Температурна похибка, як правило, в систематичною похибкою.
Похибки, що мінливі у часі, пов'язані з процесами спрацювання, втомленості або старіння. Внаслідок цих процесів змінюються у часі параметри елементів ЗВ. Ці похибки, як правило, систематичні, що визначають втрату точності ЗВ у часі і пов'язані з визначенням їх надійності.
В процесі роботи приладу як систематична, так і випадкова похибки виявляються спільно і тому вони є складовими похибками ЗВ.
Найбільша похибка ЗВ, при якій він може бути визнаний придатним, називається межею допустимої похибки. Розрахунок ЗВ на точність зводиться до визначення очікуваного значення цієї похибки.
6.5 Вплив похибки вимірювання на результати контролю
Класи точності засобів вимірювання
Похибки ЗВ нерозривно пов'язані з узагальненою характеристикою - класом точності ЗВ. Вони визначаються межами допустимих основних і додаткових похибок, а також інших властивостей, що впливають на точність вимірювання. Способи встановлення класів точності викладені у ГОСТ 8.401-80 "ДСІ. Класи точності засобів вимірювання".
Класи точності можуть встановлюватися за абсолютною, відносною та приведеною похибками. Класи точності зазначаються у паспорті на ЗВ та на циферблаті, щитку, корпусі ЗВ.
Межі допустимих основної і додаткової похибок слід виражати у формі приведених, відносних або абсолютних похибок в залежності від характеру зміни похибок у межах діапазону вимірювання. Вираження меж допустимої похибки у формі приведених і відносних похибок б переважним, тому що вони дозволяють виражати межі допустимої похибки числом, яке залишається постійним для ЗВ одного рівня точності, але з різними верхніми межами вимірювання.
|
|
Приклад.
1) Чи можна стверджувати, що тахометр, який розрахований на вимірювання до 1000 об/хв. класу точності 1 вимірює 500 об/хв. з похибкою 1 % ?
Клас точності 1 відповідає допустимій приведеній похибці γ=±1% і це характеризує метрологічні властивості ЗВ, а не похибку вимірювання цим приладом.
Похибка може бути виражена абсолютною чи відносною величиною
.
У нашому прикладі ,
2) Оцінити придатність пружинного манометра класу точності 1,0 (γ=±1%) з діапазоном вимірювання 0÷60 кПа, якщо під час його повірки методом порівнювання із зразковим манометром класу точності 0,2 (γ=±0,2%) у точці 50 кПа при підвищенні тиску було зафіксовано XM=49,5 кПа, а при понижені –XБ=50,2кПа.
Варіація показань ЗВ не повинна перевищувати основну допустиму похибку
кПа.
Варіація показань
B=XБ-XM=50,2-49,5=0,7 кПа
Манометр не придатний до експлуатації не зважаючи на те, що абсолютна похибка не перевищує допустиму.
Δ=Xi-XД, кПа; XiМ=49,5 кПа; XiБ=50,2 кПа; XД=50 кПа.
|
|
Межі допустимої абсолютної основної похибки встановлюються за формулою
Δ=±а, (6.1)
Δ=±(a+bx), (6.2)
де Δ - межі допустимої абсолютної основної похибки;
x - значення вимірювальної величини;
a, b - позитивні числа, що не залежать від x.
Δ та x виражаються в одиницях вимірювальної величини, або у поділках шкали ЗВ. Формула (1) застосовується, коли межі абсолютної похибки можна вважати практично незмінними.
Формула (2) застосовується, коли межі абсолютної похибки змінюються практично лінійно.
* Графічне зображення абсолютної похибки за формулами
-Δ (a+bxmax) |
![]() |
-Δ а |
+Δ а |
1) ![]() |
![]() |
+Δ (a+bxmax) |
2) ![]() |
![]() |
У виразі (2) значення a має назву граничного значення адитивної похибки (похибка нуля), а bx - граничного значення мультиплікативної похибки (похибка чутливості).
** Абсолютна адитивна похибка не залежить від значення вимірювальної величини x. Ця похибка, обумовлена нестабільністю (дрейфом) нуля (тертям в опорах, шумами, вібрацією і т.д.), в одному з показників якості ЗВ.
Мультиплікативна похибка пропорційна значеннюx. Вона обумовлена діями впливових величин на параметри елементів і вузлів ЗВ.
|
|
Позначення класу точності ЗВ, що нормується за абсолютною похибкою, проводиться літерами латинського алфавіту.
