Свойства глинистых материалов
Характеристика и классификация керамических изделий
Керамические изделия разделяют на грубую и тонкую керамику бытового и технического назначения.
К грубой в основном относится: архитектурно-строительная керамика (кирпич, изразцы, керамические облицовки оконных наличников, черепица и др.) и огнеупорная (плиты, капсели, подставки для обжига изделий и др.).
В производстве грубой керамики широко используются повсеместно распространенные легкоплавкие и тугоплавкие глины различного
состава и цвета. Схема приготовления масс сравнительно простая. Исходные материалы измельчают (глина должна содержать после измельчения частицы размером не более 0,5 мм, отощающие материалы - не более 3-4 мм), а затем смешивают в смесителях, куда подают воду (или пар) для получения заданной влажности массы. После обжига изделия имеют в изломе грубозернистую структуру (различимы зерна разного размера и состава).
Производство изделий тонкой керамики отличается повышенными требованиями к качеству и однородности сырья, более сложными процессами приготовления и переработки масс, формования, тщательной отделкой поверхности изделий в зависимости от технологических требований и повышенными требованиями к качеству обжига. В процессе приготовления масс все исходные материалы подвергают тонкому помолу (материалы проходят через сито, имеющее не менее 10 000 отв/см2). После обжига изделия имеют в изломе мелкозернистую однородную структуру.
К тонкой керамике бытового назначения относят изделия из фарфора, полуфарфора, тонкокаменных масс, фаянса и майолики.
Техническая керамика - материалы, искусственно синтезированные химическим путем и отличающиеся особыми специфическими свойствами. Для производства различных видов изделий из технической керамики используют преимущественно искусственные, химически чистые материалы (оксиды алюминия, магния, кальция, циркония, ванадия и др.; силикаты; бескислородные соединения, например карбид кремния и др.). Изделия технической керамики стали незаменимыми в современной радио- и электротехнике, электронике, химическом машиностроении и других отраслях техники и промышленности.
По степени спекаемости и физико-техническим свойствам различают пористые и спекшиеся изделия тонкой керамики.
Пористые изделия пропускают жидкости и газы, водопоглощение их выше 5 % по массе. Они непрозрачны. Для снижения водопроницаемости, улучшения внешнего вида изделия покрывают глазурью (стекловидное покрытие).
Спекшиеся изделия имеют водопоглощение не более 5 %, не пропускают жидкости и газы, в изломе имеют мелкозернистую блестящую структуру.
|
|
Фарфор - материал белого цвета, имеющий однородное мелкозернистое строение, блестящий в изломе, просвечивающий в тонком слое и непроницаемый для жидкостей и газов. Фарфоровые изделия бытового назначения покрывают глазурью. Фарфор обладает высокой химической и термической стойкостью, другими положительными свойствами (высокие диэлектрические показатели и др.), что позволяет применяют фарфор в различных областях техники (например, в электротехнике - фарфоровые изоляторы и др.).
В зависимости от состава исходных масс и температуры обжига получают твердый и мягкий фарфор с различными свойствами. Изделия из мягкого фарфора обжигают при температуре 1200-1250 °С, а из твердого фарфора - при температуре 1380-1430 °С.
Изделия из тонкокаменных масс по своим свойствам близки к фарфоровым, но для их производства используют различные по составу и цвету глины. Изделия из каменных масс имеют различную окраску и за счет введения в состав масс различных керамических красителей. Температура полного спекания каменных масс ниже, чем фарфоровых. После обжига материал имеет в изломе мелкозернистую, плотноспекшуюся, матово-блестящую структуру. Изделия из каменных масс имеют толстые стенки (толще, чем у фарфоровых изделий), так как в тонком слое каменные массы сильно деформируются при обжиге.
Полуфарфор - материал, получаемый из масс на основе беложгущихся глин с повышенным содержанием полевого шпата или других сырьевых материалов, которые способствуют образованию спекшегося материала при более низкой температуре обжига. Степень спекания определяется по величине водопоглощения и прочности материала после обжига.
Фаянс - материал белого цвета, мелкозернистого однородного строения в изломе, без глазури пропускает воду и газы (обладает пористостью). Фаянсовые изделия бытового назначения покрывают глазурью для улучшения внешнего вида и получения водонепроницаемого материала. Помимо изделий бытового назначения выпускают фаянсовые облицовочные плитки, санитарно-строительное оборудование (сливные бачки, унитазы, раковины, полочки) и другие фаянсовые изделия, применяемые в различных областях техники.
Различают глинистый, известковый и полевошпатовый фаянс.
|
|
|
|
Майолика - это разновидность глинистого фаянса, но материал не белого цвета, а самого различного, так как для производства майоликовых изделий используют глины разного состава и цвета. Майоликовые изделия покрывают цветными прозрачными и непрозрачными глазурями, которые маскируют цвет материала изделий. На Конаковском и Будянском фаянсовых заводах традиционно называют майоликовыми изделия, изготовленные из фаянсовых масс и декорированные цветными глазурями (поливами).
|
|
Сырьевые материалы
· Глинистые материалы
· Плавни
· Отощающие материалы
· Добавочные материалы
· Вспомогательные материалы
Сырьевые материалы, используемые для изготовления фарфоровых и фаянсовых изделий, подразделяют на пластичные и непластичные (отощающие и плавни).
