Требования к масловлагоотделителям, запорной и регулирующей арматуре
173. Каждый компрессор должен быть снабжен масловлагоотделителем, установленным на нагнетательном трубопроводе между компрессором и воздухосборником, газосборником, по возможности ближе к компрессору (концевому холодильнику). Допускается исполнение масловлагоотделителя и концевого холодильника в одном агрегате.
174. Масловлагоотделители должны быть оборудованы дренажным устройством для отвода отработанного масла и конденсата в сборники, исключающие загрязнение помещения компрессорной станции, окружающей среды, а также устройствами для автоматической и ручной продувки.
175. При отсутствии автоматической продувки ручная продувка масловлагоотделителей должна производиться два раза в смену, если руководством по эксплуатации изготовителя или технологическим регламентом не предусмотрен более короткий период продувки.
176. На нагнетательном трубопроводе (от концевого холодильника до воздухосборника, газосборника) должны быть установлены: манометр, термометр, предохранительный и обратный клапаны, отключающая арматура (задвижки, вентили) и дренажное устройство.
177. Для разгрузки электродвигателя при запуске компрессора на нагнетательном трубопроводе до обратного клапана должно быть установлено индивидуальное ответвление с запорной арматурой для сброса давления или предусматривается другое устройство.
178. Арматура, устанавливаемая на нагнетательном трубопроводе, должна быть смонтирована с учетом безопасного обслуживания и ремонта.
179. Вентили, задвижки, краны и клапаны должны быть смонтированы с учетом обеспечения возможности быстрого включения их в работу и отключения.
180. Арматура должна быть пронумерована, маховики плотно закреплены на шпинделях. На вентили (задвижки) и приводы к ним наносятся надписи:
1) номер или условное обозначение запорного или регулирующего устройства, соответствующие эксплуатационным схемам, исполнительная технологическая схема трубопроводов сжатого газа, охлаждающей воды, компрессорного масла;
2) указатель направления вращения в сторону закрытия «з» и в сторону открытия «о».
181. Надписи на арматуре и приводах располагаются следующим образом:
1) при расположении штурвала (маховика) вблизи корпуса вентиля (задвижки) – на корпусе или изоляции вентиля (задвижки) или на прикрепленной табличке;
2) при дистанционном управлении при помощи штурвала (маховика) – на колонке или кронштейне штурвала;
3) при дистанционном управлении с помощью цепи – на табличке, неподвижно соединенной с кронштейном цепного колеса и закрепленной в положении, обеспечивающем наилучшую видимость с площадки управления;
4) при дистанционном управлении вентилем или задвижкой (конец вала утоплен в полу и закрыт крышкой) – на крышке с внутренней и внешней стороны;
5) при дистанционном управлении с помощью электропривода – у кнопок управления;
6) при дистанционном управлении, кроме надписей, предусмотренных подпунктами 2), 3), 4), 5) настоящего пункта, наносятся надписи на маховики управляемой арматуры.
182. Арматура, устанавливаемая на компрессоре, сосудах и нагнетательных трубопроводах должна обозначаться маркировкой на корпусе, в которой указывается:
1) наименование или товарный знак изготовителя;
2) условный проход;
3) условное давление и температура среды;
4) направление потока среды (стрелка);
5) марка материала.
183. Выбор количества и мест установки арматуры, контрольно-измерительных приборов и предохранительных устройств определяется проектной организацией, исходя из обеспечения условий эксплуатации компрессорной установки.
184. Трубопроводы, сосуды и аппараты с температурой поверхности выше +45оС, располагаемые на рабочих местах и в местах основных проходов, должны иметь тепловую изоляцию. Стенки цилиндров компрессора изоляции не подлежат.
|
|
|
|
Требования к воздухосборникам и газосборникам
|
|
185. Для сглаживания пульсации давления сжатого газа в компрессорной установке должны предусматриваться воздухосборники или газосборники (буферные емкости).
186. Изготовление сосудов, работающих под давлением (воздухосборников) производится в соответствии с требованиями технического регламента Таможенного союза от 2 июля 2013 года № 41 «О безопасности оборудования, работающего под избыточным давлением».
187. Объем воздухосборников, газосборников воздушных компрессоров общего назначения определяется изготовителем или проектом компрессорной станции.
188. Воздухосборник или газосборник должен устанавливаться на фундамент вне здания компрессорной станции и должен быть огражден.
