Описать схему автоматизации функциональную ГЗУ «Спутник».
Описание технологического процесса и технологической схемы установки
Краткое описание технологических процессов установки АГЗУ.
Основными технологическими процессами на технологических площадках установки АГЗУ являются:
-замер дебита скважин
-сепарация;
-подогрев нефти;
-откачка разгазированной нефти насосами на УПН;
-подача газа сепарации на УПН;
-впрыск ингибитора коррозии в нефтяной поток к УПН.
На АГЗУ предусмотрен замер дебита скважины, 1-ая ступень сепарации, подогрев нефти и раздельный транспорт нефти и газа по самостоятельным трубопроводам на объекты подготовки. Процесс сепарации происходит непрерывно за счёт диффузии растворённых в нефти молекул газа в пространство над нефтью.
Наавтоматизированной групповой замерной установки АГЗУ модель «Спутник АМ-40-14-400» производится автоматическое поочередное определение дебита скважин по нефти и газу, а также дляблокировка скважин при возникновении аварийных ситуаций.
Описание технологической схемы установки АГЗУ.
Технологическая схема групповой замерной установки АГЗУ, оборудованной установкой блочной сепарационной (УБС)
Газожидкостная смесь (ГЖС) поступает с эксплуатационных скважин на АГЗУ “Спутник”- АМ-40-14-400 (1,2).
Автоматизированные групповые установки (АГЗУ) “СпутникАМ-40-14-400”предназначеныдляизмерениядебитажидкостиигаза, эксплуатационных скважин в системах группового сбора, в которых продукция каждой скважины направляется на групповую установку по одному трубопроводу (выкидной линии).
|
|
АГЗУ “Спутник АМ-40-14-400”можно классифицировать следующим образом:
-по методу измерения: объемный;
-по устройству переключения на замер: с многоходовым переключателем скважин (ПСМ);
-по режиму измерения: накопительный, импульсный с поочередным подключением на замер;
-по числу замеряемых параметров: однопараметровый.
В указанных шифрах первое число рабочее давление (40 кГ/см2), на которое рассчитана установка, второе - число подключенных к ней скважин (14) и третье - наибольший дебит (400 м3/сут) измеряемой скважины.
Продукция одной эксплуатационной скважины через ПСМ поступает в замерной гидроциклонный двухёмкостный сепаратор, установленный в “Спутнике”, в котором происходит отделение газа от жидкости (нефть+вода) и замеряется их количество по каждой скважине отдельно. Продукция остальных скважин через ПСМ по сборному коллектору транспортируется в блок УБС. В “Спутнике” предусмотрен счетчик газатурбинный“АГАТ-IМ-65”, предназначенныйдляизмеренияпопутногогазасцельюосуществленияоперативногоконтролязарежимами эксплуатации нефтяных скважин. В шифре 65-обозначает диаметр условного прохода в мм. Отсепарированный газ после замера через счетчика “АГАТ”вновь смешивается с жидкостью и вместе с продукцией остальных скважин транспортируется по сборному коллектору в блок двухфазного сепаратора (БС-2400-1,6) , где при давлении 0,1- 0,2 МПа осуществляется I-ая ступень сепарации.
|
|
Блок двухфазного сепаратора типа БС-2400-1,6 предназначен для первой ступени сепарации нефтяного газа от жидкости, с одновременным оперативным учетом их расходов в системах герметизированного сбора и транспорта продукции эксплуатационных скважин.
В шифре установки принято следующее обозначение: БС- блок двухфазного сепаратора; первое число - диаметр аппарата (2400 мм); второе расчетное давление (16 атмосфер). В блок входят; сепаратор, депульсатор, площадка обслуживания, комплектующие изделия и средства КИПиА.
Отсепарированный газ по самостоятельному трубопроводу O159х5мм через узел учёта газа поступает на факельную линию через задвижку или в коллектор выдачи газа сепарации на установку УПН через счетчик газа СГ - 16М200 и задвижку.
Счетчик СГ - 16М200, предназначен для замера газа, отсепарированного в БС.