К пластичным материалам относятся: глины, каолины и бентониты. Эти материалы в соединении с определенным количеством воды образуют пластичную массу, а после обжига приобретают прочность камня.
К отощающим материалам относятся: кварцевый песок, молотый кварц, молотый бой неглазурованных изделий, прошедших обжиг (шамот), дегидратированная глина (обожженная на температуру 600-750 °С). Количество отощающих материалов влияет на пластичность масс и препятствует сокращению размеров изделий при сушке и обжиге.
К плавным относятся материалы, которые при максимальной температуре обжига или плавятся и переходят в расплав, или образуют с другими материалами массы силикаты (расплавы), способствующие образованию прочного материала. От количества образующегося расплава зависит степень спекания материала. Необходимо также учитывать, что плавни на определенных стадиях изготовления изделий (например, при формовании и сушке) выступают как отощающие материалы. Плавнями являются полевые шпаты (альбит, ортоклаз, анортит), кварцполевошпатовое сырье, пегматиты, сиениты и др.
Глазурные шихты для фаянсовых и фарфоровых изделий отличаются в силу разного состава шихт фаянсовых и фарфоровых масс. Глазури должны иметь одинаковые с массой изменения линейных размеров при охлаждении, иначе возможны дефекты в слое глазури: отскакивание глазури от материала изделия или трещины (цек) в слое глазури. Для приготовления фаянсовых глазурей используют боратовую руду, углекислый стронций, техническую буру, борную кислоту, кальцинированную соду, сульфат натрия, полевой шпат, кварцевый песок, мел, доломит, магнезит и др. В шихту фарфоровой глазури входят полевой шпат, кварц, пегматит, тальк, волластонит, доломит, каолин, бой глазурованных изделий, оксид цинка и др.
Состав сырьевых материалов, поступающих на заводы, не стабилен. Это сказывается на изменении технологических свойств масс и глазурей, свойств полуфабрикатов и качестве готовых изделий. Требуется постоянная корректировка шихтового состава масс и глазурей при их составлении. Стабилизация состава сырьевых материалов, повышение их чистоты и однородности происходит за счет обогащения, т. е. очистки сырьевых материалов от вредных и посторонних примесей. Этот процесс осуществляют на обогатительных фабриках или комбинатах, расположенных на месторождениях сырьевых материалов.
Глинистые материалы
· Свойства глинистых материалов
· Основные месторождения глины
· Обогащение каолина
К глинистым материалам относятся глины, каолины и бентониты. Глины и каолины - природные материалы полиминерального состава, образовавшиеся в результате разрушения (выветривания) алюмосиликатных горных пород (полевых шпатов, пегматитов, гранитов и др.). Разрушение горных пород происходит в результате механических (воздействие воды, ветра, ледников), физических (нагревание, охлаждение), химических (воздействие влаги, кислорода, углекислоты и других газов, содержащихся в воздухе и воде) и бактериологических (гниение органических примесей) процессов. Вода (атмосферные осадки и грунтовые воды), попадая в трещины твердых каменистых пород, замерзает при низких температурах, увеличивается в объеме, что приводит к дальнейшему разрушению, разрыхлению пород. Вода и углекислота вызывают химическое разложение твердых алюмосили-катных горных пород, в результате чего образуются глинистые минералы - водные алюмосиликаты. Процесс разрушения полевошпатовых горных пород с образованием глинистого минерала каолинита Al2O3 · 2SiO2 · 2H2O в упрощенном виде может быть представлен следующей схемой:
K2O · Al2O3 · 6SiO2(полевой шпат (ортоклаз)) + CO2 + 2H2O - Al2O3 · 2SiO2 · 2H2O(каолинит) + K2CO3(соль) + 4SiO2 (кварц)
К важнейшим глинистым минералам относятся: каолинит — Al2O3 · 2SiO2 · 2H2O, монтморрилонит - (Са, Mg)O · Al2O3 ·4 — 5SiO2 · хH2O, гидрослюда (иллит) - K2O · MgO · 4Al2O3 · 7SiO2 · 2H2O и др.
Глины, состоящие преимущественно из каолинита или минералов каолинитовой группы, называются каолинами. Они имеют ясно выраженное кристаллическое строение и включают крупные зерна кварца. От обычных глин каолин отличается высоким содержанием глинозема Al2O3, меньшей пластичностью и обладает свойством повышать белизну обожженных керамических изделий. Глины по сравнению с каолинами имеют более сложный минералогический состав. В них в виде примесей присутствуют зерна кварца, полевых шпатов, слюды, оксиды и гидрооксиды железа и марганца, известковые и гипсовые включения и другие минералы, а также органические примеси (растительные остатки - древесина, торф, угли и др.).