189. Расстояние между воздухосборниками или газосборниками должно быть не менее 1,5 метра, между воздухосборником или газосборником и стеной здания – не менее 1 метра.
Ограждение должно устанавливаться от воздухосборника или газосборника в сторону проезда или прохода на расстоянии не менее 2 метров. Высота ограждения воздухосборника или газосборника должна быть не менее 1 метра.
190. Установка воздухосборника, газосборника внутри здания не допускается.
В отдельных случаях разрешается устанавливать в помещениях гидроаккумуляторы и воздухосборники, конструктивно встроенные в компрессорный агрегат, станок или другое технологическое оборудование.
191. Допускается (кроме угольных шахт) присоединение к одному воздухосборнику, газосборнику нескольких компрессоров с установкой на нагнетательных линиях обратных клапанов и запорной арматуры. Перед запорной арматурой устанавливаются предохранительные клапаны.
192. Для проведения профилактических и периодических внутренних осмотров, ремонтов воздухосборников или газосборников предусматривается возможность отключения от сети каждого из них.
193. Каждый воздухосборник, газосборник должен быть снабжен лазом или люком, спускным краном в низшей точке для отвода конденсата и отработанного масла, предохранительным клапаном и манометром с трехходовым краном, установленным в удобном для наблюдения месте.
194. Для удобства обслуживания, осмотра и ремонта воздухосборника, газосборника, манометра и предохранительного клапана должны предусматриваться площадки и лестницы.
195. Воздухосборник или газосборник должен быть оборудован устройством для автоматической или ручной продувки его от конденсата и отработанного масла.
196. При отсутствии автоматической продувки ручная продувка воздухосборников или газосборников должна производиться не реже одного раза в смену при наличии концевого холодильника и масловлагоотделителя и не реже двух раз в смену при их отсутствии, если руководством по эксплуатации изготовителя или технологическим регламентом не предусмотрен более короткий период продувки. Конденсат и отработанное масло должны отводиться в сборники, исключающие загрязнение стен зданий и окружающей территории.
197. Во избежание воспламенения масла и масляных отложений в воздухосборниках, газосборниках и трубопроводах, при засасывании воздуха или инертного газа с измельченной пылью и ржавчиной, которые создают заряды статического электричества, обеспечивается их заземление.
198. Измерение величины сопротивления заземляющих устройств проводится не реже одного раза в год. Результаты измерений величины сопротивления оформляются протоколом и заносятся в паспорт заземляющего устройства.
199. На каждом воздухосборнике или газосборнике должна быть вывешена табличка или нанесена надпись с указанием регистрационного номера, величины разрешенного рабочего давления, даты (число, месяц, год) проведения следующих наружного и внутреннего осмотров, гидравлического испытания.
|
|
Осушительные установки сжатого воздуха
200. Для получения глубоко осушенного воздуха, помимо концевых холодильников, компрессоры оборудуются специальными осушительными установками.
201. Осушительные установки, работающие по методу вымораживания влаги при помощи холодильных установок, должны быть расположены в изолированных от компрессорной установки помещениях.
202. Осушительные установки, работающие по методу поглощения влаги твердыми сорбентами и с использованием нетоксичных и невзрывоопасных хладагентов, допускается размещать в машинном зале компрессорной установки.
203. При применении в холодильных машинах нетоксичных и невзрывоопасных хладагентов осушительные установки допускается располагать в машинном зале.
Трубопроводы и внутрицеховые нагнетательные трубопроводы
204. Трубопроводы (воздухопроводы, газопроводы) и сосуды, входящие в состав компрессорной станции (воздухосборники, газосборники, масловлагоотделители и другие емкости), должны приниматься в эксплуатацию в порядке, определенном нормативными актами промышленной безопасности, обеспечивающими безопасную эксплуатацию оборудования, работающего под давлением.
205. Монтаж трубопроводов допускается производить по стенам здания, эстакадам и в каналах. Участки трубопроводов, проходящие через стены, заключаются в предохранительные трубы. Размеры каналов обеспечивают возможность выполнения осмотров и ремонтов.
206. На трубопроводах должны монтироваться компенсирующие устройства, предотвращающие разгерметизацию сварных и фланцевых соединений из-за температурной деформации (удлинения, сжатия) трубопровода.