Дегазированная жидкость из блочной сепарационной установки (УБС) откачивается через задвижки поршневыми насосами типа НБ-125/1,2 или центробежным насосом ЦНС-38/176/1 через путевой подогреватель типа ПП-0,63 в нефтесборный коллектор на УПН через фильтр и счетчик жидкости.
|
|
Путевой подогреватель типа ПП-0,63 представляет собой блочную печь с промежуточным водяным теплоносителем.
В технологической схеме АГЗУ дополнительно предусмотрены дренажные емкости с электронососным агрегатом для сбора дренажей с оборудования АГЗУ.
Центробежный насос типа НВ-50/50 - предназначен для откачки жидкости из дренажной емкости в нефтесборный трубопровод выхода жидкости из Спутника-1,2 на вход в сепаратор УБС. В тот же трубопровод врезана линия горячей циркуляции нефтяной жидкости от печи ПП-0,63.
Путевой подогреватель типа ПП-0,63 - предназначен для подогрева пластовой жидкости, откачиваемой поршневыми насосами в нефтесборный коллектор.
Счетчик “НОРД” - предназначен для учета объема жидкости, откачиваемого поршневыми насосами в напорный коллектор.
Для регулирования давлений (в аварийных случаях) на блочной сепарационной установке, на гидроциклонном сепараторе “СпутникаАМ-40-8-400”установлены предохранительные клапаны, отводящие трубы которых выведены на дренажную линию, а из гидроциклонного сепаратора - в дренажный колодец.
|
|
В зимнее время года, для предотвращения застывания нефти в технологический цикл “печь подогрева>спутник>поршневой насос”подается подогретая нефтьдо 50-55Споциркуляционнойлиниичереззадвижки.
Система контроля и автоматизация технологического процесса
На АГЗУ установлена система КИПиА, которая предназначена для поддержания заданных значений параметров технологического режима, предотвращения возникновения аварийных ситуаций, для оперативного учёта и контроля уровней жидкости и управления процессом откачки жидкости насосами для раздельного замера дебита скважин, суммарного учёта жидкости и газа. замерный установка автоматический газ
Для автоматического контроля уровней жидкости в УБС и управления процессом откачки применяется ультразвуковой прибор типа XPS 10 ECHOMAX. Управление насосами откачки можно также, при необходимости, осуществлять на ручном режиме кнопками “Пуск”и“Стоп”щита управления. Все сигналы идущие от точек контроля насосами откачки поступают на вторичные показывающие приборы, установленные на щите управления в операторной АГЗУ. Сигналы на щите выдаются в виде цифровой и световой индикации.
Давление жидкости и газа в трубопроводах, аппаратах, приёмно-выкидных линиях насосов контролируется техническими манометрами. Температура газожидкостной смеси контролируется термометрами.
Система КИПиА подогревателя ПП-0,63.
На входе нефти в ПП-0,63 производится контроль давления по манометрам, по месту.
Температура воды в ПП-0,63 контролируется стеклянным ртутным термометром.
Подогреватель нефти ПП-0,63 оснащен приборами контроля, управления и автоматического регулирования, обеспечивающими:
-технологический контроль:
-давления (манометрами показывающими сигнализирующими взрывобезопасными ДМ);
-температуры (манометрическим показывающим термометром ТКП);
-уровня теплоносителя внутри сосуда (ДРУ-1ПМ);
-автоматическое регулирование:
-температуры (РТ-ДО-50);
-давление топливного газа перед горелкой и запальником;
-автоматическое отключение подачи топлива к горелкам с расшифровкой и запоминанием первопричины в соответствии со СНиП 11-35-76 в случае:
- повышения давления газообразного топлива перед горелками;
- понижения давления топливного газа перед горелками;
- погасания факелов горелок;
- повышения температуры теплоносителя;
- повышения давления в змеевике.
Указанные параметры контролируются:
- манометрами показывающими сигнализирующими МП-4-1У;
- преобразователями ультрафиолетового излучения ПУИ;
-автоматический переход с режима большого на малое горение и обратно;
-автоматический переход из режима розжига в режим автоматического контроля технологических параметров;
-автоматический контроль неисправности преобразователя ультрафиолетового излучения.
Система автоматики печи снабжена блоком БУК-5.С помощью указанных блока осуществляется управление работой печи, защита, сигнализация и блокировка при отклонениях параметров работы печи от нормы.
