ИОННО-ПЛАЗМЕННОЕ РАСПЫЛЕНИЕ (И-П Р)
ТЕМА №4
ОСАЖДЕНИЕ ТОНКИХ ПЛЕНОК В ВАКУУМЕ
Тонкими называют пленки толщиной от 0,1 до 2,0 мкм. Высокая точность по толщине и химическая чистота таких пленок может быть достигнута только при выращивании их из атомарного потока. Создать такой поток можно только в вакууме, например, испаряя материал при высокой температуре в направлении к подложке. Это метод термического вакуумного испарения (ТВИ). Создать направленный поток атомов можно также распыляя нужный материал – мишень путем бомбардировки его ионами инертных газов, это метод ионно-плазменного распыления (И-ПР).
ТЕРМИЧЕСКОЕ ВАКУУМНОЕ ИСПАРЕНИЕ (ТВИ)
Упрощенная схема рабочей камеры для напыления пленок методом ТВИ показана на рисунке 1.
Рисунок 1. Упрощенная схема рабочей камеры для напыления пленок методом термического вакуумного испарения ТВИ
1–вакуумный колпак из нержавеющей стали; 2–подогрев подложек; 3-подложка; 4–подложкодержатель с подложкой, на который может быть размещен и трафарет – съемная маска; 6- испаряемый материал; 7 – испаритель, который нагревается до условной температуры испарения; 8-токоввод; 9–вакуумное уплотнение; 10- плита корпуса вакуумной установки; 11 – герметичные изоляторы для токовводов.
Высокий вакуум порядка 10-3 –10-5 Па обеспечивается включением сначала механического форвакуумного затем и высоковакуумного диффузионного или сорбционного насосов, включенных последовательно.
|
|
В производственных условиях используются многопозиционные вакуумные установки. В них одновременно обрабатывается 6, 8 или 12 групповых подложек, размещенных на диске - карусели. Подложки последовательно проходят над неподвижным испарителем, постепенно набирая необходимую толщину пленок. При этом достигается равномерная толщина на всей поверхности подложек (см. рисунки1а и 1б).
По достижении рабочего давления внутри камеры (контроль по манометру) включают нагреватели испарителя и подложек. По достижении рабочих температур (контроль с помощью термопар) заслонку отводят в сторону и атомы испаряемого вещества достигают подложки, где конденсируются. Так происходит рост пленки. Система контроля за ростом пленки фиксирует либо толщину пленки (для диэлектрика тонкопленочных конденсаторов), либо поверхностное сопротивление (для резисторов), либо время напыления (для проводников, контактных площадок и защитных покрытий). Сигнал об окончании напыления усиливается и поступает на привод заслонки, заслонка перекрывает поток пара. Далее отключают нагреватели испарителя и подложек, выключают систему откачки. После остывания подколпачных устройств через натекатель плавно впускают атмосферный воздух. После выравнивания давлений внутри и вне колпака его поднимают и начинают следующий цикл обработки.
|
|
Основными технологическими параметрами при ТВИ являются давление в камере РГ, температура испарителя Тисп, температура подложки ТП.
Температура испарителя должна обеспечивать такую интенсивность испарения, чтобы время напыления пленки не превышало 1 – 2 мин. Оптимальная интенсивность испарения обеспечивается при упругости пара (давлении пара в состоянии насыщения) РS порядка 1,33Па (10-2 мм.рт.ст.). Соответствующая этой упругости пара температура испарения называется условной и может быть вычислена по формуле
lg PS =A- B/ Tусл
где А и В эмпирические коэффициенты, характеризующие испаряемый материал, Тусл – абсолютная условная температура испарения, К.
Температура подложки существенно влияет на структуру пленки. Для получения поликристаллической структуры пленок подложки обычно нагревают до температур в пределах 150 – 350○С . Температура, выше которой все атомы испаряемого вещества отражаются от подложки и пленка не образуется, называется критической температурой конденсации, Она зависит от природы испаряемого материала и от состояния поверхности подложки.
|
|
Реально методом ТВИ напыляют пленки толщиной 1 – 2 мкм. Хорошую адгезию ( силу сцепления) к подложке имеют легко окисляющиеся металлы Al, Cr, Mn, Ti, W и др. Плохую адгезию имеют такие высокоэлектропроводные металлы как Cu, Au, Pt Pd и др.
![]() |
Рис.1а. Рабочий объем установки УВН-2М-1
1-испаритель; 2-кварцевый датчик толщины; 3-диск с трафаретами; 4-карусель подложек; 5-датчик контроля сопротивления пленки-«свидетель»;6-заслонка; 7-электронно-лучевой испаритель.
![]() |
Рис.1б. Рабочий объем установки УВН2М-2
1-карусель испарителей; 2-экраны; 3-диафрагма; 4-карусель трафаретов и подложек;5-нагркватель подложек;6-датчик сопротивления пленки; 7-электроды ионной очистки подложек; 8-коллектор; 9-заслонка.
ИОННО-ПЛАЗМЕННОЕ РАСПЫЛЕНИЕ (И-П Р)
При бомбардировке поверхности твердого тела - мишени отдельными атомами, ионами происходит множество явлений, какое явление будет преобладать зависит от кинетической энергии бомбардирующих частиц. При кинетических энергиях, превышающих энергию связи атомов мишени, возникает физическое распыление мишени. Атомы кристаллической решетки под воздействием бомбардировки частиц перемещаются в новое положение, мигрируют по поверхности. Если энергия становится достаточной, происходит выбивание этих атомов с поверхности мишени и выброс их в газовую фазу ( бильярдный механизм). Для бомбардировки обычно используются не нейтральные атомы, а ионы. Их можно ускорять с помощью электрического поля. Поток быстрых ионов выбивает электрически нейтральные атомы мишени.
|
|
Самая простая схема И-ПР это 2х электродная схема катодного распределения. Упрощенная схема рабочей камеры установки катодного распыления показана на рисунке 2.