207. Несущие колонны и элементы конструкции эстакады должны исключать вибрацию трубопровода.
Опоры трубопроводов должны обеспечивать перемещение его элементов при температурной деформации и гарантировать прочность для восприятия веса воздухопровода или газопровода и всех вспомогательных устройств. Трубопроводы должны быть закреплены на огнестойких или несгораемых конструкциях.
208. Монтаж трубопроводов и арматуры должен производиться сваркой встык. В отдельных случаях, где не представляется возможным выполнить соединения сваркой, допускается применение фланцевых соединений.
209. В качестве прокладочных материалов для фланцевых соединений должны применяться материалы, устойчивые к воздействию влаги, масла и температуры (паронит, асбест и другие).
210. Не допускается применение картонных, резиновых и других горючих или тлеющих прокладок.
211. Для уплотнения фланцевых соединений и участков трубопроводов, проложенных в подземных выработках, должны применяться прокладки из специальной тепло- и маслостойкой резины с температурой воспламенения не ниже 350 оС. Резиновые прокладки должны быть изготовлены в централизованном порядке и иметь отличительное клеймо.
212. Применение резиновых прокладок без клейма не допускается.
213. При устройстве наружных трубопроводов, применением теплоизоляции, должна исключаться возможность их внутреннего обмерзания.
214. На отдельных участках трубопроводов, где возможно скопление конденсата и отработанного масла, должны устанавливаться линейные масловлагоотделители с автоматической или ручной продувкой. Приспособления для продувки должны быть постоянно доступными для обслуживания. В случае замерзания продувочного устройства отогревание его допускается производить горячей водой, паром или горячим воздухом.
Применение для отогрева открытого источника огня не допускается.
215. При отсутствии устройства для автоматической продувки линейного масловлагоотделителя, продувка должна производиться вручную не реже двух раз в смену и отмечается в журнале учета работы компрессорной установки.
216. Трубопроводы должны укладываться с уклоном 0,003о в сторону линейных масловлагоотделителей.
217. На трубопроводах не допускается наличие мертвых зон (глухих отводов, заглушенных штуцеров и тому подобного), способствующих скоплению конденсата и отработанного масла.
218. Арматура, устанавливаемая на трубопроводах, должна быть смонтирована с учетом доступа для удобного и безопасного обслуживания, и ремонта.
219. Вентили, задвижки, краны, клапаны должны содержаться в исправном состоянии и обеспечивать возможность быстрого прекращения подачи сжатого газа.
Маховики арматуры должны плотно закрепляться на шпинделях. На вентили, задвижки, краны, клапаны и приводы к ним наносятся надписи:
1) номер или условное обозначение запорного или регулирующего органа, соответствующие исполнительным схемам трубопроводов;
2) указатель направления вращения маховика в сторону закрытия «з» и в сторону открытия «о».
220. Трубопровод, проложенный вблизи теплоизлучающих аппаратов, должен быть теплоизолирован.
221. Трубопроводы прокладываются на расстоянии не менее 0,5 метров до электрокабелей, электропроводок и электрооборудования.
Организация эксплуатации технического обслуживания
222. Для обеспечения безопасной эксплуатации компрессорных станций должны быть разработаны, в соответствии с руководством изготовителя и требованиями настоящих Правил, технологические регламенты для производства следующих видов работ:
1) безопасное обслуживание стационарной компрессорной установки;
2) очистка (промывка) промежуточных и концевых холодильников; масловлагоотделителей, воздухосборников, газосборников, нагнетательных трубопроводов (внутрицеховых и внешних);
3) эксплуатация и проверка исправности действия манометров, предохранительных клапанов, средств автоматического контроля, управления, сигнализации и защиты;
4) проведение осмотров и очистки цилиндров и клапанных коробок компрессоров от нагарообразования;
5) проведение осмотров и очистке воздушных фильтров от скопившейся пыли;
6) очистка системы охлаждения сжатого воздуха или инертного газа (рубашки цилиндров, промежуточные и концевые холодильники) от накипи, шлама и других загрязнений;
7) подготовка сосудов и нагнетательных трубопроводов компрессорной установки к техническому освидетельствованию;
8) проведение пневматического испытания трубопроводов и сосудов компрессорной установки на герметичность;
9) проведение ревизий, ремонта, регулировки и опломбирования предохранительных клапанов.
