ЗАЩИТА СТАЛЬНЫХ КОНСТРУКЦИЙ ОТ КОРРОЗИИ
7.37. В условиях монтажа работы по нанесению лакокрасочных покрытий следует выполнять при отсутствии атмосферных осадков, тумана, росы и температуре воздуха не менее 5 и не более 30°С, при этом поверхность металла должна быть чистой и сухой.
(3.06.04-91, п. 7.38)
7.38. Длительность перерыва между операциями по подготовке поверхности и окрашиванием при нахождении в помещении не должна превышать 24 ч, на открытом воздухе — 6 ч.
(3.06.04-91, п. 7.39)
7.39. Неокрашенные поверхности следует очищать от окислов и окалины механическим способом.
(3.06.04-91, п. 7.40)
7.40. Технические требования, которые следует выполнять при защите стальных конструкций от коррозии и проверять при операционном контроле, а также объем, методы и способы контроля приведены в табл. 34.
Таблица 34
Технические требования | Контроль | Метод и способ контроля |
1. Требования к материалам для окрашивания изделий, предназначенных для эксплуатации в районах с умеренным, холодным и тропическим климатом, по ГОСТ 9.074-77*, ГОСТ 9.404-81* и ГОСТ 9.401-91; толщина покрытия, мкм, для сред: | Каждой партии | Проверка по ГОСТ или ТУ на материалы |
слабоагрессивных — 70-80 | Выборочный. За толщину | Измерительный |
среднеагрессивных — не менее 80 | принимается среднее | (толщиномером |
сильноагрессивных — не менее 100 | арифметическое из пяти замеров | электромагнитного типа) |
внешний вид — VI класс | Каждого изделия | Визуальный — по |
адгезия покрытия к изделию — не более двух баллов | Выборочный или на трех образцах | ГОСТ 9.032-74*, ГОСТ 15140-78, методом решетчатого надреза |
2. Подготовка поверхности: степень обезжиривания — первая | 20 % сменной выработки | Проверка по ГОСТ 9.402-80* |
степень очистки от окалины и окислов — не ниже второй | То же | То же |
шероховатость — 30 мкм | То же | Проверка по ГОСТ 2789-73 профилографом и профилометром на образцах-"свидетелях" |
|
|
(3.06.04-91, табл. 25)
Глава 8
СВАРНЫЕ МОНТАЖНЫЕ СОЕДИНЕНИЯ
ОБЩИЕ ПОЛОЖЕНИЯ
8.1 Руководство сварочными работами должно осуществлять лицо, имеющее документ о специальном образовании или подготовке в области сварки.
Сварочные работы следует производить по утвержденному проекту производства сварочных работ (ППСР) или другой технологической документации.
(3.03.01-87, п. 8.2)
8.2. Сварку и прихватку должны выполнять электросварщики, имеющие удостоверение на производство сварочных работ, выданное в соответствии с утвержденными Правилами аттестации сварщиков.
К сварке конструкций из сталей с пределом текучести более 390 МПа (40 кгс/мм2) допускаются сварщики, имеющие удостоверение на право работ по сварке этих сталей.
|
|
(3.03.01-87, п. 8.3)
8.3. К сварке монтажных соединений допускаются сварщики, прошедшие аттестацию согласно «Правилам аттестации сварщиков» и имеющие удостоверение с указанием вида выполняемых работ.
8.4. В удостоверении должны быть записи о прохождении ежегодных испытаний, результаты которых должны быть оценены в протоколе на основании фактических материалов служб, проводивших проверку качества контрольных сварных соединений. Протоколы испытаний сварщиков оформляются комиссией, созданной по согласованию с местными органами Госгортехпадзора и организацией, монтирующей пролетное строение и должны храниться в этой организации.
(РМ 12, п. 2.5)
8.5. Все ИТР, рабочие (сборщики-монтажники, газорезчики, подогревальщики, электросварщики, сварщики-автоматчики, полуавтоматчики, правильщики, контролеры), участвующие в выполнении монтажных сварных соединений и контроле их качества, должны пройти техучебу и инструктаж для ознакомления с особенностями монтажа и сварки конструкций данного пролетного строения и техники безопасности. После окончания обучения и инструктажа, знания должны быть проверены квалификационной комиссией строительной организации или учебного пункта, проводившего обучение и инструктаж и оценены в протоколе.
|
|
(РМ 12, п. 2.4)
8.6. Техническое руководство сварочными работами на монтаже должны осуществлять лица, знающие особенности монтажа пролетного строения и сварки его металлоконструкций, имеющие специальное техническое образование или опыт по технологии сварочного производства и прошедшие курс специальной полготовки в соответствии с пунктом 8.5 настоящего «Пособия».
(РМ 12, п. 2.6)
8.7. Производственный контроль качества сварочных работ должен включать:
входной контроль рабочей технологической документации, монтируемых сварных конструкций, сварочных материалов, оборудования, инструмента и приспособлений;
специальный контроль сварочных процессов, технологических операций и качества выполняемых сварных соединений;
приемочный контроль качества выполняемых сварных соединений.
(3.03.01-87, п. 8.54)
8.8. Сварочные материалы (покрытые электроды, порошковые проволоки, сварочные проволоки Сплошного сечения, плавленые флюсы) должны соответствовать требованиям ГОСТ 9467-75*, ГОСТ 26271-84*, ГОСТ 9087-81*Е.
(3.03.01-87, п. 8.10)
8.9. Поступающие на строительство материалы (основной металл, электродная проволока, флюс, электроды и др.) перед употреблением на монтаже должны подвергаться приемке. Материалы должны иметь сертификаты и удовлетворять по маркам требованиям чертежей КМ пролетного строения, данные сертификатов должны соответствовать требованиям ТУ, ОСТов и ГОСТов на указанные материалы.
|
|
Результаты входного контроля материалов заносят в акт приемки, являющийся документом, подтверждающим пригодность данных материалов для монтажа. Материалы, не прошедшие приемку, запрещается отпускать со склада на участок.
(РМ 12, п. 17.2.1)
8.10. Каждая партия сварочной проволоки, флюса и электродов должна подвергаться технологическим испытаниям. Испытания проводят путем сварки стыковых и угловых (тавровых) соединений листового материала, применяемого в данной конструкции. Флюс и проволока считаются пригодными по технологическим свойствам, если процесс сварки на .рекомендуемом режиме протекает спокойно, формирование шва и шлаковой корки равномерное, шлак легко удаляется со шва, а в наплавленном металле отсутствуют поры и трещины.
Электроды считаются годными, если при сварке тех же соединений на оптимальном режиме дуга горит устойчиво, спокойно, плавление обмазки происходит равномерно, без образования «козырька», шлак легко удаляется со шва и в наплавленном металле отсутствуют поры и трещины.
Рекомендуется от каждой партии сварочных материалов испытывать контрольные образцы сварных соединений для проверки механических свойств, указанных в табл. 35.
(РМ 12, п. 17.2.2)
Таблица 35
Вид испытания | Число образцов, шт. | Нормируемый показатель |
Стальные конструкции | ||
1. Статическое растяжение | 2 | Временное сопротивление разрыву — не менее нижнего предела временного сопротивления основного металла, регламентируемого государственным стандартом |
2. Статический изгиб | 2 | Угол статического изгиба, град., для сталей толщиной, мм: углеродистых |
до 20 — не менее 100 | ||
св. 20 — не менее 80 | ||
низколегированных до 20 — не менее 80 | ||
св. 20 — не менее 60 | ||
3. Ударный изгиб металла шва Растяжение до разрушения | 3 | Ударная вязкость — не менее величины, указанной в технологической документации на монтажную сварку данной конструкции |
Арматура железобетонных конструкций | ||
Растяжение до разрушения | 3 | Оценка результатов по ГОСТ 10922-90 |
(3.03.01-87, табл. 35)
8.11. Сварочные материалы (электроды, проволоки, флюсы) необходимо хранить на складах монтажных организаций в заводской таре отдельно по маркам, диаметрам и партиям. Помещение склада должно быть сухим, с температурой воздуха нс ниже 15°С.
(3.03.01-87, п. 8.12)
Прокаленные сварочные материалы следует хранить в сушильных печах при 45-100°С или в кладовых-хранилищах с температурой воздуха не ниже 15°С и относительной влажностью не более 50 %.
(3.03.01-87, п. 8.13)
8.12. Перед началом монтажных работ необходимо проверить техническое состояние сварочного и монтажного оборудования, аппаратуры для неразрушающего контроля сварных швов, инструментов, механизмов, приспособлений.
