ТЕХНИКА ВАКУУМНОГО ОСАЖДЕНИЯ ТОНКИХ ПЛЕНОК
Материалы вакуумных систем
Материалы вакуумных систем должны обладать низкой скоростью газоотделения с единицы поверхности, т.е.низкой десорбцией; низкой газопроницаемостью; стойкостью к коррозии; хорошей полируемостью. Всем этим требованиям отвечают нержавеющие стали, используемые для конструкционных деталей вакуумных установок. Латунь, сплав меди с цинком, используют только для деталей, не нагреваемых выше 100-150 ○С, так как при температуре порядка 300 ○С цинк начинает испаряться. Вакуумная резина, обладающая большой эластичностью, используется для уплотнений, шлангов и т.д. Из пластмасс используется фторопласт.
Средства обеспечения вакуума
Для создания в рабочей камере необходимого высокого вакуума порядка 10-3 –10-5 Па используются механические форвакуумные насосы, например, пластинчато-роторные (рис.4) и высоковакуумные насосы, например, диффузионные (рис.5) или геттерные сорбционные (рис.6).
Рисунок 4. Пластинчато-роторный форвакуумный насос
![]() |
1- статор; 2-ротор; 3- пластины, прижатые пружинами к стенке статора; 4- внешняя среда; 5- впускной патрубок; 6- уплотнение; 7-выпускной клапан.
С помощью пластин пространство внутри статора разделяется на две области. Принцип работы пластинчато-роторного насоса состоит во всасывании впускным клапаном остаточного газа из рабочего объема вследствие расширения пространства между статором и ротором при вращении ротора. При дальнейшем вращении ротора газ сжимается и выталкивается в среду. При достижении вакуума 10-2 включается высоковакуумный насос (рис.5). Рабочая жидкость (силиконовое масло) нагревают. Горячий пар поднимается в паропроводе и выходит через расширяющееся сопло со сверхзвуковой скоростью. Расширяясь молекулы масла захватывают частицы остаточного газа, увлекая их за со
![]() |
бой. По охлажденным стенкам корпуса молекулы масла, конденсируясь, стекают вниз. Частицы газа удаляются через выпускной патрубок.
|
|
Рис.5
1-рабочая жидкость, масло; 2-корпус; 3- водяное охлаждение; 4- паропровод; 5- сопло;6- кольцевой зазор;7- зонтичный колпачок; Р.О- рабочий объем.
Для контроля вакуума используются манометры, встренные в вакуумную систему, термопарные для контроля низкого вакуума и ионизационные для контроля высокого вакуума.
Схема вакуумной системы установок для напыления тонких пленок
Типичная схема представлена на рисунке 6
![]() |
Рис.6
1-плита вакуумной установки; 2-вакуумное уплотнение; 3-рабочая камера; 4-термопарный вакуумметр; 5,6,7-вентили; 8-форвакуумный насос; 9-ионизационный вакуумметр; 10-форбаллон; 11-высоковакуумный насос; 12-высоковакуумный затвор.
|
|
Через открытые вентили 5 и7 с помощью ФВН 8 создают предварительный вакуум порядка 1-5 Па. Это давление контролируют термопарным вакуумметром 4 (рис.6а). После этого вентиль 5 закрывают, отрывают вентиль 6 и высоковакуумный затвор 12 и откачивают всю систему до такого же давления 1-5 Па. Затем включают подогреватель ВВН 11 и откачивают камеру до необходимого высокого вакуума 10-3 –10-5 Па. Это давление контролируют ионизационным вакуумметром (рис.6б). При этом ФВН 8 постоянно работает, поддерживая предварительный вакуум в форбаллоне 10. Таким образом, выход ВВН нагружен на ФБ 10, что снижает коэффициент сжатия газа, а следовательно и его конденсацию.
![]() |
Рис.6а
1-колба, соединенная с рабочим объемом; 2- провод, через который идет ток (Тпр=200○ С); 3- спай термопары; 4-термопара.
![]() |
Рис.6б
1-открытая колба, соединенная с рабочим объемом; 2-коллектор; 3-сетка; 4- катод.