223. Приказом (распоряжением) владельца или руководителя эксплуатирующей организации должны быть назначены лица, ответственные по надзору за безопасной эксплуатацией компрессорной станции и сосудов работающих под давлением, лица, ответственные за исправное состояние компрессорной станции и сосудов, работающих под давлением в соответствии с положением о производственном контроле.
224. Допуск персонала к самостоятельному обслуживанию компрессорных установок должен оформляться приказом (распоряжением) по организации.
225. Перед запуском компрессора машинист должен осмотреть установку, убедиться в ее исправности, проверить систему смазки и охлаждения, произвести пуск в соответствии с технологическим регламентом.
226. Во время работы компрессорной установки контролируются:
1) давление и температура сжатого газа после каждой ступени сжатия;
2) температура сжатого газа после промежуточных и концевого холодильников;
3) непрерывность поступления в рубашки цилиндров компрессоров, в промежуточные и концевые холодильники охлаждающей воды;
4) температура охлаждающей воды, поступающей и выходящей из системы охлаждения по точкам;
5) давление и температуру масла в системе компрессора;
6) величину силы тока статора, а при синхронном электроприводе силы тока ротора электродвигателя;
7) исправность действия лубрикаторов и уровень масла в них.
227. Показания приборов должны записываться через установленные технологическим регламентом промежутки времени, но не реже чем через каждые два часа, в журнал учета работы компрессорной установки.
228. В журнале записываются: время пуска и остановки компрессора, причина остановки, неисправности и неполадки, результаты и время проведения проверки исправности предохранительных клапанов и манометров, средств автоматического контроля, управления, сигнализации и защиты, проведение продувки и слива конденсата из масловлагоотделителей, воздухосборников, газосборников и других емкостей; внеплановые чистки фильтров.
229. Журнал учета работы компрессорной установки, проверяется и подписывается ежесуточно лицом, ответственным за исправное состояние компрессорной станции и сосудов, работающих под давлением.
230. Компрессор останавливается в случаях:
1) предусмотренных руководством по эксплуатации изготовителя;
2) если манометры на любой ступени компрессора, на нагнетательной линии показывают давление выше допустимого;
3) если манометр системы смазки механизма движения показывает давление ниже допустимого нижнего предела;
4) при внезапном прекращении подачи охлаждающей воды или другой аварийной неисправности системы охлаждения;
5) если слышны стуки, удары в компрессоре или двигателе или обнаружены их неисправности;
6) если температура сжатого воздуха выше предельно допустимой нормы, установленной руководством изготовителя;
7) при пожаре;
8) при появлении запаха гари или дыма из компрессора или электродвигателя;
9) при заметном увеличении вибрации компрессора, электродвигателя других узлов;
10) если электроприборы на распределительном щите указывают на перегрузку электродвигателя.
231. После аварийной остановки компрессора его пуск должен производиться с разрешения лица, ответственного по надзору за безопасную эксплуатацию компрессорной станции и сосудов, работающих под давлением.
232. Ремонт и очистка оборудования и трубопроводов, находящихся под давлением, не допускаются.
233. Не допускается оставлять работающие компрессоры (кроме полностью автоматизированных) без контроля лиц, допущенных к их обслуживанию.
234. Не допускается во время дежурства поручать машинисту компрессорной станции выполнение работ, не связанных с обслуживанием компрессорной установки.
235. Должен производиться регулярный наружный осмотр оборудования компрессорной установки, обтирка и очистка ее наружных поверхностей от пыли и грязи. Не допускаются утечки масла и воды, особенно попадание масла на фундамент. Причины утечек при их обнаружении устраняются.
236. Воздушные фильтры должны проверяться в сроки, предусмотренные руководством по эксплуатации компрессорной установки. Значение сопротивления проходу воздуха в фильтре должна быть не более 50 мм водяного столба, если иная величина не указана изготовителем. При большем сопротивлении фильтр очищается.
Техническое освидетельствование сосудов и трубопроводов (воздухопроводы, газопроводы). 237. Сосуды и трубопроводы в процессе их эксплуатации должны подвергаться следующим техническим освидетельствованиям:
1) наружному осмотру;
2) внутреннему осмотру (в процессе эксплуатации);
3) гидравлическому испытанию.