8.13. При контроле технического состояния сварочного оборудования и оснастки проверяется наличие на сварочных автоматах, выпрямителях и аппаратных шкафах измерительных приборов (амперметров, вольтметров), их исправность, ходовой части оборудования, возможность обеспечения данным оборудованием заданного режима (в частности, его параметров и постоянства заданных скоростей подачи проволоки и скорости сварки) и т.д.
Правильность показаний измерительных приборов, кроме предварительной проверки, контролируется не реже двух раз в месяц при помощи специальных контрольных приборов.
(РМ 12, п. 17.2.5)
8.14. При контроле технического состояния дефектоскопической аппаратуры проверяется соответствие ее основных параметров требованиям нормативно-технической документации по неразрушающим методам контроля.
(РМ 12, п. 17.2.6)
8.15. Данные о производстве работ по сварке стальных конструкций мостов и арматуры сборных железобетонных конструкций следует ежедневно заносить в Журнал сварочных работ (приложение 66).
СВАРКА МОНТАЖНЫХ СОЕДИНЕНИЙ
СТАЛЬНЫХ КОНСТРУКЦИЙ
8.16. Сварочные работы на монтаже пролетного строения должны выполняться при тщательном и непрерывном авторском надзоре со стороны проектной организации. Все отступления от принятой технологии монтажа и монтажной сварки конструкций пролетного строения должны быть согласованы с проектной организацией и научно-исследовательской организацией, оказывающей научно-техническую помощь по технологии монтажной сварки. В случае систематического появления трещин в сварных швах рекомендации по устранению причин их возникновения должны быть разработаны с привлечением указанной научно-исследовательской организации.
(РМ 12, п. 2.9)
8.17. При приемке поступающих с завода-изготовителя монтажных элементов и деталей следует проверять наличие паспорта, клейм приемки ОТК и заводской инспекции, маркировки и ее соответствие монтажной схеме. Кроме того, осуществляется контроль геометрических форм и размеров, отсутствие недопустимых остаточных деформаций и повреждений, формы подготовленных кромок монтажных соединений, а также (внешним осмотром) качества заводских сварных соединений.
(РМ 12, п. 17.2.3)
8.18. Не допускается применять при монтаже металлических конструкций пролетного строения: элементы и детали, нс соответствующие проекту, а также не имеющие маркировки завода-изготовителя, сварочные материалы и дополнительный металл без сертификатов, а также без проверки соответствия сертификатных данных требованиям стандартов и технических условий, а их марок — указаниям проекта.
(3.06.04-91, приложение 12, п. 3)
8.19. При наличии соответствующего требования в проекте производства сварочных работ при технологической документации на монтажную сварку стыковых соединений данной конструкции, каждый сварщик предварительно должен сварить пробные стыковые образцы.
Сварку образцов следует производить из того же вида проката (марки стали, толщины), в том же пространственном положении и при использовании тех же режимов, материалов и оборудования, что и при выполнении монтажных сварных соединений.
(3.03.01-87, п. 8.4)
8.20. Размеры пластин для пробных образцов стальных конструкций, а также форма и размеры образцов для механических испытаний, изготавливаемых из сварного пробного образца, после внешнего осмотра, измерения стыкового шва, должны соответствовать требованиям ГОСТ 6996-66*.
(3.03.01-87, п. 8.5)
8.21. В случае необходимости выполнения сварки стальных конструкций при температуре воздуха ниже минус 30°С сварщики должны предварительно сварить пробные стыковые образцы при температуре не выше указанной. При удовлетворительных результатах механических испытаний пробных образцов сварщик может быть допущен к работе при температуре воздуха на 10°С ниже температуры сварки пробных образцов.
(3.03.01-87, п. 8.7)
8.22. Механические испытания стыкового сварного соединения пробного образца для стальных конструкций необходимо проводить согласно ГОСТ 6996-66* в объеме, указанном в табл. 35.
При неудовлетворительных результатах механических испытаний разрешается повторная сварка пробных образцов под наблюдением руководителя сварочных работ.
(3.03.01-87, п. 8.6)
8.23. Перед подачей па сборку (монтажную площадку или участок укрупнения блоков) следует проверить качество исправления всех отклонений, зафиксированных при приемке монтажных элементов и деталей, и произвести при необходимости дополнительные исправления.
(РМ 12, п. 17.3.1)
8.24. Сборка монтажных соединений под сварку должна производиться в полном соответствии с указаниями проекта. Перед сваркой собранных соединений контролируются: правильность фиксирования элементов конструкции (в плане, профилей подлине), правильность (в пределах допусков) всех размеров и формы подготовленных кромок (величина зазора, притупления, прямолинейность, постоянство сечения разделки и др.), платность и надежность закрепления подкладок, величина депланации и уступов стыкуемых кромок, правильность и чистота свариваемых кромок и пр.
(РМ 12, п. 17.3.2)
8.25. Контроль за соблюдением установленной технологии сварки должен осуществляться периодически — не реже одного раза в смену и при выполнении каждого нового типа монтажного соединения.
Проверяется соответствие применяемых при сварке марок электродной проволоки, флюса и электродов, соответствие режима сварки, правильность наложения слоев при заполнении разделки и качество наплавленного металла (визуальным осмотром).
Особое внимание при контроле следует обращать на обязательное выполнение предварительного подогрева металла до требуемой температуры (в соответствии с требованиями п. 8.29).
(РМ 12, п. 17.3.4; 17.3.5)
8.26. Размеры конструктивных элементов кромок и швов сварных соединений, выполненных при монтаже, и предельные отклонения размеров сечения швов соединений должны соответствовать указанным в ГОСТ 5264-80*, ГОСТ 11534-75*, ГОСТ 8713-79*, ГОСТ 11533-75*, ГОСТ 14771-76*, ГОСТ 15164-78*, ГОСТ 23518-79.
(3.03.01-87, п. 8.16)
8.27. Монтажные элементы в зоне сварных стыков, имеющие припуск по длине или ширине, при сборке стыков необходимо подгонять по месту ручной газорезкой с последующей механической зачисткой кромок наждачным кругом или переносной газорежущей машиной, снабженной специальным копирующим устройством.
(3.06.04-91, приложение 12, п. 5)
8.28. Кромка и участки металла шириной 20-30 мм, прилегающие к этим кромкам с обеих сторон, следует перед сваркой зачищать по всей длине от загрязнений, ржавчины, окалины, шлака и брызг металла наждачным кругом, пескоструйной обработкой или механическими щетками (типа «Волна») с последующей продувкой воздухом.
(3.06.04-91, приложение 12, п. 6)
8.29. В сварных соединениях конструкций необходимо применять предварительный подогрев кромок под сварку при следующих условиях: при температуре воздуха ниже 0°С; для сталей с пределом текучести до 400 МПа, при положительной температуре воздуха для стали с пределом текучести 400 МПа, толщиной 16 мм и более, при вышеупомянутых условиях перед наложением последующих слоев в многослойных швах в случае, когда температура предыдущего слоя снизилась до 100°С. Температура предварительного и сопутствующего подогрева должна находиться в пределах 120-160°С. Ширина зоны подогрева (до заданной температуры) должна быть по 100 мм от оси шва в каждую сторону.
(3.06.04-91, приложение 12, п. 9)
8.30. Сварку надлежит производить при стабильном режиме. Предельные отклонения заданных значений силы сварочного тока и напряжения на дуге при автоматизированной сварке не должны превышать ± 5 %.
Оборудование для автоматизированной и ручной многопостовой сварки следует питать от отдельного фидера.
(3.03.01-87, п. 8.18, 8.9)
8.31. Монтажные швы следует проваривать по всей длине без перерыва. При случайной остановке кратер и прилегающий к нему участок шва на длине до 100 мм до возобновления сварки необходимо зачищать наждачным кругом. Сварку следует возобновлять только на зачищенном участке.
При сварке многослойных швов после каждого прохода необходимо полностью удалять шлак и устранять возможные дефекты, а последующий слой накладывать только после контроля качества предыдущего слоя внешним осмотром.
(3.06.04-91, приложение 12, п. 10)
8.32. Сварщик должен ставить личное клеймо на расстоянии 40-60 мм от границы выполненного им шва сварного соединения: одним сварщиком — в одном месте, при выполнении несколькими сварщиками — в начале и конце шва.
Взамен постановки клейма допускается составление исполнительных схем с подписями сварщиков.
(3.03.01-87, п. 8.14)
8.33. Отклонения размеров сварных элементов стальных пролетных строений от проектных не должны превышать величин, указанных в табл. 32.
