Состав и свойства твердых топлив
Твердые топлива содержат горючую органическую массу и негорючую (минеральную) часть – балласт.
Органическая масса топлива состоит в основном из углерода, водорода и кислорода. Помимо этих элементов в органической массе могут содержаться, например, азот и сера. Соотношение между отдельными элементами, входящими в состав топлива, влияет на его свойства.
Негорючая часть топлива состоит из влаги и минеральных веществ. Количество влаги в топливе зависит не только от вида топлива, но и от способа его добычи и хранения.
Минеральную часть топлива составляют карбонаты, силикаты, фосфаты, сульфаты металлов – железа, кальция, магния, алюминия, калия, натрия и др. При сжигании или газификации топлива минеральные вещества остаются в виде золы; при этом многие из них подвергаются разложению с образованием оксидов. При пиролизе зола находится в твердом остатке топлива. Примесь серы сильно влияет на свойства топлива и качество получаемых при его переработке продуктов. Она входит в топливо в виде сульфидов – сульфидная сера, сульфатов – сульфатная сера и органических соединений – органическая сера. При сжигании и газификации топлива сульфидная и органическая сера окисляется, образуя диоксид серы, а сульфатная в большинстве случаев остается в золе. При сухой перегонке топлива сера распределяется между получаемыми продуктами, но основное количество остается в твердом остатке.
|
|
Летучими веществами называются газообразные и жидкие продукты (при высокой температуре находятся в парообразном состоянии), получающиеся при нагревании топлива без доступа воздуха. Выход летучих (потери в массе топлива при нагревании его без доступа воздуха при 850 оС в течение 7 мин за вычетом имеющейся в топливе влаги) позволяет судить о целесообразности его химической переработки для получения жидких и газообразных продуктов.
Теплотворная способность – это количество теплоты, которое получают при сжигании единицы массы или объема топлива. Теплотворная способность является энергетической характеристикой топлива и выражается в джоулях; она зависит от состава и влажности топлива.
Методы переработки твердого топлива
Коксование– метод переработки твердых топлив, преимущественно углей, заключающийся в нагревании их без доступа воздуха до 900-1050 оС. Топливо при этом разлагается с образованием летучих веществ и твердого остатка – кокса. При постепенном нагревании компоненты угля претерпевают глубокие физические и химические превращения: до 250 оС происходит испарение влаги, выделение оксида и диоксида углерода; около 300 оС начинается выделение паров смолы и образование пирогенетической воды; выше 350 оС уголь переходит в пластическое состояние; при 500-550 оС наблюдается бурное разложение пластической массы с выделением первичных продуктов (газа и смол) и твердение ее с образованием полукокса. Повышение температуры до 700 оС сопровождается дальнейшим разложением полукокса, выделением из него газообразных продуктов; выше 700 оС преимущественно происходит упрочнение кокса. Летучие продукты, соприкасаясь с раскаленным коксом, нагретыми стенками и сводом камеры, в которой происходит коксование, подвергается пиролизу, превращается в сложную смесь паров (с преобладанием соединений ароматического ряда) и газов, содержащих водород, метан и др. Большая часть серы исходных углей и все минеральные вещества остаются в коксе. Таким образом, коксование – это сложный многофазный процесс, складывающийся из процессов теплоотдачи, диффузии и большого количества разнообразных реакций. При коксовании каменных углей в результате получают следующие продукты: кокс, коксовый газ, каменноугольную смолу, сырой бензол, надсмольную воду и соли аммония (большей частью сульфат аммония).
|
|
Основные задачи, стоящие перед коксохимической промышленностью:
|
|
- интенсификация процесса коксования созданием печей непрерывного коксования;
- расширение сырьевой базы для коксования за счет использования недефицитных марок угля;
- расширение ассортимента выпускаемой продукции;
- разработка рациональных схем наиболее полного и экономического выделения продуктов, содержащихся в сыром бензоле, каменноугольной смоле и коксовом газе;
- получение химически чистых индивидуальных веществ из сырого бензола и каменноугольной смолы.
