Ручная электродуговая сварка - принцип работы
Департамент образования г. Севастополя
Государственное бюджетное образовательное учреждениеПрофессионального образования«Севастопольский колледж информационных технологий и промышленности»
Допускаю к защите
________________________________
подпись
«______» __________________20____
ВЫПУСКНАЯ КВАЛИФИКАЦИОННАЯ РАБОТА
на тему
РАЗРАБОТКА ПРОЕКТА СВАРОЧНОГО УЧАСТКА ДЛЯ СПЕЦИАЛИЗИРОВАННОГО СТО С РАЗРАБОТКОЙ ТЕХНОЛОГИЧЕСКОГО ПРОЦЕССА РЕМОНТА КУЗОВА АВТОМОБИЛЯ
Студент группы 318
Ремнев Николай Сергеевич
________________________
подпись
Кричевец Денис Сергеевич
________________________
подпись
Севастополь 2017
Содержание
Введение……………………………………………………………………….….….4
РАЗДЕЛ 1ТЕХНОЛОГИЧЕСКИЙ РАЗДЕЛ ТЕХНИЧЕСКАЯ ХАРАКТЕРИСТИКА СВАРОЧНОГО УЧАСТКА………………………………..7
1.1 Назначение сварочного участка……………………….……..………8
1.2 Подготовка металла (деталей) к сварке……………………………..8
1.3 Сборка деталей под сварку……………………………………...……9
1.4 Виды выполняемых работ на участке……………………………...10
РАЗДЕЛ 2ОРГАНИЗАЦИОННЫЙ РАЗДЕЛ……………………………..…...…13
2.1 Газосварочное оборудование……………………………………….14
2.2 Газовая сварка металлов………………………………………….…16
2.3 Газовая резка металлов………………………………………...……16
2.4 Ручная дуговая сварка MMA………………………………………..17
2.5 Ручная электродуговая сварка - принцип работы…………………17
2.6 Подбор и выбор оборудования для проведения сварочных работ на АТП………………………………………………………………...….19
2.7 Сварка кузова автомобиля углекислым полуавтоматом……….....25
2.8 Сварочные работы……………………………………………...……29
|
|
РАЗДЕЛ 3 ЭКОНОМИЧЕСКАЯ ЧАСТЬ………...………………………….……31
3.1Технические показатели Станции технического обслуживания автомобилей…………………………………………………………..….32
3.2 Капитальные вложения………………………………………….…..33
3.3 Расчет численности персонала………………………………...……35
3.3.1 Расчет численности производственных рабочих……………..…35
3.3.2 Расчет численности руководителей, специалистов и служащих………………………………………………………………...36
3.4 Расчет затрат на выполнение работ………….……………………..37
3.4.1 Расчет фонда оплаты труда производственных рабочих…….....37
3.4.2 Расчет фонда оплаты труда административно-управленческогоперсонала……………………………………………………………...….39
3.5 Расчет отчислений на социальное страхование…………………...40
3.5.1 Расчет отчислений на страхование от несчастных случаев на производстве…………………………………………………………..…40
3.6 Расчёт затрат на основные материалы по соответствующим видам работ……………………………………………………………………...41
3.6.1 Расчет амортизационных отчислений……………………………41
3.7 Расчет накладных расходов…………………………………………42
3.8 Расчёт дохода, прибыли и срока окупаемости проекта……….......45
3.9 Заключение…………………………………………………………..47
|
|
РАЗДЕЛ 4 ОХРАНА ТРУДА……………………………………………..……….48
4.1 Общие требования охраны труда…………………………………...49
4.2 Требования охраны труда перед началом работы………………....52
4.3 Требования охраны труда во время работы………………………..56
4.4 Требования охраны труда в аварийных ситуациях………………..62
4.5 Требования охраны труда по окончании работы……………….…65
РАЗДЕЛ 5 КОНСТРУКЦИОННАЯ ЧАСТЬ………………………..………….…67
5.1 Автомат для сварки толстостенных изделий в узко щелевую разделку АСУР-1250…………………………………………………….68
5.2 Назначение…………………………………………………………...68
5.3 Основные Особенности……………………………………………..69
5.4 Система Управления………………………………………………...69
5.5 Технические Характеристики……………………………………....71
ЗАКЛЮЧЕНИЕ……………………………………………………………………..72
СПИСОК ЛИТЕРАТУРЫ………………………………………………………….73
|
|
Введение
Ремонт автомобилей является объективной необходимостью, которая обусловлена техническими и экономическими причинами.