Примечание: Регулировку системы автоматики печей см. схему автоматики в Паспорте на печь ПП-0,63 поставщика оборудования. Эскиз печи ПП-0,63 с промежуточным теплоносителем представлен на рис. 2 в приложении к документу.
Описание схемы подачи ингибитора коррозии (БР-2,5)
Для впрыска ингибитора коррозии на АГЗУ применены блоки дозирования реагента (модель БР-2,5).
Краткая характеристика блока БР-2,5
В блоке БР-2,5 смонтированы:
-безнапорный расходный бак, оснащенный электрическим обогревателем (при наличии такового);
-насос шестеренчатый;
-насос дозировочный.;
-технологические трубопроводы с запорно-регулирующей арматурой, первичными приборами КИПиА.
Дозировочные блоки выполняют следующие функции:
-прием концентрированного химреагента из бочек в бак;
-подогрев химреагента в баке (при условии комплектации);
-дозированная подача химреагента в трубопровод.
Система контроля и автоматики блоков дозирования реагента предусматривает:
-местный контроль уровня и температуры химреагента в баке (поз.LIA, LA,TA);
-автоматическое управление электрическим обогревателем СЭМ-ЗУЗ для поддержания температуры реагента по сигналам датчика температуры (контур TISA) в пределах от +20 до +60оС (при условии комплектации);
-автоматическое отключение дозировочных насосов при повышении давления нагнетания выше установленного (контур PISA), при снижении уровня химреагента в баке ниже допустимого (контур LSA), включение аварийной вытяжной вентиляции при повышении концентрации горючих газов в блоке до 10%НКПВ (контур QISA), отключение электропитания при пожаре, при Т=70оС (контур TSA).
-защиту всех электроприемников от короткого замыкания и перегрузок.
Электрооборудование и средства КИПиА применены во взрывозащищенном исполнении. Все оборудование установки БР-2,5 смонтировано в теплоизолированном блоке, установленном на сварной раме-санях. В будке блока предусмотрено освещение, автоматический обогрев, вытяжная и приточная вентиляция.
Будка герметической перегородкой разделена на два отсека - технологический и приборный.
Емкость технологическая заполняется реагентом из бочек или от передвижной емкости (автоцистерны) или из герметичных бочек объемом 200 л с помощью заправочного насоса блочной установки.
После заполнения технологической емкости включается насос-дозатор, устанавливается расход подачи ингибитора коррозии в нефтесборный коллектор на входе сырой нефти в УБС. Расход ингибитора коррозии устанавливается на основании рекомендаций производителя, научных организаций, испытывающих реагент в лабораторных и промысловых условиях и опыта применения реагента.
В емкости технологической имеется местный указатель уровня.
Предусмотрено аварийное отключение дозировочного насоса, электронагревателя реагента, автоматическое управление вытяжным вентилятором (при наличии).
Кислотная обработка скважин.
Кислотные обработки скважин предназначены для очистки забоев, призабойной зоны, НКТ от солевых, парафинисто-смолистых отложений и продуктов коррозии при освоении скважины с целью их запуска, а так же для увеличения проницаемости пород. Под воздействием соляной кислоты в породах ПЗС образуются пустоты, каверны, каналы разъедания, вследствие чего увеличивается проницаемость пород, а следовательно и производительность нефтяных (газовых) и приемистость нагнетательных скважин.
Различают следующие разновидности кислотных обработок:
Кислотные ванны предназначены для очистки поверхности открытого забоя и стенок скважины от цементной и глинистой корок, смолистых веществ, продуктов коррозии, кальциевых отложений от пластовых вод и освобождения прихваченного пробкой подземного оборудования. Объем рабочего раствора, при кислотной ванне, составляет не более объема ствола (колонны) в заданном интервале, закачивают его до забоя, не продавливая в пласт. Раствор кислоты выдерживают в интервале обработки 16 - 24 ч. Затем отреагировавшую кислоту вместе с продуктами реакции удаляют из скважины обратной промывкой. В качестве промывочной жидкости используют воду. Простая кислотная обработка предназначена для воздействия на породы ПЗС с целью увеличения их проницаемости. Процесс ведется с обязательным задавливанием кислоты в пласт. Вначале закачивают нефть или воду, затем при открытом затрубном пространстве - расчетное количество приготовленного рабочего раствора соляной кислоты. При этом объем первой порции кислоты рассчитывают так, чтобы она заполнила трубы и кольцевое пространство от башмака до кровли пласта. После этого закрывают задвижку на затрубном пространстве скважины и под давлением закачивают в скважину остатки кислотного раствора. Кислота начинает проникать в пласт. Оставшуюся в трубах и в фильтровой части скважины кислоту продавливают в пласт нефтью или водой.