Наприклад.
У паспорті на ЗВ пишеться клас точності M, а на ЗВ тільки літера M.
Недоліком такого позначення класу точності є чисто умовний характер.
Межі допустимої відносної похибки встановлюються за формулою
, (6.3)
, (6.4)
де δ - межі допустимої відносної основної похибки, %;
X - значення вимірювальної величини;
q- довільне позитивне число, яке вибирається із ряду (1; 1,5; 1,6; 2; 2,5; 3; 4; 5; 6)*10n; (n=1; 0; -1; -2і т.д.);
Xк- більша (за модулем) із меж вимірювання;
c, d - позитивні числа, які вибираються із вище згаданого ряду;
,
a, d- позитивні числа, які не залежать від X.
Графічне зображення відносної похибки за формулами:
Формула (3) застосовується, коли межі відносної похибки можна вважати практично незмінними;
Формула (4) застосовується, коли межі відносної похибки змінюються.
Позначення класу точності ЗВ, що нормуються за відносною похибкою, залежить від формули. Якщо межі допустимої відносної основної похибки визначаються за формулою (3), то у паспорті на ЗВ вказується значенняq%,яке відповідає допустимій відносній основній похибці ЗВ, а на приладі ставиться величина у колі.
|
|
Наприклад.
δ=±0,5%. У паспорті - клас точності 0,5, а на ЗВ - 0,5.
Якщо межі допустимої відносної основної похибки визначаються за формулою (4), то ставляться значення c/d з формули.
Наприклад.
.
У паспорті клас точності 0,02/0,01, а на ЗВ - 0,02/0,01.
Межі допустимої приведеної основної похибки встановлюються за формулою
(5)
деγ - межі допустимої приведеної основної похибки, %;
XN - нормуюче значення, яке виражене у тих же одиницях, що і Δ;
р - довільне позитивне число, яке вибирається із вище зазначеного ряду (дивись q).
Нормуюче значення XN для ЗВ з практично рівномірною степенною шкалою, а також, якщо нульове значення знаходиться на краю або поза діапазоном вимірювання, слід приймати рівним більшому із меж вимірювання. Якщо нульове значення знаходиться у середині діапазону вимірювання, то XN приймається рівним сумі модулів меж вимірювання.
У цьому випадку клас точності ЗВ позначається величиною приведеної основної похибки.
Наприклад.
Вольтметр має діапазон вимірювання 0...400.XN=400 V .
Амперметр має діапазон вимірювання від-3 А до+3 А. XN=6А; γ=±1,5%. У паспорті на ЗВ - клас точності 1,5, а на ЗВ -1,5.
Для ЗВ з істотно нерівномірною шкалою нормуюче значення XN приймається рівним всій довжині шкали. У цьому випадку межі основної похибки виражаються в одиницях довжини.
Наприклад.
γ=±0,5% У паспорті на ЗВ - клас точності 0,5, а на ЗВ –0.5 в круглій рамці.
Приклад №1.
Порівняти похибки вимірювання тиску в 100 кПа пружинними манометрами класів точності 0,2 з діапазоном вимірювання 0...600 кПа та 1,0 з діапазоном вимірювання 0... 100 кПа.
Для порівняння величин (похибок) найбільш зручно користуватись відносною похибкою. У зазначеному приладі клас точності відповідає приведеній похибці 0,2→γ=±0,2%; 1,0→γ=±1,0%. Приведена і відносна похибки пов'язані формулою
,
де X - значення вимірювальної величини (X=100 кПа);
XN - нормуюче значення.
Таким чином маємо:
Манометр класу точності 0,2-XN=600 кПа; γ=±0,2%.
Манометр класу точності 1,0-XN=100 кПа; γ=±1,0%.
Вимірювальна величина X=100 кПа.
Значення відносних похибок:
.
Манометр з вищим класом точності (0,2) має більшу похибку (δ=±1,2%).
Приклад №2
Проводиться вимірювання тиску в 100 кПа манометрами одного класу точності 0,2 але з різними діапазонами вимірювання 0÷600 кПа та 0÷100 кПа. Порівняти похибки вимірювання.
Маємо:
Таким чином похибка вимірювання у манометра з більшим діапазоном вимірювання (0÷600кПа) більша.