Во-первых, потребность народного хозяйства в автомобилях частично удовлетворяется путем эксплуатации отремонтированных автомобилей.
Во-вторых, ремонт обеспечивает дальнейшее использование тех элементов автомобилей, которые не полностью изношены. В результате сохраняется значительный объем прошлого труда.
В-третьих, ремонт способствует ремонту материалов, идущих на изготовление новых автомобилей. При восстановлении деталей расход материалов в 20...30 раз ниже, чем при их изготовлении.
Многочисленные исследования показали, что первый капитальный ремонт, как правило, по всем слагающим экономической эффективности затрат общественного труда выгоднее приобретения нового автомобиля. Это объясняется двумя возможными обстоятельствами:
-фактические затраты на первый капитальный ремонт большинства видов машин и оборудования не превышает 30-40% их балансовой стоимости, повторные же ремонты обходятся значительно дороже;
- большинство видов машин подвергается первому капитальному ремонту, как правило, до наступления морального износа.
Общее число деталей в современных автомобилях составляет тысяча наименований. Однако число деталей, лимитирующих их срок службы до капитального ремонта, не превышает несколько десятков наименований. Задача заключается в том, чтобы повысить долговечность этих деталей до уровня обеспечивающего наибольшую долговечность автомобиля.Наряду с поиском путей и методов повышения надежности, которая закладывается, в конструкцию автомобиля при проектировании и внедряется в сфере производства , необходимо изыскать пути и методы для решения этой же задачи в сфере эксплуатации и ремонта.
|
|
Авторемонтное производство, получив значительное развитие, еще не в полной мере реализует свои потенциальные возможности. По своей эффективности организационному и технологическому уровню оно еще от основного производства автомобилестроения. Качество ремонта остается низким, стоимость высокой, уровень механизации достигает лишь 25-40% вследствие чего производительность труда в два раза ниже, чем в автомобилестроении. Авторемонтное предприятие (АРП) оснащены в основном универсальным оборудованием большей степени изношенности и малой точностью. Это негативные стороны современного состояния авторемонтного производства и определяют пути его развития. В развитии авторемонтного производства нашей страны до конца 70-х годов преобладало первое направление. Различные министерства и ведомства, эксплуатирующие автомобили, создавали свои сети АРП, в которых преобладали предприятия по КР полнокомплектных автомобилей. Развитие этого вида ремонта шло в ущерб применению других видов, в частности ремонта по техническому состоянию, позволяющего сокращать объемы ремонтных воздействии за счет использования остаточных ресурсов деталей и сопряжений.При капитальном ремонте полнокомплектных автомобилей они на длительный срок выбывают из эксплуатации. Стремление сократить простои автомобилей в ремонте привело к практике строительство АРП в местах высокой автомобильного парка, с тем, чтобы максимально их приблизить к поставщикам ремонтного фонда.
Организационно-техническая перестройка АРП в последние годы ускорилась в связи с изменением социально-экономических условий хозяйствования в нашей стране. Наряду с развитием традиционных ведомств и самостоятельных АРП производственные объединения автомобильной промышленности создали и развивают фирменные системы обслуживания и ремонта автомобилей.
Дальнейшее эффективное развитие АРП базируется на идеях и принципах, которые порождаются интеграционными процессами заводов-изготовителей новой технике с предприятиями, выполняющими услуги по централизованному ТО и ремонту этой технике. Необходимость систематизации и углубления знаний о ремонте автомобилей повышает роль научных исследований этой области. Машиностроительная промышленность производит продукцию для всех отраслей народного хозяйства. Очевидно, что технический прогресс и дальнейший рост экономики в целом в значительной степени зависят от развития машиностроения. В данной работе рассматриваются основные вопросы и направления развития одной из важнейших частей технологии машиностроения - сварочного производства. Оно представляет собой неотъемлемую, но весьма специфическую часть машиностроительной отрасли.