По условиям образования различают первичные и вторичные месторождения глинистых сырьевых материалов. Если продукты выветривания остаются на месте своего образования и из них вымываются только водорастворимые составляющие, то это первичные месторождения. К ним относят месторождения каолина. В результате переноса продуктов разрушения горных пород дождевыми или снеговыми водами, ледниками, ветрами образовались вторичные месторождения глинистого сырья (глины). Глины с высоким содержанием кварцевого песка называют суглинками. Если увеличено содержание известняка, доломита или гипса - это мергель. Тонкодисперсную смесь глинистых минералов, кварца, полевого шпата и известняка называют лессом.
Свойства глинистых материалов
Важнейшими технологическими свойствами глинистых материалов являются пластичность, связующая способность, разжижаемость, зыбкость, спекаемость, воздушная, огневая усадка и др.
Пластичность - способность глинистых материалов в увлажненном состоянии (состоянии теста) принимать под воздействием внешних сил любую форму без разрывов и трещин и сохранять ее после прекращения внешнего воздействия.
Глинистые материалы становятся пластичными при замешивании их с водой, причем количество воды, необходимое для проявления пластических свойств, у различных по составу глинистых материалов колеблется в широких пределах. Мера - число пластичности — определяется как разность между влажностью, соответствующей нижней границе текучести (масса растекается), и влажностью предела раскатывания (масса крошится). У непластичных материалов предел раскатывания и предел растекаемости совпадают. Для высокопластичных глин число пластичности составляет свыше 25.
![]() |
Частицы глинообразующих материалов обладают значительной степенью дисперсности (малые размеры частиц) и несут на себе положительный заряд. При соединении сухой глины с водой глинистые частицы отдают ионы с поверхности и присоединяют молекулы воды, создавая вокруг себя водную оболочку (так называемую сольватную пленку), что вызывает набухание глины (рис. 2). Сольватная пленка воды прочно связана с глинистыми частицами и обеспечивает их скольжение при воздействии на глинистые материалы внешних сил (ручное формование из пластичных масс или формование с использованием шаблонов и формующих роликов). Добавление воды в глинистую пластичную массу приводит вначале к образованию вязкотекучей массы, а затем - жидкотекучей (суспензии).
На пластичность влияют природа минералов, составляющих глинистое вещество, и соотношение их в массе, величина и форма частиц, количество воды и растворенные в ней вещества. Тонкодисперсные глины имеют более высокую пластичность (табл. 3), чем грубодисперсные каолины, и требуют больше воды для затворения (у тонких, мелких частиц глин увеличивается поверхность смачивания).
Увеличение пластичности глин достигается вылеживанием, вакуумированием, отмучиванием, введением высокопластичных глин и пластифицирующих добавок. При вылеживании на открытых площадках под воздействием атмосферных осадков (дождь, снег) глинистые материалы набухают, а при перепадах температур (минусовых и плюсовых) замораживаются и оттаивают, что приводит к их разрыхлению (вода, замерзая, увеличивается в объеме и разрушает крупные куски глин). Кроме того, в них образуются гидрооксиды алюминия и железа и кремниевая кислота, развиваются микроорганизмы, что также способствует повышению пластичности глинистых материалов. Отмучиванием, т. е. распусканием глин и каолинов в большом количестве воды, добиваются отделения их от крупных тяжелых включений (кварца, извести, остаточных горных пород, органических частиц и др.), которые оседают на дне емкостей. Для понижения пластичности в массу вводят отощающие непластичные материалы (кварцевой песок, шамот и др.).
Связующая способность - это способность глин сохранять пластичность при введении в них непластичных материалов (песка, шамота и др.) и обеспечивать достаточную механическую прочность отформованных изделий после сушки. Критерием связующей способности является число пластичности. Измеряется связующая способность глин количеством песка, при добавлении которого образуется масса с числом пластичности 7. Высокопластичные глины способны связывать 60-80 % кварцевого песка, пластичные - 20-60, тощие - 20 %.
Разжижаемость - важное свойство глинистых материалов, определяющее пригодность их для изготовления изделий способом отливки в гипсовых формах. Технологически и экономически выгоднее, если в шликере меньше воды, но в то же время сохраняются необходимая текучесть и большая влагоотдача шликера при достижении достаточной связности и прочности набранного слоя массы. Разжижение глинистых материалов без повышения влажности шликера достигается добавлением в него электролитов - соды и жидкого стекла (силикат натрия) и др. - в количествах до 0,01 %. На степень разжижения влияют также минералогический состав глин, их дисперсность, концентрация и количество вводимого электролита.
Зыбкость глинистых материалов (каолинов) проявляется в том, что нормальная на вид пластичная масса может растекаться при незначительном встряхивании. Снижение зыбкости каолинов достигается введением в каолиновую суспензию коагуляторов (известнякового молока, хлористого кальция, сульфата кальция). Зыбкость каолинов вызывает; зыбкость фарфоровых масс и затрудняет формование изделий, так как в состав фарфоровых масс входит большое количество каолина.