СВАРКА МОНТАЖНЫХ СОЕДИНЕНИЙ
ЖЕЛЕЗОБЕТОННЫХ КОНСТРУКЦИЙ
8.34. Производственный контроль качества выполнения монтажных сварных соединений арматуры железобетонных конструкций включает проверку:
— соответствие рабочим чертежам и ГОСТ размеров конструктивных элементов сварных соединений стержневой арматуры (стержней между собой и с элементами закладных изделий), а также предельных отклонений размеров выполненных швов;
— соответствия рабочим чертежам классов применяемой стержневой арматуры, марок стали плоских закладных изделий и соединительных деталей, а перед сваркой также размеров и точности сопряжения соединительных элементов. Точность сборки выпусков арматурных стержней должна соответствовать требованиям ГОСТ 10922-90 и ГОСТ 14098-91;
— выполнения предварительного подогрева стержней арматурыприотрицательной температуре окружающего воздуха (до –30°С) и др.
8.35. Выполненные сварочные работы перед бетонированием следует оформлять актами приемки партии арматуры по внешнему осмотру, а в случаях, предусмотренных ГОСТ 10922-90 — актами контроля физическими методами.
(3.03.01-87, п. 8.46)
8.36. Для стыков стержневой горячекатаной арматуры из стали классов А-I, A-II и Ас-II и А-III при монтаже конструкций допускается применение ванной сварки на удлиненных стальных накладках (подкладках) длиной не менее 5 диаметром стержней, а также стыков с парными смещенными накладками, приваренными односторонними или двусторонними швами суммарной длиной не менее 10 диаметров стыкуемых стержней. Ванную сварку следует применять при диаметре стержней не менее 20 мм.
(2.05.03-84, п. 3.160 изм.)
8.37. Для выполнения монтажных соединений арматурной стали разных классов следует применять сварочные материалы, указанные в табл. 36.
8.38. Для механизированных способов сварки следует использовать источники постоянного сварочного тока универсальные или с жесткой характеристикой до 500А, для ручной дуговой сварки — источники постоянного сварочного тока универсальные или с падающей характеристикой и сварочные трансформаторы на токи до 500А.
(3.03.01-87, п. 8.36)
8.39. Перед сборкой конструкций необходимо установить соответствие рабочим чертежам классов стержневой арматуры, марок стали плоских закладных деталей и соединительных деталей, а перед сваркой также размеры и точности сопряжения соединительных элементов.
Таблица 36
Классы | Рекомендуемые типы электродов для сварки
| ||
арматуры | Ванной, ванно-шовной и дуговой многослойными швами стыковых соединений | Протяженными швами стыковых и нахлесточных соединений | Дуговой ручной прихватками |
А-I | Э42, Э46, Э42А, Э46А | ||
А-II | Э50А, Э55 | Э42А, Э46А, Э50А | Э50А, Э55 |
А-III | Э55, Э60 | Э42А, Э46А, Э50А | Э50А, Э55 |
Ат-IIIС | То же | То же | То же |
Ат-IVС | То же | Э50А, Э55, Э60 | То же |
Примечание. При отсутствии электродов типов Э55 к Э60 ванно-шовную и дуговую многослойными швами сварку стали класса А-III, Ат-IIIС и Ат-IVС допускается выполнять электродами Э50А.
|
(3.03.01-87, табл. 39)
Точность сборки выпусков арматурных стержней должна соответствовать ГОСТ 10922-90 и ГОСТ 14098-91.
(3.03.01-87, п. 8.37)
8.40. Перед сваркой (ванной, многослойными или протяженными швами) арматурные стержни в месте соединения следует зачищать на длине, превышающей на 10-15 мм сварной шов или стык.
(3.03.01-87, п. 8.38)
8.41. При сборке конструкций не разрешается обрезка концов стержней или подготовка их кромок электрической дуговой.
(3.03.01-87, п. 8.42)
8.42. После сборки под сварку несоосность стыкуемых арматурных стержней, переломы их осей, смещения и отклонения размеров элементов сварных соединений должны соответствовать требованиям ГОСТ 10922-90. Отгиб стержней для обеспечения их соосности допускается осуществлять нагревом до температуры 600-800°С.
(3.03.01-87, п. 8.43)
8.43. Сварку элементов конструкций следует производить в надежно зафиксированном проектном положении. Запрещается сварка выпусков арматурных стержней конструкций, удерживаемых краном.
(3.03.01-87, п. 8.44)
8.44. После окончания сварки выполненное сварное соединение необходимо очистить от шлака и брызг металла.
(3.03.01-87, п. 8.45)
8.45. Конструкции сварных соединений стержневой арматуры, их типы и способы выполнения в зависимости от условий эксплуатации, класса и марки свариваемой стали, диаметра и пространственного положения при сварке должны соответствовать требованиям ГОСТ 14098-91.
(3.03.01-87, п. 8.47)
8.46. Прихватка дуговой сваркой в крестообразных соединениях стержней рабочей арматуры согласно ГОСТ 14098-91 при отрицательных температурах запрещается.
(3.03.01-87, п. 8.48)
8.47. На поверхности стержней рабочей арматуры не допускаются ожоги дуговой сваркой.
(3.03.01-87, п. 8.49)
8.48. Для выполнения ручной или механизированной сварки при отрицательной температуре окружающего воздуха до минус 30°С необходимо:
увеличить сварочный ток на 1 % при понижении температуры воздуха на каждые 3°С, ниже 0°С;
производить предварительный подогрев газовым пламенем стержней арматуры от 200-250°С на длину 90-150 мм от стыка;
подогрев стержней подлежит осуществлять после закрепления на них инвентарных форм, стальных скоб или круглых накладок без разборки кондукторов, используемых для временного закрепления монтируемых конструкций;
снижать скорость охлаждения выполненных ванными способами сварки соединения стержней посредством обмотки их асбестом;
при наличии инвентарных формующих элементов следует снимать последние после остывания выполненного сварного соединения до 100°С и ниже.
(3.03.01-87, п. 8.51)
8.49. Допускается сварка стержневой арматуры при температуре окружающего воздуха от минус 30°С до минус 50°С по специальной технологии, разработанной в ППР и ППСР.
(3.03.01-87, п. 8.52)
8.50. В соединениях стержней с накладками или внахлестку и с элементами закладных изделий, сваренных при отрицательных температурах, удаление дефектов в швах следует выполнять после подогрева прилегающего участка сварного соединения до 200-250°С. Заварку восстанавливаемого участка надлежит производить также после подогрева.
(3.03.01-87, п. 8.53)
КОНТРОЛЬ КАЧЕСТВА
8.51. Контроль качества сварных швов должен осуществляться в объеме, предусмотренном разделом 9 главы СНиП III-18-75 и разделом 8 главы СНиП 3.03.01-87. Категории сварных монтажных швов должна устанавливать проектная организация в чертежах КМ. Внешнему осмотру и обмеру должны подвергаться 100 % монтажных швов. На чертежах КМ сварных конструкций следует указывать: типы, размеры всех швов и обозначения монтажных и заводских швов; способ выполнения всех сварных швов (автоматическая, полуавтоматическая сварка под флюсом, ручная сварка и др.) и типы подкладок для стыковых швов, а при необходимости — также последовательность наложения швов; участки сварных швов с полным проплавлением толщины детали; все места конструкции, подлежащие обработке в соответствии с «Инструкцией по механической обработке сварных соединений в стальных конструкциях мостов» (Минтрансстрой, МПС, 1978 г.), с указанием соответствующего пункта.
(2.05.03-84, п. 4.143)
Расположение и размеры зон механической обработки, а также получаемая в результате форма детален и соединений должны быть указаны в чертежах КМД.
(188-78 п. 1.3)
8.52. Допуски по технологическим дефектам швов сварных соединений стальных конструкций мостов приведены в табл. 37.
