ТЕХНИКА И ТЕХНОЛОГИЯ РАЗРАБОТКИ МОРСКИХ МЕСТОРОЖДЕНИЙ УВ
5.1. МНОГООБРАЗИЕ ТЕХНИЧЕСКИХ РЕШЕНИЙ ПРИ ОСВОЕНИИ МОРСКИХ МЕСТОРОЖДЕНИЙ НЕФТИ И ГАЗА
Промышленное освоение морских нефтегазовых месторождений начинается после получения достаточно достоверных результатов геологической разведки бурением, включая получение промышленных притоков нефти и газа, подсчета и утверждения запасов углеводородов (УВ) и выполнения комплекса проектных работ, связанных с технико-экономическим обоснованием освоения конкретного месторождения. В результате рассмотрения наиболее рациональных технологий разработки месторождения и вариантов его обустройства (с учетом стоимостных показателей и сроков реализации в совокупности с суммарной добычей УВ) выбирается оптимальный вариант, который после утверждения в соответствующих надзорных государственных инстанциях подлежит реализации в обуславливаемые сроки.
Извлечение суммарного объема углеводородов с наименьшими затратами является конечной целью освоения конкретной залежи. Но для поиска оптимального решения необходимо рассмотреть, а точнее «перебрать» несколько наиболее подходящих для конкретного объекта вариантов обустройства, что и позволит сделать свой окончательный выбор. Поэтому в рассматриваемых вариантах могут быть рекомендованы не только различные типы морских нефтегазопромысловых сооружений (МНГС), но и плавучие технические средства, а также береговые технологические сооружения (так называемые береговые технологические комплексы — БТК).
|
|
БТК могут возводиться не только на морских побережьях, но и (там, где это целесообразно) на мелководных акваториях путем создания искусственных островов. Современные МНГС характеризуются большим разнообразием по конструкции, технологическому предназначению, материальному и конструктивному исполнению, по характеру закрепления на морском дне, по количеству скважин и технологических операций на них, числу опорных блоков, по ярусности, форме и площади палуб верхних строений платформ (ВСП).
Это многообразие обусловлено, прежде всего, разнообразием климатических и геолого-технических условий, гидрометеорологических сведений на точке, где предполагается установить платформу.
Конструкцию платформ определяют глубина воды, интенсивность волновых, ветровых и, возможно, ледовых нагрузок, технические возможности строительства, береговая инфраструктура, удаленность от берега, оптимальные условия транспортировки и обработки добываемой пластовой продукции и т.д.
В связи с этим МНГС можно классифицировать по:
а) материальному исполнению:
- грунтовые,
- ледовые,
|
|
- металлические,
- железобетонные,
- комбинированные;
б) конструктивным особенностям:
- дамбы и острова (насыпные),
- эстакады с приэстакадными площадками,
—погружные платформы,
—маятниковые сооружения,
—сооружения на натяжных опорах;
в) методам крепления ко дну моря:
—свайные,
—гравитационные,
—свайно-гравитационные,
—с якорными оттяжками (из канатов, цепей, труб, штанг);
г) внешним воздействиям:
—от волновых нагрузок (в том числе и «цунами»),
—от ледовых нагрузок,
—от степени сейсмичности района;
д) назначению:
—бурение скважин с одновременной их эксплуатацией, включая подготовку пластовой продукции (ПП) до товарной кондиции,
—бурение скважин с одновременной их эксплуатацией и последующей подготовкой ПП до товарных кондиций на берегу, тендерном судне или же в центральной технологической платформе (ЦТП),
—только эксплуатация скважин с их бурением с ПБУ,
—бурение скважин с ПБУ с последующей их эксплуатацией на стационарном основании и подготовкой ПП до товарных кондиций.
Со временем в основу классификации МНГС стали закладывать совокупность определенных принципов, что оправданно не только значительным усложнением самих конструкций, но и тяжелыми природными условиями новых акваторий, где открыты нефтегазовые залежи.
|
|
Это утверждение основано на тенденциях освоения более глубоководных акваторий и замерзающих морей, осложненных сейсмической активностью. Обстоятельства побуждают к поиску новых технических решений, реализация которых будет способствовать дальнейшему развитию МНГС и совершенствованию его классификации.
Наиболее полной из последних представляется предложенная Д.А. Мирзоевым классификация МНГС.
Не вдаваясь в подробности этой классификации, отметим лишь тенденции создания таких сооружений в различных условиях:
—на мелководье незамерзающих морей возможны островные сооружения при необходимости соединенные между собой дамбами. Здесь приемлемы также эстакады (предназначенные для прокладки по ним трубопроводов и перевозки грузов и людей) с приэстакадными площадками (для размещения скважин технологического оборудования);
—на глубинах до 300—350 м преимущественно используются стационарные платформы (со свайным или гравитационным закреплением), которые в зависимости от местных условий и промышленной инфраструктуры могут быть как металлическими, так и железобетонными;
|
|
- при глубинах свыше 300—350 м стационарные платформы встречаются довольно редко, на смену им приходят полупогружные плавучие технологические комплексы или суда, на которые поступает пластовая продукция уже для скважин с подводным заканчиванием.
Для эксплуатации месторождений возможна и комбинация стационарных сооружений с плавучими средствами – полупогружными платформами и судами. Например, сочетание малогабаритного бурового основания с тендерным судном, на которое поступает вся добываемая ПП, также подготавливаемая для последующей отгрузки на челночно курсирующие танкеры. Другим вариантом может быть сочетание СПБУ с выдвижной консолью (на которую переводится буровая установка, обладающая возможностью бурения до 9—12 скв.) со стационарной платформой, где размещается технологическое оборудование.
Удаленность от береговых баз, а также продолжительность ледового периода, затрудняющая регулярное снабжение платформ, вызывают необходимость обеспечения их продолжительной автономности. Независимо от климатических условий необходимо создавать достаточно комфортные условия на рабочих местах и местах отдыха для вахтенного пребывания обслуживающего персонала, что тоже ведет к увеличению размеров сооружений. И, наконец, следует отметить уязвимость северной природы требующая повышенных мер по защите окружающей среды, надежности и безопасности морских сооружений.