Прочность в высушенном состоянии определяется величиной предела прочности при изгибе высушенных образцов. Повышению прочности изделий в высушенном состоянии способствует снижение в массе содержания отощающих материалов, введение пластифицирующих (бентонит и др.) или поверхностно-активных добавок.
Цвет глин в природном состоянии разнообразный. Они бывают белого, серого, зеленоватого, темно-серого и даже черного цветов, а также от кремового до темно-красного. Каолины чаще всего бывают белыми и светлых тонов. Цвет глинистых материалов зависит от количества присутствующих в них органических и неорганических красящих примесей. Органические примеси (водоросли, включения угля, торфа, остатки растительного происхождения) придают глинам зеленоватый, голубоватый, серый, черный и другие цвета. При обжиге органические примеси сгорают. Неорганические же минеральные красители (соединения железа и титана) окрашивают природные глины в цвета от светло-кремового до темно-красного и в серые. Эти красители не выгорают при обжиге. Цвет глин после обжига зависит от количества содержащихся в них неорганических красителей, а также от температуры обжига и газовой среды обжига (окислительная или восстановительная).
Огнеупорность - способность глин противостоять, не расплавляясь, воздействию высоких температур. Определяется огнеупорность температурой, при которой образец (конус), изготовленный из испытуемой массы, при обжиге изгибается и касается своей вершиной основания. Каждый состав керамической массы имеет определенную температуру огнеупорности. На этом основано изготовление керамических пироскопов (конусов Зегера), с помощью которых контролируют температуру обжига изделий. На огнеупорность влияют химико-минералогический состав глин и процессы взаимодействия в обжиге составляющих материалов.
Водопоглощение - свойство пористой обожженной керамической массы поглощать и удерживать воду при непосредственном соприкосновении с ней. Водопоглощение является мерой спекания масс. Оно характеризует степень заполнения открытых пор материала при кипячении в воде и выражается в процентах по массе. Коэффициент насыщения под водой - отношение объема поглощенной воды к объему пор. Показатели водопоглощения керамических (материалов, %, по массе приведены ниже.
Фарфор............................................ 0—0,5
Полуфарфор........................................ 3—5
Фаянс:
твердый....................................... 9—12
мягкий....................................... 17—22
Спекаемость - способность глин под действием высоких температур превращаться в камнеподобный материал с водопоглощением менее 5%. Количественно степень спекаемости глин характеризует температурный интервал спекания и интервал спекшегося состояния. Температурным интервалом спекания называется разность между температурой, при которой отмечаются признаки пережога (плавление или вспучивание), и температурой начала спекания глин, при которой начинается интенсивное уплотнение обжигаемого материала. Интервалом спекшегося состоянияназывается разность между температурой, при которой замечаются признаки пережога, и температурой, при которой водопоглощение материала равно 5% (ниже этой величины лежит область спекшегося состояния). Интервал спекания - важный технологический показатель, определяющий режим конечной стадии обжига изделий, при котором они приобретают кондиционные (эксплуатационные) свойства. Наименьший интервал спекания у легкоплавких глин (50-100°С), а наибольший (до 400 °С) - у огнеупорных. По температуре спекания различают глины низкотемпературного спекания (до 1100 °С), среднетемпературного (от 1100 до 1300 °С) и высокотемпературного (свыше 1300 °С).
Воздушная усадка - это уменьшение линейных размеров и объемов изделий при сушке вследствие удаления из массы воды затворения и сближения твердых частиц массы. Чем выше дисперсность и пластичность глин, тем больше они требуют воды для получения массы необходимой пластичности и больше набухают, а при сушке дают большую усадку (см. табл. 3). Воздушную усадку определяют по формуле, %:
Lв=[(l0-l1)/l0]·100
где l0 - расстояние между метками на сыром образце (размеры сырого изделия, размеры модели с припуском на технологическую усадку массы к сушке и обжиге), мм; l1 - расстояние между этими метками на высушенном образце (размеры изделия после сушки), мм; Lв - воздушная усадка, %.
Благодаря воздушной усадке происходит отделение изделий от стенок гипсовых форм при сушке.
Огневая усадка - это уменьшение линейных размеров изделия и его объема в обжиге. При одинаковой конечной температуре обжига усадка тем больше по величине, чем больше плавней содержит глиномасса и чем меньше размеры твердых частиц. Снижают усадку при обжиге отощающие материалы, введенные в массу, и более крупный помол исходных материалов массы. Огневую усадку определяют по формуле, %:
L0=[(l1-l2)/l1]·100,
где l2 - расстояние между метками на образце после обжига (размеры готового изделия, проектные размеры), мм: L0 - огневая усадка, %.
Полная усадка - это уменьшение размеров отформованного изделия после сушки и обжига. Полную усадку определяют по формуле, %:
L=[(l0-l2)/l0]·100,
где L - полная усадка, %.