Таблица 37
Категория | Типы швов | Технологический дефект в шве сварного соединения | ||
швов, сварных соединений | сварных соединений, входящих в данную категорию | Поры наружные и внутренние, шлаковые включения | Подрезы поперек усилий | Подрезы вдоль усилий |
I | 1. Поперечные и продольные стыковые швы растянутых поясов сплошных балок 2. Поперечные и продольные стыковые швы растянутых элементов ферм 3. Угловые швы, прикрепляющие основные детали и элементы конструкции и работающие на отрыв (при растяжении или изгибе) | Поры или шлаковые включения диаметром более 2 % толщины металла и более 1 мм не допускаются в крайних четвертях ширины стыкового шва (поз. 1, 2, 7) и в соединениях, перечисленных в поз. 4, 5, 6. В остальной зоне стыковых швов (поз. 1, 2, 7) и в соединениях, указанных в поз. 3 допускаются единичные дефекты диаметром не более 1 мм для металла толщиной до 25 мм и не более 4% толщины для металла | Без исправления не допускаются подрезы глубиной до 0,5 мм на металле толщиной до 20 мм и глубиной не более 3 % толщины на металле толщиной более 20 мм, а также местные подрезы длиной до 20 % длины шва при глубине подреза не более 6 % толщины металла. Разрешается исправлять зачисткой без предварительной заварки подреза | Без исправления не допускаются. При наличии их глубиной до 1 мм на металле толщиной до 20 мм и глубиной не более 6 % толщины на металле толщиной более 20 мм можно устранять зачисткой. Подрезы глубиной не более 1 мм, расположенные непосредственно на ребрах жесткости, к которым не присоединяются элементы поперечной конструкции пролетного строения, можно оставлять без исправления |
толщиной более 25 мм в количестве не более четырех дефектов на участке шва длиной 400 мм. Расстояние между дефектами не менее 45 мм. | Подрезы большей величины, чем указано выше, следует заваривать с последующей зачисткой; при заварке подреза независимо от способа сварки должно быть обеспечено выполнение требований табл. 32, п. 6 | |||
4. Концевые участки (длиной 100 мм) стыковых и угловых швов, прикрепляющих к растянутым элементам ферм и растянутым поясам сплошных балок узловые фасонки или расположенные вдоль усилия фасонки связей. 5. Концевые участки (длиной 100 мм) угловых поясных и соединительных швов в местах обрыва одной из частей, сечения сплошных балок (стенки или пояса) в растянутой зоне и растянутых элементов ферм. 6. Концевые участки (длиной 100 мм) угловых косых швов, прикрепляющих концы накладных компенсаторов или обрываемых в пролете листов пакетов растянутых поясов сплошных балок. 7. Концевые участки поперечных стыковых швов стенки балок на протяжении 40 %высоты растянутой зоны, но не менее 200 мм, считая от растянутого пояса. | ||||
II | 8. Угловые поясные швы растянутых поясов сплошных балок (кроме швов по поз. 5) 9. Угловые соединительные швы растянутых элементов ферм (кроме швов по поз. 5) 10. Угловые соединительные швы пакетов растянутых поясов сплошных балок (кроме швов по поз. 6) 11. Поперечные стыковые швы стенок балок в растянутой зоне на участке протяжением 40 % ее высоты, примыкающем к концевому участку (см. поз. 7) | Допускаются единичные дефекты диаметром не более 1,5 мм в количестве не более пять дефектов на участке шва длиной 400 мм. Расстояние между дефектами не менее 15 мм. | Без исправления не допускаются. Имеющиеся подрезы устраняются зачисткой или заваркой с последующей зачисткой согласно указаниям для швов 1-й категории. | Допускаются глубиной не более 1 мм при ширине не менее 2мм и плавном очертании. Подрезы большей глубины или неплавного очертания устраняются зачисткой или заваркой с последующей зачисткой согласно указаниям для 1-й категории. |
12. Продольные стыковые швы стенок балок расположенные в растянутой зоне в пределах 80% ее высоты, считая от растянутого пояса. 13. а) Концевые участки (длиной 100 мм) угловых швов, прикрепляющих горизонтальные фасонки связей к стенкам балок в растянутый зоне в пределах 40 % ее высоты, считая от растянутого пояса. б) Стыковые и угловые швы (за исключением концевых участков, см. поз. 5), прикрепляющие к растянутым поясам сплошных балок узловые фасонки или расположенные вдоль усилия фасонки связей, а в неразрезных сталежелезобетонных пролетных строениях — упоры. | Допускаются единичные дефекты диаметром не более 1,5 мм в количестве не более пять дефектов на участке шва длиной 400 мм. Расстояние между дефектами не менее 15 мм. | Без исправления не допускаются. Имеющиеся подрезы устраняются зачисткой или заваркой с последующей зачисткой согласно указаниям для швов 1-й категории. | Допускаются глубиной не более 1 мм при ширине не менее 2 мм и плавном очертании. Подрезы большей глубины или неплавного очертания устраняются зачисткой или заваркой с последующей зачисткой согласно указаниям для швов 1-й категории. | |
III | 14. Поперечные и продольные стыковые швы сжатых поясов сплошных балок 15. Поперечные и продольные стыковые швы стенок на участке за вычетом поз. 7 и 11. 16. Продольные стыковые швы стенок балок, расположенные в пределах части высоты балки, остающейся за вычетом поз. 12. 17. Стыковые и угловые швы, прикрепляющие к сжатым элементам ферм и сжатым поясам сплошных балок узловые фасонки или расположенные вдоль усилия фасонки связей, а в сталежелезобетонных пролетных строениях — упоры 18. Угловые поясные швы сжатых поясов сплошных балок 19. Угловые соединительные швы сжатых элементов ферм 20. Угловые соединительные швы пакетов сжатых поясов сплошных балок 21. Угловые швы, прикрепляющие горизонтальные фасонки связей к стенкам балок (за исключением швов, указанных в п. 13 а) 22. Угловые швы, прикрепляющие вертикальные и горизонтальные ребра жесткости, диафрагмы, а также расположенные поперек усилия в элементе, поясе или стенке сплошной балки фасонки связей 23. Угловые швы, прикрепляющие элементы связей к фасонкам и ребрам жесткости | Допускаются единичные дефекты диаметром не более 2 мм в количестве не более 6 дефектов на участке шва длиной 400 мм. Расстояние между дефектами не менее 10 мм. | Согласно указаниям для швов II категории. | Согласно указаниям для швов II категории. |
Примечания: 1. Категории швов сварных соединений сжато-вытянутых элементов зон конструкций — те же, что и растянутых. 2. В конструкциях с ортотропной плитой на швы ее сварных соединений распространяются требования, предъявленные к поясам балок. 3. Ортотропная плита железнодорожного проезда, включенная в работу главных ферм, также относится к элементам ферм. 4. Под шириной стыкового шва понимается расстояние между линиями сплавления металла шва с основным металлом на поверхности детали.
|
(Ш-18-75, табл. 41)
8.53. Методы и нормы контроля сварных соединений стальных конструкций мостов приведены в табл. 38.
Таблица 38
Методы контроля | Нормы контроля для швов сварных соединений категорий | ||
I | II | III | |
1. Систематическая проверка выполнения заданного технологического процесса сборки и сварки | 100 % швов | 100 % швов | 100 % швов |
2. Наружный осмотр и промер швов | 100 % длины швов | 100 % длины швов | 100 % длины швов |
3. Ультразвуковая дефектоскопия | 100 % отнесенной к I кат. длины каждого стыкового и углового шва | 100 % отнесенной ко II кат. длины стыковых и угловых швов по поз. 13а табл. 37; 100 % длины каждого второго стыкового шва II категории по поз. 11 табл. 37 и 50 % длины каждого стыкового шва II кат. по поз. 12 табл. 37 (швы выбираются контролирующим органом). При выявлении дефектов, выходящих за пределы допусков, контролю подлежат 100 % стыковых швов по поз. 11*, 12 табл. 37. | 100 % длины каждого третьего стыкового шва I кат. по поз. 14, 15 табл. 37 (швы выбираются контролирующим органом). Если при этом качество более чем 10 % проверенных стыков признано неудов-летворительным, то производится дополнительный контроль такого количества стыков, чтобы общий объем проверенных ультразвуковой дефектоскопией швов составлял 50 %. Если и при дополнительном контроле выявляются стыковые швы неудовлетворитель-ного качества, то контролю подлежат 100 % стыковых швов данной категории |
4 Просвечивание проникающими излучениями | Швы, результаты проверки которых ультразвуковой дефектоскопией требуют уточнения | ||
5. Металлографические исследования макрошлифов на торцах стыковых швов. | 100 % стыковых швов по поз. 1, 2 табл. 37. за исключением стыковых швов внутренних листов элементов коробчатого сечения. | По два макрошлифа на каждом стыковом шве по поз. 14, 15, табл. 37, в котором при контроле ультразвуковой дефектоскопией выявлены дефекты. Если при осмотре макрошлифов обнаружены недопустимые дефекты, то осматриваются еще два макрошлифа на данном элементе. Если на дополнительных макрошлифах обнаруживаются недопустимые дефекты, то осматриваются макрошлифы на всех стыковых швах данного элемента. | |
_________ * Нормы контроля действуют для швов по поз. 11 и в случае, если недопустимые дефекты обнаружены в швах по поз. 7 табл. 37.
|
(III-18-75, табл. 42)
8.54. При контроле внешним осмотром следует проверить наличие номера или знака сварщика, выполнившего данный шов.
(РМ 12, п. 17.4.6)
8.55. Качество стыковых швов контролируют также по макрошлифам на торцах швов после удаления выводных технологических планок и зачистки кромки.