Якщо проаналізувати формулу зв'язку відносної та приведеної похибок δ=γ*XN/X, то можна зробити висновок, що чим ближча величина вимірювання до верхнього діапазону шкали, тим нижча похибка вимірювання. На підставі цього необхідно вибирати такий ЗВ, щоб точка вимірювання орієнтовно знаходилась на відстані 3/4 шкали від нижнього діапазону для ЗВ з постійним навантаженням та 2/3 – при наявності динамічного навантаження.
Лекція 7.ОСНОВНІ ПОЛОЖЕННЯ РОЗРАХУНКУ РОЗМІРНИХ ЛАНЦЮГІВ
7.1 Основні поняття, терміни, визначення, позначення
Загальні відомості ГОСТ 16319-80, ГОСТ 16320-80
Гармонійне і технологічне співвідношення взаємопов'язаних розмірів для надійної та довготривалої роботи вузла, визначення економічних допусків досягається на етапі конструювання механізмів, машин, приладів, інших виробів, проектуванні технологічних процесів і перевіряється при виробництві, виборі засобів і методів вимірювань. При цьому виникає необхідність проведення розмірного аналізу з використанням теорії розмірних ланцюгів.
Розмірним ланцюгомназивається сукупність взаємопов'язаних розмірів, які утворюють замкнений контур і визначають взаємне положення поверхонь (або осей) однієї чи декількох деталей. Замкнутість розмірного ланцюга призводить до того, що розміри, які входять до нього, не можуть призначатись незалежно, тобто значення і точність хоча б одного з розмірів визначаються за рахунок інших.
Розмірний ланцюг складається з ланок.
Ланкоюназивається кожний з розмірів, що утворюють розмірний ланцюг. Ланками можуть бути будь-які лінійні або кутові параметри:
- діаметральні розміри;
- відстані між поверхнями або осями;
- зазори, натяги, перекриття;
- мертві ходи;
- відхилення форми і розташування.
Під час конструювання машин, приладів та інших виробів, проектування технологічних процесів, вибір засобів та методів вимірювання проводиться розмірний аналіз, за допомогою якого досягається правильне співвідношення взаємопов’язаних розмірів та визначається допустима похибка. Подібні геометричні розрахунки виконуються з використанням теорій розмірних ланцюгів.
Розмірний ланцюг – сукупність взаємопов’язаних розмірів, що утворюють замкнутий контур та визначається взаємне положення поверхонь (осей) однієї або декількох деталей.
Розмірний ланцюг складається із окремих ланок. До складу якої можуть входити розміри окремих поверхонь деталей або вузлів.
Ланка – це кожний розмір, що входить до розмірного ланцюга.
Ланкою розмірного ланцюга може бути будь-який лінійний або кутовий параметр (діаметр, відстань між поверхнями або осями, зазор, натяг. Мертвий хід, відхилення форми тощо).
![]() |
![]() |
![]() |
![]() |
![]() |
![]() |
![]() |
![]() |
![]() |
![]() |
![]() |
![]() |
![]() |
![]() |
Рис. 7.1. Приклади розмірних ланцюгів
Ланки розмірного ланцюга поділяються на одну вихідну (замикаючу, в розмірному ланцюгові буває лише одна), а решта – складові ланки розмірного ланцюга.
До вихідної ланки ставляться основні вимоги до точності, що визначають якість виробу у відповідності з технічними умовами.
Під час обробки, або складання виробу вихідна ланка завжди остання тобто замикає розмірний ланцюг. У цьому випадку ця остання ланка називається замикаючою. Таким чином замикаюча ланка безпосередньо не виконується, а вона є результатом виконання решти ланок ланцюга.
Складова ланка, це ланки зі зміною котрих змінюється і замикаюча ланка. Тому ці ланки діляться на збільшуючі та зменшуючі.
Складові ланки розмірного ланцюга позначаються будь-якими буквами абетки з порядковим індексом (A1, A2, A3…), а вихідна ланка (замикаюча) має індекс ΣабоΔ ( AΣабо AΔ).
Збільшуюча ланка – ланка при збільшенні якої, замикаюча ланка також збільшується.Збільшуюча ланка позначається Aзб..
Зменшуюча ланка – ланка при збільшенні якої, замикаюча ланка також зменшується. Зменшуюча ланка позначається Aзм..
7.2 Класифікація розмірних ланцюгів
ГОСТ 16319-80 встановлює ряд класифікаційних ознак за якими відбувається класифікація розмірних ланцюгів (див. табл. 7.1).