Основные месторождения глины
К основным наиболее изученным месторождениям глинистого сырья, используемого для производства хозяйственного фарфора и фаянса, относятся следующие: по каолинам - Просяновское (Днепропетровская обл.), Глуховецкое (Винницкая обл.), Алексеевское (Каз. ССР) и Кыштымское (Челябинская обл.); по беложгущимся глинам - Дружковское (УССР) и Трошковское (Красноярский край); по бентонитовым глинам - Огланлинское (Туркменская ССР) и Пыжевское (УССР). Для изготовления огнеприпаса используют Латненские глины (Воронежская обл.).
Просяновское месторождение каолинов - самое крупное из разведанных. В состав каолинов этого месторождения помимо каолинита в значительном количестве входит слюда и неразложившийся полевой шпат. Допускается суммарное содержание красящих оксидов (Fe2O3 + TiO2): для высшего сорта - не более 0,8%; для I - не более 1; для II - не более 1,4; для III сорта - не более 1,8 %.
Глуховецкое месторождение каолина отличается большой мощностью залегания (до 100 м). Глуховецкий каолин отличает тонкая зернистость и однородность глинистого вещества. По техническим условиям допускается суммарное содержание красящих оксидов (Fe2O3 + TiO2): для I сорта -1,3%, для II - 1,8%. Этот каолин используют в производстве фаянса и капсельного припаса.
Алексеевское месторождение каолина отличает повышенное содержание оксида калия и включение небольшого количества гидрослюды.
Кыштымский каолин имеет непостоянный химический и минера логический состав, что ограничивает его применение. Он используется для изготовления фаянса и каменной массы. Содержание красящих оксидов составляет: для I сорта - 1,6%, для II - 2,9, для III сорта - 3%.
Дружковское месторождение глин известно глинами в Ново-Швейцарском, Веселовском и Ново-Райском карьерах. Высокая пластичность и белый цвет после обжига делают эти глины ценным сырьем для фарфоровой и фаянсовой промышленности. Содержание в них глинозема (Al2O3) и диоксида титана (TiO2) на прокаленное вещество должно быть не менее 33-35%, оксида железа - не более 1,4%. Минералогический состав: каолинит, монотермит и гидрослюда.
Трошковские глины не набухают в воде и содержат меньше оксидов железа и титана, чем дружковские. Тонкий помол глины в шаровой мельнице обеспечивает получение массы с высокой пластичностью и способствует увеличению прочности полуфабриката, прошедшего сушку. Изделия из фарфоровых масс, в состав которых входят трошковские глины, имеют повышенную белизну и просвечиваемость. Глины подразделяют на высший, I и II сорта. Содержание глинозема соответственно не менее 32,30 и 30 %, а сумма оксида железа и диоксида титана - не более 1,3; 1,6; 2,5%. Для производства фарфоровых изделий используют глины высшего и I сортов. Минералогический состав - каолинит с примесью монтморрилонита.
Латненские глины тонкодисперсны (содержание частиц с размерами 0,001 мм составляет 50-70%), так как содержат до 83% каолинита. Цвет светло- и темно-серый до черного (углистого). Содержание глинозема колеблется от 30 до 41%, оксида железа не более 2,5%. Ввиду высокого содержания красящих веществ латненскую глину используют в производстве огнеупорного припаса.
Бентонитовые глины образовались в результате расстекловывания и химического превращения стекловидной фазы вулканического пепла или туфа. По своим свойствам они чрезвычайно неоднородны. Цвет бентонитов - от белого до темно-коричневого. Бентонит обладает способностью при затворении водой до 10 раз увеличиваться в объеме и находиться продолжительное время во взвешенном состоянии в шликере. Его вводят в массу как пластифицирующую добавку. Ввод в массу до 4 % бентонита позволяет заменить пластичные глины каолинами и повысить белизну фарфора. Бентонит увеличивает прочность полуфабриката в высушенном состоянии. Его температура спекания 1100-1200 °С, плавления 1250-1400 ºC, т. е. бентонит является материалом (плавнем), интенсифицирующим процессы спекания изделий в обжиге. В состав бентонитов входят монтморрилонит (основной минерал) и примеси кварца, слюды, полевых шпатов, карбонатов и др.
Обогащение каолина
Обогащение глинистого сырья способствует стабилизации состава и технологических свойств масс, повышает качество изделий и производительность оборудования, снижает трансфертные расходы, улучшает технико-экономические показатели производства.
Процесс обогащения каолинов предусматривает выделение из них основного глинистого минерала - каолинита, очищенного от крупнозернистых примесей и красящих оксидов. Каолин в природе встречается в виде полиминеральной смеси, состоящей из каолинита, кварца, полевых шпатов, слюды, железо- и титаносодержащих соединений, причем размер частиц кварца, полевого шпата и слюды в 10-100 раз превышает размер частиц каолинита. На этой разнице в размерах частиц и, следовательно, массы частиц основан способ обогащения глинистых материалов (каолина). Обогащенный каолин содержит в основном каолинит, в то время как в неотмученном (сыром) каолине его не более 45 %.
Обогащение каолинов осуществляют мокрым (электролитным) и сухим способами.