Цель работы заключается в анализе сварки как специфической части машиностроения.
Соответственно многообразию создаваемых изделий сварщики используют десятки способов и сотни разновидностей сварки, термической резки и других родственных технологий, таких как пайка, наплавка, напыление и др., основанных на использовании электрической дуги, газового пламени, электронного и лазерного лучей, контактного тепла, энергии взрыва и других источников. Каждому виду энергии соответствует специальное оборудование, технологии, материалы и т.п., с помощью сварки детали соединяются в узлы и конструкции. Сварка, являясь последующей операцией, зависит от предыдущих: их материала, размеров, формы и других параметров. В свою очередь, сварные изделия также могут подвергаться механической и термической обработке, сборке, окраске. Таким образом, сварка является не окончательной, а некоторой промежуточной операцией в цикле получения готового изделия. В то же время именно сварка, оказывая глубокое влияние на структуру, состав и свойства металла сварных соединений, возникновение внутренних напряжений и деформаций в металле, в большинстве случаев определяет в целом качество, работоспособность и экономичность создаваемых изделий.
РАЗДЕЛ 1 ТЕХНОЛОГИЧЕСКИЙ РАЗДЕЛ ТЕХНИЧЕСКАЯ ХАРАКТЕРИСТИКА СВАРОЧНОГО УЧАСТКА
| ||||||||||
ГБОУ ПО СевКИТиП | ||||||||||
Изм. | Лист | № докум. | Подп | Дата | ||||||
Разраб. | Ремнев Н.С | Лит. | Лист | Листов | ||||||
Пров. | Кричевец Д.С. | |||||||||
№318 | ||||||||||
Н.контр. | ||||||||||
Утв. | ||||||||||
1.1 Назначение сварочного участка
Сварочное отделение предназначено для ремонта поврежденных деталей сваркой, заварки трещин кузова, кабины, оперения, а также восстановление изношенных деталей наплавкой металла. В отделении применяется электродуговая и газовая сварка. Работы газовой сварки обычно подразделяют на сварку деталей из толстолистовой стали и сварку тонколистовой стали кузовов, а так же тонкостенных деталей. Электросваркой ремонтируют массивные детали (раму).При поломке какой-то детали, которую можно восстановить сваркой ее направляют в сварочное отделение. После очистки проводят дефектовку, то есть определяют можно восстановить данную деталь. Если это невозможно ее списывают. Если возможно, то решают, каким именно способом будет проводиться сварки (газовое или электродуговая). После сварки проводят контроль качества для того, чтобы определить пригодность восстановленной детали к дальнейшей эксплуатации. Если возобновляемая деталь входила в состав узла или агрегата, который разбирали непосредственно в отделении то после монтажа этот узел или агрегат отправляют на выдачу.
1.2 Подготовка металла (деталей) к сварке.
Металл, идущий на изготовление сварных конструкций, предварительно очищают и выправляют. Очистка должна производиться до сборки узла. В месте сварки кромки тщательно очищают от ржавчины, масла, влаги, окалины, загрязнений, наличие которых приводит к образованию пор и других дефектов. Особенно следует обратить внимание на зачистку в зазоре между кромками. Если в зазор уже собранного узла попали загрязнения, его следует тщательно продуть сжатым воздухом или прожечь пламенем горелки.
Очистка производится ручными и механическими проволочными щетками, пламенем многофакельной горелки, абразивными кругами, травлением в растворах кислот и щелочей, промывкой растворителями.
Перед сваркой кромки деталей, если это предусмотрено чертежами, подвергают обрезке, скосу и очистке.
Для обеспечения качественного провара и формирования сварного шва выполняют подготовку кромок под сварку элементами геометрической формы подготовки кромок под сварку являются: угол разделки кромок, угол скоса одной кромки, зазор между стыкуемыми кромками и притупление. Существующие способы ручной дуговой сварки позволяют сваривать без разделки кромок металл ограниченной толщины - до 6 мм. Поэтому при сварке металла большой толщины необходимо разделывать кромки для доступа сварочной дуги вглубь соединения и полного проплавления кромок на всю толщину.