Совокупность указанных факторов привела к созданию новых типов сооружений принципиально отличающихся от традиционных стальной, сквозной или решетчатой конструкций, прекрасно зарекомендовавших себя в незамерзающих морях, не всегда приемлемых для жестких условий северного континентального шельфа. Исходя из общего анализа природно-климатических условий северных и дальневосточных морей и принимая во внимание географические и экономические факторы этих районов, можно установить область применения передвижных, переносных, стационарных и искусственных островных сооружений.
Бурение и эксплуатация нефтегазовых месторождений в условиях замерзающих морей проводятся с помощью МНГС в зависимости от глубин моря. При наличии карьеров крупнозернистого песка (гравия, камня) наиболее доступными в исполнении для глубин моря до 5 м являются искусственные островные сооружения (с укрепленными и неукрепленными откосами), соединенные между собой и с берегом грунтовыми дамбами.
При наличии крупных дрейфующих льдин, подводная часть которых может бороздить дно, предлагается использовать туннельно-шахтный метод. В этом случае по морю прокладывается туннель до места, где создается искусственная полость (камера) над месторождением, достаточная для размещения бурового и эксплуатационного оборудования. Применение этого метода зависит, безусловно, от расстояния месторождением и берегом, а также от грунтовых условий по трассе прокладки туннеля. Однако необходимо заметить, что этот метод еще нигде не реализован.
На мелководных участках (до 15—20 м), в отсутствие высокой сейсмичности, наиболее эффективными могут оказаться островные сооружения из земляных или иных материалов в сочетании с железобетонными или металлическими ограждающими конструкциями. Примерно на этих же глубинах в определенных условиях можно применение железобетонных и металлических платформ наплавного типа, балластируемых песком.
Глубоководные стационарные платформы делятся, в зависимости от реакции сооружения на воздействие динамической волновой нагрузки, на «жесткие» и «упругие», что, во-первых, объективно отражает соотношение их главных размеров и конфигурации, а во-вторых, указывает на величину собственных колебаний. Например, период колебаний жестких оснований находится в пределах 4—6 с упругих — превышает 20, а в одном из проектов плавучей башни достигает 138.
По способам обеспечения устойчивости под воздействием внешних нагрузок платформы подразделяются на «гравитационные» и «свайные» Если же сооружение неподвижно относительно морского дна благодаря собственной массе и системе свай — оно относится к конструкциям со смешанным способом крепления (гравитационно-свайным).
Разделение конструкций на «жесткие-гравитационные» (или «гравитационно-свайные») базируется на преимущественной составляющей доле материала, из которое изготовлено сооружение. Так, к «стальным» отнесены трехопорные основания (треноги) и пространственные фермы (джекеты); к «бетонным» — гравитационные башни а к «комбинированным» — конструкции, основные части которых из стали и бетона.
В категории «жесткие-свайные» конструкции подразделяются на «стандартны фермовые» и «плавучие фермовые».
По способам обеспечения устойчивости под воздействием внешних нагрузок упругие конструкции подразделяются:
—на «башни с оттяжками» — сохраняющие свою устойчивость с помощью системы оттяжек, резервуаров плавучести и противовесов;
—«плавучие башни» — подобные качающемуся маятнику, возвращающиеся в состояние равновесия с помощью порожних резервуаров, установленных ниже уровня моря в верхней части опорной конструкции;
—«гибкие башни» — отклоняющиеся от вертикали под воздействием волн; но при этом они, подобно сжатой пружине, стремятся возвратиться в состоянии равновесия.
Платформы разной конструкции объединяются едиными квалификационными признаками и по классификации образуют десять групп конструкций, обозначаемые началъными буквами английских слов, что принято в качестве отличительных признаков. Например, RGS: Rigid Gravity Steel — жесткая-гравитационная-стальная RGC: Rigid Gravity Concrete — жесткая-гравитационная-бетонная.
В заключение следует отметить, что высоту платформы (ее опорной части) необходимо принимать с учетом не только глубины воды и высоты волн, но и с учетом опускания морского дна по мере разработки месторождения. Так, компания «Филлипс Петролеум» вынуждена была провести в 1987 г. дополнительные операции по подъему семи платформ на месторождении Экофиск (Северное море) на 6—6,5 м, чтобы компенсировать их погружение в результате проседания дна.
5.2. МОРСКИЕ СТАЦИОНАРНЫЕ ПЛАТФОРМЫ (МСП)
Одним из самых капитало- и материалоемких объектов из всех видов технических средств, используемых на шельфе, является морская стационарная платформа (МСП) — специальное гидротехническое сооружение, предназначенное для одновременного бурения, добычи, подготовки и транспорта продукции морских нефтегазовых скважин, количество которых на современных МСП превышает 120 ед. и лимитируется в настоящее время не столько техническими возможностями, сколько геологическими: глубиной бурения, отклонением от вертикали, расположением продуктивных пластов, их мощью и т.д.
Бурение большого числа скважин с одной платформы осуществляется двумя станками, с целью экономии времени. При этом части палубы вспомогательных систем комплекса едины: хранилища для труб разного предназначения, райзеров, цемента, глины и других компонентов буровых и цементных растворов.
Все операции — бурение скважин, добыча и подготовка добываемой продукции и её транспорт — осуществляются соответствующим оборудованием, которое устанавливается преимущественно на палубе платформы, возвышающейся над водой на безопасном расстоянии. Поэтому все комплексы оборудования объединяются в так называемые верхние строения платформы, ВСП. Однако, в зависимости от конструкции опорного блока МСП, они могут быть установлены и в самой опорной части, если она имеет размеры, способные вместить часть оборудования (например, складские помещения, насосные агрегаты и т.п.).
Различие глубин, климатических условий и степени волнения моря, а также уровень береговой инфраструктуры способствовали созданию многочисленных конструкций опорной части МСП, которые различаются:
- по способу закрепления на морском дне;
- принципиальными конструктивными особенностями;
- материальным исполнением.