Качество стыковых швов по торцевым макрошлифам проверяется на поясах главных балок в цельносварных и комбинированных стыках, а также стыках горизонтальных листов опорных диафрагм, поперечных стыках, вставок продольных ребер ребристых плит.
(РМ 12, п. 17.4.2)
8.56. Контроль качества швов сварных соединений конструкций неразрушающими методами следует производить после исправления недопустимых дефектов, обнаруженных внешним осмотром.
(3.03.01-87, п. 8.59)
8.57. Контроль УЗД должен осуществляться до удаления выводных планок посте подготовки поверхности соединений к контролю.
(РМ 12, п. 17.4.3)
8.58. Исправление дефектных сварных швов производится методом сварки, предусмотренным рабочими чертежами КМ. В отдельных случаях по согласованию с представителем института, оказывающего научно-техническую помощь по монтажной сварке, и технического отдела Мостоотряда (Мостопоезда) допускается заварка вскрытого механическим путем (вырезка тонкими шлифовальными дисками и др.) дефектного участка, сваренного автоматом или полуавтоматом, ручной сваркой.
Исправление дефектного участка более двух раз допускается в исключительных случаях после установления причин возникновения данного дефекта. В этом случае в дополнение к применяемым методам контроля сварных швов проверяется качество исходных материалов с помощью химического или спектрального анализа и испытаний механических свойств сварного соединения и металла шва. При проверке необходимо применять материалы, использованные при сварке дефектных швов, и выполнять контрольные образцы по той же технологи.
(РМ 12, п. 17.4.5)
8.59. Сварные соединения, контролируемые при отрицательной температуре окружающего воздуха следует просушивать нагревом до полного удаления замерзшей воды.
(3.03.01-87, п. 8.67)
8.60. Механические испытания контрольных образцов проводят при наличии требований в чертежах КМ и показателем прочности, пластичности и вязкости металла шва и зоны термического влияния сварного соединения.
Число контрольных образцов при механических испытаниях должно быть не менее:
на статическое растяжение стыкового соединения — 2,
на статическое растяжение металла, шва стыкового, углового и таврового соединений — по 3,
на статический изгиб стыкового соединения — 2,
на ударный изгиб металла шва и зоны термического влияния стыкового соединения — 3,
тип образца и места надрезов должны быть указаны в чертежах КМ,
на твердость (НВ) металла шва и зоны термического влияния сварного соединения низколегированной стали (не менее, чем в четырех точках) — 1.
(3.03.01-87, п. 8.68)
8.61. Механическую обработку сварных соединений производят в соответствии с ВСН 188-78. Контроль качества производится визуальным осмотром.
При контроле в соответствии с ВСН 188-78 проверяют: выполнение обработки во всех зонах, оговоренных проектом; соответствие форм и качества обработки; чистоту поверхности металла в зоне обработки; радиусы переходов; отсутствие на обработанной поверхности рисок, расположенных поперек направления усилий, действующих в элементе при его работе; отсутствие в зоне обработки ослабления сечения, превышающего установленный нормами допуск; отсутствие острых кромок и заусениц, а также поверхностных ожогов металла.
Увеличение зоны обработки и радиусов перехода не является браковочным признаком.
(РМ 12, пп. 17.5.1 и 17.5.2)
8.62. Приемочный контроль выполненных сварных стыковых соединений арматуры должен предусматривать внешний осмотр и комплекс испытаний, проводимых в соответствии с ГОСТ 10922-90 и ГОСТ 23858-79.
Объем партии сварных соединений выпусков арматуры устанавливается теми же стандартами. Бетонирование конструкции до получения результатов оценки качества сварных соединений не разрешается.
(3.03.01-87, п. 8.77)
8.63. Подварку допускаемых к исправлению дефектов следует производить электродами диаметром 4 мм после зачистки места дефекта абразивным инструментом и предварительного подогрева стыка до 200-250°С.
(3.03.01-87, п. 8.78)
8.64. Сварные стыковые соединения арматуры, не удовлетворяющие требованиям ГОСТ 10922-90 и ГОСТ 23858-79 необходимо вырезать. На место вырезанного стыка следует вварить промежуточную вставку длиной не менее 80 мм с последующим ультразвуковым контролем двух выполненных сварных соединений.
(3.03.01-87, п. 8.79)
8.65. Результате механических испытаний сварных стыковых соединений арматуры заносятся и контрольную карту (приложение 67).
8.66. Сварные стыковые соединения при монтаже сборных железобетонных конструкций перед замоноличиванием стыков должны быть приняты с оформлением приемки актом (приложение 68).
8.67. Во всех случаях обнаружения дефектов в сварных швах работники технического надзора совместно с руководителями сварочных работ на основе данных контроля должны установить причины возникновения дефектов, разработать мероприятия по ремонту швов и проследить в дальнейшем, чтобы появление подобных дефектов не повторялось.
(РМ 12, п. 17.4.7).
8.68. Смонтированные конструкции стальных пролетных строений со сварными соединениями до загружения их строительными и эксплуатационными нагрузками должны быть приняты в порядке, предусмотренном п. 6.50 «Пособия».
Глава 9
СООРУЖЕНИЕ ДЕРЕВЯННЫХ МОСТОВ
9.1. Правила и рекомендации, изложенные в настоящей главе «Пособия» распространяются на производственный контроль качества при строительстве деревянных мостов под железную и автомобильную дороги.
9.2. В деревянных мостах, как правило, следует применять элементы заводского изготовления, а элементы железнодорожных мостов и элементы всех мостов с клеевыми соединениями — только заводского изготовления.
(2.05.03-84*, п. 6.1)
9.3. Конструкции, изделия и материалы, применяемые при возведении деревянных конструкций, должны отвечать требованиям соответствующих норм, стандартов, технических условий и рабочих чертежей.
(3.03.01-87, п. 1.6)
9.4. Деревянные конструкции должны поставляться предприятием-изготовителем комплектно с элементами соединений. К комплекту должны быть приложены: документ о качестве (паспорт на конструкцию или изделие, спецификация, инструкция по сборке, акты на выполненную защитную обработку).
9.5. При приемке (входном контроле) поступающих на строительство сборных деревянных конструкций должно быть установлено: сопоставление конструкций требованиям норм и проекта, комплектность поставляемых конструкций, наличие технической документации, маркировки и клейма предприятия-изготовителя, отсутствие в элементах деформации и повреждений.
9.6. При приемке клееных деревянных конструкций следует также учитывать требования ГОСТ 20850-84.
Конструкции, имеющие или получившие при транспортировании и хранении дефекты и повреждения, устранение которых в условиях стройплощадки не допускается (например, расслоение клеевых соединений, сквозные трещины и т.д.), запрещается монтировать до заключения проектной организации-разработчика. В заключении выносится решение о возможности применения, необходимости усиления поврежденных конструкций или замене их новыми.
(3.03.01-87, п. 5.1)
9.7. Приемку с входным контролем по СНиП 3.01.01-85*, сортировку и обмер лесоматериалов следует производить с учетом породы древесины и вида лесоматериалов согласно требованиям ГОСТ 2292-88*, ГОСТ 6564-84*, ГОСТ 3808.1-80*, ГОСТ 6782.2-75*, ГОСТ 9014.0-75* и ГОСТ 6782.1-75*, естественную сушку — по ГОСТ 3808.1-80* и ГОСТ 6782.2-75*, хранение — по ГОСТ 9014.0-75*.
(3.06.04-91, п. 8.4)
9.8. Параметр допустимой шероховатости поверхности элементов из пиломатериалов, в том числе предназначенных для покраски, должен соответствовать требованиям ГОСТ 7016-82*.
(3.06.04-91, п. 8.5)
9.9. Для деревянных конструкций мостов следует применять древесину сосны, ели, лиственницы, пихты, удовлетворяющим требованиям ГОСТ 9463-88* и ГОСТ 8486-86*Е растянутые и изгибаемые элементы пролетных строений и мостовые брусья должны выполняться из древесины первого сорта. Остальные элементы конструкций мостов могут быть выполнены из древесины 2 сорта.
9.10. Допуски, характеризующие точность изготовления и сборки деревянных конструкций, следует определять по ГОСТ 21779-82. Остальные отклонения не должны превышать допустимых отклонений по СНиП 3.06.04-91, таб. 27.
9.11. Деревянные конструкции и их элементы при хранении должны быть защищены от воздействия атмосферных осадков и солнечной радиации. Элементы в штабелях должны опираться на неповреждающие древесину прокладки между элементами и грунтовым основанием не менее 20 см.
Клееные главные балки пролетных строений следует хранить в положении, соответствующем рабочему положению их в конструкции.
(3.06.04-91, п. 8.10)
Глава 10
ЗАСЫПКА УСТОЕВ МОСТОВ.