При мокром способе измельченный каолин распускают в мешалках в воде при добавлении электролитов. Электролиты интенсифицируют процесс обогащения, способствуют повышению плотности каолиновой суспензии при одновременном снижении расхода воды в 4-5 раз, улучшают условия отделения каолинитовых частиц от примесей. Происходит осаждение песка и других каменистых примесей. Из мешалок суспензию сливают в чаны через спускной кран, расположенный выше дна мешалки с учетом высоты осадка каменистых тяжелых частиц. В чаны добавляют коагуляторы (известковое молоко, полиакриламид и др.) для укрупнения каолинитовых частиц. Из чанов суспензию подают насосами в камерные фильтр-прессы, в которых происходит частичное обезвоживание суспензии (при давлении 1 МПа и времени фильтрации 50 мин). Далее коржи измельчают и направляют в сушильный барабан. Температура теплоносителя на входе в сушильный барабан 800-900 ºС, на выходе - 100-150 ºC. Высушенный каолин тарируют в мешки и отправляют на склад готовой продукции.
Основной недостаток этого способа при использовании в качестве коагулятора известкового молока - трудность получения каолина со стабильными свойствами, из-за чего может произойти ухудшение литейных свойств шликера и формовочных свойств масс.
Мокрый способ обогащение каолина применяют на Просяновском, Глуховецком и Кыштымском обогатительных комбинатах.
При сухом способе каолин-сырец проходит сушку в сушильном барабане при температуре 800- 850 ºC в течение 40-45 мин до остаточной влажности 0,7-0,8%. Высушенный каолин подвергают тонкому помолу в центрифугальных мельницах, а затем пропускают его через воздушные сепараторы и циклоны. Фракции размером менее 0,3 мм уносятся из мельницы воздушным потоком, более крупные частицы удаляются через разгрузочное отверстие. Тонину помола регулируют скоростью воздушного потока. Очистка воздушного потока от мельчайших частиц, не улавливаемых в сепараторах, проходит в рукавных, электрических фильтрах, электрических или пылеосадительных камерах.
Сухой способ обогащения каолина обеспечивает извлечение 80-82% ценных фракций из сырого каолина. Его используют при обогащении каолинов и глин, содержащих крупнозернистое примеси. Этот способ обогащения применяют на Просяновском обогатительном комбинате.
Сухой способ обогащения каолинов проще мокрого. Однако к недостаткам этого способа следует отнести снижение качества каолина за счет удаления из него наиболее ценной тонкой фракции, которую не удается уловить при воздушной классификации. В результате этого снижается пластичность и связующая способность глинистых материалов.
Качество будущих изделий зависит от способа обогащения сырьевых материалов и от соблюдения технологии обогащения. Так, добавление в каолиновую суспензию коагулянтов приводит к укрупнению и осаждению глинистых частиц, но одновременно может вызвать и нежелательные явления, отмечаемые в заводской практике, например, способствует образованию пробок в шликеропроводах и недоливу изделий при шликерном литье
Пригодность глин и каолинов для производства фарфоровых и фаянсовых изделий оценивают также по качеству огневой пробы. Глину и каолин обжигают при определенной температуре (для фаянса - до 1280 °С, а для фарфора - до 1430 °С). Окраска глин и каолинов после обжига должна быть светлой (белой), без пятен и «мушек» (точек рыжего или темного цвета, указывающих на присутствие в массах вкраплений железа и титана).
Плавни
В качестве плавней используют полевые шпаты, пегматиты, перлиты, мел, доломит, тальк, нефелиновые сиениты, сподумен и другие минералы, материалы и породы. Действие различных плавней в массах неодинаково. Одни из них (полевые шпаты, пегматиты и др.) образуют жидкую стекловидную фазу при плавлении, другие (мел, доломит, тальк и др.) образуют расплав при взаимодействии с кварцем, глинистым веществом и другими компонентами массы под воздействием высокой температуры обжига.
Плавни вводят в состав масс (от 5 до 30 %) для снижения температуры обжига. При увеличении количества плавней в обжигаемом материале возрастает количество образующейся стекловидной массы, в результате чего улучшается просвечиваемость фарфоровых изделий в тонком слое, уменьшается пористость и увеличивается прочность фаянса и фарфора.
Полевые шпаты составляют большую группу алюмосиликатов калия, натрия, кальция, широко представленную в земной коре (до 60%) минералами: ортоклазом (микроклином) K2O · Al2O3 · 6SiO2, альбитом Na2O · Al2O3 · 6SiO2, анортитом СаО · Al2O3· 6SiO2. В чистом виде они встречаются редко, поэтому полевые шпаты, используемые в производстве фарфоровых и фаянсовых изделий, представляют собой смеси этих минералов. Лучшими плавнями для фарфоровых масс считают калиево-натриевые полевые шпаты, в которых преобладает ортоклаз. Различные по составу полевые шпаты по-разному проявляют себя в обжиге. При температуре обжига твердого фарфора 1410 ºC натриевый полевой шпат, расплавляясь, имеет более низкую вязкость, чем расплав калиевого полевого шпата, что приводит к сильной деформации изделий в обжиге. Поэтому в фарфоровые массы вводят калиевые или калиево-натриевые полевые шпаты. С увеличением содержания в полевом шпате оксида кальция снижается прозрачность расплава, т. е. просвечиваемость фарфорового черепка в тонком слое.
