Конструктивная характеристика и анализ нагрузочной способности цилиндрического зубчатого редуктора
Министерство образования и науки Республики Казахстан
Карагандинский государственный технический университет
Им В.А., Апачиди Н.К., Бударагина А.А., Надобенко Е.А.
МЕТОДИЧЕСКИЕ УКАЗАНИЯ
К ЛАБОРАТОРНЫМ РАБОТАМ
ПО ДИСЦИПЛИНАМ
«Основы конструирования и детали машин»,
«Основы конструирования и автоматизации проектирования»,
«Детали машин и основы конструирования»
Караганда 2009
Министерство образования и науки Республики Казахстан
Карагандинский государственный технический университет
Кафедра систем автоматизированного проектирования
Им В.А., Апачиди Н.К., Бударагина А.А., Надобенко Е.А
МЕТОДИЧЕСКИЕ УКАЗАНИЯ
к лабораторным работам по дисциплинам
«Основы конструирования и детали машин»,
«Основы конструирования и автоматизации проектирования»,
«Детали машин и основы конструирования»
для студентов специальностей
050704 «Вычислительная техника и программное обеспечение»,
050712 «Машиностроение»,
050724 «Технологические машины и оборудование»,
050713 «Транспорт, транспортная техника и технологии»
Форма обучения: дневная
Караганда 2009
УДК 621.74.004.12
Им В.А., Апачиди Н.К., Бударагина А.А., Надобенко Е.А Методические указания к лабораторным работам по дисциплинам «Основы конструирования и детали машин», «Основы конструирования и автоматизации проектирования», «Детали машин и основы конструирования»
|
|
Караганда: КарГТУ, 2009. 46 с.
Методические указания составлены в соответствии с требованиями учебного плана и программой дисциплины «Основы конструирования и детали машин» и включает все необходимые сведения по выполнению тем лабораторных работ курса.
Методические указания предназначены для студентов специальностей 050704 «Вычислительная техника и программное обеспечение», 050712 «Машиностроение», 050724 «Технологические машины и оборудование», 050713 «Транспорт, транспортная техника и технологии»
Рецензент - член Редакционно-издательского совета КарГТУ
_______________________________________
Утверждено Редакционно-издательским советом университета
© Карагандинский государственный технический университет, 2009
Содержание
Введение 5
Лабораторная работа №1 9
Лабораторная работа №2 22
Лабораторная работа №3 34
|
|
Список рекомендуемой литературы 45
Введение
Редуктором называется механическая передача, выполненная в виде самостоятельного агрегата. Судя по переводу с латинского, редуктор должен понижать частоту вращения, подаваемую на его входной (ведущий) вал, одновременно повышая вращающий момент на выходном (ведомом) валу.
Однако, если ведомый вал редуктора сделать ведущим, а ведущий — ведомым, получается агрегат, называемый мультипликатором, который повышает подаваемую на ведущий вал частоту вращения, понижая при этом вращающий момент.
Внешне редуктор и мультипликатор не отличаются друг от друга, но редукторы применяются гораздо чаще, так как двигатели, приводящие входной вал в движение, имеют обычно частоту вращения, существенно превышающую необходимую для приводимого рабочего органа той или иной машины. Поэтому во всех случаях будем использовать термин «редуктор», имея в виду и мультипликатор.
Редукторы состоят из закрытых механических передач, установленных в герметичном корпусе со своей системой смазки, ее контроля, возможно охлаждения, вентиляции и т.д. Разновидностей редукторов очень много, чаще всего — это зубчатые и червячные редукторы, которые имеют преимущественное применение. Планетарные и волновые редукторы находят все большее распространение в технике. Соединение редукторов с двигателем и рабочей машиной осуществляется с помощью различных муфт, ременных и цепных передач.
|
|
Следует заметить, что широко применяются редукторы, выполненные в одном агрегате с электромотором, — мотор-редукторы. Мотор-редукторы имеют меньшие габаритно-массовые показатели и большую экономичность по сравнению с тихоходными высокомоментными электродвигателями с равным вращающим моментом на выходе и системами, состоящими из отдельного электродвигателя, соединенного с редуктором муфтой или механической открытой передачей.
Редукторы классифицируют по типам, типоразмерам и исполнениям. Тип редуктора определяется по виду применяемых передач, порядку их размещения от входного вала к выходному, по числу ступеней, расположению оси выходного вала.
