Классификация баз. Правило шести точек
Базы – поверхности или сочетание поверхностей, линий, точек и их совокупности, принадлежащие заготовке и используемые для базирования. Базы бывают конструкторские, сборочные, технологические и измерительные. Конструкторская база – база, используемая для определения положения детали в изделии. Сборочная база - база, по отношению к которой фактически ориентируются другие детали изделия. Для обеспечения наиболее широких допусков на размеры, без изменения точности, необходимо совместить сборочные и измерительные базы. Измерительная база – база, используемая для определения относительного положения поверхности и средств измерения. Под измерительной базой понимают поверхность, линию или точку, от которой производится измерение размеров.
Технологическая база – база, относительно которой ориентируется обрабатываемая поверхность на данной операции. В зависимости от способа применения базирующих поверхностей в процессе обработки они делятся на: 1) опорные; 2) настроечные; 3) поверочные.
Опорные базирующие поверхности детали – поверхности, которые непосредственно соприкасаются с установочными поверхностями приспособления или станка.
Настроечные - поверхности, по отношению к которым ориентируются другие обрабатываемые поверхности на данной детали.
Поверочные – поверхности, по которым происходит выверка положения детали на станке или установка р.и.
|
|
По значению для готового изделия технологические базы делятся на: основные и вспомогательные базы.
Основная технологическая база – поверхность детали, которая служит для установки детали при обработке, и сопрягаются с другой деталью совместно работающей в собранном изделии.
Вспомогательная технологическая база – поверхность, которая служит только для установки деталей при обработке и не оказывает никакого влияния на работу данной детали в машине.
ПРАВИЛО 6 – ти ТОЧЕК. В течение всего времени обработки заготовка должна сохранять определенное положение на станке относительно инструмента. Для этого нужно исключить 6 степеней свободы: 3х поступательных движений и 3х вращательных движений. Лишение всех степеней свободы достигается установкой детали на 6 опорных точек в 3х взаимно перпендикулярных плоскостях. Эти три плоскости представляют из себя совокупность трех баз, называемых комплектом баз и образующих координатную систему заготовки.
Классификация типовых деталей машин
Машины и приборы состоят из деталей и узлов. Деталью называют элемент конструкции, изготовленный из материала одной марки без применения сборочных операций. Детали частично могут объединяться в сборочные единицы (узлы).
|
|
Сборочной единицей называют совокупность деталей, соединенных на предприятии изготовителе посредством сборочных операций и предназначенных для совместной работы.
Простейшая сборочная единица может включаться как составная часть в более сложную. Характерными примерами сборочных единиц являются по мере нарастания сложности подшипник, узел опоры, редуктор.
В машинах количество деталей исчисляется сотнями и тысячами. Несмотря на различное конструктивное оформление и назначение машин, большинство деталей и сборочных единиц (узлов) в них являются типовыми.
Типовыми называют детали, которые встречаются практически в любой машине и независимо от назначения машины выполняют одинаковые функции.
Типовые детали можно объединить в несколько характерных групп:
· детали соединений (резьбовых, заклепочных, шпоночных, шлицевых, сварных, клеммовых, прессовых и т.д.);
· детали передач (зубчатых цилиндрических и конических, червячных, ременных, цепных, фрикционных и т.д.)
· валы и оси;
· опоры валов и осей (подшипники);
· детали муфт;
· упругие элементы (пружины, рессоры);
· корпусные детали.
Тонкая обработка валов и поверхностей
|
|
Методы тонкой обработки валов
Для достижения высокой точности и малой шероховатости наружных цилиндрических поверхностей валов применяют различные виды чистовой отделочной обработки. Основные методы отделочной обработки валов: шлифование, тонкое (алмазное) точение, полирование, суперфиниширование, притирка, обкатывание роликами и др. Метод обработки выбирают, исходя из требований к точности и шероховатости обрабатываемых поверхностей, а также в зависимости от характера детали.
Шлифование - наиболее распространенный метод чистовой обработки наружных поверхностей валов. Обычно при помощи шлифования получают 6...7-й квалитет точности и 8-й класс шероховатости поверхности (Ra ?0,63 мкм).
Тонкое (алмазное) точение применяют главным образом для обработки валов из цветных металлов и сплавов (бронзы, латуни, алюминиевых и др.), реже для обработки валов из чугуна и стали. Шлифование цветных сплавов сложнее шлифования стали и чугуна из-за засаливания шлифовального круга.
Тонкое точение производят алмазными резцами или резцами, оснащенными твердыми сплавами (например, Т30К4). Обработку производят при малой глубине резания (t = 0,05...0,3 мм) и подаче (S = 0,13...0,15 мм/об) и высокой скорости резания (v = 100...1000 м/мин).
|
|
Станки для алмазного точения должны быть быстроходными (частота вращения до 8000 мин-1) и обладать повышенной точностью и жесткостью.
По производительности тонкое (алмазное) точение несколько превосходит шлифование.
Суперфиниширование - окончательная обработка предварительно шлифованных поверхностей (чаще наружных цилиндрических) при помощи мелкозернистых абразивных или алмазных брусков, совершающих сложное движение для получения высокого качества поверхности. Бруски для суперфиниширования изготовляют из шлиф- и микропорошков.
Полирование - обработка деталей при помощи мелкозернистой абразивной (полировальной) пасты, нанесенной на эластичный полировальный круг, который изготовлен из войлока, кожи и парусины. В качестве абразива применяют порошки оксида хрома, крокуса (оксид железа), венской извести, иногда корунда и карбида кремния. Окружная скорость вращения круга при полировании деталей из стали и чугуна 30…35 м/с. Деталь прижимается к кругу силой, равной 20…50 Н.
Притирка - процесс обработки поверхности притиром, рабочая поверхность которого шаржирована мелкозернистым абразивным порошком (величина зерна 3...20 мкм), при наличии смазки или специальной пасты. Обрабатываемая деталь при этом вращается и совершает сложное движение. Притиры изготовляют из чугуна, бронзы или меди.
Дата добавления: 2018-04-05; просмотров: 677; Мы поможем в написании вашей работы! |
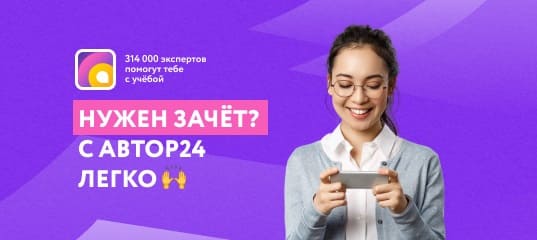
Мы поможем в написании ваших работ!