Объем, методы и периодичность проведения технических освидетельствований проводятся в соответствии с требованиями промышленной безопасности при безопасной эксплуатации оборудования, работающего под давлением.
238. Сосуд или трубопровод должен останавливаться для проведения очередного технического освидетельствования не позднее срока, указанного в их паспортах.
239. При наружном осмотре вновь смонтированного нагнетательного трубопровода должно быть проверено соответствие проекту: расположение опор, компенсаторов, арматуры, спускных, продувочных и дренажных устройств, контрольно-измерительных приборов, предохранительных устройств и тому подобное.
240. Должны быть осмотрены все сварные соединения. При осмотре выявляются следующие поверхностные дефекты: трещины, наплывы, подрезы, прожоги, незаверенные кратеры, непровары пористости, излом и неперпендикулярность осей соединяемых элементов, смещение кромок, отступления размеров формы швов от проектных и другие технологические дефекты.
241. Методы, объемы и последовательность контроля качества сварных соединений (неразрушающие методы контроля, механические испытания, металлографические исследования) определяются проектной организацией и указываются в проекте компрессорной станции.
242. Вновь смонтированные трубопроводы должны быть подвергнуты наружному, внутреннему осмотрам и гидравлическому испытанию до наложения изоляции.
243. В процессе эксплуатации компрессорной установки периодический наружный осмотр трубопроводов, проложенных открытым способом или в проходных и полупроходных каналах, должен быть произведен с выборочным вскрытием изоляции.
244. При периодическом наружном осмотре компрессорной установки проверяется:
1) состояние компрессора и электродвигателя;
2) электроаппаратура и заземление;
3) исправность системы смазки и охлаждения;
4) промежуточный и концевой холодильники, сосуды (масловлагоотделители, воздухосборники, газосборники);
5) нагнетательные трубопроводы (воздухопроводы, газопроводы);
6) продувочные и дренажные устройства;
7) контрольно-измерительные приборы, средства автоматического контроля, управления, сигнализации и защиты;
8) предохранительные и обратные клапаны;
9) запорная и регулирующая арматура (вентили, задвижки, краны);
10) степень затяжки болтовых соединений;
11) исправность фланцевых и резьбовых соединений (установка гильз для термометров, присоединение манометров, трехходовых кранов и тому подобное);
12) наличие и содержание технической документации (паспорта, положение о производственном контроле, журналы, схемы, акты, графики, протоколы и тому подобное).
245. Если при наружном осмотре обнаружены неисправности или нарушения настоящих Правил и требованийпромышленной безопасности при безопасной эксплуатации оборудования, работающего под давлением, создающие опасность для жизни людей, компрессор необходимо остановить и принять меры по устранению неисправностей и нарушений правил безопасности.
246. Результаты наружного осмотра компрессорной установки должны быть оформлены актом.
247. Внутренний осмотр трубопровода проводится выборочно путем разборки фланцевых соединений, снятия задвижек и вентилей, вырезки отдельных участков, одновременно проводится ревизия запорной и регулирующей арматуры, и крепежа.
248. Наружный и внутренний осмотры проводятся с целью:
1) при первичном освидетельствовании проверить, что нагнетательный трубопровод изготовлен и смонтирован в соответствии с настоящими Правилами, проектом и представленными при регистрации актами, трубопровод и его элементы не имеют повреждений и дефектов в сварных соединениях;
2) при периодических и внеочередных освидетельствованиях установить исправность трубопровода, отсутствие на внутренней поверхности стенок масляных отложений и возможность его дальнейшей эксплуатации.
249. Выявленные при наружном и внутреннем осмотрах трубопровода дефекты, неисправности должны быть устранены.
Результаты внутреннего осмотра трубопровода считаются удовлетворительными, если не обнаружены дефекты, выходящие за пределы норм действующих требований промышленной безопасности.
250. Результаты внутреннего осмотра должны быть занесены в паспорт трубопровода с указанием срока следующего внутреннего осмотра.
251. При наружном и внутреннем осмотрах трубопровода, находившегося в нерабочем состоянии более 12 месяцев, проверяется:
1) осуществление контроля за соблюдением режима консервации;
2) в выборочном порядке – состояние внутренних поверхностей трубопровода (путем разборки фланцевых соединений, снятия задвижек, вырезки отдельных участков и другое);
3) состояние изоляции, на основании результатов осмотра принимается решение о целесообразности частичного или полного удаления изоляции.