В зависимости от применяемых передач редукторы обозначаются русскими буквами: Ц — цилиндрические; К — конические; Ч — червячные; Г — глобоидные; П — планетарные; В — волновые; КЦ — коническо-цилиндрические; ЧЦ — червячно-цилиндрические; ЦЧ — цилиндрическо-червячные.
|
|
В зависимости от числа ступеней редукторы делятся на одноступенчатые, двухступенчатые, трехступенчатые. Если число одинаковых передач (например, цилиндрических или червячных) две и более, то в обозначении редуктора после буквы ставят соответствующую цифру. На рисунках 1 и 2 изображены основные типы одноступенчатых и двухступенчатых редукторов.
а — горизонтальный цилиндрический; б — вертикальный цилиндрический; в — горизонтальный конический; г — конический редуктор с вертикальным тихоходным валом; д — червячный с нижним расположением червяка; в — червячный с верхним расположением червяка; Б — быстроходный вал; Т — тихоходный вал
Рисунок 1 – Одноступенчатые редукторы
Широкие редукторы обозначают буквой Ш, узкие — У, соосные — С; в мотор-редукторах к обозначению впереди добавляют букву М (например, МП — мотор-редуктор планетарный).
В зависимости от расположения оси выходного вала в пространстве бывают редукторы горизонтальные, вертикальные, универсальные. Наиболее распространены горизонтальные редукторы, поэтому они особого обозначения не имеют. Если все валы редуктора расположены вертикально, то добавляется индекс В. Если ось тихоходного вала вертикальна, добавляют индекс Т, если быстроходного — Б.
Типоразмер редуктора определяют тип и главный параметр тихоходной ступени. Для цилиндрической, червячной (глобоидной) передач главным параметром является межосевое расстояние; для конической — внешний делительный диаметр колеса de2; для планетарной — радиус водила Rw; для волновой — внутренний диаметр гибкого колеса d в недеформированном состоянии. Все размеры даются в миллиметрах.
Исполнение редуктора определяется по передаточному отношению, варианту сборки, форме концевых участков валов (коническая, цилиндрическая).
а — горизонтальный цилиндрический по развернутой схеме; б — горизонтальный цилиндрический соосный; в — вертикальный цилиндрический соосный; г — горизонтальный коническо-цилиндрический; Б — быстроходный вал; Т —тихоходный вал
Рисунок 2 – Двухступенчатые редукторы
Для силовых характеристик основное значение имеет вращающий момент Т2 на выходном (тихоходном) валу.
Показателем технического уровня редуктора является удельная масса у — отношение массы редуктора, кг, к номинальному вращающему моменту Т2, Н-м. Чем меньше у, тем выше технический уровень редуктора.
Например, значения у, кг/(Н-м), для одноступенчатых редукторов при Т2 = 315 Н-м равны: для червячного — 0,14; конического — 0,12; цилиндрического — 0,095; планетарного — 0,085; волнового — 0,063; для двухступенчатых редукторов при Т2 = 1000 Н-м: коническо-цилиндрического — 0,1; цилиндрического по развернутой схеме — 0,085; соосного — 0,07. В конструкциях редукторов с высокотвердыми поверхностями зубьев можно получить у = = 0,03...0,05 кг/(Н-м).
Среди типов редукторов следует отдавать предпочтение цилиндрическим редукторам из-за их простоты, распространенности, достаточно низкой стоимости и высокого КПД. Весьма перспективными являются планетарные и волновые редукторы, находящие все большее применение в современной технике.
Корпуса (картеры) редукторов должны быть прочными и жесткими. Внешние очертания должны быть простыми; для удобства сборки корпуса выполняют разъемными по плоскости расположения валов. Корпуса редукторов, выпускаемых большими сериями, изготовляют литьем из чугуна или алюминиевых сплавов. В индивидуальном или мелкосерийном производстве используют сварные корпуса. В качестве опор валов редукторов применяют подшипники качения соответствующих типов.
Большое значение имеет смазывание передач в редукторе. В большинстве случаев смазывание зацеплений осуществляется погружением в масляную ванну, а подшипников — масляным туманом, образующимся при разбрызгивании масла при окружных скоростях колес свыше 3 м/с.
При больших окружных скоростях, свыше 12 м/с, применяют другие способы смазывания. В большой степени это касается планетарных передач, где детали водила и сателлиты создают большие потери при смазке погружением.
Вязкость масла назначается тем выше, чем больше значения контактных напряжений и меньше окружные скорости. Смазка должна периодически заменяться.
ЛАБОРАТОРНАЯ РАБОТА №1.