Кислотная обработка под давлением применяют с целью продавки кислоты в малопроницаемые интервалы продуктивного пласта. Проводят с применением пакера.
При открытой задвижке затрубного пространства скважины и непосаженом пакере в скважину закачивают кислотный состав в объеме труб и подпакерного пространства, после чего пакером герметизируют затрубное пространство и закачивают кислоту в объеме спущенных труб с максимальным повышением темпа закачки. Затем, не снижая давления, вслед за кислотой прокачивают расчетный объем продавочной жидкости и закрывают задвижку. Скважину оставляют в покое до полного спада или стабилизации давления. Пенокислотные обработки применяют при значительной толщине пласта и низких пластовых давлениях. В призабойную зону скважины вводя аэрированный раствор кислоты и ПАВ в виде пены. При таких обработках используют кислотный агрегат, компрессор и аэратор. Пенокислотная обработка имеет следующие преимущества:
Ø Кислотная пена медленнее растворяет карбонатный материал, что способствует более глубокому проникновению активной кислоты в пласт.
Ø Кислотная пена обладает меньшей плотностью и повышенной вязкостью, что позволяет увеличить охват воздействием всей продуктивной толщины пласта.
Ø Содержание в пене ПАВ снижает поверхностное натяжение кислоты на границе с нефтью, а сжатый воздух, находящийся в пене, расширяется во много раз при понижении давления после обработки; все это в совокупности способствует улучшению условий притока нефти в скважину и значительно облегчает ее освоение.
Многократные обработки заключаются в том, что ПЗС обрабатывают несколько раз с интервалами между обработками в 5 - 10 суток с целью вывода скважины на максимальную производительность за короткий срок. Поинтервальные (ступенчатые) обработки нескольких интервалов пласта значительной толщины с целью полного охвата пласта или отдельных продуктивных пропластков.
После обработки первого интервала и кратковременной его эксплуатации, принудительно-направленным способом воздействует интервал, пока полностью не будет охвачена вся толщина пласта. Проводить ступенчатые обработки целесообразно в скважинах после выхода их из бурения или в начальный период эксплуатации.
Термохимические обработки - обработки скважин горячей соляной кислотой, с магнием в специальном наконечнике, спущенном на НКТ в пределы интервала, намеченного под обработку. Применяют для очистки ПЗС от асфальто-смолистых, парафиновых и других материалов.Термокислотные обработки - комбинированный процесс, в первой фазе которого осуществляется термохимическая обработка, во второй (без перерыва во времени) - обычная, простая СКУ. Наполненный магнием наконечник спускают на трубах в скважину и устанавливают в зоне обрабатываемого интервала пласта. Затем закачивают нефть и вслед за ней, без перерыва, 15% раствор соляной кислоты. Скорость прокачки кислоты должна быть такой, чтобы в течение всего процесса на выходе наконечника была одинаковая запланированная температура и постоянная кислотность раствора. Для загрузки наконечника используют магний в виде стружек или брусков квадратного или круглого сечения.
Дата добавления: 2018-05-12; просмотров: 1147; Мы поможем в написании вашей работы! |
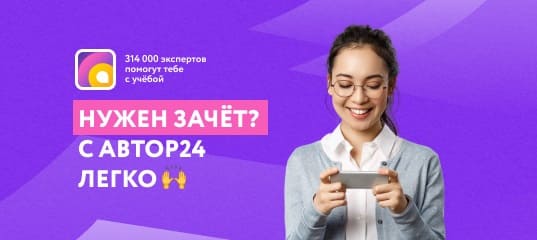
Мы поможем в написании ваших работ!