Таблиця 7.1
Класифікація розмірних ланцюгів
Класифікаційний признак | Назва розмірного ланцюга | Призначення, характеристика |
Область використання | Конструкторський | Вирішується задача забезпечення точності при конструюванні виробів |
Технологічний | Вирішується задача забезпечення точності при виготовленні виробів | |
Вимірювальний | Вирішується задача вимірювання величин, що характеризують точність виробу | |
Місце у виробі | Детальний | Визначає точність відносного розташування поверхонь або осей одної деталі |
Складальний | Визначає точність відносного розташування поверхонь або осей деталей, що входять в складальну одиницю | |
Взаємне розташування ланок | Лінійний | Ланки ланцюга є лінійними розмірами. Ланки розташовані на паралельних прямих |
Кутовий | Ланки ланцюга с кутовими розмірами, відхилення яких можуть бути задані в лінійних величинах, віднесених до умовної довжини, або в градусах | |
Плоский | Ланки ланцюга розташовані довільно в одній або декількох паралельних площинах | |
Просторовий | Ланки ланцюга розташовані довільно в просторі | |
Характер ланок | Скалярний | Всі ланки ланцюга є скалярними величинами |
Векторний | Всі ланки ланцюга є векторними похибками | |
Комбінований | Частина складових ланок розмірного ланцюга - векторні похибки, усі інші -скалярні величини | |
Характер взаємних зв'язків | Паралельно зв'язані | Розмірні ланцюги (два або більше), що мають хоча б одну загальну ланку |
Незалежні | Розмірні ланцюги, що не мають спільних ланок |
7.3 Складання раціональних розмірних ланцюгів
Рекомендується складати розмірні ланцюги і виділяти ланки при проведенні розмірного аналізу, користуючись такими посиланнями.
1) Чітко має бути сформульована задача, для рішення якої розраховується розмірний ланцюг. В кожному розмірному ланцюзі може бути лише одна вихідна ланка.
2) Для виявлення вихідної ланки потрібно встановити вимоги до точності виробу. Ці вимоги можна розділити на дві групи:
- точність взаємного розташування деталей, складальних одиниць, що забезпечує якісну роботу виробу при експлуатації;
- точність взаємного розташування деталей, складальних одиниць, яка забезпечує складальну придатність виробу.
3) Номінальні розміри та граничні відхилення вихідних ланок встановлюються згідно із стандартами, технічними умовами, теоретичними розрахунками або експериментальними результатами.
4) Всі виявлені складові ланки та вихідна ланка повинні складати замкнений контур.
5) Складові ланки розмірного ланцюга позначаються прописними літерами латинського алфавіту (крім О, І.., Р, К) з цифровим індексом (цифра позначає порядок ланки в ланцю зі). Вихідна ланки позначається тою ж літерою, що і складові, з індексом "£".
6) Позначення, терміни і визначення регламентуєГОСТ 16319-80.
7.4 Задачі, які вирішуються за допомогою розмірних ланцюгів
Розрахунки розмірних ланцюгів є необхідним етапом конструювання, виготовлення та експлуатації широкого класу виробів (машин, механізмів, приладів, апаратів тощо). За допомогою теорії розмірних ланцюгів можуть бути вирішені такі конструкторські, технологічні та метрологічні задачі:
- - встановлення геометричних та кінематичних зв'язків між розмірами деталей;
- розрахунок номінальних значень, відхилень і допусків розмірів ланок;
- розрахунок норм точності і розробка технічних умов на машини та їхні складові частини;
- аналіз правильності проставлення розмірів і відхилень на робочих кресленнях деталей;
- розрахунок міжопераційних розмірів;
- розрахунок припусків і допусків;
- перерахунок конструктивних розмірів на технологічні (при неспівпаданні конструкторських та технологічних баз);
- обґрунтування послідовності технологічних операцій при виготовленні і складанні виробів;
- обґрунтування і розрахунки необхідної точності пристосувань;
- вибір засобів і методів вимірювань, розрахунок досягнутої точності вимірів.
Розрахунок розмірного ланцюга є необхідним етапом конструювання, виготовлення та експлуатації виробів. За допомогою теорії розмірного ланцюга можуть бути вирішені наступні конструкторську, технологічні та метрологічні задачі:
1) Встановлення геометричних та кінематичних зв’язків між розмірами деталей, розрахунок номінальних значень, відхилень та допусків розмірів ланок.