Конструктивная характеристика и анализ нагрузочной способности цилиндрического зубчатого редуктора
Цель и задачи работы – изучение конструкции типовых цилиндрических зубчатых редукторов, определение и анализ их кинематических, геометрических и силовых параметров.
1 Порядок выполнения работы
1.1 Знакомство с конструкциями цилиндрических редукторов
Ознакомление с основными элементами классификации и конструкций редукторов производится по натуре, атласам и справочникам:
1) Корпусные детали: основание, крышка, люки; способы соединения их друг с другом, а также редуктора с рамой (диаметры отверстий для болтов, их расположение и расстояние между осями).
2) Детали зубчатого зацепления: шестерни, колеса, валы, шпоночные и шлицевые соединения.
3) Подшипники валов, крышки и уплотнения. Способы регулировки подшипниковых узлов.
4) Смазка редуктора: способ заливки, слива и контроль уровня масла; способ смазки зацепления и подшипников. Устройство отдушин.
5) Приспособления для подъема редукторов при транспортировке и монтаже: рым-болты, проушины, захваты.
Дать краткую характеристику данного редуктора, пользуясь основными элементами классификации; проанализировать преимущества и недостатки данной схемы в сравнении с другими.
Начертить кинематическую схему редуктора с указанием чисел зубьев колес и частот вращения валов.
1.2 Определение и расчет кинематических и геометрических параметров одной ступени редуктора (по указанию преподавателя)
Определить замером с помощью штангенциркуля и линейки параметры зубчатых колес (см. таблицу 1 и рисунок 1).
Таблица 1 – Замеренные геометрические параметры цилиндрических зубчатых колес
Наименование параметра | Обозначение | Величина |
1 | 2 | 3 |
Число зубьев шестерни | ![]() | |
Ширина венца шестерни, мм | ![]() |
Продолжение таблицы 1
1 | 2 | 3 |
Диаметр вершин зубьев шестерни, мм | ![]() | |
Диаметр впадин зубьев шестерни, мм | ![]() | |
Число зубьев колеса | ![]() | |
Ширина венца колеса, мм | ![]() | |
Диаметр вершин зубьев колеса, мм | ![]() | |
Диаметр впадин зубьев колеса, мм | ![]() | |
Угол наклона зубьев, град | ![]() | |
Межосевое расстояние, мм | ![]() | |
Диаметр вала колеса | ![]() |
Рисунок 1 – замеряемые геометрические параметры цилиндрического зубчатого колеса
Определить расчетами геометрические параметры цилиндрических колес. Значение параметров вычислять с точностью до сотых
1.2.1 Определение окружного и нормального модулей зацепления:
, мм (1.1)
, мм (1.2)
Полученное значение нормального модуля принимается по ГОСТ 9563-66 из ряда:
1-й ряд:1; 1,25; 2; 2,5; 3; 4; 6; 8; 10; 12; 16; 20;
2-й ряд: 1,375; 1,75; 2,25; 2,75; 3,5; 4,5; 7; 9; 11; 14; 18; 22.
Примечание: 1-й ряд следует предпочитать 2-му.
1.2.2 Уточнение угла наклона зубьев:
, (1.3)
Значение косинуса угла наклона зубьев определяется с точностью до четвертого знака после запятой.
1.2.3 Определение диаметров делительных окружностей (определяется для шестерни и колеса, значения округляются до сотых):
– для прямозубой передачи:
, (1.4)
– для косозубой передачи:
, (1.5)
1.2.4 Проверка межосевого расстояния:
, (1.6)
1.2.5 Определение диаметров окружностей вершин (определяется для шестерни и колеса):
, (1.7)
1.2.6 Определение диаметров окружностей впадин (определяется для шестерни и колеса):
, (1.8)
Полученные расчетные значения и
сравнивают с замеренными. При совпадении подсчитанных и измеренных значений диаметров (при расхождении
мм) – передача нарезана без смещения (
), при несовпадении – имеет место нарезание колес со смещением. В этом случае расчет геометрических параметров зубчатых колес со смещением производится по формулам, представленным в таблице 2.