1.3 Сборка деталей под сварку
Более 30 % общей трудоёмкости изготовления сварных деталей и узлов составляют затраты труда на сборку деталей под сварку.
Сборка деталей под сварку выполняется с целью установления взаимного пространственного положения элементов сварных конструкций. Для уменьшения времени сборки, а также повышения её точности применяют различные приспособления: установочные детали, прижимные механизмы, стенды, кондуктор и др.
Сборку деталей под сварку выполняют несколькими способами. Наиболее рационален метод секционной сборки, предусматривающий сборку и сварку отдельных узлов, из которых состоит конструкция, а затем сборку и сварку всей конструкции.
При изготовлении сварных конструкций широко используют так называемый метод общей сборки сварной конструкции. Он заключается в том, что вначале всю конструкцию собирают из отдельных заготовленных элементов, а затем её сваривают. Если это не удается, то детали последовательно присоединяют к уже сваренной конструкции.
Технологический процесс сварочных работ на АТП следующий: после снятия с автомобиля кабин, оперения, с них снимают старую краску, ржавчину и направляют на сварочный участок. Здесь детали подвергаются дефектовке. Сварщик заваривает трещины, вырезает дефектные участки и приваривает заплаты. После этого зачищаются швы.
Кузова, кабины, оперение автомобилей, поступающих в ремонт, имеют стабильный характер дефектов, которые, как правило, повторяются в одних и тех же местах, что позволяет заранее разработать серию типовых дополнительных ремонтных деталей в виде заплат различной конфигурации, централизовать их изготовление на жестяницком участке и затем при ремонте приваривать их взамен удалённых дефектных участков.
Ремонт кабин и деталей оперения целесообразнее всего выполнять путём вырезки дефектных участков, неподдающихся ремонту (коррозионные разрушения, сильно помятые и разорванные поверхности и др.) и приварке ремонтных деталей.
Как правило, характер дефектов на этих деталях позволяет создать довольно стабильную номенклатуру дополнительных ремонтных деталей (боковой панели передней части кабины, нижних панелей задней части кабины, порога двери и др.)
1.4 Виды выполняемых работ на участке
Ремонт кабины
1) Деформация стоек ветрового окна и передней части крыши аварийного характера, не поддающиеся наложением заплат, заменой элементов конструкции и другими способами - браковать;
2) Вмятины с острыми загибами и разрывами на панелях передка, задка, крыши, на полу и на подставке сиденья пассажиров; Разрывы по нижнему отверстию спереди кабины в местах крепления крыла; коррозионные разрушения на нижнем поясе кабины на панелях задка, передка, порогах дверей, полу-ремонтировать, вырезание повреждённой части и приварка соответствующей дополнительной ремонтной детали;
3) Трещины на панелях передка, задка, крыши, на полу, на пороге; трещины, идущие от угла проёма двери к лобовому стеклу; трещины наот бортовке в месте сопряжения внутренней панели с полом; трещины в дверном проёме в местах крепления петель; трещины в местах крепления подставы сидения пассажиров-ремонтировать, заварка, при трещинах не устраняемых заваркой, вырезание повреждённой части кабины и приварка соответствующей дополнительной ремонтной детали.
Ремонт двери кабины
1) Трещины или разрывы на внутренней или наружных панелях, в местах крепления верхних петель; коррозионное разрушение нижней части панели-ремонтировать, вырезание повреждённой части с последующей приваркой дополнительной ремонтной детали.
2) Отрыв усилителей панели, кронштейнов обоймы двери, соединителей панелей, держателей уплотнителя - ремонтировать, заварка.
Ремонт облицовки радиатора
1) вмятины на облицовке, трещины или разрывы на нижней части облицовки - ремонтировать, заварка, вырезание повреждённой части с последующей приваркой дополнительной ремонтной детали.
2) Трещины и разрывы, проходящие через отверстия для фар и подфарников - ремонтировать, заварка или приварка накладок.
