Ульразвуковые и светолучевые методы обработки.
Ультразвуковые методы обработки основаны на использовании энергии ультразвуковых колебаний частотой 18…44 кГц. Источником ультразвука служат пьезокерамические или магнитострикционные преобразователи, возбуждаемые от ультразвукового генератора. Эффектом магнитострикции обладает никель, железоникелевые, железоалюминиевые сплавы, ферриты. Для увеличения амплитуды колебаний магнитострикционного сердечника используется волновод, что увеличивает амплитуду колебаний до 10…60 мкм.
На волноводе закрепляют рабочий инструмент. В зону обработки между инструментом и заготовкой поливом или под давлением подают водную абразивную суспензию, содержащую карбиды бора, кремния, алмазные порошки и т.п. В процессе обработки инструмент поджимает к заготовке с небольшой силой 1..60 Н (по некоторым источникам до 200 Н). В рабочей зоне наблюдаются два основных процесса:
· ударное вдавливание абразивных зерен, вызывающее выкалывание небольших частиц материала заготовки;
· циркуляция абразивного материала для удаления выколотых частиц и доставки свежего абразива.
Размер выкалываемых частиц небольшой, однако, количество ударов велико (18…44кГц) и при определенных условиях обработка идет достаточно успешно. Например, при обработке твердых сплавов производительность достигает 40…80 мм3/мин. В зависимости от вида подачи, а так же формы инструмента можно осуществить различные кинематические схемы ультразвуковой обработки (рис. ). Ультразвуковые методом обрабатывают сквозные глухие отверстия любой формы поперечного сечения, фасонные полости, разрезают заготовки на части, профилируют наружные поверхности, гравируют, нарезают резьбу и др. Инструменты изготовляют из закаленных (HRC 35…40), но вязких материалов.
|
|
Ультразвуковым методом обрабатывают хрупкие твердые материалы: стекло, керамику, ферриты, кремний, кварц, драгоценные минералы, в том числе алмазы, твердые и титановые сплавы, вольфрам и др.
Преимущество ультразвуковой обработки перед электроэрозионной и электрохимической – возможность обработки диэлектриков, а при обработке тугоплавких металлов и твердых сплавов – более высокое качество поверхностного слоя.
Применение ультразвука для интенсификации обычных процессов резания труднообрабатываемых материалов путем сообщения вынужденных колебаний малой амплитуды (3…10 мкм) инструменту или заготовке наиболее эффективно при работе с малым сечением среза, например, при нарезании резьбы метчиками. Снижается усилие резания, улучшается качество обработанной поверхности и за счет уменьшения количества метчиков в комплекте в 1,5… 3 раза повышается производительность процесса.
|
|
Ультразвуковое нарезание резьбы малого диаметра (М3…М12) позволяет механизировать процесс, повысить стойкость инструмента, исключить брак, вызываемый поломками метчиков.
Перспективным направлением физико-химических методов является рациональное совмещение различных процессов. Например, совмещение ультразвуковой и электрохимической обработки позволяет при обработке тугоплавких металлов и твердых сплавов повысить производительность в 10 раз по сравнению с электроэрозионной и в 5…6 раз по сравнению с ультразвуковой, при этом в 5 раз снижается износ инструмента и в 3…5 раз усиливается энергоемкость процесса.
Установлено, что при ультразвуковой обработке твердых сплавов образуются сжимающие остаточные напряжения в поверхностном слое, в результате повышается износостойкость и усталостная прочность твердосплавных штампов, матриц, пресс-форм, фильер и других деталей, обработанных ультразвуковым методом.
Оптические квантовые генераторы – лазеры, результат независимого открытия в 1955 году советских физиков Н. Г. Басова и А. М. Прохорова, а также Ч. Таунсона (США), в настоящее время успешно применяют в технологиях различных отраслей промышленности, электроники, медицины. Лазер – источник электромагнитного излучения атомов и молекул видимого инфракрасного и ультрафиолетового диапазонов. Излучение, сфокусированное в крошечное пятно, можно применять для различных целей. Полупроводниковые лазеры используют для волоконно-оптической связи, голографии. Перспективны лазерные технологии такие, как лазерная химия, лазерное воздействие на живую ткань, лазерный термоядерный синтез, лазерная спектроскопия, лазерная обработка металлов и многие другие.
|
|
Лазерные технологии, применяемые в промышленности, можно условно разделить на два вида. В первом виде используется возможность тонкой фокусировки лазерного луча и точного дозирования энергии, как в импульсном, так и в непрерывном режиме. В таких технологических процессах применяют лазеры сравнительно невысокой средней мощности: это газовые лазеры импульсно-периодического действия, на кристаллах иттрий-алюминиевого граната с примесью неодима. С помощью последних разработаны технологии сверления тонких отверстий (диаметром 1…10 мкм, глубиной 10 – 100 мкм) в рубиновых и алмазных камнях для часовой промышленности, при изготовлении фильер для процессов волочения тонкой проволоки. Основная область применения маломощных импульсных лазеров связана с резкой и сваркой деталей в микроэлектронике и электровакуумной технике, с маркировкой миниатюрных деталей, автоматическим выжиганием букв, цифр, изображений для нужд полиграфической промышленности, в фотографии для изготовления сверхминиатюрных печатных плат, интегральных схем и других элементов микроэлектронной техники.
|
|
Второй вид лазерных технологий основан на применении лазеров со средней мощностью от 1 кВт и выше. Мощные лазеры используют для резки и сварки толстых стальных листов, поверхностной закалки, наплавки и легирования крупногабаритных деталей и др.