2) Розрахунок норм точності та розробка технічних умов на ланки та іхні складові частини.
3) Аналіз правильності нанесення розмірів та відхилень на робочих кресленнях деталей.
4) Розрахунок між операційних розмірів, припусків та допусків, перерахунок конструкторських розмірів на технологічні )при різних базах відліку).
5) Обґрунтування послідовності технологічних операцій під час виготовлення та складання виробів.
6) Обґрунтування та розрахунок необхідної точності пристроїв.
7) Вибір засобів і методів вимірювання, розрахунок максимально можливої степені точності вимірювання.
Повний розрахунок розмірного ланцюга виконується у процесі розробки робочого проекту машини, попередні розрахунки слід проводити ще під час конструкторського опрацювання технічного проекту.
Методи досягнення заданої точності вихідної ланки.
Існують слідуючи методи:
- Метод повної взаємозамінності;
- Теоретико-ймовірний метод;
- Метод групової взаємозамінності (селективного складання);
- Метод припасування (підгонки);
- Метод регулювання.
При виборі методу досягнення точності необхідно враховувати функціональні призначення виробів, його конструкторські та технологічні особливості, вартість вироблення та складання. Експлуатаційні вимоги тощо.
Задана точність вихідної ланки повинна досягатись з найменшими технологічними та експлуатаційними витратами.
При рівних умовах необхідно вибирати такі методи досягнення точності при складання виробу відбувається без використання методу підбору, припасування та регулювання, тобто використовувати метод повної взаємозамінності або теоретико-ймовірний метод.
Метод повної взаємозамінності економічно доцільно застосовувати лише для ланцюгів малої точності або ланок з невеликою кількістю ланок. Цей метод застосовують при мало серійному виробництві.
Теоретико-ймовірний метод застосовують у серійному та масовому виробництві. Істотною перевагою цього методу є можливість розширення полів допусків складових розмірів.
Метод групової взаємозамінності часто застосовуються в розмірних ланцюгах високої точності з нев5еликою кількістю ланок.
Метод припасування має обмежене застосування тому, що необхідно використовувати висококваліфікованих фахівців. Роботи припасування не піддаються механізації та мають велику вартість.
Метод регулювання більш широко застосовується в розмірних ланцюгах високої точності з великою кількістю ланок. Цей метод може бути використаний не лише під час складання, а і під час експлуатації.
У залежності від вихідних даних розмірний ланцюг може вирішуватись з використанням прямої чи зворотної задач. Зворотна задача використовується для перевірки правильності розрахунків прямої задачі.
Пряма задача – по заданому номінальному розміру та граничних відхиленнях замикаючої ланки, а також номінальними розмірами складових ланок визначаються граничні відхилення та допуски розмірів складових ланок.
Зворотна задача – по заданих номінальних розмірах та граничних відхиленнях складових ланок визначають номінальний розмір та граничні відхилення замикаючої ланки.
Суть прямої задачі полягає в тому, щоб розподілити допуск замикаючої ланки між складовими ланками. Для цього використовується декілька способів.
Спосіб проб. При цьому способові на складові ланки призначається економічно доцільні допуски на підставі досвіду експлуатації подібних приладів. Допуск замикаючої ланки визначається по зворотній задачі та порівнюється з заданим допуском [T] замикаючої ланки.
TΔ≤[TΔ]
Спосіб рівних допусків. Допуски всіх складових ланок приймаються рівними. Цей спосіб пропонується для попереднього призначення допусків складових ланок з наступним їх корегуванням або для розмірних ланцюгів з близькими по значенню номінальними розмірами.
Tc=[TΔ]/(m+n).
Спосіб одного квалітету. На усі складові ланки призначаються допуски одного квалітету. Величина допуску залежить від номінального розміру складових ланок.
Дата добавления: 2018-05-09; просмотров: 998; Мы поможем в написании вашей работы! |
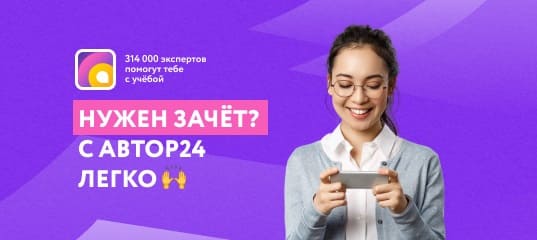
Мы поможем в написании ваших работ!