем повышения плотности дефектов.
Применяют три основных метода упрочнения металлов – деформационное упрочнение, легирование и термическая, термомеханическая или химико-термическая обработки. Холодная пластическая деформация вызывает интенсивный рост плотности дислокаций (до 1011... 1012 см -2) и сопровождается деформационным упрочнением (наклепом), величина которого достигает (10–3... 10–2) G. Наклеп сохраняется при нагреве до температуры рекристаллизации.
Получаемые при легировании сплавы могут иметь однофазную, либо многофазную структуру. При образовании твердых растворов вокруг растворенных атомов происходит искажение кристаллической решетки. Возникающие упругие поля затрудняют перемещение дислокаций, в результате чего повышается предел прочности, предел текучести, твердость. При образовании твердых растворов внедрения искажения кристаллической решетки, а следовательно, и прочность существенно выше, чем для твердых растворов замещения. Твердорастворное упрочнение достигает величины σ0,2 = 10–3 G
Если легирование в сочетании с термической обработкой формируют в сплавах гетерофазную структуру, то упрочнение существенно возрастает. В сплавах с высокодисперсной структурой выделившиеся частицы избыточной фазы затрудняют перемещение дислокаций, что вызывает повышение прочности до 10–2 G (дисперсионное твердение). Степень упрочнения зависит от природы выделяющейся фазы. Чем более сложную кристаллическую решетку имеет фаза-упрочнитель, чем больше она отличается от решетки матричного твердого раствора, тем больше эффект упрочнения.
Детали машин, приборов, конструкций имеют самые разнообразные размеры, геометрию и условия работы, поэтому материалы, из которых они изготовлены, должны удовлетворять разным комплексам требований. Основным требованием, предъявляемым к конструкционным материалам, является конструкционная прочность, под которой подразумевают комплекс свойств, обеспечивающих надежное выполнение рабочих функций изделия в течение всего срока эксплуатации. Конструкционная прочность — это характеристика, сочетающая критерии прочности, надежности и долговечности. В соответствии с ГОСТ 27.002-89, надежность — это свойство изделия сохранять во времени и в установленных пределах значения всех параметров, характеризующих способность выполнять требуемые функции. Долговечность — свойство изделия сохранять работоспособность до предельного состояния.
Конструкционная прочность изделия и определяющие её критерии зависят от выбранного материала, конструктивных особенностей детали, технологии ее изготовления и обработки, и условий эксплуатации. Для сравнительно небольшого количества простых по форме изделий, работающих при статическом нагружении, характеристиками конструкционной прочности являются предел прочности (σв) и предел текучести (σт), характеризующие сопротивление материала развитию пластической деформации. Характеристиками пластичности служат относительное удлинение (δ) и относительное сужение (ψ). Для экспрессной оценки прочностных свойств в технике часто используют твердость, которая связана с прочностью. Для оценки прочности деталей, работающих при циклических нагрузках, используют предел выносливости ( ).
Для тяжелонагруженных высокопрочных изделий, деталей сложной формы, крупномасштабных конструкций конструкционная прочность определяется не столько критериями статической прочности, сколько критериями надежности. При эксплуатации таких изделий наиболее опасным является хрупкое разрушение, которое происходит при напряжениях меньше предела текучести, развивается внезапно и с большой скоростью и часто приводит к катастрофическим последствиям. Для оценки надежности недостаточно знания характеристик пластичности (δ и ψ); определяющими становятся такие характеристики, как ударная вязкость (КСU, КСV, КСТ) и вязкость разрушения (КIС). Коэффициент КIС связывает среднее приложенное напряжение σ с критической длиной трещины
где – форм-фактор, т.е. коэффициент, зависящий от геометрии трещины.