Ремонт крыла
1) Вмятины с острыми загибами или разрывами на крыле с повреждением боковин и усилителей, трещины или разрывы крыла, отрыв усилителей и боковины крыла, коррозионное разрушение крыла - ремонтировать, вырезание повреждённой части с последующей приваркой дополнительной ремонтной детали.
2) Повреждение отверстий для крепления - ремонтировать, заварка или приварка накладок.
Для выполнения всех этих работ необходимо следующее оборудование, которое сведено в таблицу 1.1
Наименование | Модель | Количество | Мощность Квт | Габаритные Размеры, мм | Площадь М2 |
Установка точечной сварки | УТ-300 | 1 | 10 | 800*400 | 0, 32 |
Сварочный трансформатор | ТС-300 | 1 | 10 | 800*500 | 0, 4 |
Сварочный выпрямитель | ВС-300 | 1 | 100 | 750*500 | 0, 375 |
Табл. 1.1
Сварочное оборудование позволяет быстро и надежно соединить металлические детали, в зависимости от технологии (ММА, MIG/MAG, TIG или SPOT), формируется прочный сварной шов или сварная точка. Поэтому оборудование для сварки различных видов широко используется во многих отраслях: на производствах, в строительстве, возведении металлических конструкций, автомобилестроении и автосервисах.
РАЗДЕЛ 2 ОРГАНИЗАЦИОННЫЙ РАЗДЕЛ
| ||||||||||
ГБОУ ПО СевКИТиП | ||||||||||
Изм. | Лист | № докум. | Подп | Дата | ||||||
Разраб. | Ремнев Н.С | Лит. | Лист | Листов | ||||||
Пров. | Кричевец Д.С. | |||||||||
№318 | ||||||||||
Н.контр. | ||||||||||
Утв. | ||||||||||
Газосварочное оборудование
Газосварка и газовая резка металлов – это способы обработки заготовок методом плавления. Преимуществами являются независимость от электроэнергии, возможность проведения работ в любом положении и в труднодоступных местах.
Технология проведения работ требует применения специального газосварочного оборудования:
Рис. 2. 1
Источник газа – баллон с пропаном или ацетиленом.
Рис. 2.2
Источник кислорода – баллон с кислородом.
Рис. 2.3
Редукторы – устанавливаются на баллоны для подачи газа и контроля давления в них и рукавах.
Рис. 2.4
Рукава – соединяют баллоны для подачи газа с рабочим инструментом.
Рабочий инструмент – для резки металлов используют газовый резак (Рис. 2.8), для сварки применяют горелку (Рис.2.9). По конструкции они схожи: к корпусу подводится два рукава, подающие газ для воспламенения. Смесь кислорода и пропана (ацетилена) под давлением выходит из сопла и воспламеняется. У резака имеется вентиль подачи газа для продувки.
Рис. 2.6 |
Рис. 2.5 |
Газосварочное оборудование в комплексе заменяет сварочный аппарат. В производственной сфере используются вспомогательные приспособления, механизирующие рабочий процесс. Например, машина для газового реза сокращает время работ и помогает получить более ровный рез.
Газовая сварка металлов
Как правило, если необходимо соединить заготовки методом плавления, прибегают к их стыковке. Струя горящего газа из сопла горелки направляется к месту стыка, туда же подается присадочный пруток. При медленном их ведении нагревается металл, его кромки расплавляются – образуется сварочный шов. В отличие от электродугового, газосварочное оборудование требует более медленной и плавной работы. Этот вид сварки используют при обработке тонколистовых заготовок, цветных металлов, чугуна, латуни, свинца и других, для которых важен медленный нагрев и медленное охлаждение.
Газовая резка металлов
В зону разрезаемого металла направляется струя горящего газа. Сначала нагревают место начала реза. Затем на резаке открывают вентиль подачи газа для продувки – струя становится мощнее и выдувает расплавленный металл. Струю плавно ведут по намеченной траектории реза. За счет нагрева и продувки происходит разделение металла. Данным методом осуществляют прямые и фигурные резы, газосварочным оборудованием производят демонтаж металлоконструкций, раскрой стальных листов, а также газовую резку труб. Главными преимуществами по сравнению с механической резкой являются высокая скорость выполнения работ, снижение трудозатрат и повышение качества обработки металла. Кроме того, с помощью газосварочного оборудования возможно осуществление работ в стесненных условиях и при любом положении резака.
