Технология изготовления корпуса РДТТ
В элементах конструкций ракетных двигателей используют практически все виды конструкционных КМ, различные типы теплозащиты и специальные покрытия (табл. 6.1).
Таблица 6.1 Композиты в элементах конструкции ракетных двигателей
Наименование элемента конструкции двигателя | КМ, применяемые при изготовлении конструкций |
Силовые оболочки корпусов твердотопливных двигателей Силовые бандажи, соединительные "юбки" Закладные фланцы корпуса, закон-цовки соединительных отсеков Элементы соплового блока твердотопливных двигателей: воротники, критические вставки, выходные раструбы Выходные раструбы жидкостных двигателей (насадки) Камеры микрожидкостных двигателей Корпуса газогенераторов | Органопластик, углепластик, стеклопластик Стеклоуглепластик, боропластик, углепластик, органопластик Металлокомпозиты на легкоплавкой матрице (AIB, MgB, AIC, MgC) Углепластик, УУКМ УУКМ УУКМ, карбидоуглеродный КМ Жаропрочные металлокомпозиты (вольфрам — никель, вольфрам — 1 титан, сталь - ниобий) |
На рис. 6.1 показано изменение относительной массовой характеристики корпусов РДТТ трех ступеней межконтинентальной баллистической ракеты "Минитмен" по годам за счет применения новых материалов и технологий изготовления.
Типовая конструкция цельномотаного корпуса РДТТ из полимерных волокнистых композитов с полюсными отверстия-
|
|
6. ПРОЦЕССЫ ИЗГОТОВЛЕНИЯ КОНСТРУКЦИЙ ИЗ КОМПОЗИТОВ
ми и конструктивно-технологическая схема его организации представлена на рис. 6.2. Основным элементом корпуса (рис. 6.2, а) является силовая оболочка (рис. 6.2, б) как силовой элемент камеры сгорания двигателя. Внутренняя теплозащита
Рис.6.1. Изменение относительной массы корпусов РДТТ баллистической ракеты "Минитмен":
1, 2, 3 - первая, вторая, третья ступени; стальной корпус;
стеклопластиковый; органопластиковый
|
Рис. 6.2. Конструктивно-технологическая схема организации корпуса РДТТ:
а - корпус РДТТ из полимерных композитов; б - СО с узлами стыка; в - ТЗП корпуса с фланцами
408
409
6А. Технология изготовления корпуса РДТТ
(рис. 6.2, в) предохраняет силовую оболочку от воздействии продуктов сгорания топлива. Передний фланец соединяет кор пус с воспламенительным устройством. Задний фланец прел назначен для соединения соплового блока с корпусом РДTТ С помощью узлов стыковки корпус ракеты соединяют с еёсмежными элементами (переходные отсеки, ступени). Компен сационный клин применяют для снятия экстремальных, нор мальных и сдвиговых напряжений в СО и УС.
Поэлементная организация СО, УС и ТЗП, которые пред ставляют собой типовые конструкторские решения, показана рис. 6.3.
|
|
Рис. 6.3. Поэлементная организация типовых ТЗП, днищ СО, УС
Рассмотрим технологические процессы изготовления кор пуса РДТТ.
Силовая оболочка корпуса. Конфигурация СО и схема её армирования должны быть такими, чтобы при действии экс плуатационных нагрузок корпус деформировался в предела допустимых значений. Классической конфигурацией СО кор пуса двигателя является конструкция типа "кокон", выполнен ная в виде цилиндрической оболочки, с овалоидными осесим метричными днищами. В малогабаритных двигателях днища обычно имеют сферическую форму, в корпусах крупногабарит ных двигателей — изотензоидную форму. Существует два тех
6. ПРОЦЕССЫ ИЗГОТОВЛЕНИЯ КОНСТРУКЦИЙ ИЗ КОМПОЗИТОВ
нологических метода формирования силовой оболочки ~ методы спиральной и плоскостной (или орбитальной) намотки. В первом случае арматура наматывается на оправку спирально-винтовыми витками по» равновесным геодезическим траекториям, и цилиндрическая часть корпуса дополнительно бан-дажируется кольцевыми слоями. Тангенциальные напряжения при нагружении в такой конструкции воспринимаются одновременно волокнами спирально-перекрестной и кольцевой систем оболочки, а коаксиальные напряжения растяжения ~ только волокнами спирально-перекрестной системы.
|
|
Во втором случае арматура наматывается плоскими непрерывными витками, укладываемыми на оправку под углом 17° к оси симметрии (воспринимают коаксиальные напряжения), а на цилиндрическую часть наматываются кольцевые слои, воспринимающие тангенциальные напряжения при действии внутреннего давления.