Вязкость разрушения определяется экспериментально на стандартных образцах с надрезом и наведенной трещиной, в условиях плоского деформированного состояния. Величина КIС характеризует сопротивление развитию вязкой трещины: чем больше значение К1С, тем выше надежность. Зная вязкость разрушения, можно определить максимальный безопасный размер трещины для действующих напряжений или, напротив, безопасный уровень действующих напряжений при известном размере дефекта. Общая закономерность для металлических материалов — при повышении предела текучести вязкость разрушения снижается.
Для оценки надежности необходимо знать температуру хрупко-вязкого перехода, называемую также температурным порогом хладноломкости. Это – температура, при которой вязкий механизм разрушения сменяется на хрупкий. В литературе она обозначается, как ТХили Т50. Температура ТХопределяется испытанием серии образцов на ударную вязкость при различных температурах. Температура, при которой в изломе образца 50 % площади приходится на вязкий излом, а 50 % — на хрупкий, и соответствует температуре хрупко-вязкого перехода. Чем ниже температура ТХотносительно температуры эксплуатации детали, тем выше так называемый запас вязкости и тем меньше вероятность хрупкого разрушения.
Долговечность изделий обеспечивается высокой износостойкостью, сопротивлением усталостным разрушениям. Если деталь работает при повышенных температурах или в агрессивной среде, то к критериям долговечности добавляются сопротивление ползучести или коррозионная стойкость.
Таким образом, понятие «конструкционная прочность» может быть наполнено разным содержанием для материалов разного назначения, а работоспособность различных изделий обеспечивается сочетанием нескольких разнообразных критериев конструкционной прочности.
Прочность конструкции в целом невозможно определить только по результатам испытания образцов. Эксплуатация и разрушение реальных деталей могут происходить в более сложных условиях, чем те, в которых испытывается стандартный образец. Вид напряженного состояния, форма детали, наличие концентраторов, предшествующие технологические воздействия — все эти факторы влияют на конструкционную прочность изделия. Поэтому для оценки прочности конструкции в целом необходимо проведение стендовых, натурных или эксплуатационных испытаний.
Конструкционные материалы должны также иметь хорошие технологические свойства: обрабатываемость резанием, давлением, свариваемость, литейные свойства и др. Не менее важным является экономический фактор, определяемый стоимостью самого материала и технологии его обработки для получения необходимого комплекса свойств.
Если легирование в сочетании с термической обработкой формируют в сплавах гетерофазную структуру, то упрочнение существенно возрастает. В сплавах с высокодисперсной структурой выделившиеся частицы избыточной фазы затрудняют перемещение дислокаций, что вызывает повышение прочности до 10–2 G (дисперсионное твердение). Степень упрочнения зависит от природы выделяющейся фазы. Чем более сложную кристаллическую решетку имеет фаза-упрочнитель, чем больше она отличается от решетки матричного твердого раствора, тем больше эффект упрочнения. Деформационное, твердорастворное упрочнение и дисперсионное твердение сопровождаются снижением пластичности и повышением температуры хрупко-вязкого перехода. В металлических материалах только зернограничное упрочнение не вызывает охрупчивания.
Границы между зернами и блоками являются непреодолимыми препятствиями для дислокаций. Поэтому чем мельче зерно и больше площадь межфазных границ, тем выше прочность сплава. Эта закономерность описывается уравнением Холла–Петча:
где – напряжение, необходимое для перемещения дислокации в решетке; k – константа материала; d – размер зерна.