252. Гидравлическое испытание трубопровода должно производиться только при удовлетворительных результатах наружного и внутреннего осмотров.
253. Гидравлическому испытанию с целью проверки прочности и плотности трубопроводов, их сварных и других соединений подлежат трубопроводы со всеми элементами и установленной арматурой после окончания монтажа, в процессе эксплуатации трубопровода. Гидравлическое испытание трубопроводов при первичном освидетельствовании не является обязательным, если их сварные соединения подвергались 100% контролю ультразвуком или другим равноценным методом неразрушающей дефектоскопии по всей длине швов.
254. Гидравлическое испытание трубопроводов должно быть произведено лишь после окончания всех сварочных работ, установки и окончательного закрепления опор и подвесок. При этом должны быть представлены документы, подтверждающие качество выполненных работ.
255. На всех высоких точках испытываемого трубопровода должен быть предусмотрен выпуск воздуха при наполнении его водой. Устанавливаются временные воздушники из вваренных в трубопровод штуцеров с установленными на них вентилями диаметром 14-38 мм в зависимости от диаметра и длины трубопровода. Наличие воздуха в трубопроводе не позволит произвести гидравлическое испытание.
256. Для гидравлического испытания применяется вода с температурой не ниже +5оС и не выше +40оС.
257. Гидравлическое испытание трубопроводов должно производиться при положительной температуре окружающего воздуха.
258. Давление в трубопроводе необходимо повышать плавно. Использование сжатого воздуха для подъема давления не допускается.
259. Давление при испытании должно контролироваться двумя манометрами. При этом выбираются манометры одного типа с одинаковым классом точности, пределом измерений и ценой деления шкалы.
260. Минимальная величина пробного давления при гидравлическом испытании трубопроводов должна составлять 1,25 рабочего давления, но не менее 0,2 МПа (2 кгс/см2). Сосуды, являющиеся неотъемлемой частью трубопровода, испытываются тем же пробным давлением, что и трубопровод.
261. Время выдержки трубопровода и его элементов под пробным давлением должно быть не менее 10 минут.
262. После снижения пробного давления до рабочего производится тщательный осмотр трубопровода по всей его длине, а сварные соединения простукиваются молотком весом не более 1,5 кг.
263. Разность между температурами металла и окружающего воздуха во время гидравлического испытания не должна вызывать выпадения влаги на поверхностях испытуемого трубопровода. Для гидравлического испытания используется вода которая не повлечет за собой образование загрязнения трубопровода и не вызовет интенсивной коррозии.
264. Для проведения гидравлического испытания трубопровода, расположенного на высоте более 3 метров, должны устраиваться подмостки с ограждениями или другие приспособления, обеспечивающие возможность безопасного осмотра трубопровода.
265. Трубопровод и его элементы считаются выдержавшими гидравлическое испытание, если не обнаружено:
1) течи, потения в сварных соединениях и в основном металле;
2) трещин всех видов и направлений в сварных швах и зонах термического влияния;
3) видимых остаточных деформаций.
266. Результаты гидравлического испытания и заключение о возможности дальнейшей эксплуатации трубопровода (воздухопровод, газопровод) с указанием разрешенного давления и сроков следующего технического освидетельствования (число, месяц, год наружного и внутреннего осмотров, гидравлического испытания) должны быть записаны в паспорт нагнетательного трубопровода компрессорной установки.
267. Если при техническом освидетельствовании трубопровода окажется, что он находится в аварийном состоянии или имеет серьезные дефекты, вызывающие сомнение в его прочности, то дальнейшая эксплуатация трубопровода не допускается, а в паспорте делается соответствующая запись с указанием всех замечаний лицом, проводившим техническое освидетельствование.
268. Испытание трубопроводов на плотность (герметичность) должно проводиться воздухом или инертным газом под давлением, равным рабочему давлению. Испытание трубопроводов организует владелец организации или руководитель эксплуатирующей организации.
269. Результаты испытания трубопроводов на плотность оформляются актом на ремонт, ревизию и испытание трубопроводов и записываются в паспорт трубопровода лицом, ответственным за исправное состояние компрессорной станции и сосудов, работающих под давлением.
270. Результаты испытания считаются удовлетворительными, если во время испытания не произошло падения давления по манометру, а в сварных швах, трубах, корпусах, арматуре и тому подобных не обнаружено признаков разрыва, течи и запотевания.