Связь МСП с морским дном (закрепление в донном фунте) осуществляется различными способами:
- свайным закреплением, т.е. путем забивки в морское дно свай, жестко скрепленных с опорной частью («ногами») МСП (рис. 21);
- гравитационным, под собственной тяжестью, когда масса опорной части достаточно велика, что достигается заполнением ее грунтом или водой, чтобы она прочно осела на морское дно (рис. 22), заранее подготовленное путем полного или частичного извлечения ила, устранения мешающих скальных пород, крупных камней и т.п.;
- комбинацией первых двух способов, когда затапливаемый опорный массив, располагаемый на дне, не только заполняется какой-либо средой, но и дополнительно закрепляется сваями по всему периметру своей донной части;
Рис. 21. Стальные стационарные платформы со свайным закреплением
Рис. 22.. Стационарные платформы гравитационного типа
- установкой палубы со всем комплексом ВСП на решетчатой опоре («гибкой» или «упругой»), жестко или шарнирно закрепленной на морском дне (рис. 23)
- жесткой опорой палубы со всем комплексом ВСП на затопленные (погруженные в воду полностью или частично) понтоны, прикрепляемые ко дну с помощью якорных цепей или натяжных тросов.
Опорная часть данного типа МСП может быть выполнена из пространственных решетчатых конструкций (ферм), получивших в мире наименование «джекет».
Рис. 23.. Опорные колонны стационарных платформ, закрепленные: а – шарнирно, б - жестко
Другая, принципиально иная конструкция опорной части представляет собой сплошной непроницаемый корпус, устанавливаемый на дно, как мы уже отмечали, под тяжестью собственного веса.
В этом случае опорная часть может быть и как единое целое с палубой, на которой установлены все ВСП (такое техническое решение обычно реализуется на мелководье), и как жесткое сочленение затопленной емкости большого диаметра с вертикальными сплошными опорами («ногами») значительно меньших диаметров (решение характерное для достаточно больших глубин — 100—300 м), причем в зависимости от условий гидрометеорологического режима таких опор может быть несколько. Но в любом случае гравитационное закрепление предполагает достаточно развитую поверхность подводной емкости, плотно прилегающую ко дну. Большой же объем внутреннего пространства таких опор позволяет перенести часть складских помещений и оборудования, обычно располагаемых на многоярусной палубе, внутрь опорной части.
По материалам конструкции опорные части МСП могут быть стальными (премущественно трубчатыми), железобетонными или же комбинированными (композитными). Последний тип обычно скомбинирован и по конструкции: нижняя часть - гравитационная, изготовленная из железобетона, а закрепленная над ней решетчатая конструкция опоры — из стальных труб расчетного диаметра.
Наиболее характерны глубоководные сооружения для двух районов мира, а именно — Северного моря и Мексиканского залива. В северной части Северного моря находится наибольшее количество глубоководных платформ.
Гравитационные несущие сооружения — уникальная разработка, созданная преимущественно для Северного моря; железобетонные платформы решили весьма важную проблему хранения нефти на месте добычи с периодической транспортировкой ее на берег. Появилась возможность накапливать внутри кессонных оснований 150 - 500 тыс. т продукции, перекачиваемой затем в танкеры с помощью морских загрузочных устройств, называемых беспричальными системами налива нефти, и перевозить на берег. Две наиболее удачные конструкции такого типа — платформы GBS и «Кондип», созданные в Норвегии.
Дальнейшие предложения направлены на создание все более глубоководных платформ. Принцип этих конструкций в том, чтобы сделать башни (сооружения) эластичными» - дать им возможность мягко воспринимать волну. Смещение их палуб по отношению к глубине моря считается незначительным. Такие сооружения, обозначаемые термином «податливые», это:
—шарнирно-сочлененные сооружения;
—платформы на напряженных опорах;
—расчаленные башни.
Предложены также «амортизаторные» несущие сооружения. Они остаются жесткими до тех пор, пока исключительно сильный ветер не перевесит заложенный в конструкцию «амортизаторный» эффект. После этого амортизаторы позволяют сооружению немного отклониться под влиянием дополнительной силы волн.
5.3. ПЛАВУЧИЕ ДОБЫЧНЫЕ И ТЕХНОЛОГИЧЕСКИЕ ПЛАТФОРМЫ И СУДА
В последние годы значительно возрос интерес нефтедобывающей промышленности на шельфе к плавучим комплексам эксплуатации (ПКЭ). Этот интерес вызван как экономическими, так и техническими соображениями. И если принять во внимание, что вновь открытые месторождения все дальше уходят в море и возрастают глубины, то можно утверждать, что во многих случаях экономическая целесообразность применения ПКЭ начинает превосходить выгоду от применения стационарных платформ традиционной конструкции, в особенности на небольших нефтегазовых месторождениях. А при определенных условиях ПКЭ является лучшим вариантом в случае эксплуатации даже больших нефтяных месторождений, когда стоимость работ по строительству подводных трубопроводов превышает стоимость использования челночных танкеров и беспричального налива нефти.
«Эксплуатационные преимущества плавучих комплексов очевидны при рассмотрении их технических проблем, которые могут встать на пути к освоению более сложных нефтегазовых месторождений с применением стационарных платформ. Например, глубина моря может оказаться непомерно большой, или мощность нефтеносного пласта небольшой, но с распространением в горизонтальном направлении, что вызывает необходимость в большом объеме работ по строительству сборных подводных трубопроводов. Также существенны факторы внешней среды, как, например, появление в районе промысла айсбергов, предъявляющие нереальные требования к прочности стационарных сооружений.
С другой стороны, с применением ПКЭ глубина моря уже не является столь ограничивающим фактором. При эксплуатации обширных нефтегазовых месторождений затраты можно свести к минимуму путем эксплуатации нескольких небольших плавучих установок вместо строительства подводных трубопроводов. В случае опасности появления айсберга плавучая установка без особых проблем переводится в более безопасный район, на время прерывая добычу нефти.
Преимущества гибкой и подвижной работы ПКЭ проявляются и в других случаях. По завершении работ в одной точке полупогружная установка оперативно переводится на другую или переоборудуется в целях выполнения других работ. После полной разработки месторождения его окончательный вывод из эксплуатации достаточно прост.