Испарители
Испаритель Это приспособление, с помощью которого нагревается и испаряется нужный материал. Температура испарения Тисп для разных материалов различна. Чтобы оценить необходимую температуру испарителя, основываются на необходимости достичь установившееся давление паров испаряемого материала приблизительно1,33 Па (10-2 мм.рт.ст.). Для большинства материалов, представляющих практический интерес такое давление требует Тисп =1000-2000○С.
|
|
Материалами, отвечающими таким требованиям, являются тугоплавкие металлы и окислы металлов. Кроме того эти материалы должны при температуре испарения иметь пренебрежимо малое давление паров, не должны вступать в химическое взаимодействие с испаряемым материалом. Поэтому внутри класса тугоплавких наиболее широко используются вольфрам, молибден тантал.
Испарители и испаряемые вещества могут нагреваться или непосредственным пропусканием через них электрического тока (джоулевый нагрев), или индукционным способом (с помощью высокой частоты), или электронной бомбардировкой испаряемого вещества.
Выполнены испарители могут быть из проволоки и из металлической фольги, если испаряют небольшие навески испаряемого вещества (1-2 г.) т.е. при напылении очень тонких пленок, в основном резистивных, а также адгезионных и защитных слоев.
Для напыления более толстых слоев – проводниковых (1-2 мкм) используют тигельные (рис.7) и электронно-лучевые испарители (рис.8).
![]() |
|
|
Рис.7
1-молибденовый тигель; 2- танталовый нагреватель; 3- экраны; 4- испаряемое вещество.
![]() |
Рис.8
1-водяное охлаждение; 2-испаряемый материал; 3- остро сфокусированный пучок электронов; 4- катод; 5 – анод.
Электронно-лучевой испаритель обеспечивает наибольшую гибкость в управлении процессом напыления пленок.
Для испарения сплавов метод взрывного испарения. Он заключается в подаче из вибробункера на нагретый до нужной температуры испаритель расчетных доз компонентов сплава. Используется для получения пленок сложного состава и метод И-ПР.
Средства контроля параметров пленок
Особенности контроля параметров тонких пленок определяются их малыми толщинами (от 10 до 1000нм) и скоростью их напыления (от 1 до100нм/с). Контроль параметров пленок в процессе их напыления способствует устранению или сокращению подгонки параметров элементов после напыления. Методы контроля можно разделить на 2 группы.
1-методы контроля электрических характеристик напыляемых элементов (резистивный и емкостной датчики);
2-методы контроля основных физических характеристик, которые связаны аналитически с электрическими характеристиками пленок (кварцевый, ионизационный, интерференционный датчики).
Резистивный метод (метод «свидетеля») используется в основном для контроля сопротивления резистивных пленок. Специальную контрольную подложку с предварительно напыленными контактными площадками устанавливают в подложкодержатель рядом с рабочей подложкой или на одну из позиций на карусели подложек. С помощью прижимных контактов и проводов «свидетель» подключается в плечо моста, одно из сопротивлений которого подстроено на требуемую величину. В процессе напыления пленки сопротивление «свидетеля» достигает величины, необходимой для уравновешивания моста. Цепь обратной связи обеспечивает прекращение процесса напыления путем поворота заслонки и перекрытия потока пара.
Емкостной метод основан на измерении относительного изменения емкости планарного воздушного конденсатора, предварительно сформированного на контрольной подложке, при заполнении пространства между обкладками диэлектрической пленкой
Метод кварцевого датчика основан на измерении отклонения резонансной частоты кварцевого элемента при изменении его массы за счет напыляемой пленки. Предварительно строится градуировочный график зависимости толщины пленки от смещения частоты (рис.9).
![]() |
Рис.9
1-кварцевый элемент; 2-держатель; 3-кожух;4- контакты; 5- охлаждающие трубки; 6 –градуировочный график.
Интерференционный метод основан на измерении числа темных и светлых полос m при отражении монохроматического света от системы пленка-подложка, т.е. от внешней и внутренней поверхности пленки:
dпл =m λ /4nпл
где dпл –толщина пленки;
m – число светлых и темных слоев
λ –длина волны монохроматического света;
nпл –коэффициент преломления материала пленки.
Тема №6
Дата добавления: 2018-05-12; просмотров: 270; Мы поможем в написании вашей работы! |
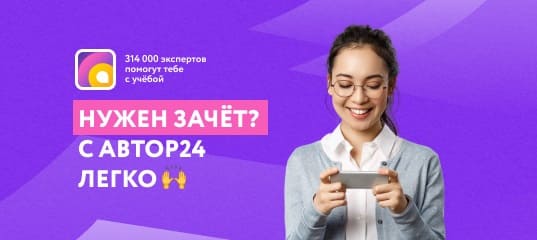
Мы поможем в написании ваших работ!