В полевошпатовых породах вредными включениями являются слюда и оксиды железа. Слюда очень трудно поддается измельчению и после обжига образует на фарфоре и фаянсе «мушки». Оксиды железа также влияют на снижение белизны фарфоровых и фаянсовых изделий. Повышенное содержание оксидов железа в сырьевых материалах способствует получению желтоватого оттенка у изделий. Содержание оксидов железа в полевых шпатах, используемых при производстве фарфора и фаянса, не должно превышать 0,5%, а суммарное содержание оксидов калия и натрия должно быть не менее 11 %. Химический состав Чупинского полевого шпата, %: SiO2 - 63,13; Al2O3 - 21,27; Fe2O3 - 0,3; СаО - 0,83; MgO - 0,50; K2O - 12,04; Na2O - 1,62; потери при прокаливании (ППП) - 0,30.
Из-за дефицитности чистых разновидностей полевого шпата применяют природные разновидности: пегматиты, плагиоклазы с низким содержанием оксида кальция (калиевый полевой шпат с прорастаниями альбита и анортита), перлиты, нефелиновые сиениты или нефелин-сиенитовый концентрат.
Пегматиты - полевые шпаты, проросшие кристаллами кварца. Пегматиты содержат 30-35% кварца и 65-70% полевого шпата. При использовании пегматита в массе соответственно уменьшают количество кварца или кварцевого песка.
В пегматитах не должно быть вредных примесей: гидрооксида железа в виде натеков и железосодержащих минералов (биотит, пирит, турмалин и др.). Содержание оксида железа в пегматитах не должно превышать 0,5 %, если они предназначены для фарфоровых или фаянсовых масс, и 0,2 % - для глазурей.
Качество полевых шпатов и пегматитов оценивают по огневой пробе. Их образцы обжигают при температуре обжига изделий (фаянс - до 1280 ºC, фарфор - до 1430 °С). После обжига пробы полевых шпатов и пегматитов должны быть белыми, стекловидными, без пятен и «мушек».
Нефелиновый сиенит - это горная каменистая порода, в состав которой кроме нефелина (К, Na)2O · Al2O3 · 2SiO2 входят микроклин, альбит, слюда, магнетит и другие минералы в небольших количествах. Температура плавления нефелиновых сиенитов около 1200 ºC, содержание щелочей K2O + Na2O в них составляет 15-30%. Химический состав нефелин-сиенита, поставляемого горнохимическим комбинатом «Апатит» (Мурманская обл.), %: SiO2 - 45,2; Al2O3 - 32,3; K2O - 5,0; Na2O - 15,7; Fe2O3 - 0,9; СаО - 0,2; ППП - 0,4.
Нефелин-сиенитовый концентрат - отходы производства апатита, подвергнутого дополнительному обогащению.
Перлиты - стекловидные вулканические породы с включениями кварца, полевого шпата и других минералов. Залегают перлиты близко к поверхности, добычу их проводят открытым способом. Температура размягчения перлитов 1030-1040 °С, а расплавления -1300-1320 °С. Химический состав перлита Арагацкого месторождения (Армянская ССР), %: SiO2 - 72,75; TiO2 - следы; Al2O3 - 0,2-0,4; СаО -0,1-1,1; MgO - 0,3-0,6; Na2O + K2O - 5-8,2; SO3 - 0,19-0,34; ППП -2,3-4,5.
Тальк - гидросиликат магния 3MgO · 4SiO2 · H2O с плотной структурой, называемый жировиком. Образование в природе связано с действием на доломит СаCO3 · MgCO3щелочных растворов, содержащих CO2 и SiO2. Огнеупорность талька 1490-1510 ºC. Применяют тальк в производстве керамических плиток, огнеупорных и термостойких изделий. Химический состав талька Шабровского месторождения (Свердловская обл.), %: SiO2 - 30,4; Al2O3 - 1,25; Fe2O3 - 1,25; Fe2O3 + + FeO - 8,0; СаО - 0,6; MgO - 32,7; ППП - 22,5- 32,0.
Мел, мрамор СаCO3, магнезит MgCO3, доломит СаCO3 · MgCO3 (опока) - это карбонаты кальция и магния. Их флюсующее действие проявляется лишь при температуре обжига выше 1000 ºC. При температуре 800-900 ºC они разлагаются на соответствующий оксид и углекислый газ. Образующиеся оксиды СаО и MgO при температуре свыше 1000 ºC вступают в контакт с другими оксидами, входящими в шихту массы, и образуют стекловидную фазу (силикаты кальция и магния). Мел - белая осадочная порода, состоящая из мелких частиц кальцита (микроскопических скорлупок, раковин, водорослей с известковым панцирем). Мрамор - зернистая порода, образовавшаяся при перекристаллизации известняков. Доломит (опока) образовался при воздействии магнезиальных растворов на известняки.