Первый ПКЭ, на базе переоборудованной ППБУ, установлен в 1975 г. в Северном мope, на месторождении Арджилл, при глубине моря 80 м, и рассчитан на подключение 11 подводных скважин. ПКЭ на базе переоборудованного танкера установлен в 1977 г. (месторождение Кастелон) на средиземноморском шельфе Испании, при глубине 161 м.
В 1999 г. на Мировом шельфе в эксплуатации находилось свыше 90 ПКЭ, в том числе 22 — на базе переоборудованных ППБУ и 16 — на базе танкеров; примерно одна треть из них построена фирмой «Акер» (Норвегия). В ближайшие годы предполагается ввести в эксплуатацию еще около 20 комплексов.
Первый специализированный, а не переоборудованный ПКЭ был спроектирован фирмой «Гетаверкен Арендал» для месторождения Балморал в Северном море (глубина воды 140 м, извлекаемые запасы нефти 11 млн т, пиковый общий объем добычи из 13 эксплуатационных скважин 3 млн т/год, при сроке рентабельной эксплуатации месторождения 12 лет). Для поддержания пластового давления предусматривалось оборудование для подготовки и закачки воды (13,7 тыс. м3 при давлении 7 МПа в шести нагнетательных скважинах), оборудование для газлифтной добычи нефти, рассчитанное на закачку 280 тыс. м3/сут газа, жилой блок на 120 чел, а также глубоководный комплекс (для работы в насыщении) на 12 чел. Расположение оборудования обеспечивало проведение подземного ремонта без прекращения добычи (сведения по Интернету).
Один из крупнейших в мире ПКЭ работает с января 1986 г. на шельфе Нигерии. Нефть из 20 скважин добычных СП трех относительно удаленных месторождений поступает по трубопроводу на специальную стационарную платформу на мелководье, с постоянно пришвартованным к ней (через вертлюг) танкером дедвейтом 285 тыс. т и с двумя раздельными системами подготовки нефтей, легкой и тяжелой по 5480 т/сут. Комплекс рассчитан на хранение 278 тыс. т очищенной нефти и загрузку челночных танкеров дедвейтом 250 тыс. т.
Добычная установка на основе танкера обычно дешевле переоборудованной ППБУ рассчитаной на глубину моря до 600 м и подключение до 15 скважин с дебитом до 1 тыс. м3/сут. Такая установка стоит 70—100 млн долл., а установка на основе переоборудованной ППБУ — 120—250 млн долл. (в ценах 1996—1998 гг.),
Среди многочисленных параметров, определяющих общую экономическую целесообразность проектов любой конструкции, можно выделить следующие:
—данные по нефтегазовому месторождению, например, количество и характеристики пластов, свойства углеводородов;
—данные по окружающей среде — глубина моря, состояние морского грунта, климат в районе месторождения, расстояние до берега или до других нефтепромыслов;
—возможные варианты организации транспорта, системы сдачи продукции — наличие трубопроводов, расходы на транспорт;
—перспективы дальнейшей разработки месторождения — количество, типы и местонахождение имеющихся буровых установок, время реализации данного проекта, динамика производительности, затраты на эксплуатацию;
—характеристика рынка — динамика стоимости нефти и газа;
—возможные варианты финансирования — баланс собственного и ссудного капитала, процентные ставки, сроки погашения долгов;
—общая экономическая обстановка, включая темпы инфляции, обменные курсы, размеры налогообложения, лицензионные платежи и т.д.
5.4. ВОДОПОДГОТОВКА НА МОРСКИХ МЕСТОРОЖДЕНИЯХ ДЛЯ ПОДДЕРЖАНИЯ ПЛАСТОВОГО ДАВЛЕНИЯ
Первоначальное пластовое давление обычно является достаточным для обеспечения подъема нефти из эксплуатационных скважин на поверхность, но продолжающаяся добыча при естественном режиме на истощение влечет снижение пластового давления, а соответственно и объемов добычи. Естественные режимы разработки дают возможность достичь так называемой первоначальной нефтеотдачи, т.е. извлечения приблизительно 25% первоначальных запасов нефти. Экономическая целесообразность в увеличении степени нефтеотдачи и возможно большем увеличении количества добытой нефти привела к росту значимости вторичных методов разработки с использованием заводнения для поддержания первоначального пластового давления.
В большом перечне задач по освоению ресурсов континентального шельфа проблема максимального извлечения нефти занимает ведущее место, поскольку максимум добытой нефти способствует эффективности капитальных вложений, неотъемлемых при освоении морских месторождений.
Во всем мире проблеме эффективности максимального извлечения уделяется огромное внимание и наиболее признанным путём считается заводнение продуктивных пластов с целью поддержания пластового давления (ППД), неуклонно снижающегося по мере роста объемов добытой нефти. ППД, как правило, осуществляют с самого начала разработки месторождения в объемах, превышающих объемы добычи продукции в 1,3—1,8 раза в зависимости от геологической структуры, включающей разнообразные параметры, такие как пористость и проницаемость пласта, слагаемые породы, физико-химические свойства флюидов в пластовых условиях и т.д.
В настоящее время использование заводнения рассматривается на концептуальной фазе для большинства новых месторождений, причем уже не только нефтяных, но и газоконденсатных. Море — наиболее распространенный источник воды для закачки в особенности на начальном этапе разработки; на суше могут применяться пластовая и речная (озерная) воды.
Для обеспечения фильтрации нефти в пористых осадочных коллекторах между порами должно существовать сообщение, и размер сообщающихся пор должен быть достаточным для фильтрации флюидов с необходимой скоростью. На практике, для поддержания проницаемости и пористости пласта необходимо удаление из закачиваемой воды взвешенных частиц, включающих в себя морские организмы, частицы нефти, глину, бактерии, продукты коррозии и т.д., так что система очистки для заводнения может быть достаточно сложной. Итак, параметры качества нагнетаемой воды определяются инженерами по разработке на основе исследований и испытаний образцов керна. Они позволяют установить допустимые значения размеров и концентраций мехпримесей в воде, исследовать совместимость воды источника с пластовой водой, возможность продолжения добычи после снижения первоначального пластового давления.