В установках типа “Квант” в качестве активной рабочей среды используют твердые тела – стержни из искусственного рубина, стекла с добавками неодима, алюмонатриевого граната и др. Актовной средой газовых ОКГ является смесь газов – обычно СО2 + Не + N2 (лазеры на СО2), лазеры типа ЛТ-1, ЛТ-1-5 и др.
Кратковременные вспышки газоразрядной лампы 1 (рис. ) возбуждают часть атомов хрома рубинового стержня, переводя их в более высокое энергетическое состояние. Возбужденные атомы передают энергию соседним атомам. Волна, идущая вдоль оси кристалла, многократно отражается от его параллельных торцов и быстро усиливается. Через нижний (полупрозрачный) торец стержня выходит мощный импульс красного цвета, проходя через диафрагму 2, оптическую фокусирующую систему 3 и защитное стекло 4 на поверхности детали 5.
Энергия излучения ОКГ невелика – 10…100 Дж, а КПД составляет 0,1…1%. Температура в точке приложения луча на детали 5500…9000°К, достаточная для плавления и испарения металла.
Основными характеристиками лазерного излучения являются: мощность излучения (Вт), длина волны (0,04…10,6 мкм), длительность (мкс), форма импульсов, расходимость пучка.
Лазерный луч применяют для прошивания отверстий диаметром от нескольких микрон до десятков миллиметров и глубиной до 15 мм. Производительность обработки до 60 … 240 отверстий в минуту. При лазерной резке ширина реза составляет 0,3 … 1 мм, толщина разрезаемого материала до 10мм. Скорость резки зависит от толщины и свойств обрабатываемого материала и составляет 0,5 … 10 м/мин.
Преимуществом светолучевой обработки по сравнению с электронно-лучевой обработкой является:
· возможность обработки крупногабаритных деталей;
· возможность обработки труднодоступных мест;
· не требуется вакуумных камер, обработка ведется в воздушной среде;
· меньше габариты оборудования;
· не требуется защиты от рентгеновского излучения, достаточно применения защитных очков;
Недостатки обработки световым лучом:
· сравнительно невысокая излучаемая мощность;
· мощность подкачки в 1000…3000 раз больше излучаемой мощности;
· низкий КПД квантовых генераторов (1…2%);
· перегрев кристалла и трудности его охлаждения;
· относительно низкая точность обработки (9…10 квалитет).
Одним из новых направлений светолучевых технологий является лазерная стереолитография.
В условиях конкурентной экономики сокращение сроков и затрат на создание новых и модернизацию действующих изделий, а также быстрое освоение их производства благодаря использованию новейших технологий приобретает решающее значение для производителей наукоемкой продукции. Автоматическое проектирование стало основным инструментом разработчиков и производителей новой техники. Применение ЭВМ на стадии технической подготовки производства позволяет быстро переходить к выпуску новых высококачественных изделий за счет ускоренного процесса конструирования и изготовления технологической оснастки.
САД/САМ системы, применяемые лидерами мирового машиностроения, основаны на твердотельном моделировании.
Лазерная стереолитография – технология изготовления прототипов, моделей и технологической оснастки по компьютерной математической модели методом фотополимеризации (отвердения под лазерным излучением специальных пластических масс – фотополимерных композиционных материалов).
В развитых странах используется свыше 500 стереолитографических установок.
Использование оборудования и программного обеспечения САД/САМ – систем на базе лазерной стереолитографии обеспечивает:
· в десятки раз сокращается время на разработку и внедрение в прототипы деталей, а так же создания мастер-моделей для технологической оснастки;
· значительную экономию времени и средств на конструкторскую и технологическую подготовку производства;
· высокую точность (в пределах 0,08...0,1 мм), изготавливаемых моделей-прототипов разрабатываемых конструкций.
Наиболее эффективна САД/САМ – технология в таких производствах, как: литейная, кузнечно-прессовая, листоштамповочное, инструментальное, порошковая металлургия и др.
Дата добавления: 2018-05-12; просмотров: 571; Мы поможем в написании вашей работы! |
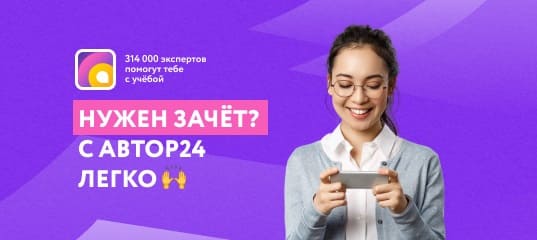
Мы поможем в написании ваших работ!