271. Трубопроводы, проложенные в непроходных каналах, испытываются по падению давления.
272. При минусовых температурах наружного воздуха гидравлические испытания должны производиться горячей водой с температурой воды не выше +40оС и со сливом ее после испытания.
273. Методы, объемы и последовательность контроля качества сварных соединений (неразрушающие методы контроля, механические испытания, металлографические исследования и тому подобные) определяются проектной организацией и указываются в проекте.
Ремонт оборудования компрессорных установок
274. Ремонт оборудования компрессорных установок должен выполняться в соответствии с графиком планово-предупредительного ремонта, утвержденным техническим руководителем организации.
275. График планово-предупредительного ремонта и технологический регламент по ремонту компрессорного оборудования и трубопроводов составляется с учетом руководства по эксплуатации изготовителя и фактического их состояния.
276. Очистка промежуточных и концевых холодильников, сосудов масловлагоотделителей, воздухосборников, газосборников, нагнетательных трубопроводов (внутренних и внешних) от масляных отложений должна производиться через 5000 часов работы компрессора способом, не вызывающим коррозию металла в соответствии с технологическим регламентом.
277. Очистка трубопроводов и сосудов должна производиться 3%-ным раствором сульфанола. После очистки должна производиться продувка сжатым воздухом в течение 30 минут (не менее).
278. В отдельных случаях очистку оборудования и трубопроводов допускается производить 5%-ным раствором каустической соды. Отсутствие следов щелочи после промывки проверяется фенолфталеиновой бумагой или 1%-ным спиртовым раствором фенолфталеина. После очистки производится промывка водой до полной нейтрализации и продувка сжатым воздухом в течение не менее получаса.
279. Не допускается производить очистку промежуточных и концевых холодильников, масловлагоотделителей, трубопроводов от масляных отложений способом выжигания.
280. Очистка внутренних поверхностей цилиндров компрессора от нагара должна производиться в соответствии с руководством по эксплуатации изготовителя компрессора.
281. Осмотр клапанных коробок компрессора на отсутствие нагара должен производиться через 1000 часов работы. В случае обильного нагарообразования выясняется и устраняется причина, а все клапанные коробки очищаются от нагара.
282. Для компрессорных станций, где установлены компрессоры без смазки полостей сжатия, или в установках, где предусмотрена очистка сжатого воздуха от масла в капельном виде, если температура воздуха в воздухосборнике и воздухопроводах не превышает 50оC, осмотр и очистка воздухосборников и воздухопровода должны производиться не реже одного раза в год.
283. Не допускается применять для очистки воздухосборников, масловлагоотделителей и другого оборудования горючие и легковоспламеняющиеся жидкости (бензин, керосин).
284. Рубашки цилиндров и трубки промежуточных и концевого холодильников компрессора должны очищаться от накипи и грязи по графикам осмотра и планово-предупредительного ремонта.
285. При внутреннем осмотре, чистке или ремонте сосудов, других емкостей и трубопроводов они должны быть отключены от соответствующей сети заглушками с хвостовиками, полностью освобождены от оставшихся осадков, продуваться чистым воздухом в течение 10 минут (не менее).
Толщина применяемых при отключении сосуда или трубопровода заглушек и фланцев должна быть определена с расчетом на прочность.
Между фланцами и заглушкой должны использоваться прокладки без хвостовиков.
286. Внутренний осмотр, чистка или ремонт сосуда должны производиться не менее чем двумя работниками, один из которых должен находиться снаружи и непрерывно следить за состоянием работающего персонала внутри.
Работник, находящийся внутри сосуда, должен быть снабжен спецодеждой, обувью, каской и защитными очками.
287. Работы внутри сосуда производятся только по разрешению инженерно-технического работника, ответственного за исправное состояние компрессорной установки, после проведения инструктажа персонала о правилах безопасного ведения работ и методах оказания первой помощи.
Данные работы проводятся по наряду-допуску.
288. Все люки и лазы сосуда во время нахождения в нем работающего персонала должны быть открыты, сосуд непрерывно вентилируется.
289. При работе внутри сосуда (внутренний осмотр, чистка, ремонт и тому подобное) должны применяться взрывозащищенные светильники с величиной напряжения не выше 12В.