Качество исходной воды должно быть исследовано в течение определенного промежутка времени, чтобы быть уверенным, что возможные сезонные колебания не окажут негативного влияния на работу установки подготовки воды. Необходим регулярный отбор проб с регистрацией всех параметров воды после лабораторных исследований применимости ее для нагнетания. В некоторых случаях, для получения еще более надежных показателей, проводятся и пилотные испытания.
При разработке всего комплекса технических решений по водоподготовке необходимо, прежде всего, изучить все свойства продуктивного пласта, подлежащего заводнению. С этой целью создается модель пласта со всеми присущими ему ocoбенностями, с тем чтобы изучить:
—характер вытеснения нефти закачиваемой в пласт водой (морской и пластовой);
—характер взаимодействия реальной морской воды с пластовой;
—необходимость воздействия определенных химреагентов на морскую и пластовую воды;
—интенсивность заводнения и т.п.;
—влияние температуры закачиваемой в пласт воды (что особенно важно для вытеснения высоковязких и тяжелых нефтей);
—влияние газонасыщенности на характер вытеснения;
—влияние дозируемых в воды химреагентов (с предварительным их выбором).
Зная качество воды для нагнетания, пластовые требования и все вопросы совместимости, можно разработать соответствующую схему очистки воды. В схеме должно уделяться внимание (в особенности для морской добычи) требованиям по размер весу и, разумеется, стоимости оборудования, с целью достижения простой, надежной работы с необходимыми параметрами.
Забор воды обычно производится из срединного морского слоя, где попадание взвешенного материала с поверхности и со дна сведено к минимуму. Поверхностные слои содержат биологический материал в форме морских водорослей/планктонов концентрация которых обыкновенно подвержена сезонным изменениям и характеризуется так называемыми «периодами цветения», когда увеличенные скорости роста могут приводить к проблемам с фильтрацией. Донные слои могут содержать количество неорганических примесей, поднятых со дна моря волновой активностью и течениями, вода насыщена кислородом, который вместе с соленостью образует сильно коррозионную жидкость, требуя особого внимания к выбору материалов.
Контроль содержания микроорганизмов в системе закачки обычно осуществляется хлором как бактерицидом. Без стерилизации аэробные и анаэробные бактерии, размножаясь без помех, могут привести к закупорке пласта, в то время как морская микроорганика, увеличиваясь, блокировала бы систему пласт — скважина — оборудование — трубопроводы. Производство хлора из морской воды путем электролиза, где бактерицид получается в удобной форме разбавленного раствора гипохлорита, устраняет необходимость в доставке и использовании газообразного хлора. Он может подаваться непосредственно в морскую воду у подъемных насосов в количестве, необходимом для эффективного уничтожения бактерий. Раствор гипохлорита является высококоррозионным и должен подаваться по пластиковым или титановым трубам.
Грубая фильтрация морской воды широко применяется для удаления наиболее крупного взвешенного материала, обеспечивая разгрузку основных фильтров в периоды цветения или штормов. Она также очищает воду, предназначенную для обратной промывки фильтров с отсыпкой, предотвращающей закупоривание системы распределения обратной промывки. В случаях применения морской воды для коммунальных целей, эти фильтры помогают устранить увеличение концентрации взвешенных материалов в трубах и емкостях. Фильтры грубой очистки обычно автоматическиe, с обратной промывкой, обеспечивающие нормальную работу во время очистки-— удаление мехпримесей размером более 80—100 мкм. В случае предполагаемых особенно бурных периодов цветения или сильных возмущений морского дна, фильтрационные мощности должны быть соответственно рассчитаны, с тем чтобы обеспечить их постоянную работу в любое время.
Требования к закачиваемой профильтрованной морской воде очень высоки: показатель в 95—98% удаления всех частиц размером более 2 мкм достаточно типичен. В большинстве случаев морская вода имеет невысокую концентрацию взвешенных частиц, с преобладанием высокого процента частиц размером менее 5 мкм.
Наиболее подходящим для этой работы принят сегодня двухслойный фильтр с потоком сверху вниз, поскольку предлагает высокую степень очистки при минимальном размере и весе фильтра, хорошей возможности хранения частиц и автоматизации работы и процесса обратной промывки.
5.5. СПЕЦИФИКА ЗАКАЧКИ ВОДЫ НА МОРСКИХ НЕФТЕГАЗОВЫХ ЗАЛЕЖАХ
Специфика закачки воды на морских месторождениях заключается в том, что на разных этапах разработки пластовая вода в добываемой нефти или отсутствует, или слишком мало для реализации требований к объемам заводнения. Поэтому приходится закачивать в пласт морскую воду. В последующем, с ростом содержания пластовой воды в добываемой нефти можно закачивать как морскую воду, так и пластовую соответственно снижая объемы морской воды. И, наконец, на заключительных этапах разработки, когда объемы пластовой воды будут превышать объемы нефти, добываемой из скважин, закачку продолжают, значительно сократив объемы морской воды за счет увеличения объемов пластовой.
Поскольку технология подготовки к закачке пластовых вод и морской воды существенно различается, на платформе необходимо иметь различное оборудование подбор которого осуществляется в зависимости от характера этих вод, их состав производительность — исходя из максимальной потребности закачки.
Закачка пластовых вод в продуктивный пласт, безусловно, предпочтительнее, чем их сброс в море, даже после тщательной очистки, с технологических позиций не говоря уже об экологических. С технологических позиций, операция закачивания пластовой воды в родной пласт наиболее приемлема, поскольку очищенная, она по своему составу практически не отличается от вод в пласте, и смешивание их не вызывает никаких осложнений, тем более, что пластовые воды обладают более высокими моющими свойствами, чем морская вода. Именно поэтому, как только количество пластовой воды оказывается достаточным с точки зрения объемов закачки, подавать в пласт морскую воду прекращают или же существенно уменьшают.