Таблица 2 – Основные геометрические соотношения в передачах внешнего зацепления цилиндрических зубчатых колес, выполненных со смещением
Параметры зацепления | Прямозубые передачи | Косозубые передачи |
Коэффициент смещения исходного контура | ![]() | ![]() |
Здесь диаметры | ||
Коэффициент уравнительного смещения (только при ![]() | ![]() | ![]() |
Модуль зацепления | ![]() | ![]() |
Здесь | ||
Делительные диаметры | ![]() | ![]() |
Диаметры вершин зубьев (должны совпадать с замеренными) | ![]() | ![]() |
Диаметры впадин зубьев (должны совпадать с замеренными) | ![]() | ![]() |
Расчетное значение межосевого расстояния (должно совпадать с замеренным) | ![]() | ![]() |
1.3 Определение нагрузочных параметров редуктора и усилий в зацеплении
1.3.1 Исходные данные:
а) частота вращения ведущего вала: n1=1440 об/мин;
б) передача реверсивная или нереверсивная (принимает студент);
в) материалы шестерни и колеса, термообработка задаются в следующих сочетаниях:
1-й вариант:
шестерня – сталь 40ХН, улучшенная, НВ 270,
колесо – сталь 40ХН, нормализованная, НВ 240.
2-й вариант:
шестерня – сталь 40Х, нормализованная НВ 240,
колесо – сталь 50, нормализованная, НВ 210.
3-й вариант:
шестерня – сталь 45, нормализованная НВ 220;
колесо – сталь 40, нормализованная НВ 190.
4-й вариант:
шестерня – сталь 40ХН, закалка, HRC 54,
колесо – сталь 40ХН, закалка HRC 50.
1.3.2 Определение допускаемых контактных напряжений , определяется для шестерни
и колеса
(работа длительная NHE > NHO – эквивалентное число циклов перемены напряжений больше базового):
,МПа (1.9)
где – предел контактной выносливости поверхностей зубьев, соответствующий базовому числу циклов перемены напряжений, определяется для шестерни и колеса по формуле 1.10 или 1.11:
– при твердости :
,МПа (1.10)
– при твердости >
:
,МПа (1.11)
– коэффициент безопасности, принимается
(при
) и
(при
>
);
– коэффициент, учитывающий шероховатость сопряженных поверхностей зубьев, принимается
(при
);
– коэффициент долговечности, учитывающий влияние срока службы и режима нагрузки передачи (в лабораторных работах принимается
).
Для прямозубых колес в качестве расчетного допускаемого напряжения бHP принимают меньшее (обычно по колесу). Для косозубых колес бHP определяется по формуле:
,МПа (1.12)
где – допускаемое контактное напряжение для колеса;
– допускаемое контактное напряжение для шестерни.
1.3.3 Определение допустимого крутящего момента на ведомом валу (валу колеса; значения ,
– в мм,
– в МПа). Вычисляется для четырех вариантов в зависимости от значения допускаемых контактных напряжений по формуле:
, Н.м (1.13)
где – передаточное число зубчатой пары, определяется по формуле:
, (1.14)
– коэффициент нагрузки, определяется по формуле:
, (1.15)
где – коэффициент, учитывающий распределение нагрузки между прямыми зубьями, зависит от окружной скорости и степени точности колеса.
Определяется окружная скорость по формуле:
, м/с (1.16)
где – делительный диаметр шестерни, мм.
В зависимости от окружной скорости колес, принимается необходимая степень точности передачи по таблице 3.
Таблица 3 – Ориентировочные рекомендации по выбору степени точности передачи для цилиндрических зубчатых колес
Степень точности | Окружная скорость до м/с | Область применения | |
для прямозубых колес | для косозубых колес | ||
7-я (точные передачи) | 8 | 12,5 | Передачи, работающие с повышенными скоростями и умеренными нагрузками, или наоборот |
8-я (передачи средней точности) | 5 | 8 | Передачи общего машиностроения, не требующие особой точности |
9-я (передачи пониженной точности) | 2 | 3,5 | Тихоходные передачи с пониженными требованиями к точности |
Определяется значение коэффициента по таблице 4.
Таблица 4 – Значения коэффициента
Степень точности | Окружная скорость | |||
до 5 | 5…10 | 10…15 | 15…20 | |
6 | 1,02 | 1,03 | 1,04 | 1,05 |
7 | 1,04 | 1,07 | 1,1 | 1,12 |
8 | 1,09 | 1,13 | –– | –– |
9 | 1,16 | –– | –– | –– |
Примечание.Для прямозубых колес |
– коэффициент, учитывающий распределение нагрузки по ширине венца, зависит от твердости материала, расположению колес относительно опор, коэффициента
и определяется по таблице 5.