УКРЕПИТЕЛЬНЫЕ РАБОТЫ
10.1. Засыпку устоев мостов следует выполнять после освидетельствования качества засыпаемых грунтов и проверки соответствия проекту выполненных работ по возведению конструкций, устройства дренажей и гидроизоляции.
(3.06.04-91, п. 9.1)
10.2. При выполнении работ по засыпке устоев мостов необходимо соблюдать требования СНиП II-39-76.
В случае возведения сооружений в районах распространения вечной мерзлоты следует соблюдать также специальные указания проекта в части подготовки оснований под засыпку и температурного режима засыпки в зависимости от принципа использования грунтов основания в период эксплуатации.
10.3. Отсыпку конусов у мостов, а также участков насыпей за устоями мостов (на длину, равную высоте насыпи за устоем плюс 2 м по верху и не менее 2 м — в уровне естественной поверхности) и засыпку прогалов за подпорными стенками следует выполнять дренирующими грунтами с коэффициентом фильтрации не менее 2 м/сут.
Послойное уплотнение грунта конусов следует начинать от бровки Откоса и выполнять продольными ходами вокруг устоя.
Грунты конусов и насыпей за устоями мостов, а также прогалов за подпорными стенками следует уплотнять виброударными машинами или навесными вибротрамбовками.
(3.06.04-92, п. 9.8)
При выполнении работ по засыпке устоев мостов необходимо производить промежуточный контроль качества засыпки с оформлением акта промежуточной приемки работ. (Приложение № 69).
10.4. При засыпке устоев мостов в зимнее время должны вестись наблюдения (с записью в журнал производства работ) за температурой укладываемого грунта, за тем, чтобы в засыпке не было снега и льда. В журнале также следует указывать способы контроля плотности.
10.5. Толщина отсыпаемых слоев грунтов (в плотном теле), конусов должна быть не менее 0,50-0,65 м для песчаных грунтов при уплотнении машинами на базе тракторов ДТ-75 или Т-130Г и 0,20-0,25 м при уплотнении пневмокатками массой 25-30 т.
(3.06.04-91, Таблица 29)
10.6. Надводные периодически подтопляемые откосы конусов, подходных насыпей защитных и регуляционных сооружений должны быть предварительно спланированы, как правило, срезкой грунта.
Подсыпка допускается при условии доведения ее плотности до проектной. Подводные постоянно затопленные откосы всех сооружений и склоны берегов и дна рек должны быть очищены от крупных предметов (остатков строительных конструкций, карчей, топляка и т.п.) и спланированы срезкой или подсыпкой в соответствии с требованиями проекта без последующего уплотнения.
(3.06.04-91, п. 9.12)
10.7. Плиты и блоки решетки следует укладывать на откос от подошвы к гребню сооружения. В покрытии из плит швы следует омоноличивать до затопления откоса. На постоянно затопленные откосы или подводные склоны и дно реки покрытия из гибких плит необходимо укладывать картами площадью более 100 кв.м в виде «чешуи» с нахлестом 0,5-1,5 м с помощью специальных устройств в соответствии с ППР. Швы между плитами в картах омоноличивать не следует.
(3.06.04-91, п. 9.15)
10.8. Технические требования по укрепительным работам, а также методы и способы контроля приведены в табл. 39.
Таблица 39
Технические требования | Контроль | Метод и способ контроля |
1. Отклонение поверхности грунта откоса от проектной ± 5 см | 2 замера на поперечнике с шагом, указанным в проекте | Измерительный (измерение откосным шаблоном и линейкой) |
2. Характеристика подготовки из щебня, гравия, песчано-гравийных смесей — по СНиП 2.05.02-85, ГОСТ 8267-82*, ГОСТ 10260-82*, ГОСТ 8736-85, ГОСТ 3344-83 | 1 раз на партию материалов | Проверка по ГОСТ 3394-83 ГОСТ 8269-87* ГОСТ 8735-88 ГОСТ 25607-83* |
3. Минимальная толщина слоев подготовки, см: 10 — при ручной укладке, 15 — при укладке механизмами | 1 замер на 200 кв.м откоса | Измерительный (измерение линейкой) |
4. Отклонение поверхности подготовки (ровность) + 3 см на базе 5 м | То же | Измерительный (измерение шаблоном и линейкой) |
5. Характеристика геотекстиля (подготовки): коэффициент фильтрации Кф — 0,02 см/с, поверхностная плотность не менее 500 гр/кв.м, прочность на размыв не менее 30 кг на полосу шириной 5 см. | На заводе-изготовителе по ТУ на геотекстиль | Проверка по ТУ на геотекстиль |
6. Допускаемый нахлест полотен геотекстиля при стыковании не менее 10 см при сварке и склейке сплошным швом | 1 замер на 50 м длины шва | Измерительный (измерение линейкой) |
7. Превышение граней смежных бетонных и железобетонных плит не более 10 мм, ширина раскрытия швов в конструкциях без омоноличивания не более 10 мм; при большем раскрытии швы омоноличиваются | 1 замер на 100 кв.м поверхности откоса | То же |
10.9. Производство и приемку работ по укреплению поверхности конусов и других защитных и регуляционных сооружений путем посева трав и одерновки следует выполнять согласно главы СНиП 3.02.01-87.
Глава 11
ГИДРОИЗОЛЯЦИЯ И ВОДООТВОД
11.1. Правила и рекомендации, изложенные в настоящей главе, распространяются на производственный контроль за качеством работ по устройству гидроизоляции и водоотвода с проезжей части балластного корыта железобетонных и сталежелезобетонных пролетных строений и устоев железнодорожных мостов, плиты проезжей части и тротуаров железобетонных сталежелезобетонных, стальных с железобетонной плитой проезжей части пролетных строений и устоев автодорожных и городских мостов, путепроводов и других мостовых сооружений.
Контроль качества работ по устройству гидроизоляции мостов следует выполнять с соблюдением требований СНиП 3.04.01-87, СНиП 3.06.04-91, ВСН 32-81.
11.2. Гидроизоляция должна выполняться в соответствии с проектом конструкции и проектом производства работ, учитывающих технологические характеристики применяемых материалов, климатические условия района строительства и местные особенности производства работ.
11.3. Применяемые для устройства гидроизоляции материалы должны соответствовать характеристикам, указанным в проекте и удовлетворять требованиям ГОСТ и технических условий на их изготовление. Не допускается применять гидроизоляционные материалы при отсутствии сертификата (паспорта) завода-изготовителя или его копни, подтверждающие их свойства.
11.4. Замена предусмотренных проектом материалов, изделий и составов допускается только по согласованию с проектной организацией и заказчиком.
(3.04.01-87, п. 1.2)
11.5. Применяемые для устройства гидроизоляции материалы должны соответствовать указанным в проекте характеристикам и требованиям стандартов и технических условий на их изготовление. Не допускается применять гидроизоляционные материал при отсутствии сертификата. В случае, когда при визуальном осмотре качество материала вызывает сомнение, необходимо произвести его проверку в лаборатории в соответствии со стандартами и ТУ.
(3.06.04-91, п. 10.18)
11.6. Применяемые для устройства гидроизоляции грунтовки приготавливают на месте с соблюдением составов указанных в табл. 40.
(ВСН 32-81, п. 2.3)
Таблица 40
Вид грунтовки | Состав грунтовки: | Вязкость грунтовки | |
Материал | Содержание по массе, % | по ВЗ-4 при 20°С | |
Битумная | Горячий битум | 25-30 | 10-15 |
Бензин | 75-70 | ||
Изольная | Мастика изол | 30 | 10-15 |
Бензин | 70 | ||
Тиоколовая | Тиоколовые герметик или мастика | 50 | 10-15 |
Растворители р-4, р-5, 647 | 50 | ||
Битумно-каучуковая | Битумно-каучуковая мастика | 50 | 10-15 |
Бензин или скипидар | 50 | ||
Примечание: Технология приготовления грунтовок должна соответствовать требованиям ВСН 32-81.
|
(ВСН 32-81, прил. 1, табл. 2)
11.7. Состав битумных мастик для гидроизоляции конструкций мостов и труб в зависимости от климатической зоны должны соответствовать указаниям табл. 41.