Ручная дуговая сварка MMA
Ручная электродуговая сварка штучными электродами различных металлов. Покрытие электрода образует газовую атмосферу, которая препятствует взаимодействию места сварки с воздухом. Ручная дуговая сварка MMA применяется для обработки, черных и легированных металлов. Предназначенное для этого метода оборудование имеет небольшие размеры, может использоваться для работ на высоте и очень удобно в эксплуатации (справится и профессионал, и новичок).
Ручная электродуговая сварка - принцип работы
Как любая другая, дуговая mma-сварка подразумевает соединение металлических заготовок с помощью тепловой энергии, возникающей в результате горения электродуги. Такой метод получил еще название сварка покрытыми электродами, так как они имеют специальную обмазку. При замыкании электрической цепи аппарат дуговой сварки подает ток на электрод, его покрытие начинает плавиться, образуя вокруг рабочей зоны газовое облако, блокируя попадание воздуха в сварочную ванну.
Различают установки для ручной дуговой сварки переменного тока и постоянного. К первым относят трансформаторы, которые преобразуют сетевой ток в переменный нужного напряжения. Как правило, электродуговая сварка переменного тока используется для углеродистых сталей. Для обработки нержавеющей стали нужна электрическая сварка на постоянном токе, для чего может использоваться различное оборудование MMA-сварки: выпрямитель или инверторный аппарат.
Для электродуговой сварки металлов применяется следующее оборудование:
· инверторы - такие электродуговые установки обладают высокой мощностью при малом весе;
· трансформаторы - классическое средство дуговой сварки, обладает низкой ценой и высокой эффективностью;
· выпрямители - преобразуют переменный ток в постоянный, позволяющий получить более качественный шов.
Электродуговая сварка является наиболее популярным методом. Она находит применение и в профессиональной сфере, и в быту. Строительство, производство, ремонтные и монтажные работы – далеко не все сферы ее использования. Это обусловлено неоспоримыми достоинствами данного метода, которые включают в себя:
· Универсальность заключается в том, что работа выполняется во всех пространственных положениях, расширяя сферу применения. Можно выполнять вертикальные, угловые, стыковые швы, работать с тонколистовыми металлами.
· Удобство обеспечивается тем, что дуговая сварка позволяет сваривать материалы даже в стесненных условиях, труднодоступных местах и на высоте. Многие аппараты мобильны, поэтому сварщик может быстро перемещаться по рабочей площадке.
· Работа с любыми металлами открывает широкие возможности для электродуговой сварки. Метод подходит для различных видов сталей, цветных металлов, чугуна. Важно правильно подбирать электроды и выставлять силу тока на аппарате.
· Устойчивость к погодным условиям дает возможность работать на улице в любое время года и практически при любой погоде (за исключением дождя и снега). Влажность влияет на качество сварки, но проблема решается просушкой электродов.
· Простота метода позволяет легко освоить процесс даже новичку. Кроме того, ручная дуговая сварка не требует большого количества приспособлений, как, например, газосварка.
При всех своих преимуществах метод имеет некоторые недостатки. Такая сварка вредна для человека – опасности подвергаются зрение и дыхательные пути. Качество шва во многом зависит от опыта сварщика. К тому же процесс дуговой сварки не удается сделать высокопроизводительным, как, например, это происходит при работе полуавтоматом.
Дата добавления: 2018-04-15; просмотров: 408; Мы поможем в написании вашей работы! |
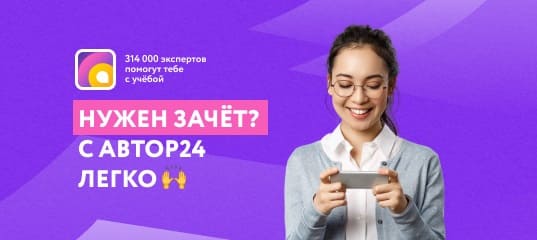
Мы поможем в написании ваших работ!