Днища с фланцами. В полярные отверстия СО вматываются фланцы, изготавливаемые из высокопрочных легких сплавов (алюминиевых или титановых) или прессованные из композитов. Соединение СО с фланцем осуществляют склеиванием через эластичный промежуточный слой, выполняющий функции компенсатора термоупругих деформаций и упругого шарнира при передаче нагружения с фланца на СО. Кроме того, в эластичной прослойке имеется специальный локальный компенсатор в виде местного раскрепления (расслоения) шарнира. Обычно фланцы изготавливают совместно с элементами конструкции теплозащиты (см. рис. 6.2, в), собирают и устанавливают на оправку перед намоткой силовой оболочки. В процессе намотки арматуры СО витки нитей охватывают петлями перо фланца, образуя конфигурацию днища. Петельная структура законцовки днища создает кромку полюсного отверстия, которая является основным элементом, передающим нагрузки от фланца на СО корпуса.
|
|
Узлы стыка корпуса. Для соединения корпуса с другими агрегатами ракеты в корпусе предусматривают специальные стыковочные узлы, которые имеют форму цилиндрических "юбок", скрепленных с СО корпуса. Конструкция УС и метод соединения "юбки" и шпангоута могут быть самыми разнообразными (рис. 6.4). Наиболее часто используют два типа кон-структорско-технологических решений: "юбки" композитные
410
411
6.1. Технология изготовления корпуса РДТТ
с металлическими шпангоутами и "юбки", целиком изготов-ленные из КМ. В обоих случаях цилиндрическая конструкция "юбки" воспринимает и передает на СО нагрузки сжатия, растяжения и изгиба. Цилиндрическую часть "юбки" армируют| продольными слоями под углом 0° (для передачи нагрузки) и кольцевыми слоями (для обеспечения жесткости конструкции) Кроме того, в ряде случаев используют перекрестное армиро вание под углами ± 45°. Торцевые стыковочные шпангоуты обеспечивают точность и надежность соединения с другими элементами конструкции ракеты. Как и в системе СО — фланец, в соединении "юбок" с СО корпуса для компенсации термоупругих, отрывающих и касательных напряжений предус- матривают эластичные компенсаторы в виде прослойки с клиновым утолщением в развилке.
Рис.6.4. Конструктивная организация "юбки" корпуса РДТТ:
/ - ТЗП; 2 - компенсационный резиновый клин; 3 - "юбка" из КМ;
4 — СО из композита; 5 — стыковочный фланец из алюминиевого
сплава
Теплозащита корпуса. Элементы конструкции корпуса дви гателя должны быть защищены от теплового воздействия высокотемпературных продуктов сгорания твердого топлива Вследствие сложной конфигурации, низкой и изменяющейся по длине жесткости СО, больших деформаций и перемещения днищ относительно фланцев, газо- и влагопроницаемости сте нок корпуса из композитного материала применяют ТЗП, обладающее высокой эластичностью и герметизирующими свой ствами. Для защиты стенок корпуса от наружного аэродина-мического нагрева, воздействия газов, истекающих из сопла, а также от других тепловых потоков используют специальную наружную теплозащиту.
Конструктивно-технологические решения внутренней теп лозащиты корпуса обусловлены главным образом повышенной склонностью СО к деформациям.
6. ПРОЦЕССЫ ИЗГОТОВЛЕНИЯ КОНСТРУКЦИЙ ИЗ КОМПОЗИТОВ
Для прочно скрепленных твердотопливных зарядов (ТТЗ) деформации корпусов ограничиваются пределами 1,4...4 %. В цельномотаных корпусах деформации в районе днищ сущест-венно превышают указанные значения, достигая 30 %. Поэтому используемые для защиты металлических корпусов теплозащитные материалы нельзя применять в качестве внутренних ТЗМ пластиковых корпусов, так как вследствие их малых относительных удлинений не обеспечивается совместная работа днищ СО и ТЗМ. Для обеспечения монолитности во всем диапазоне функциональных перемещений элементов корпуса наиболее приемлемыми являются резиноподобные эластичные ТЗМ. Кроме того, в каждом случае необходимо разрабатывать конструкцию компенсаторов в зонах повышенной деформации, особенно для заднего соплового фланца. Концентрация напряжений в зоне скрепления фланцев с СО зависит от таких факторов, как размер полярного отверстия, ширина, натяжение ленты армирующего материала, диаметр корпуса, толщина пластика вокруг фланца и некоторых других.
Наиболее теплонапряженными участками внутренней поверхности корпуса являются днища, где отсутствует теплоизолирующее влияние свода топлива. Температура продуктов сгорания ТТЗ составляет около 3600 К, степень запыленности конденсированной фазой — до 35 %, окислительный потенциал — до 0,1, скорость обтекания переднего днища — 4...6 м/с, заднего — 60...20 м/с (уменьшается по времени вследствие разгара канала).
Как показывает опыт проектирования и отработки крупногабаритных двигателей, наиболее рациональной в целях обеспечения минимальной массы и номенклатуры применяемых ТЗМ является двухслойная конструкция ТЗП: наружный слой из материала с повышенной эрозионной стойкостью, обладающего, как правило, пониженной эластичностью, и внутренний слой из материала с пониженной теплопроводностью и повышенной эластичностью. Наряду с указанными слоями в конструкции ТЗП в зоны, контактирующие с ТТЗ, вводят защитно-крепящий слой, состоящий из защитного подслоя (препятствующего миграции компонентов топлива в ТЗП) и скрепляющего подслоя, имеющего развитую поверхность для повышения адгезии топлива к ТЗП.
412
413
6.1. Технология изготовления корпуса РДТТ
Дата добавления: 2018-05-02; просмотров: 2876; Мы поможем в написании вашей работы! |
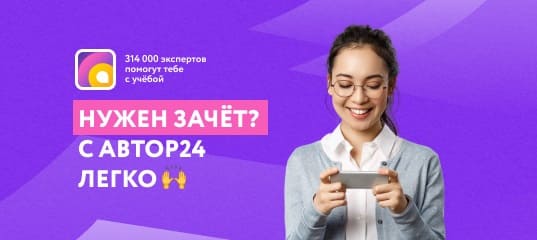
Мы поможем в написании ваших работ!