Электрохимические методы обработки.
Электрохимические методы обработки основаны на процессе электролиза металла в электролите, при котором молекулы вещества распадаются на электрически заряженные частицы – ионы. При наложении постоянного тока процесс анодного растворения металла активизируется, продукты электролиза переходят в раствор. Процесс анодного растворения подчиняется закону Фарадея, согласно которому количество растворенного металла пропорционально количеству прошедшего электричества и времени процесса. Производительность процессов электрохимической обработки определяется главным образом свойствами обрабатываемого материала, электролита и плотностью тока. В промышленности наибольшее распространение получили электрохимическое полирование, электрохимическая размерная обработка, а так же электроабразивная и электроалмазная обработка.
Электрохимическое полирование выполняется при небольшой плотности тока и неподвижном электролите (рис. ). Обрабатываемая деталь является анодом; катодом служит металлическая пластинка не вступающая в химическую реакцию с электролитом. В зависимости от обрабатываемого материала в качестве электролита используют водные растворы кислот и щелочей. Процесс анодного растворения происходит избирательно, – в первую очередь растворяются вершины микронеровностей, происходит их сглаживание, поверхность приобретает металлический блеск.
|
|
Наряду с электрополированием используется и чисто химический процесс – размерное травление (химическое фрезерование). При этом поверхности, не подлежащие обработке, защищаются слоем лака. Это процесс наиболее эффективен при обработке сталей, а так же титановых сплавов с большими площадями, типа вафельных панелей, обшивок гондолы двигателя, створок и т. п. По сравнению с процессом резания трудоемкость обработки снижается в 2…3 раза.
Электрополирование повышает электрофизические характеристики поверхности деталей, уменьшается глубина микротрещин, повышается коррозионная стойкость, усталостная прочность и предел выносливости металла.
Электрополирование применяют перед гальваническими покрытиями, для снятия тонких слоев металла при изучении остаточных напряжений, для доводки режущих кромок инструмента, в процессах изготовления тонких лент и фольги, для зачистки и декоративной отделке деталей и др. Возможна обработка сразу партии деталей по всей их поверхности.
Электрохимическая размерная обработка производится при повышенной плотности тока (до 100 А / см2 и более) и с прокачкой электролита под давлением между электродом – инструментом и заготовкой. Наибольшее распространение получила электрохимическая обработка в проточном электролите при малых зазорах (до 0,5…1,0 мм) между электродами (рис. ). При этом можно произвести обработку неподвижным электродом: удаление заусенцев на кромках отверстий, ребер, скругление кромок, маркировка, калибрование. При поступательном движении электрода производится электрохимическая прошивка отверстий, копирование, протягивание, калибрование, острение. При вращательном движении катода – инструмента выполняется обработка плоских и фасонных поверхностей, отрезка, кольцевая вырезка.
|
|
Наибольшее применение в промышленных условиях получили процессы удаления заусенцев, прошивки глухих и сквозных отверстий различного профиля, копирования фасонных поверхностей (лопатки турбин, поверхности штампов и др.). В процессе обработки струя электролита, непрерывно подаваемого в межэлектродный зазор, растворяет образующиеся на заготовке – аноде соли и удаляет их из зоны обработки. Обработке подвергается вся поверхность, находящаяся под активным воздействием катода, что обеспечивает высокую производительность процесса. Инструменту придают форму, обратную форме обрабатываемой поверхности, образование которой происходит по методу отражения практически без износа инструмента, так как его роль выполняет струя электролита.
|
|
Недостатком процесса является относительно невысокая точность обработки (до 0,2…0,3 мм).
Для повышения точности используют следующие способы:
· применение импульсного напряжения, синхронизированного с вибрацией катода в направлении его подачи;
· электрохимическое формообразование с отводом катода от заготовки в период действия электрического тока;
· обработка в воздушно – электролитной рабочей среде;
· электрохимическая обработка в импульсно – циклическом режиме (разделяется цикл анодного растворения и промывки межэлектродного зазора – удаления гидрооксидов металлов).
Наиболее эффективным является последний способ, точность повышается до ± 0,05…0,10 мм.
Электрохимическая обработка применяется для обработки заготовок из высокопрочных сплавов и труднообрабатываемых материалов. Отсутствие давления инструмента на заготовку позволяет обрабатывать нежесткие конструкции, тонкостенные детали с высокой точностью и качеством обработанной поверхности.
Для размерной электрохимической обработки используют нейтральные электролиты – водные растворы солей NaCl, NaNO3 и Na2SO4.
|
|
Разновидностью размерной электрохимической обработки является электроабразивная и электроалмазная обработка (рис. ) при которых электродом- инструментом служит шлифовальный круг, выполненный из абразивного материала на электропроводящей связке (бакелитовая с графитовым наполнителем). Между заготовкой - анодом и инструментом – катодом за счет выступающих из связки абразивных зерен образуется межэлектродный зазор, куда под давлением подается электролит. Пленка, образующаяся на поверхности заготовки в результате анодного растворения, снимается абразивными зернами вращающегося круга; заготовке сообщается движение подачи.
Электроабразивные и электроалмазные методы применяют для отделочной обработки заготовок из труднообрабатываемых материалов, а также нежестких заготовок, так как силы резания этих процессов незначительны. В результате обработки большая часть припуска удаляется за счет анодного растворения (до 90 % при электроабразивной и до 75% при электроалмазной), а остальная – за счет механического воздействия абразивных или алмазных зерен. По сравнению с обычным процессом шлифования указанные методы обеспечивают более низкую шероховатость (0,16 …0,04 мкм) в поверхностном слое отсутствуют микротрещины, так как снижается температурное воздействие, уменьшается износ шлифовальных кругов.
Введение в зону резания ультразвуковых колебаний повышает производительность процесса в 2…2,5 раза при значительном улучшении качества обработанной поверхности.
Отделочную обработку поверхностей выполняют также электрохимическим хонингованием (рис. ). В отличие от обычного хонингования при электрохимическом на заготовку подается положительное, а на инструмент отрицательное напряжение, процесс осуществляется в электролите, вместо абразивных на хон устанавливают деревянные или пластмассовые бруски. Продукты анодного растворения удаляются с поверхности заготовки брусками при вращательном и возвратно-поступательном движениях хонинговальной головки. Для интенсификации процесса в раствор электролита добавляют абразивные материалы. После удаления припуска включают электрический ток, но продолжают обработку “выхаживанием” до полного удаления анодной пленки с поверхности. Электрохимическое хонингование по сравнению с обычным обеспечивает более низкую шероховатость, поверхность получается зеркальной, а производительность увеличивается в 4…5 раз.
Дата добавления: 2018-05-12; просмотров: 292; Мы поможем в написании вашей работы! |
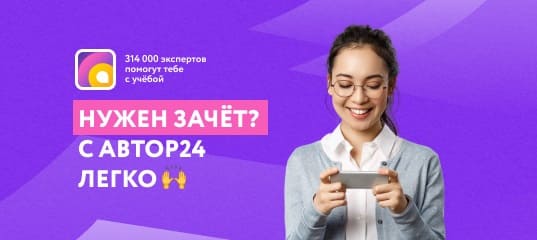
Мы поможем в написании ваших работ!