Расчет винта на устойчивость.
Задача 6.1 Рассчитать винтовой съемник для демонтажа подшипников качения с диаметром внутреннего кольца dв = 70мм; Dподш = 180мм. (рис. 6.1).
![]() |
Наибольшее усилие, необходимое для демонтажа
подшипника, Q = 65 кН. В демонтаже участвуют
двое рабочих, Fраб ≈ 350 Н. Коэффициент трения
между винтом и траверсой (сталь по стали)
f = 0,1…0,15.
В результате расчета определить:
размеры резьбы винта;
высоту гайки Н;
длину рукоятки lрук ;
диаметр траверсы dтр .
Решение.
1.1. Резьба винта трапецеидальная. Средний диаметр резьбы
≥
=
= 43,6мм ( табл. 2.36). [ 5]
= 1,2…2,5; [p]изн = 8…13МПа.
Средний диаметр d2 = 44, шаг резьбы р = 12мм, наружный диаметр d =50мм, внутренний диаметр d1 = 37мм ( табл. 2.36). [5]
1.2.Высота гайки
мм.
Число витков
zВ = z = 8.
1.3.Угол подъема резьбы
1.4. Коэффициент трения f = 0,14; угол трения j = arctg f = arctg 0,14 = .
|
|
1.5. Момент трения в резьбе
Трез = Н ⋅ мм,
1.6. Момент торцевого трения
Н ⋅ мм,
(внутренний диаметр подшипника равен 70 мм по условиям задачи).
1.7. Длина рукоятки
мм на 2-х рабочих.
![]() |
1.8 Диаметр траверсы определяем из условия прочности на изгиб, считая траверсу двухопорной балкой, нагруженной силой Q = 65 кН, длину траверсы принимаем равной наружной диаметру подшипника. D = 180мм (рис. 6.2).
Опорные реакции
|

Изгибающий момент в середине длины траверсы
Условие прочности при изгибе
σи = ≤ [σ]и ;
≤ [σ]и .
|
|
[σ]и = 100…160 МПа – для среднеуглеродистых сталей.
[σ]и = 140 МПа – для стали 35. Допускаемое напряжение [σ]и ориентировочно принято для детали ( в данном примере – траверсы), работающей по отнулевому циклу.
Из условия прочности:
≥
=
dтр = 60мм.
Расчет на прочность сварных соединений.
Основным критерием работоспособности швов сварных соединений является прочность.
Исходным условием проектирования соединений является равнопрочность шва и соединяемых деталей.
Стыковые соединения
Расчет производят по напряжениям растяжения или сжатия по площади А поперечного сечения соединяемых деталей.
Условие прочности:
|
где F— сила, действующая в соединении, Н;
δ — толщина шва (принимается равной толщине детали), мм; lш— длина шва, мм;
σр — расчетное напряжение для шва, МПа; [σ']р — допускаемое напряжение для шва (табл. 7.1), МПа.
|
|
При статической нагрузке допускаемые напряжения для сварных швов определяют как часть от [σ]р на растяжение основного металла:
[σ]р = ,
где σт – предел текучести основного металла, МПа; [Sт] – допускаемый коэффициент запаса прочности; [Sт] = 1,35…1,6 – для низкоуглеродистой стали.
Отношение [σ'] к допускаемому напряжению основного металла детали [σ] является коэффициентом прочности сварного соединения.
= 0,9...1,0 – значение напряжений (табл.7.1)
Таблица 7.1.
Допускаемые напряжения в швах.
Вид технологического процесса сварки | Допускаемые напряжения в швах при
| ||||
растяжении [σ']р | сжатии [σ']сж | срезе [τ'] | |||
Автоматическая под флюсом, ручная электродами Э42А и Э50А, контактная стыковая. | [σ]р | [σ]р | 0,65[σ]р | ||
Ручная дуговая электродами Э42 и Э50, газовая сварка. | 0,9 [σ]р | [σ]р | 0,6[σ]р | ||
Контактная точечная и шовная | - | - | 0,5[σ]р |
|
В тех случаях, когда требуется повысить прочность соединения, применяют косые швы. Расчет косого шва выполняют по формуле, в которой [σ'] = [σ]р (рис. 7.1).
