Требования, предъявляемые к электротехническим изотропным сталям.
В зависимости от назначения требования к стали дифференцируются. В одних случаях основное значение имеет уровень удельных потерь (крупные гидро- и турбогенераторы, крупные синхронные и асинхронные турбодви-гатели), в других – уровень удельных потерь и магнитной индукции (двига-тели и генераторы мощностью 100-1000 кВт, разнообразные реле, сварочное оборудование), в-третьих – уровень магнитной индукции в средних и силь-ных магнитных полях (малые асинхронные машины, статоры машин постоянного тока и др.).[2]
Магнитные свойства стали, определяемые согласно ГОСТ 12119-80 должны соответствовать нормам, указанным в табл.3.2.
Таблица 3.2
Магнитные свойства холоднокатаных электротехнических изотропных сталей
Марка стали | Толщина, мм | Удельные магнитные потери Р1,5/50, Вт/кг, не более | Магнитная индукция при напряженности магнитного поля 2500 А/м, В, Тл, не менее | Анизотропия магнитной индукции, ΔВ, Тл, не более. | Коэффициент анизотропии удельных магнитных потерь, %, не более | Коэф-фици-ент старе-ния,%, не более |
2211 | 0,5 | 5,5 | 1.56 | 0,13 | 12 | 6 |
2212 | 5,0 | 1.60 | ||||
2213 | 5,0 | 1,65 | ||||
2214 | 4,8 | 1,62 | ||||
2215 | 4,5 | 1,64 | ||||
2216 | 4,0 | 1,60 |
Магнитная индукция измеряется как среднее значение вдоль и поперек направления прокатки. Разница в значениях магнитной индукции при напряженности магнитного поля 2500 А/м вдоль и поперек направления прокатки не должна превышать для стали с содержанием Si до 1,8 % - 0,13 Тл.
|
|
При использовании любых марок электротехнической стали должна быть уверенность в неизменности её магнитных свойств в процессе эксплуатации.
Вследствие потерь энергии при перемагничивании магнитопроводов и тепловыделений, связанных с намагничивающими обмотками, имеет место нагрев стали, в процессе которого могут происходить фазовые превращения, приводящие к необратимому ухудшению магнитных свойств (старение стали).[3] Коэффициент старения Кс определяют на образцах после нагрева их в течении 120 ч при 120˚С по формуле:
Кс= {(Р1- Р0) / Р0} ´ 100%, (3.4)
где Р0 и Р1 – значение удельных потерь, измеренных до и после старения соответственно, Вт/кг.
Предельные отклонения по ширине рулонов и по ширине и длине листов не должны превышать ±0,5%. Предельные отклонения по ширине ленты должны соответствовать ГОСТ 21427-83.
Разнотолщинность листа и поперечная разнотолщинность рулона и ленты не должны превышать 1/2 суммы предельных отклонений по толщине.
На кромках стали не должно быть расслоений. Допускаются дефекты на кромках, не выводящие продукцию за пределы номинальных размеров.
|
|
Волнистость и коробоватость листов, существенно отклоняющие лист от плоскости, не допустимы, так как из недостаточно плоских листов не может быть собран плотный магнитопровод.
Коэффициент заполнения Кз определяют на образце, спрессованном по всей поверхности под давлением 490 кПа и составленном не менее чем из 100 пластин, взятых для определения магнитных свойств:
Кз=М / V · r, (3.5)
где М – масса образца, кг;
V – объем образца после пресования,м3;
r - плотность стали, кг/м3.
Коэффициент заполнения горячекатаной стали составляет 0,9-0,93; холоднокатаной 0,95-0,97. Чтобы оценить это различие, необходимо иметь в виду, что снижение Кз на 1% равномерно повышению удельных потерь на 2-3% и снижению магнитной индукции на 1-2 %.
Общим для всех марок стали является наличие на поверхности листов изоляционных слоев, снижающих потери на вихревые токи при эксплуатации магнитопроводов. Покрытия на листах электротехнической стали в зависимости от её назначения должны удовлетворять различным требованиям, касающимся электрического сопротивления, пробивного напряжения, термо- и химической стойкости. Существенной является толщина покрытия, влияющая на Кз магнитопровода сталью. Этот коэффициент является важной характеристикой, определяющей наряду с магнитными свойствами стали уровень технико-экономических показателей магнитопроводов машин и трансформаторов.[4] Физические и эксплуатационные свойства электроизоляционного покрытия должны соответствовать нормам, указанным в табл.3.3.
|
|
Прочность сцепления покрытия с металлом определяют путем изгиба образца на 908 вокруг стержня диаметром 20 мм. Электрическое сопротивление покрытия измеряется при давлении в контактах 450 МПа.
Таблица 3.3
Требования к электроизоляционному покрытию
Марка покрытия | Коэффициент сопротивления, Ом.см2, не менее | Термостойкость | Влияние на штампуемость | Основа покрытия |
Т1 Т5 | 1,0 5,0 | 760°С, 1,5 ч в защитной атмосфере или 700°С, 2 мин на воздухе | Не ухудшает | Неоргани-ческие |
ТШ1 ТШ10 ТШ20 ТШ40 | 1,0 10,0 20,0 40,0 | 760°С, 1,5 ч в защитной атмосфере | Улучшает
| Полуорга-ническое |
НШ1 НШ10 НШ20 НШ40 | 1,0 10,0 20,0 40,0 | 200°С, 24 ч на воздухе | Органичес-кое или полуорга-ническое |
Дата добавления: 2018-05-12; просмотров: 311; Мы поможем в написании вашей работы! |
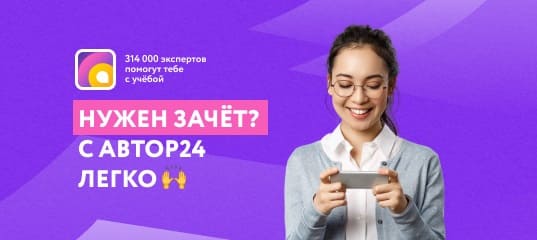
Мы поможем в написании ваших работ!