Особенности закачки на морских месторождениях еще и в том, что комплекс подготовки пластовой воды и морской должны быть установлены в составе верхних строений платформы (ВСП) до начала ее функционирования, поскольку очень затруднительно вести строительно-монтажные работы в процессе бурения и эксплуатации скважин.
И, наконец, специфическое отличие закачки на море заключается в так называемой возможной несовместимости морской и пластовой вод — образование ocaдка при смешивании этих вод, способного закупорить призабойную зону нагнетательных скважин. В связи с этим необходимо предварительно изучить природу этих вод с тем чтобы не допустить их смешивания до закачки, которую следует производить отдельно, по нагнетательным скважинам, расположенным за первоначальным контуром нефтеносности, т.е. за пределами продуктивного пласта, содержащего нефть. Пластовую же воду следует закачивать в скважины, ранее бывшие эксплуатационными, а затем переведенные в разряд нагнетательных, в связи с отбором пластовой продукции, не превышающей 10—15% от общего извлекаемого объема. Естественно, что период наращивания объемов закачки пластовой воды находится в полной зависимости от темпов обводнения.
Указанную несовместимость вод нередко преодолевают путем химической обработки, т.е. с помощью химреагентов, подбираемых опытным путем. При этом следует отметить, что состав пластовых вод имеет тенденцию к изменению, в то время как состав морской воды остается неизменным весь период разработки месторождения. Отсюда вытекает необходимость периодического контроля пластовых вод с целью подбора химреагентов, предотвращающих осадкообразование при смешивай
Проблема совместимости вод возникает на этапе, когда объем пластовой воды еще не может полностью обеспечить поддержания пластового давления на необходимом уровне, т.е. когда необходимо закачивать в пласт не только пластовую воду, но и морскую. Именно при их смешении происходит резкое изменение состава, в результате чего порой возникают нерастворимые осадки в виде хлопьев, взвешенных в потоке, представляющих собой смесь взвесей кальцита и гипса, которые могут интенсивно отлагаться на стенках насосно-компрессорных труб, опускаемых в нагнетательные скважины, так и забивать поровое пространство призабойной зоны (процесс кольматации), препятствуя тем самым эффективному поддержанию пластового давления.
В связи с этим необходимы предварительные исследования по выявлению стабильности образующейся смеси вод, которые выполняются на основе многократного изучения составов и физико-химических свойств исходных вод, пластовой и морской.
Помимо модельных расчетов проводятся и натурные исследования при различных соотношениях вод, близких к реально предполагаемым. Рассчитывается склонность исследуемой воды к выделению кальцита и гипса по степени насыщения воды этими веществами.
Вообще следует заметить, что достаточно сложная природа взаимодействия вод объясняется ещё и тем, что пластовые воды содержат осадки эмульгированной нефти, количество которой со временем неизменно возрастает, что подтверждает необходимостъ периодического контроля состава и характеристики пластовых вод.
Способы очистки пластовых вод (ПВ) от эмульгированной нефти приводятся ниже.
5.5.1. МЕХАНИЧЕСКАЯ ОЧИСТКА
Под этим способом понимают осаждение подавляющей массы механических взвесей при отстаивании отсепарированной ПВ, содержащей как механические примеси, так и эмульгированную нефть.
Механизм отделения последней от воды по сути такой же, и отличается лишь тем, что частицы нефти не оседают, а всплывают благодаря разности плотностей, и чем больше эта разность, тем интенсивнее идет процесс расслоения жидкости.
Однако на морских платформах в силу ограниченности площадей отстойные пруды и нефтеловушки практически не используются.
5.5.2. ФЛОТАЦИЯ
Более интенсивным способом расслоения водонефтяных эмульсий является флотация, при которой под столб неочищенной жидкости непрерывно подается воздух к пузырькам которого прилипают частички нефти, а на поверхности образуется пена, устойчивость которой зависит от используемых химреагентов.
По существу флотация ПВ представляет собой принудительно ускоренный процесс сепарации (разделения) двух жидкостей (нефти и воды) с помощью микропузырьков воздуха или газа.
5.5.3. ХИМИЧЕСКАЯ ОЧИСТКА
Одним из наиболее эффективных для очистки пластовых вод является способ основанный на непрерывном добавлении в неочищенную воду коагулянтов при определенной концентрации которых происходит интенсивное расслоение частиц эмульгированной и коллоидной нефтей, минеральных взвесей и воды.
В присутствии коагулянта происходит укрупнение всех загрязняющих воду примесей; коагулянт, являясь электролитом, снижает отрицательный заряд отталкивающихся друг от друга частиц и способствует их укрупнению, нарушая стабильность коллоидного раствора. Коагулирующая способность электролита, имеющего противоположный заряд частиц, находящихся в воде, зависит от его валентности. Взвешенные частицы, как центры коагуляции, адсорбируют образующийся гидрат окиси металла, обволакиваясь им и образуя крупные хлопья, которые, в свою очередь адсорбируют из воды коллоидные вещества.
При осаждении хлопьев с ними механически увлекается часть неадсорбируемых веществ, загрязняющих воду.
Интенсивность процесса коагуляции зависит от солевого состава воды, особенно от концентрации в воде анионов и их валентности.
В слабоминерализированной воде образующийся коллоидный раствор гидроокиси коагулянта может, не скоагулировав, в виде коллоида пройти через фильтр. Поэтому при низком содержании солей в воду вводят ограниченное количество коагулянта.
5.5.4. ГИДРОЦИКЛОНЫ
Издавна хорошо известно, что при вращательном движении многофазной жидкости происходит ее расслоение по плотности: в поле центробежных сил тяжелая фракция отбрасывается на периферию, т.е. к стенкам, ограничивающим это поле сосуда. Более плотная фаза по стенкам сосуда стекает вниз, а менее плотная перемещается вверх создаваемым вихрем.
На этом принципе работают гидроциклонные сепараторы. Обычно гидроциклоны для очистки от нефти ПВ представляют собой цилиндрическую конструкцию с конической секцией и углами, составляющими 10—20°, как показано на рис. 8.9. В верхней установлено несколько тангенциально расположенных входов, через которые поток, попадая в циклон, разделяется на фазы: жидкая стекает по спирали и направляется к нижнему выходу, а газовая фаза с капельками нефти устремляется в центр перемещается вверх и выходит через верхнее отверстие (эффект «торнадо»).