Таблица 41
Состав мастик в частях по массе | |||
Климатические зоны | |||
Компоненты мастик | I | II | III |
Марки мастик | |||
Ю-1 | Ю-2 | С 3 | |
Битум нефтяной пластбит для изоляции нефтегазопроводов или мастика МБР | 95-100 | 85-90 | 75-80 |
Индустриальное масло | 5-0 | 15-10 | 25-20 |
Асбест № 7 | 0 | 0 | 25-20 |
Битум нефтяной строительный | 90-100 | 75-80 | — |
Индустриальное масло | 10-0 | 25-20 | — |
Асбест № 7 | 0 | 25-0 | — |
Битум нефтяной БНК | 95 | 85-90 | — |
Индустриальное масло | 5 | 15-10 | — |
Асбест № 7 | 0 | 25-0 | — |
Примечание: Составы мастик принимают на основе их подбора по результатам лабораторных испытаний
|
(ВСН 32-81. Прил. 1, табл. 3)
Таблица 42
Климатические зоны | ||||
Показатели | I | II | III | Методы испытаний |
Расчетная температура, °С | Выше -20 | От -20 | Ниже -40 | — |
до -40 | — | |||
Марки мастики | Ю-I | Ю-II | С-3 | |
Температура размягчения по методу «кольцо и шар», °С не ниже | + 68 | + 61 | + 54 | ГОСТ 11506-73* |
Глубина проникания иглы, 0,1 мм: при + 25°С, не менее | 35 | 50 | 100 | ГОСТ 11501-78* |
при 0°С, не менее | 10 | 15 | 25 | ГОСТ 11501-78* |
Растяжимость при 25°С, не менее | 2 | 3 | 4 | ГОСТ 11505-75* |
Температура хрупкости по Фраасу, °С не выше | -17 | -25 | -35 | ГОСТ 11507-78 |
Хладостойкость. Отсутствие трещин при изгибе образца, выдержанного в хладоагенте (сухой лет + спирт) 30 мин на шаблоне с радиусом кривизны 250 мм при температуре °С не менее | -20 | -30 | -40 | Изгибается образец со слоем мастики толщиной 1 мм нанесенный на полоску гидроизола размером 150 х 50 мм |
Теплостойкость. Отсутствие отекания мастики с образца, выдержанного 2 ч в термостате при температуре, °С | + 65 | + 50 | + 45 | Испытывается слой мастики, нанесенной на полоску гидроизола размерами 100х50 мм, вертикально подвешенную в термостате |
(ВСН 32-81, табл. 1)
11.8. Требования к физико-механическим показателям битумных мастик приведена в табл. 42.
11.9. Гидроизоляционные утяжеленные битумные и резиноподобные материалы, холодные тиоколовые и битумно-каучуковые мастики, армирующие материалы, должны соответствовать по своим физико-механическим показателям требованиям ВСН 32-81 (Минтрансстрой и МПС).
11.10. Образцы мастик и грунтовок для устройства изоляции и деформационных швов до начала работ должны быть проверены в лабораториях и удовлетворять требованиям, приведенным в проекте для данной климатической зоны и условий производства работ. Повторные испытания мастик и грунтовок производятся в случаях изменения состава и качества применяемых материалов.
Запрещается применение мастик и грунтовок, подобранных без лабораторной проверки.
11.11. Гидроизоляционные материалы, не израсходованные потребителем и течение установленных ГОСТами или ТУ допустимых сроков хранения могут быть применены, если проверочными испытаниями будет подтверждено соответствие качественных показателей требованиям нормативных документов.
(ВСН 32-81, п. 2.12)
11.12. Цементно-песчаный раствор (мелкозернистый бетон) подготовительного (выравнивающего) и защитного слоя гидроизоляции должны иметь водоцементное отношение не выше 0,42 и марку по прочности не ниже М300 для пролетных строений, марку по морозостойкости во всех случаях равную 200 для 1 и 300 — для II и III климатических зон; содержать, как правило, а для III климатической зоны обязательно, воздухововлекающие газообразующие и пластифицирующие добавки (типа СНВ, ГКЖ-94, СДБ). Введение химических добавок-ускорителей твердения, вызывающих коррозию бетона и арматуры запрещается.
(ВСН 32-81, п. 2.6)
11.13. Арматурная сетка защитного слоя должны быть одинарной из проволоки диаметром 2-4 мм и размерами ячейки в свету 45-75 мм и не иметь антикоррозионной смазки.
(ВСН 32-71, п. 2.9)
11.14. Гидроизоляционные работы в условиях строительной площадки выполняют при отсутствии атмосферных осадков и температуре наружного воздуха не ниже плюс 5°С, в ветреную и дождливую погоду — под покрытием легких разборных тентов или шатров.
В зимнее время и при температуре наружного воздуха ниже плюс 5°С, гидроизоляционные работы следует выполнять под прикрытием сборно-разборных тепляков с обеспечением в них положительной температуры. Тепляки следует обогревать электрокалориферами; использование коксовых жаровен и других приборов с открытым пламенем для нагрева воздуха в тепляках запрещается.
Гидроизоляционные работы с применением наплавляемых рулонных материалов (тип БРН) и резиноподобных (типа РПР) допускается выполнять при отрицательной температуре до минус 10°С, а с применением полиэтиленовой пленки (тип ПЭР) — до минус 15°С.
(ВСН 32-81, п. 5.3)
11.15. Устройству гидроизоляции должна предшествовать подготовка изолируемого основания приданием ему проектного профиля путем укладки выравнивающего слоя толщиной не менее 30 мм с учетом требований п. 11.12 «Пособия». На поверхности выравнивающего слоя не должно быть раковин, острогранных включений, бугров и других дефектов. Раковины устраняют заделкой цементно-песчаным раствором, бугорчатые неровности — механической шлифовкой. В местах пересечения изолируемых поверхностей устраивают выкружки радиусом закругления 10-15 см.
(ВСН 32-81, п. 5.7)
11.16. К началу выполнения гидроизоляционных работ прочность раствора или бетона выравнивающего слоя должны быть не менее 50 кг/см2 (5 МПа).
(ВСН 32-81, п. 5.8)
11.17. Перед устройством гидроизоляции поверхность выравнивающего слоя должны быть очищена от мусора, промыта струей воды и высушена.
(ВСН 32-81, п. 5.9)
11.18. Сухую и чистую поверхность выравнивающего слоя покрывают грунтовкой, соответствующей принятому в проекте типу гидроизоляции. Грунтовку в условиях строительной площадки изготавливают с соблюдением требований табл. 40. Огрунтовка изолируемого снования, покрытого снегом или льдом запрещается.
(ВСН 32-81, п. 5.10)
11.19. Интервал между нанесением грунтовки и началом устройства гидроизоляционных слоев должен быть не менее 2 ч и не более 16 ч.
(ВСН 32-81, п. 5.12)
11.20. При производстве работ по устройству гидроизоляции осуществляется операционный контроль в соответствии с требованиями, приведенными в табл. 43.
11.21. Гидроизоляция у водоотводных трубок и в местах расположения столбов, прерывающих сплошность гидроизоляционного ковра, должна быть выполнена перед устройством гидроизоляции всей изолируемой поверхности. Дополнительная гидроизоляция у водоотводных трубок должна быть заведена в их раструб и плотно обжата вставляемым и него металлическим стаканом, предварительно покрытым битумной грунтовкой.
Все зазоры между деталями водоотводных трубок должны быть тщательно заделаны.
Гидроизоляция в месте сопряжения с водоотводными трубками не должна иметь местных утолщений, препятствующих стоку воды.
(3.06.04-91, п. 10.23)
11.22. При выполнении гидроизоляционных работ следует контролировать соответствие качества гидроизоляции требованиям проекта, СНиП 3.04.01-87, СНиП 3.06.04-91, ВСН 32-81, проверить герметичность у водоотводных трубок и деформационных швов, а также в местах примыкания (в углах, к бортикам, бордюрам и столбам) и, кроме того, качество выравнивающего, изолирующего и защитного слоев.
Таблица 43
Технические требования | Контроль | Способ контроля |
1. Допускаемая температура окружающего воздуха при устройстве гидроизоляции, °С, не ниже: на заводе — 5 | На каждом мосту | Измерительный (измерение термометром) |
на строительстве с применением битумных мастик — 5 | » | То же |
То же, из резиноподобных и наклеиваемых методом наплавления рулонных битумных материалов — минус 10 | » | » |
То же из полиэтиленовой пленки — не ниже минус 15 | » | » |
2. Температура рабочих составов горячих битумных мастик 160-180°С | Каждой партии мастики | » |
3. Допускаемые нахлест и смещение стыков рулонных гидроизоляционных материалов и армирующих слоев, мм: нахлест в первом слое — не менее 100 | Каждого слоя | Измерительный (измерение линейкой) |
смещение в последующих слоях по отношению к стыкам предыдущего слоя — не менее 300 | То же | То же |
4. Покрытие местных повреждений гидроизоляционного ковра заплатой от края повреждения — не менее 200 мм | Каждого повреждения | » |
(3.06.04-91, табл. 22, пп. 2-5)
В слоях гидроизоляции не должно быть непроклеев, складок, проколов и других механических повреждений. На все обнаруженные в каждом слое повреждения гидроизоляции должны быть поставлены заплаты.