290. После очистки и ремонта оборудования компрессорной установки следует удостовериться в том, что внутри сосуда не осталось каких-либо посторонних предметов.
291. В эксплуатирующей организации или владельцем должен вестись журнал учета ремонта компрессорной установки, в который лицом, ответственным по надзору за безопасной эксплуатацией компрессорной станции и сосудов, работающих под давлением, вносятся сведения о выполненных чистках и ремонтных работах, не вызывающих внеочередного технического освидетельствования сосуда или трубопровода. После капитального ремонта оборудования компрессорной установки, кроме записи в журнале должны быть составлены акт на ремонт, ревизию и испытание трубопроводов и акт приема-передачи агрегата, сосуда из ремонта. Сведения о ремонтных работах, вызывающих проведение внеочередного технического освидетельствования сосуда или трубопровода, о материалах, использованных при ремонте, сведения о качестве сварки должны заноситься в паспорт сосуда или трубопровода.
292. Ремонт с применением сварки сосудов и их элементов, работающих под давлением, должен проводиться по технологии, разработанной изготовителем.
293. К ремонту оборудования компрессорной установки с применением сварки допускаются сварщики, прошедшие проверку знаний по вопросам промышленной безопасности.
Техническая документация
294. Каждая компрессорная станция или группа однородных компрессорных установок должны быть оснащены технической документацией:
1) паспорт компрессора;
2) руководство изготовителя по монтажу и эксплуатации компрессора.
3) паспорт на каждый сосуд компрессорной установки (масловлагоотделитель, воздухосборник, газосборник и другие емкости, работающие под давлением).
К паспорту сосуда приобщаются:
- удостоверение о качестве монтажа;
- исполнительная схема трубопроводов (сжатого воздуха, инертного газа, охлаждающей воды, масла) с указанием места установки и присвоенного номера каждому запорному и регулирующему органу (вентиль, задвижка, кран, обратный клапан), концевому и промежуточным холодильникам, сосудам (масловлагоотделителям, воздухосборникам, газосборникам), контрольно-измерительным приборам, предохранительным клапанам, воздухомерам, газомерам, средствам автоматического управления. На схеме должен быть указан источник давления, рабочая среда, ее параметры. Исполнительная схема трубопроводов должна быть утверждена техническим руководителем организации и вывешивается в машинном зале на видном месте;
- паспорт на каждый предохранительный клапан с расчетом его пропускной способности.
4) паспорт трубопроводов;
5) положение о производственном контроле;
6) технологические регламенты проведения работ по монтажу, эксплуатации, обслуживанию, техническому освидетельствованию и ремонту компрессорных установок;
7) акт о проведении ревизии, ремонта, регулировки и опломбирования предохранительных клапанов;
8) журнал учета работы компрессорной установки;
9) журнал учета ремонтов компрессорной установки, в который также заносятся результаты проверки сваренных швов;
10) журнал периодических контрольных проверок манометров;
11) журнал учета расхода компрессорного масла;
12) паспорта-сертификаты на компрессорные масла и результатами их лабораторных анализов;
13) паспорт заземляющего устройства компрессорной установки;
14) протоколы замеров величины сопротивления заземляющего устройства, проверок состояния устройств молниезащиты компрессорной станции;
15) протокола проверки знаний персоналом требований промышленной безопасности;
16) графики профилактических осмотров, планово-предупредительных и капитальных ремонтов компрессорных установок.
295. К ремонтному журналу прилагаются:
1) эскизы и чертежи на усовершенствования или изменения, произведенные при ремонте;
2) акты приемки оборудования после среднего и капитального ремонта;
3) акты очистки трубопроводов, компрессоров, воздухосборников, холодильников и воздушных фильтров;
4) сварочный журнал на трубопроводы высокого давления.
Дата добавления: 2018-05-12; просмотров: 1486; Мы поможем в написании вашей работы! |
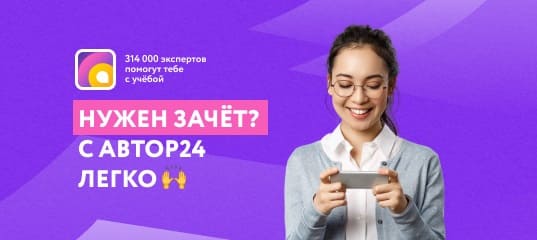
Мы поможем в написании ваших работ!