|
Значения предела текучести в зависимости от свариваемого материала (или от основного металла) – (табл. 3)
Таблица 3 Значения механических характеристик для некоторых марок сталей |
Марка стали | Предел прочности σр , МПа | Предел текучести σт , МПа | Предел выносливости σ-1р , МПа | Марка стали | Предел прочности σр , МПа | Предел текучести σт , МПа | Предел выносливости σ-1р , МПа |
Ст3 и10 20 35 45 | 340 400 500 600 | 200 240 300 360 | 160 170 180 240 | 30Х 30ХГСА ВТ16 | 800 1000 1200 | 640 900 - | 280 300 350 |
Стыковую сварку применяют не только как способ соединения деталей, но и как технологический способ изготовления самих деталей.
Нахлесточные соединения угловыми швами (рис.7.2). Угловые швы рассчитывают на срез по опасному сечению т—т, совпадающему с биссектрисой прямого угла. Расчетная высота опасного сечения
h = 0,7K — для ручной сварки (сечение т—т); h = К — для автоматической.
![]() |
Условие прочности шва на срез: τср = F/A = F/h ⋅ lш ≤ [τ']ср ,
где τср и [τ']ср – расчетное и допускаемое напряжение среза для шва, МПа (табл. 7.1)
Lш – расчетная длина шва, мм
В соединении лобовыми швами lш = 2lл , фланговыми – lш = 2lфл .
В комбинированном шве lш = lл + lфл
Задача 7.1. Длины лобовых швов, соединяющих листы (рис. 7.3) ; b = 100 мм. Листы из СтЗ. Толщина листов δ = 8. Нагрузка F = 10 кН. Сварка ручная дуговая Э50А. Проверить прочность шва.
![]() |
Решение.
1.1. Определить допускаемое напряжение листа из Ст3:
[σ]р = =
= 140 МПа.
Допускаемое напряжение шва при срезе
[τ']ср = 0,65 ⋅[σ]р (табл. 7.1).
[τ']ср = 0,65 ⋅ 140 = 91 МПа.
1.2. Определить напряжение среза лобового шва из условия прочности на срез:
τср
h = 0,7K;
|
τср= |
биссектриса h шва равна 0,7К (рис. 7.3), К = δ = 8мм;
Условие прочности выполняется.
1.8.8 Расчет болтового соединения.
Опыт эксплуатации машин, аппаратов показал, что отказы соединений обычно происходят из-за разрушения резьбовых изделий и разгерметизации стыков. Как правило происходит поломка болтов и шпилек по резьбовой части. Реже встречаются поломки болтов под головкой и срез резьбы в гайке. Рассмотрим некоторые случаи нагружения болтов (винтов).
![]() |
|
|
1. Стержень винта нагружен только внешней растягивающей силой F. (рис. 8.1)
Опасным является сечение резьбы по диаметру d1 – внутренний диаметр резьбы.
Условие прочности при растяжении:
≤
; d1 ≥
(мм);
F - H; [σ]р – МПа.
Расчетный диаметр d1 – согласовать со стандартом и записать найденный номинальный диаметр резьбы.
2. Болт затянут, внешняя нагрузка отсутствует (крепление крышек корпусов редукторов, крепление герметичных крышек). Болт затягивается осевой силой F0 и закручивается моментом сил трения в резьбе (рис. 8.2).
![]() |
Напряжение растяжения от силы Fзат :
σp = 4Fзат. / πd2расч. ,
где dрасч. = d – 0,94p;
d и p – наружный диаметр резьбы и шаг резьбы.
Fзат. на практике определяют:
Fзат. = Кзат. F, где F – внешняя нагрузка на один болт;
Кзат. - коэффициент затяжки по условию нераскрытия стыка.
При постоянной нагрузке Кзат. = 1,25…2.
При переменной нагрузке Кзат. = 2,5…4.
При металлической фасонной прокладке Кзат. = 2…3.
При металлической плоской прокладке Кзат. = 3…5.
Напряжение кручения от трения в резьбе
τкр = .
где - угол подъема резьбы;
- приведенный угол трения.
Эквивалентное напряжение по теории энергии формоизменения
≤ [σ] .