Таблица 5 – Значения коэффициента
Расположение колес относительно опор | |
| ||||||
![]() | 0,4 | 0,8 | 1,2 | 1,6 | 0,4 | 0,8 | 1,2 | 1,6 |
Симметрично | 1,02 | 1,05 | 1,1 | 1,15 | 1,08 | 1,08 | 1,15 | 1,25 |
Несимметрично | 1,08 | 1,12 | 1,15 | 1,28 | 1,13 | 1,28 | 1,5 | –– |
Консольно | 1,17 | 1,4 | –– | –– | 1,45 | –– | –– | –– |
– динамический коэффициент, (зависит от окружной скорости), в рамках данной лабораторной работы принимается
.
1.3.4 Построить график зависимости:
, (1.17)
Для этого полученные значения крутящих моментов на валу колеса и допускаемые контактные напряжения
по вариантам заносятся в таблицу 6.
Таблица 6 – Параметры для построения графика
Параметры | Значения по вариантам | |||
1 | 2 | 3 | 4 | |
Крутящий момент на валу колеса ![]() | ||||
Допускаемое контактное напряжение ![]() |
1.3.5 Определение мощности, которую может передать зубчатая передача:
,кВт (1.18)
где – угловая скорость колеса, определяется по формуле:
,рад/с (1.19)
где – частота вращения ведомого вала (вала колеса), определяется по формуле:
,об/мин (1.20)
1.3.6 Определение сил, действующих в зацеплении зубьев рассматриваемой передачи:
– окружная сила:
, Н (1.21)
– радиальная сила:
, Н (1.22)
где – угол зацепления,
.
– осевая сила:
,Н (1.23)
1.3.7 Определение допускаемых напряжения на выносливость зубьев при изгибе (определяется для шестерни и колеса):
,МПа (1.24)
где – предел выносливости зубьев при изгибе, соответствующий базовому числу циклов перемены напряжений:
– при твердости ,
определяется оп формуле:
,МПа (1.25)
– при твердости >
, принимается
МПа (меньшее значение принимается для колеса, большее – для шестерни);
- коэффициент безопасности, определяется по формуле:
, (1.26)
где – коэффициент, учитывающий нестабильность свойств материалов: при изготовлении зубчатых колес из углеродистых и легированных сталей нормализованных или улучшенных
, при использовании закаленных материалов
(в рамках данной лабораторной работы материал и вид термообработки определяются вариантом студента);
– коэффициент, учитывающий способ получения заготовки: для поковок и штамповок
, для проката
, для литых заготовок
(в рамках данной работы студент сам выбирает способ получения заготовки);
– (реверсивный) коэффициент, учитывающий реверсивность работы передачи (студент сам выбирает реверсивность передачи):
(при нереверсивной передачи),
(при реверсивной передачи и
),
(при реверсивной передачи и
>
); в рамках данной лабораторной работы принимается, что зубчатая передача нереверсивная;
- коэффициент долговечности, учитывающий срок службы и режим нагрузки передачи, в рамках данной лабораторной работы принимается
.
– коэффициент, учитывающий шероховатость переходной поверхности зубьев: для шлифования и зубофрезерования при шероховатости не ниже
принимается
, для полирования при нормализации и улучшении
(в рамках данной лабораторной работы принять
).
1.3.8 Проверка прочности зубьев на выносливость при изгибе
Сравнительная оценка прочности зубьев на изгиб осуществляется по формуле:
, (1.27)
где – коэффициент нагрузки, определяется по формуле:
, (1.28)
где – коэффициент, учитывающий неравномерность распределения нагрузки по длине зуба (коэффициент концентрации нагрузки), зависит от коэффициента
, твердости рабочих поверхностей зубьев, расположению зубчатых колес относительно опор и определяется по таблице 7.
Таблица 7 – Значения коэффициента
| Твердость поверхности зубьев | |||||
|
| |||||
I | II | III | I | II | III | |
1 | 2 | 3 | 4 | 5 | 6 | 7 |
0,2 0,4 | 1,00 1,03 | 1,04 1,07 | 1,18 1,37 | 1,03 1,07 | 1,05 1,10 | 1,20 1,45 |
0,6 0,8 1,0 1,2 1,4 1,6 1,8 | 1,05 1,08 1,10 1,13 1,19 1,25 1,32 | 1,12 1,17 1,23 1,30 1,38 1,45 1,53 | 1,62 –– –– –– –– –– –– | 1,09 1,13 1,20 1,30 1,40 –– –– | 1,18 1,28 1,40 1,53 –– –– –– | 1,72 –– –– –– –– –– –– |
Примечание. Данные, приведенные в столбце I, относятся к передачам с консольным расположением зубчатого колеса; II – к передачам с несимметричным расположением колес по отношению к опорам; III – к передачам с симметричным расположением. |
– коэффициент, учитывающий динамическое действие нагрузки (коэффициент динамичности), зависит от степени точности колес, твердости рабочих поверхностей зубьев, окружной скорости и определяется по таблице 8.