Карбонатные породы, используемые в производстве фарфора и фаянса, не должны содержать железистых включений более 0,3%, а кварца - не более 3 %.
Введение в массу плавней позволяет получить фарфор при температуре обжига 1250 °С (низкотемпературный фарфор). Снижение температуры обжига изделий на 100 ºC при прочих равных условиях способствует снижению удельного расхода топлива на 11-13 %.
Отощающие материалы
Введение отощающих материалов в шихту фарфоровых и фаянсовых масс позволяет регулировать технологические свойства формовочных масс и литейных свойств шликера, а также получать изделия с заданными свойствами. Отощающие материалы снижают пластичность масс и, следовательно, уменьшают усадку изделий в сушке и обжиге, а также препятствуют деформации изделий в сушке и обжиге. Количество вводимых в массы отощающих материалов, их природа, зерновой состав и температура обжига изделий влияют на физико-технические свойства фарфора и фаянса (прочность, водопоглощение и др.).
В качестве природных отощающих материалов используют кварц жильный молотый, кварцевый песок, кварцевые отходы обогащения каолинов, а искусственных - шамот и дегидратированную глину.
Шамот - размолотый бой обожженных неглазурованных изделий или керамический материал, получаемый обжигом глин и каолинов при температуре не ниже 800 °С. Дегидратированная глина - это глина, обожженная до температуры 700-750 °С, при которой она теряет химически связанную воду (из каолинита уходит кристаллически связанная вода и становится непластичной при смешивании с водой.
Содержание отощающих материалов в массах доходит до 40%.
Кремнезем SiO2, образующий кварцевые породы, при обжиге претерпевает полиморфные превращения, переходит из одной кристаллической формы в другую. Эти переходы сопровождаются изменением объема кварца, что необходимо учитывать при выборе режима обжига и охлаждения, так как это обратимые процессы.
Например, при температуре 117 °С модификация кварца α-тридимит переходит в β-тридимит, при этом объем кварца увеличивается на 0,2 %; при температуре 180-270 °С β-кристобалит переходит в α-кристобалит с увеличением в объеме на 2,8%; β-кварц при температуре 573 °С переходит в α-кварц с увеличением в объеме на 0,82%. Реакции идут с большой скоростью, поэтому в этих интервалах температур, особенно при температуре 573 ºC, необходима выдержка без резкого подъема температуры. Несоблюдение режима обжига в этот период может стать причиной растрескивания изделий. Данный эффект используют для облегчения помола кварца, который вначале обжигают при температуре 900 °С, а потом резко охлаждают. При этом куски кварца растрескиваются и затем легко измельчаются.
Кремнеземистые материалы, используемые для производства фарфоровых и фаянсовых изделий, должны содержать не более 0,2% оксида железа и не менее 95% SiO2 для I сорта.
Каолинизированный кварцит (гусевский камень) двух разновидностей используют в производстве фарфоровых изделий. Бесщелочная разновидность (K2O + Na2O менее 0,5 %) - темно-серого цвета, состоит в основном из кварца (56 %) и каолинита (40 %). Кварцит нормальной щелочности (K2O + Na2O до 2,5%) - серого и темно-серого цветов, содержит кварц (50-55%), каолинит (20-30%) и гидрослюду (14-22%). Гусевский камень, введенный в фарфоровые массы (до 50 %), частично заменяет полевой шпат, каолин, кварц и кварцевый песок и способствует повышению белизны и просвечиваемости фарфора.
В капсельные массы, используемые для изготовления огнеупорных изделий (капселей, плит, стоек и др.), вводят шамот. Шамот получают обжигом огнеупорных глин с последующим измельчением или используют размолотый и просеянный бой бракованных капселей, плит и других изделий.
Контрольные вопросы
1. Какие факторы влияют на цвет глин в природе и после обжига? 2. Каковы основные свойства глинистых материалов? 3. Как классифицируются глинистые материалы? 4. Какое влияние оказывают плавни на свойства готовых изделий? 5. Каково назначение отощающих материалов в массах и влияние их на свойства массы и готовых изделий? 6. Назовите способы увеличения и снижения пластичности глиномасс. 7. Какие требования предъявляются к сырьевым материалам, используемым для производства фарфора и фаянса? 8. Какое значение имеет обогащение сырьевых материалов? Охарактеризуйте способы обогащения. 9. Перечислите добавочные и вспомогательные материалы. Каково их назначение?
Дата добавления: 2018-04-15; просмотров: 498; Мы поможем в написании вашей работы! |
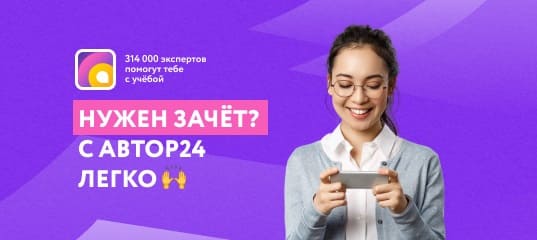
Мы поможем в написании ваших работ!