(3.06.04-91, п. 10.24)
11.23. Гидроизоляция, выполненная на месте строительства, должна быть принята представителем заказчика и оформлена надлежащими актами (приложение 70).
При контроле гидроизоляции проверке подлежат:
качество применяемых материалов и правильность приготовления на месте составов мастик и грунтовок;
состояние подготовленной поверхности и ее соответствие проекту;
правильность выполнения гидроизоляции в местах примыканий, сопряжений и стыков (у водоотводных трубок, деформационных швов и в местах примыкания изоляции в углах, к бортикам, бордюрам, тротуарам, столбам);
соответствие конструкции гидроизоляции проекту и проверка ее толщины;
сцепление гидроизоляции с выравнивающим слоем и отдельных слоев между собой;
правильность армирования гидроизоляции;
состояние поверхности слоев гидроизоляции.
(ВСН 32-81, пп. 7.1, 7.2)
11.24. Ровность выравнивающего слоя проверяют:
на проезжей части автодорожных мостов — контрольной трехметровой рейкой, просветы под которой в количестве не более двух не должны превышать 5 мм в направлении вдоль уклона и 10 мм — поперек уклона;
на блоках железнодорожных пролетных строений — специальными шаблонами.
(ВСН 32-81, п. 7.4)
11.25. Сцепление гидроизоляционных слоев с основанием и между собой проверяют путем медленного их отрыва на небольшом участке.
Прочность наклейки считается достаточной, если отрыв битумной гидроизоляции произойдет по слою мастики, а тиоколовой — по контакту с выравнивающим слоем с повреждением его поверхности.
Наличие неприклеенных мест обнаруживают по глухому звуку при простукивании поверхности только гидроизолирующего слоя.
(ВСН 32-81, п. 7.5)
11.26. Толщину гидроизоляционного слоя в необходимых случаях проверят контрольными надрезами с замером толщины отогнутых концов, а тиоколовой гидроизоляции — с помощью иглы, погружаемой в незавулканизирующийся слой.
Проколы и надрезы изоляции, служащие для контроля ее толщины и прочности сцепления с основанием допускаются не более одного на каждые 10 м2. После проверки места проколов и надрезов следует тщательно заделать.
(ВСН 32-81, п. 7.6)
11.27. Состояние поверхности гидроизоляции проверяют визуально, фиксируя подлежащие устранению дефекты-вздутия, складки, просветы армирующих материалов, разрывы и т.д.
Обнаруженные дефекты или отклонения от проекта должны быть устранены до устройства защитного слоя.
(ВСН 32-81, п. 7.7)
11.28. При устройстве обмазочной гидроизоляции нанесение каждого последующего слоя изоляции допускается после освидетельствования качества затвердевшего предыдущего слоя.
Готовая обмазочная гидроизоляция должна быть сплошной, не иметь раковин, вздутий и отслоений. Все обнаруженные дефектные места надлежит расчистить и покрыть заново.
11.29. При устройстве гидроизоляции деформационных швов контролируются: правильность подготовки шва под изоляцию (очистка, конопатка), состав мастики и тщательность заполнения шва (мастикой, поропластом и т.п.), прочность крепления компенсаторов, герметичность швов в местах нахлестки между отдельными листами и в местах сопряжения компенсаторов с гидроизоляцией, правильность выполнения гидроизоляции швов в местах перехода с горизонтальной поверхности на вертикальную.
11.30. После устройства деформационных швов должна проверяться их герметичность путем контрольной заливки водой с проезжей части.
11.31. Данные о производстве работ по устройству гидроизоляции ежесменно заносятся в «Журнал работ по гидроизоляции, антикоррозионной защите, окраске стальных конструкций» (приложение 71).
11.32. Промежуточной приемке с составлением актов на скрытые работы с участием представителей технадзора заказчика и в необходимых случаях авторского надзора подлежат: установка водоотводных трубок и подготовленное под гидроизоляцию основание, нанесение грунтовки и первого слоя изоляции, нанесение каждого последующего слоя, выполнение гидроизоляции на участках, подлежащих закрытию грунтом, кладкой или защитным ограждением, устройство деформационных швов, устройство защитного слоя по изоляции (приложения 70 и 72).
При изготовления на полигонах пролетных строений мостов под ж.д. или их блоков, а также блоков устоев, гидроизоляция в балластных корытах должна быть принята заводской инспекцией пооперационно и в законченном виде. Отметки о приемке заносятся в Паспорт изделия.
Окончательная приемка гидроизоляции оформляется актом (приложение 72).
Глава 12
УСТРОЙСТВО МОСТОВОГО ПОЛОТНА
12.1. Правила и рекомендации, изложенные в настоящей главе распространяются на производственный контроль качества работ по устройству мостового полотна железнодорожных, автодорожных и городских мостов.
12.2. Устройство и конструкция мостового полотна железнодорожных, автодорожных и городских мостов должны отвечать требованиям проекта, СНиП 3.06.04-91, а также действующих правил и инструкций.
УСТРОЙСТВО МОСТОВОГО ПОЛОТНА
ЖЕЛЕЗНОДОРОЖНЫХ МОСТОВ
12.3. Работы по устройству мостового полотна следует начинать после закрепления пролетных строений на постоянных опорных частях.
До начала производства работ по устройству пути на балласте должны быть выполнены и приняты с оформлением акта (Приложение 72) все работы по устройству гидроизоляции и водоотвода.
12.4. На цельноперевозимых блоках пролетных строений надлежит обследовать состояние гидроизоляции, выполненной на предприятиях или полигонах и при необходимости выполнить ремонтные работы.
12.5. В соответствии с «Указаниями по устройству и конструкции мостового полотна на железнодорожных мостах» МПС в качестве балласта на мостах используется щебень из естественного камня по ГОСТ 7392-85.
Мостовые брусья должны изготавливаться из сосны или лиственницы не ниже 1 сорта по ГОСТ 8486-86Е* с ограничениями по порокам древесины согласно ГОСТ 2140-81 *.
Другие породы древесины допускаются только с разрешения Главного управления пути МПС.
Брусья пропитываются масляными антисептиками.
12.6. Перед отсыпкой балластного слоя вокруг крышек водоотводных трубок должен быть уложен щебень или галька крупностью 80-120 мм. При отсыпке и уплотнении балласта, а также при укладке пути следует принимать меры по предохранению гидроизоляции от повреждения.
Мостовые брусья, укладываемые на шкафных стенках устоев, следует прирубать по высоте по всей площади опирания и закреплять.
(3.06.04-91, пп. 10.2, 10.3)
12.7. Вырубки и отверстия в брусьях для болтов, костылей и шурупов необходимо антисептировать, трещины заделывать антисептической пастой, а концы брусьев стягивать полосовым железом. На брусьях следует проставить год укладки.
(3.06.04-91, п. 10.4)
12.8. Контроль качества работ по устройству мостового полотна со стальными поперечинами, а также по укладке пути на безбалластные железобетонные плиты должны выполняться по специальным указаниям и рабочей документации.
12.9. Уложенное мостовое полотно до пропуска поездной нагрузки должно быть принято представителем дистанции пути или отдела временной эксплуатации строительства.
Обнаруженные дефекты должны устраняться до пропуска поездной нагрузки.
Открытие рабочего движения при отсутствии предусмотренной проектом гидроизоляции проезжей части моста с защитным слоем не допускается.
(3.06.04-91, п. 10.8)
12.10. Технические требования, которые следует соблюдать при устройстве верхнего строения пути на железнодорожных мостах и проверять при операционном контроле, а также объем и способы контроля приведены в табл. 44.
12.11. Контроль качества работ по устройству безбалластного мостового полотна на железнодорожных мостах следует выполнять в соответствии с рабочими чертежами и «Инструкцией по применению безбалластного мостового полотна на железобетонных плитах на металлических пролетных строениях железнодорожных мостов», утвержденной МПС 23.08.79 г.
УСТРОЙСТВО МОСТОВОГО ПОЛОТНА
Дата добавления: 2018-05-02; просмотров: 430; Мы поможем в написании вашей работы! |
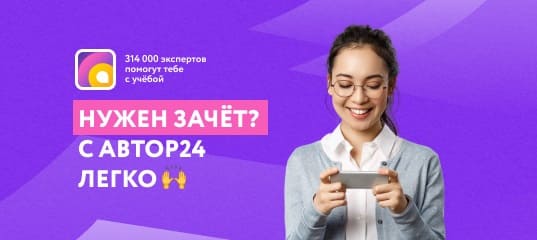
Мы поможем в написании ваших работ!