Следует отметить, что нормальная работа гидроциклона может быть обеспечена при условии, когда перепад давления на выходах очищенной воды и газовой фазы одинаков и постоянен.
Простота конструкции и ее компактность привлекают к себе внимание для использования на морских платформах.
Фирма «Серк Бейкер», одна из ведущих в области проектирования и изготовления средств для очистки различных вод, создала несколько модификаций гидроциклонов.
Выход механических примесей
Рис.8.9. Гидроциклон цилиндрический
5.5.5. ЦЕНТРИФУГИРОВАНИЕ
В случаях, когда эмульгированная нефть имеет высокую дисперсность, а вода на границе с нефтью – низкое поверхностное натяжение, эффективно применение центрифуг, которые находят ограниченное использование на морских платформах в силу высокой стоимости, большого расхода энергии и необходимости квалифицированного обслуживания, т.е. когда другие способы очистки ПВ неэффективны. Центрифуга представляет собой чашеобразное устройство, приводимое в действие с помощью электрического двигателя. Характерная скорость вращения составляет примерно 5000 об/мин, что и позволяет достигать эффективности сепарации до 1—2 мкм.
Центрифуги состоят из дисков, расположенных друг над другом. Вращающаяся чаша содержит несколько дисков конической формы. В результате вращения вода отбрасывается на периферию, нефть по дискам, как более легкая фаза, концентрируется в центре и постепенно направляется вверх, мехпримеси периодически удаляются из аппарата.
5.5.6. ФИЛЬТРОВАНИЕ
В качестве фильтрующего материала чаще всего используется крупнозернистый песок. Отсепарированная ПВ, содержащая частицы нефти, проходя через слой песка, освобождается от значительной части нефтяных частиц, которые обволакивают зерна песка.
Процесс фильтрации ПВ происходит во времени неодинаково, поскольку в начальный период зерна песка обладают определенной гидрофильностью, но со временем, покрываясь пленкой нефти, становятся олеофилъными. Прилипание нефти зависит от скорости фильтрации воды в загрузочном материале; при этом возможно достичь и эмульгирования нефти, чему способствует снижение поверхностного натяжения.
С этой целью используют поверхностно-активные вещества, например, отходы асбестового производства, смешиваемые с кварцевым песком: крупность зерен песка составля-0,5—2,0 мм, содержание 95—96%, отходы асбеста — до 3% и другие примеси — до 1. Скорость фильтрации при толщине слоя до 40— 100 см рекомендуется в пределах 5—6 м/ч.
Режим регенерации фильтров устанавливается опытным путем, с промывкой их в несколько этапов горячей водой температурой 70—80 °С. Хотя фильтры, разработанные в различном конструктивном исполнении, в целом неплохо зарекомендовали себя при очистке ПВ, они достаточно громоздки и на платформах используются довольно редко в силу необходимости их дублирования, т.е. когда один фильтр работает, другой находится в регенерации.
5.6. ПОДВОДНАЯ ДОБЫЧА УГЛЕВОДОРОДОВ
Освоение морских месторождений путем строительства платформ и бурения скважин с них принципиально не изменило конструкции фонтанной арматуры на устье скважины, которая, как и на суше, располагалась на дневной поверхности, т.е. на палубе, и так, чтобы можно было ею управлять не только вручную, но и производить необходимые профилактические и ремонтные работы. Отличие заключается лишь в ограниченности пространства на платформе по сравнению с сушей.
С развитием технологии морского бурения, в особенности при проводке наклонных скважин со стационарных платформ, резко возросло их количество. Однако простое увеличение числа скважин не может удовлетворить всех запросов рациональной разработки месторождения, требующей достаточно четкого расположения забоев в строгом соответствии с намеченной сеткой скважин. И хотя технология бурения за последние десятилетия активно совершенствовалась, и отклонение забоев скважин от платформы возросло до 12 км. тем не менее выполнить в полном объеме требования разработки удается не всегда. Кроме того, число скважин на платформе не может быть бесконечным, а превышение стоимости проводки наклонных скважин значительно (по сравнению с вертикальными), что также ограничивает возможности, точнее, рентабельность их строительства.
В связи с этим на окраинных участках залежей стали бурить с ПБУ сперва отдельные вертикальные скважины с подводным расположением устья, а потом и целые «кусты» скважин. Так стали возникать первые конструкции скважин в подводим исполнении, или как принято их называть скважины с подводным закончиванием. В настоящее время подобные скважины появились на значительной части месторождений, как крупных, так и малых.
Фирмой «Хемилтон» создана в 1975 г. первая в мире ППБУ (TW-58), с которой начали бурить такие скважины; на платформе было установлено технологическое оборудование производительностью по жидкости 11 тыс. т/сут, приспособленное к фонтанной и газлифтной добыче нефти и закачке воды для поддержания пластовых давления в объеме 9,5 тыс. м3/сут.
5.6.1. КОНСТРУКЦИИ УСТЬЕВ ПОДВОДНЫХ СКВАЖИН
При всем многообразии созданных конструкций их можно условно разделить на два типа:
1) открытый, когда устьевое оборудование установлено непосредственно в морской воде и подвергается воздействию полного гидростатического давления столба воды, рис. 24 (нередко этот тип называют «мокрым»);
2) закрытый, когда устьевое оборудование заключено в герметичную камеру (естественно, рассчитанную на гидростатическое давление при известной глубине), в которой устанавливается нормальное давление, а иногда и несколько избыточное, рис. 25-а и 25-б (поэтому тип конструкции нередко именуют сухим).
Рис. 24. Открытая («мокрая») конструкция подводной скважины
Также существуют «гибридные» системы, когда часть оборудования, чаще всего управляющие органы, заключены в кожух.