Сырьем для коксования служат спекающиеся угли, которые дают прочный и пористый металлургический кокс, например коксующиеся угли марки К. Однако в промышленной практике составляется смесь – шихта, состоящая не только из коксующихся углей, но и из углей других марок; например, шихта из донецких углей имеет примерно следующий состав: газовых углей 20 %, жирных 40 %, коксовых 20 % и отощенных спекающихся 20 %. Включение в шихту углей различных марок позволяет расширить сырьевую базу коксохимической промышленности, получить качественный кокс и обеспечить высокий выход смолы, сырого бензола и коксового газа.
Устройство и работа коксовых печей. Коксование углей представляет собой высокотемпературный химический процесс. Реакции протекают сначала только в твердой фазе. По мере повышения температуры происходит образование газо- и парообразных продуктов, протекают сложные реакции внутри твердой и газовой фаз, а также происходит взаимодействие между ними.
|
|
![]() |
Коксование углей проводят в коксовых печах, или батареях (рис. 1.5), состоящих из 61-77 параллельно работающих камер, представляющих собой длинные, узкие каналы прямоугольного
Рис. 1.2.2.1. Схема коксовой батареи
сечения, выложенные огнеупорным кирпичом и разделенные между собой пустотелыми простенками, называемые вертикалами, в которых циркулируют горячие газы, нагревающие угольную загрузку. По вертикалам движутся греющие газы, они отдают теплоту стенкам камеры и уходят в регенераторы.
Исходные угли, после обогащения, сушатся, дробятся, рассеиваются до получения фракции 3-6 мм. Из углей готовят шихту (20 тонн), которую загружают в коксовые камеры сверху. В своде камеры находятся загрузочные люки, которые открываются при загрузке угля и закрыты в период коксования. Каждая камера имеет переднюю и заднюю съемные двери, которые в момент загрузки камеры плотно закрыты.
В обогревательном канале поддерживается температура 1400 оС, температура угольной загрузки 1100 оС, средняя скорость подъема температуры 1оС в 1 мин, продолжительность коксования 13 час.
Если рассматривать состояние материала в камере во время периода коксования, то видно, что у стенок находится слой образовавшегося кокса; далее по мере снижения температуры от стенок к оси камеры располагаются слой полукокса, затем угля, находящегося в пластическом состоянии и, наконец, в центре камеры неизмененная шихта. С течением времени температура по сечению выравнивается, слои перемещаются к оси камеры и постепенно угольная загрузка прококсовывается.
Образующаяся в процессе коксования смесь паров и газов непрерывно выводится из камеры через стояк. По окончании коксования передняя и задняя двери специальным механизмом снимаются и образовавшийся в камере «коксовый пирог» при помощи коксовыталкивателя выдается из камеры и попадает в тушильный вагон, где охлаждается орошением водой или газом. За счет резкого понижения температуры, кокс растрескивается; формируется внутренняя структура кокса; образуются поры, из которых вымываются остатки каменноугольной смолы и газы. Затем кокс просыхает, дробится на щековых дробилках и сортируется по величине кусков.
Таким образом, процесс коксования в каждой камере периодический. Однако наличие в коксовой батарее ряда параллельно работающих камер обеспечивает непрерывность работы всей установки.
Прямой коксовый газ, удаляемый через стояки из каждой камеры, непрерывно поступает общий для всех камер горизонтальный газосборник. Все камеры коксовой батареи имеют общие, обслуживающие их механизмы – загрузочный вагон, из которого производится загрузка угля в камеры, двересъемные устройства, коксовыталкиватель, тушильный вагон, тушильную башню, в которой тушильный вагон с раскаленным коксом орошается водой, и угольную башню – бункер для загрузки камер углем.
Дата добавления: 2018-05-12; просмотров: 1107; Мы поможем в написании вашей работы! |
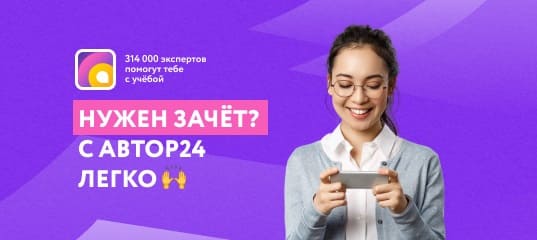
Мы поможем в написании ваших работ!