Рис. 8. Зависимость напряжения течения, напряжения разрушения при растяжении и деформации до разрушения железа от размера зерна. Переход от хрупкого разрушения к вязкому наблюдается при размере зepнa, соответствующем : 1 - напряжение разрушения; 2 - напряжение течения; 3 - деформация до разрушения ( - 195° С)
Рис. 9. Критическая температура в зависимости от размера зерна стали с 0,11% С [6]. Критическая температура линейно зависит от ln d -1/2и уменьшается
С измельчением зерна
Между тем основным критерием, по которому можно судить о применимости какого-либо нового способа повышения прочности, является величина одновременного повышения прочности и вязкости. Так как общее диспергирование структуры дает возможность достижения такого результата, то вклад величины зерна в прочность представляет особый интерес. В общем случае при увеличении прочности происходит уменьшение ударной вязкости. По-видимому, для получения высокопрочного состояния нужно искать какой-то компромиссный путь. Согласно одной из оценок, «полезная» прочность конструкционных материалов, вероятно, не будет превышать 350 кгс/мм2. Даже этот уровень прочности можно считать полезным лишь в том случае, если могут быть допущены большие упругие деформации при эксплуатации изделия из такой стали. Однако нагружение до таких высоких напряжений приводит к большому запасу упругой энергии, что определяет возможности нестабильного роста трещины. Дилемма прочность—вязкость может быть рассмотрена и с энергетических позиций: с повышением запасенной упругой энергии должна быстро увеличиваться и энергия, необходимая для распространения трещины, при условии, что существующие в металле микротрещины остаются стабильными.
При переходе из одного зерна в другое трещина часто меняет направление, разветвляется и теряет энергию. Следовательно, чем мельче зерно, тем менее вероятно развитие хрупкого разрушения, тем ниже ТX.
Большое значение для обеспечения надежной работы деталей имеет чистота металла. Повышение чистоты стали, например, по сере, фосфору, кислороду приводит к существенному снижению температуры хрупко-вязкого перехода и увеличению вязкости разрушения.
Многие детали машин работают на изгиб и кручение, когда максимальные напряжения возникают в поверхностных слоях, где часто располагаются концентраторы напряжений в виде подрезов, рисок, переходных сечений и т.д. При циклическом нагружении образование усталостной трещины происходит, как правило, на поверхности детали под действием растягивающих напряжений. Если создать на поверхности напряжения сжатия, то предел выносливости резко увеличивается и вместе с тем снижается чувствительность к концентраторам напряжений.
В настоящее время проблема формирования требуемых свойств поверхности выделяется в самостоятельную область — инженерию поверхности. В технике используют многочисленные методы поверхностной обработки, позволяющие целенаправленно создавать структуру поверхностных слоев. Улучшить качество поверхности и создать на поверхности слой с напряжениями сжатия можно механическими методами – полированием, алмазным выглаживанием, пластической деформацией поверхностных слоев путем обдувки дробью, обкатки роликами. При этом повышается прочность и предел выносливости.
Поверхностная закалка приводит к образованию в поверхностных слоях структуры мартенсита, удельный объем которого больше, чем ферритно-цементитной смеси, благодаря чему на поверхности формируются напряжения сжатия. Химико-термическая обработка (цементация, азотирование, нитроцементация, диффузионная металлизация), приводящая к изменению состава поверхностных слоев, также может формировать в них напряжения сжатия.
Влияние примесей. Наиболее распространенным конструкционным материалом являются углеродистые стали. Хотя основные компоненты этих сталей — железо и углерод, они являются многокомпонентными системами. Кроме железа и углерода, в стали всегда есть примеси, которые подразделяются на постоянные и скрытые. Постоянные примеси в стали — это кремний и марганец, сера и фосфор. Их присутствие обусловлено технологическими особенностями выплавки стали. Скрытыми примесями являются растворяющиеся в жидком металле газы — кислород, водород, азот.
Кремний и марганец добавляют для раскисления стали, и их количество определяется степенью раскисления. Они не ухудшают свойств стали, а, напротив, считаются полезными в определенных количествах. Конструкционные стали содержат кремния < 0,37 %, марганца — < 0,8 %, если эти элементы не вводятся в состав стали в качестве легирующих. Кремний и марганец растворяются в феррите, несколько упрочняя его, однако, при этом ухудшается обрабатываемость резанием. Кремний при раскислении образует силикаты SiO2 — неметаллические включения, которые всегда присутствуют в некотором количестве в промышленных сталях. Кремний в количестве более 0,6 % значительно снижает пластичность стали.