Таблица 8 – Значения коэффициента
Степень точности | Твердость рабочих поверхностей зубьев | Окружная скорость | |||
до 3 | 3…8 | 8…12,5 | |||
6 7 8 | ![]() ![]() ![]() ![]() ![]() ![]() | 1/1 1/1 1,15/1 1,15/1 1,25/1,1 1,2/1,1 | 1,2/1 1,15/1 1,35/1 1,25/1 1,45/1,3 1,35/1,2 | 1,3/1,1 1,25/1 1,45/1,2 1,35/1,1 – /1,4 – /1,3 | |
Примечание. В числителе указаны значения | |||||
- коэффициент, учитывающий распределение нагрузки между зубьями:
, (1.29)
где – коэффициент торцевого перекрытия, в рамках данной лабораторной работы принимается
;
– степень точности колеса;
– коэффициент, учитывающий наклон зуба, определяется по формуле:
, (1.30)
– коэффициент формы зуба (определяется для обоих колес), зависящий от эквивалентного числа зубьев, определяющихся по формуле:
, (1.31)
Формула (1.31) считается для шестерни и колеса, полученные значения округляют до целого большего числа.
Значение коэффициента для колес, нарезанных без смешения определяется по таблице 9.
Таблица 9 – Значения коэффициента
![]() | 17 | 20 | 25 | 30 | 40 | 50 | 60 | 80 | 100 | 150 |
![]() | 4,25 | 4,06 | 3,90 | 3,80 | 3,70 | 3,65 | 3,63 | 3,60 | 3,60 | 3,60 |
Рассчитывать на изгиб по формуле (1.27) следует зубья того колеса, для которого отношение будет меньше. Находится отношение для шестерни
и сравнивается с отношением колеса
.
2 Порядок выполнения работы
1) Вычерчивается схема редуктора с указанием чисел зубьев, передаточных отношений по ступеням и частот вращения валов.
2) Приводится краткое описание редуктора.
3) Рассчитываются основные кинематические и геометрические параметры заданной передачи. Данные свести в таблицу со сравнительным анализом расчетных и замерных параметров.
4) Определяются допускаемые контактные напряжения при длительной работе передачи для четырех вариантов.
5) Рассчитывается допустимый крутящий момент на ведомом валу из условия контактной прочности для 4-х вариантов.
6) Определяется мощность, передаваемая рассматриваемой ступенью редуктора для 4-х вариантов.
7) Определяются усилия в передаче для 4-х вариантов.
8) Определяются допускаемые напряжения при расчете на изгиб для 4-х вариантов.
9) Производится проверка прочности зубьев на выносливость при изгибе.
10) Изображается на схеме передачи направление окружных, радиальных и осевых усилий.
11) Строится график зависимости Т2Н=f(бHP) по четырем расчетным параметрам.
12) Вычерчивается рабочий чертеж детали по заданию преподавателя.3
Контрольные вопросы
1) Механические передачи.
2) Передачи зацеплением.
3) Редуктор, его назначение.
4) Достоинства и недостатки зубчатых передач.
5) Классификация зубчатых передач по форме колес.
6) Классификация зубчатых колес по виду зубьев.
7) Применение прямозубых зубчатых колес.
8) Применение косозубых зубчатых колес.
9) Применение шевронных зубчатых колес.
10) Виды повреждений зубчатых колес.
11) Передаточное число зубчатой пары.
12) Основные геометрические параметры цилиндрических зубчатых колес.
13) Эквивалентные колеса.
14) Силы в зацеплении цилиндрических зубчатых передач.
ЛАБОРАТОРНАЯ РАБОТА №2
Дата добавления: 2018-05-12; просмотров: 1109; Мы поможем в написании вашей работы! |
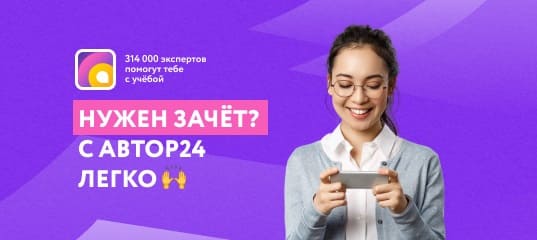
Мы поможем в написании ваших работ!