Подставляя выражение σp и τкр в формулу σэкв и принимая для стандартных болтов с метрической резьбой ,
и f = 0,15; чему соответствует
,
получим: σэкв ≈ 1,3 σp .
Итак, расчет болта на совместное действие растяжения и кручения можно заменить расчетом на растяжение, т. е. Fрасч = 1,3F0. Расчетный диаметр болта:
≤ [σ]p , следовательно dрасч ≥
, где [σ]p - см. гл. I, п. 5.5. [5]
dpасч согласовать с ГОСТ 9150-81 по табл. 1.12. [5]
3. Болтовые соединения, нагруженные поперечной силой Q.
Болт поставлен в отверстие с зазором (рис. 8.3, а) и затянут так, чтобы сила трения возникающая между поверхностями соприкасающихся деталей, обеспечила нормальную работу соединения без смещения деталей. Расчет болта ведут по силе затяжки:
где К = 1,4…2 – коэффициент запаса по сдвигу деталей,
при статической нагрузке К = 1,3…1,5,
при переменной нагрузке К = 1,8…2;
f – коэффициент трениядля стальных и чугунных поверхностей
f = 0,15…0,2;
i - число стыков (на рис. 8.3, а i = 1; на рис. 8.3, в i = 2);
z – число болтов;
расчетный диаметр резьбы болта определяется по формулам, приведенным в гл. I, п. 5.8; [5].
[σ]p - в гл. I, п. 5.7. [5].
Болт поставлен в отверстие из-под развертки без зазора. (рис. 8.3, б).
Расчет ведется на срез по диаметру стержня d0 .
≤ [τ]ср - условие прочности,
где i = 1…2 - число плоскостей среза (на рис. 8.3, б i = 1; на рис. 8.3, в i = 2);
|
![]() |
79
z — число болтов;
[τ]ср — допускаемое напряжение на срез стержня болта, [τ]ср = (0,2...0,3)σт ; σт — табл. 1.14. [5]
Проектировочный расчет таких болтов ведется и на смятие по условию прочности:
|
где δ — толщина более тонкой детали;
[σ]см = (0,8...1,0) σт — для углеродистой стали;
[σ]см = (0,6...0,8) σт — для легированной стали ( табл. 1.14). [5]
Определить диаметр стержня болта из условия прочности на смятие:
|
Из двух полученных значений d0 принимают большее (табл. 1.16): [5.]
d0 = d + (1...2) мм,
где d — номинальный диаметр резьбы болта.
Задача 8.1. Подобрать болты для соединения стальных планок по данным:
F = 5,5 кН - растягивающая сила планки 1,3 и 2 (рис.8.4.);
z = 2 - число болтов. Материал болтов СтЗ;
f = 0,17 - коэффициент трения на стыке деталей;
класс прочности - 3,6, затяжка неконтролируемая.
Решение.
![]() |
1.1.Болт поставлен с зазором, расчет ведется из условия прочности на растяжение с кручением. По табл. 1.14 [5] для СтЗ находим предел текучести σт = 200 МПа, по табл. 1.15 [5] находим [s]T = 4.
|
1.2.Определение силы затяжки при условии отсутствия сдвига деталей
F ≤ Ff i = F0 f i,
где Ff - сила трения; i = 2 – число стыков, отсюда
;
учитывая коэффициент запаса по сдвигу, получим
где z - число болтов, К = 1,7, тогда
1.3.Условие прочности по эквивалентным напряжениям
≤
,
отсюда .
По ГОСТ 9150 – 81 (табл. 1.12) [5] : d1 = 23,319мм, номинальный диаметр М 27, шаг резьбы р = 3мм;
Примечание. М 27 – не рекомендуется. Примем М 30, р = 3,5мм.
Дата добавления: 2018-05-12; просмотров: 752; Мы поможем в написании вашей работы! |
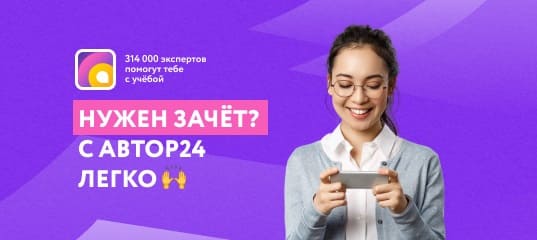
Мы поможем в написании ваших работ!