Сера и фосфор относятся к вредным примесям. Сера, образуя с железом легкоплавкий (988 °С) сульфид железа FеS, вызывает красноломкость стали. Если в стали содержится марганец, то благодаря большему его сродству к сере, чем у железа, вместо сульфида железа образуется более тугоплавкий сульфид марганца (1620 °С), что приводит к устранению красноломкости. Наличие сульфидов мало влияет на прочность стали, но достаточно существенно — на вязкость, пластичность и предел выносливости. Работа зарождения трещины не зависит от содержания серы, а вязкость разрушения с увеличением содержания серы резко снижается (рис. ).
Сульфиды пластичны и легко деформируются, например, при прокатке. В результате возникает анизотропия свойств, которая особенно выражена в сталях, сильно загрязненных серой. Кроме того, сера ухудшает свариваемость и коррозионную стойкость. Содержание серы в зависимости от качества стали не должно превышать 0,035...0,06 %.
Фосфор, растворяясь в феррите в очень небольших количествах, значительно влияет на его свойства. При увеличении содержания фосфора уменьшаются пластичность и вязкость феррита и резко повышается температура хрупко-вязкого перехода (рис.). Каждая сотая доля процента фосфора повышает Тх на 20...25°С.
Кроме того, фосфор чрезвычайно склонен к ликвациям, из-за чего даже при очень небольшом содержании фосфора возможно образование фосфидной эвтектики, ухудшающей свойства стали. Фосфор является также причиной развития обратимой отпускной хрупкости. Поэтому содержание фосфора в сталях, в зависимости от качества стали допускается не более 0,025...0,045%.
![]() |
![]() |
Рис. 10. Влияние серы на характеристики вязкости стали | Рис. 11. Влияние фосфора на тепературу вязко-хрупкого перехода |
Кислород, азот, водород всегда присутствуют в сталях в виде твердых растворов в железе, в виде молекул газов в дефектных участках металла или в виде оксидов, нитридов, гидридов. Наибольшую опасность представляет водород, атомы которого из-за резкого уменьшения растворимости водорода в железе при переходе γ-Fе в α-Fе имеют тенденцию скапливаться в дефектных местах стали и образовывать молекулы газа, что сопровождается резким увеличением объема, вызывающим локальное растрескивание металла и образование внутренних надрывов — флокенов. Водородная хрупкость более выражена в высокопрочном структурном состоянии, в связи с чем чувствительность к образованию флокенов возрастает с увеличением содержания углерода, особенно более 0,6 %. Вследствие чрезвычайно высокой диффузионной подвижности водорода его содержание в стали может возрасти в процессе эксплуатации в водородсодержащих средах и в ходе выполнения технологических операций, например, при травлении или при нанесении гальванических покрытий. Существенное снижение содержания водорода в стали достигается вакуумной плавкой или разливкой в вакууме.
Оксиды и нитриды относятся к неметаллическим включениям. Оксиды — хрупкие включения, которые в литых сталях имеют глобулярную форму, а после пластической деформации разрушаются с образованием строчек, состоящих из обломков первичных оксидов. При любой морфологии оксиды снижают пластичность стали и являются концентраторами напряжений, а строчечное расположение оксидов вызывает также анизотропию свойств, в особенности, ударной вязкости.
БИБЛИОГРАФИЧЕСКИЙ СПИСОК
Головин С.А. Физика прочности и пластичности. Учеб. пособие. – Тула: Изд-во ТулГУ, 2006. - 192 с.
Дата добавления: 2018-05-12; просмотров: 596; Мы поможем в написании вашей работы! |
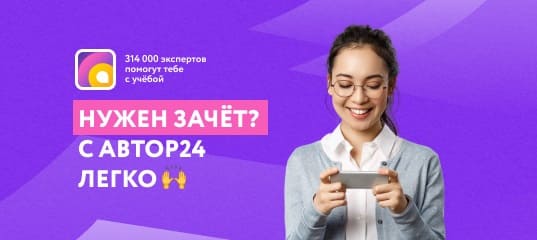
Мы поможем в написании ваших работ!