Рис.2
1-вакуумный колпак из нержавеющей стали; 2- катод; 3- экран; 4-игольчатый натекатель для непрерывной подачи аргона; 5- подложка; 6- анод; 7- вакуумплотный изолятор; 8-вакуумный уплотнитель по периметру колпака; 9-плита корпуса вакуумной установки.
В разряженном газе при давлении порядка 10-2 10-3 мм рт.ст. (1-10-1 Па)создаётся тлеющий разряд, путем приложения к катоду- мишени высокого отрицательного потенциала относительно заземлённого анода. Здесь используется самостоятельный разряд, возбуждаемой автоэлектронной эмиссией (испускание электронов металлом под действием сильного внешнего поля ). Электроны, эмитировавшие из катода. ионизируют атомы газа. В результате положительные ионы газа устремляются к отрицательному катоду и выбивают атомы катода- мишени, которые летят нормально к его поверхности и оседают на подложке, лежащей на аноде.
Основной технологический параметр этого процесса Скорость распыления мишени Wp = Kp JHmM, кг/с
где Kp- коэффициент распыления мишени (атомы выбитые 1 ионом).Принимает значения от0,1 до50, в отдельных случаях до100;
JH- плотность тока катода
mM- атомная масса материала мишени
Kp- зависит от давления рабочего газа РГ. Наибольшее значение соответствует некоторому оптимальному давлению порядка ≈ 10-3 мм рт.ст., когда достаточно велика средняя длина свободного пробега ионов, с одной стороны, а с другой стороны, и самих ионов достаточно.
Коэффициент распыления зависит также от природы ионов и мишени. Наибольший коэффициент распыления имеют ионы инертных газов т.к. их энергия тратится только на выбивание атомов и не тратится на химическое взаимодействие с атомами мишени.
Важным параметром, определяющим КР является угол падения ионов. С уменьшением угла между направлением движения ионов и плоскостью мишени КР увеличивается, так как при этом уменьшается угол между направлениями импульсов движения падающих ионов и выбитых атомов, летящих нормально к поверхности мишени.
![]() |
Чистота пленок, полученных методом И-ПР тем выше, чем больше скорость осаждения и выше степень вакуума в рабочей камере. Такие условия создаются в трех электродной системе:
1-термокатод; 2-мишень; 3-анод; 4-подложка; 5-держатель подложки;
Рис.3
Если нужно распылять высокоомные или диэлектрические материалы, то на мишень подают переменное высокочастотное (ВЧ) напряжение (13,56 МГц). Распыление мишени идет в полупериод, когда мишень заряжена отрицательно. Такая частота напряжения удерживает электроны в области разряда и происходит почти 100% ионизация газа. Это способствует увеличению скорости роста пленок.
Если в камеру ВЧ распыления ввести специально активный газ, то можно получить пленку химического соединения газа, напр., кислорода, азота, углерода с распыляемым материалом мишени. Это будет реактивное распыление.
Использование магнитного поля, перпендикулярного электрическому между анодом и катодом позволило создать усовершенствованные 2-х электродные системы распыления –магнетронные распылительные системы. В них достигается 100% -я ионизация рабочего газа. Высокая скорость осаждения (десятки нм/с) пленок металлов, сплавов, полупроводников и диэлектриков.
Сравнительный анализ процесса ТВИ и И-ПР
преимущества И-ПР:
а) скорость распыления разных металлов и сплавов различается слабо, поэтому возникает возможность использовать И-ПР разных материалов, в том числе тугоплавких, полупроводников, а так же материалов с высоким содержанием окислов;
б) возможность получать пленки сложных материалов- керметов, нержавеющей стали, стекла, пермолоя;
в) возможность использовать мишени с большой площадью, что способствует получению равномерных по толщине пленок;
г) сухая финишная очистка подложек упрощается. Перед осаждением можно очистить подложку, подав на анод отрицательный потенциал;
д) малый расход материала мишени.
недостатки И-ПР:
а) по сравнению с ТВИ мала скорость роста пленок;
б) энергия атомов подлетающих к подложке ИПР на 1,2 порядка выше чем при термическом испарении. Это может вызывать дефекты структуры пленки;
в) ухудшает структуру пленок при И-ПР наличие в потоке атомов заряженных частиц;
г) т.к. процесс И-ПР идет при высоком давлении рабочего газа, то наличие атомов газа в пленке тоже выше, следовательно степень чистоты пленки меньше.
ТЕМА №5
Дата добавления: 2018-05-12; просмотров: 708; Мы поможем в написании вашей работы! |
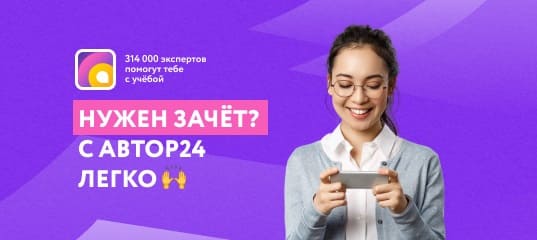
Мы поможем в написании ваших работ!