Преимущественное развитие получили мокрые системы — около 85 %, сухих значительно меньше — около 10%, а гибридных — менее 5%. Такое положение объясняется прежде всего тем, что первые значительно проще изготавливать для целых кустов подводных скважин, в то время как сухие предпочтительны для одиночных.
Рис. 25-а. Закрытый («сухой») тип конструкции устья подводной
Рис. 25-б. Система «сухой» оболочки
Во всех случаях устья скважин устанавливаются выше уровня морского дна, значительно реже их поднимают на палубу, целиком погруженную в воду. Такой вариант иногда используют на больших глубинах, чтобы облегчить работу водолазов.
На замерзающем мелководье и неглубоких акваториях с интенсивным рыбным промыслом подводные устья можно защитить, укрыв их кожухами обтекаемой формы или несколько заглубив в дно. При этом в некоторых случаях заглубляемую подводную арматуру размещают в башне (которую иногда называют силосной) (рис. 26-а – 26-в).
Естественно, что для создания углублений в дне моря необходимо наличие соответствующих технических средств: подводного бульдозера или устанавливаемой на судне лебедки с электрогидравлическим грейдером. Наиболее надежной и рентабельной является конструкция, защищающая подводное устье (рис. 26-г), которая установлена на многих подводных скважинах.
В связи с ограничениями и сложностью контроля и инспекции подводного оборудования, а также высокой стоимостью их проведения, проблема обеспечения надежности является одной из самых главных при использовании методов и средств подводной технологии. Большая часть неисправностей и отказов может существенно повлиять на состояние окружающей среды. Только непрерывная добыча углеводородов запланированных объемов в состоянии окупить значительные капитальные вложения в подводную добычу.
Рис. 26-а. Заканчивание с «открытой воронкой»
Рис.26-б. Система заканчивания с кессоном
Рис. 26- в. Заканчивание «силосной» скважины
Рис. 26- г. Защита устьевой арматуры, расположенной на морском дне:
1 — гнездо для присоединения третьего отвода трубопровода; 2 — первый отвод трубопровода; 3 — гнездо для возможного присоединения отвода трубопровода; 4 — верхняя конструкция, покрытая защитными панелями; 5 — трубопровод диаметром 762 мм; 6 — бетонная обваловка по периметру колпака
Минимизация подводных операций, извлекаемость компонентов техники, относительная легкость своевременной замены неисправных узлов, могут обеспечить непрерывность процесса. Поэтому в систему подводной добычи закладывается принцип частичного дублирования технологических функций, успешно реализуемый при строгом контроле качества используемых изделий и их надлежащем испытании. Кроме того, особое внимание уделяется подбору материалов, из которых должны изготавливаться подводные изделия, обеспечивающие стойкость к коррозии и другим вредным воздействиям водной среды.
Перечисленные требования могут быть реализованы при доступности использования водолазов, а в ряде случаев и применении манипуляторов, действия которых большая глубина практически не ограничивает.
Эксплуатация скважин с подводным заканчиванием проводится преимущественно с помощью дистанционно управляемой арматуры, а профилактический надзор или ремонт — подготовленными водолазами. В случае сухого типа устья используются подводные аппараты, которые могут шлюзоваться с герметическим корпусом подводного устья.
Устьевое оборудование под водой может быть установлено на устьях отдельных вертикалъно пробуренных или наклонно-направленных скважин, расположенных на ограниченной площади кустом.
Для управления этим оборудованием и манифольдными камерами применяются гидравлические или электрогидравлические системы. Управление каждой задвижкой может осуществляться либо по отдельным линиям, идущим с обслуживающего судна, либо через единый распределительный блок. При использовании электрогидравлических систем управления электроэнергия подается с обслуживающего судна по кабелю либо берется от аккумуляторной батареи, размещенной непосредственно под водой.
На практике системы с открытым расположением устьевого оборудования сочетаются с закрытыми манифольными переключателями и наоборот. Оборудование, предназначенное для установки под водой на устье пробуренной скважины, должно быть предварительно опрессовано при давлении, превышающем максимально возможное рабочее давление. Обязательной является установка дистанционно управляемого отсекающего клапана. Устьевая арматура в сборе спускается с судна на канатах. Монтаж её производиться водолазами либо с помощью специальных подводных роботов-манипуляторов. Предложено также несколько конструкций миниатюрных подводных лодок, за счет чего эффективное время пребывания водолазов под водой значительно увиличивается.
Особые требования с точки зрения надежности предъявляются к запорной арматуре-задвижкам и клапанам, приводные устройства которых должны характеризоваться надежностью, а сами задвижки и клапаны — полной герметичностью. Арматура изготавливается из специальных сталей, отличающихся высокой коррозионной стойкостью к агрессивному воздействию морской воды.
Системы подводного заканчивания в сочетании с плавучими технологическими платформами по сравнению с традиционными методами освоения, при которых устья скважин размещены на стационарных платформах, имеют следующие преимущества:
- ускоренный вывод месторождения на проектную мощность за счет испольвания заранее пробуренных с ПБУ эксплуатационных скважин;
- высокая гибкость технологии подводной добычи за счет возможности быстрой смены технологического оборудования (например, при переходе от фонтанного к газлифтному способу добычи) путем замены одной технологической платформы на другую (например, на бразильском шельфе месторождение Энчова, открытое в 1977 г., было переоборудовано 5 раз, а месторождение Гарупа — 3 раза);
- возможность сезонной разработки месторождений, расположенных в районах с неблагоприятными гидрометеорологическими условиями (например, в арктических морях при наличии ледовых полей, торосов, айсбергов) и др.
Дата добавления: 2018-04-05; просмотров: 2282; Мы поможем в написании вашей работы! |
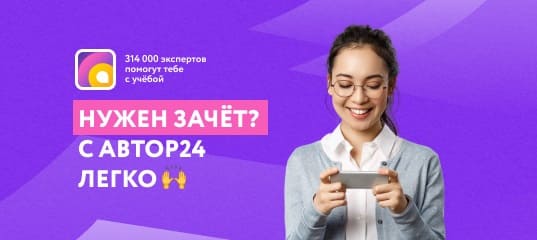
Мы поможем в написании ваших работ!