Охарактеризуйте азотирование
Азотированием называется процесс насыщения поверхности сталей азотом. Целью азотирования является создание поверхностного слоя с особо высокой твердостью, износостойкостью, повышенной усталостной прочностью и высоким сопротивлением коррозии. Процесс азотирования состоит в выдержке деталей в течение длительного времени (до 60 ч) в атмосфере аммиака при 500-600 ºC. При более высокой температуре образуются более крупные нитриды, и твердость уменьшается.
Азотирование проводят в стальных герметически закрытых ретортах, в которые поступает аммиак. Реторту помещают в нагревательную печь. Аммиак разлагается на азот и водород: NH3 →3H+N. Активные атомы азота проникают в решетку α-железа и диффундируют в ней. Высокую твердость азотированному слою придают нитриды легирующих элементов: хрома, молибдена, алюминия. При легировании стали этими элементами твердость по Виккерсу достигает 1200HV, в то время как после цементации и закалки твердость составляет 900HV.
Азотированию обычно подвергают стали 38Х2МЮА, 35ХМА, а также некоторые штамповые стали 5ХНМ, 3Х2В8. Азотированию обычно подвергают готовые изделия, прошедшие механическую и окончательную термическую обработку (закалку с высоким отпуском, температура которого выше температуры азотирования). После такой термической обработки металл приобретает структуру сорбита, имеющую высокую прочность и вязкость. Эта структура сохраняется в сердцевине детали и после азотирования. Высокая твердость при азотировании достигается сразу и не требует последующей термической обработки. Участки, не подлежащие азотированию, защищают нанесением тонкого слоя олова электролитическим методом. Глубина азотированного слоя достигает 0,3-0,6 мм. Азотирование применяют для изготовления мерительного инструмента, зубчатых колес, втулок, коленчатых валов и др.
|
|
Каковы достоинства и недостатки азотирования и цементации?
По сравнению с цементацией азотирование имеет ряд преимуществ и недостатков. Преимуществами являются более высокая твердость и износостойкость поверхностного слоя и высокая коррозионная стойкость. Азотирование не требует, что позволяет избежать сопутствующих закалке дефектов. К недостаткам азотирования относятся: более высокая длительность процесса и необходимость применения дорогостоящих легированных сталей.
Охарактеризуйте цианирование.
Цианированием (нитроцементацией) называется процесс совместного насыщения поверхности стальных деталей азотом и углеродом. Основная цель цианирования состоит в повышении твердости и износостойкости деталей. При цианировании нагрев осуществляется либо в расплавленных солях, содержащих цианистые соли NaCN или KCN, либо в газовой среде, состоящей из смеси CH4 и NH2.
|
|
В зависимости от температуры процесса различают высокотемпературное (850-950 ºC) и низкотемпературное (500-600 ºC) цианирование. Чем выше температура , тем меньше насыщение поверхностного слоя азотом и больше углеродом. Низкотемпературному цианированию подвергают окончательно изготовленный и заточенный режущий инструмент из быстрорежущих марок стали с целью повышения их износостойкости и красностойкости. Глубина цианированного слоя 0,01-0,04 мм с твердостью 1000HV.
При высокотемпературном цианировании на глубину 0,6-1,8 мм в течение 3-10 часов детали подвергают закалке и низкому отпуску. Твердость после термообработки составляет 59-62 HRC. По сравнению с цементованным цианированный слой имеет более высокую твердость и износостойкость, а также более высокое сопротивление коррозии.
Недостатком цианирования является более высокая стоимость процесса, связанная с необходимостью строгого соблюдения правил техники безопасности из-за высокой токсичности цианистых солей.
Охарактеризуйте диффузионную металлизацию.
Диффузионной металлизацией называется процесс диффузионного насыщения поверхностных слоев стали различными металлами.
|
|
Металлизация бывает твердая, жидкостная и газовая. При жидкостной металлизации стальную деталь погружают в расплав металла. При твердой и газовой металлизации насыщение происходит с помощью летучих соединений хлора с металлом AlCl3, CrCl3, SiCl4, которые при температуре 1000-1100 ºC вступают в реакцию с железом с образованием диффундирующего элемента в активном состоянии.
При алитировании детали приобретают повышенную коррозионную стойкость благодаря образованию плотной пленки Al2O3, предохраняющей металл от окисления. Толщина слоя составляет 0,2-0,5 мм.
При хромировании обеспечивается высокая стойкость против газовой коррозии до 800 ºC, а также стойкость против коррозии в морской воде и кислотах. Толщина слоя до 0,2 мм.
Силицирование (насыщение кремнием) придает высокую кислотоупорность в соляной, серной и азотной кислотах, и применяется для деталей, используемых в химической и нефтяной промышленности. Толщина слоя - 0,3-1,0 мм. Борирование придает поверхностному слою исключительно высокую твердость (до 1800-2000 HV), износостойкость и устойчивость против коррозии в различных средах.
|
|
Вопросы к теме 12. Способы упрочнения поверхности металлов. Химико-термическая обработка сталей.
6. Назовите способы упрочнения поверхностного слоя.
7. Какие процессы обеспечивают упрочнение поверхностного слоя?
8. На какой стадии изготовления производят упрочнение поверхностного слоя?
9. Охарактеризуйте дробеструйную обработку поверхности.
10. Охарактеризуйте обкатку роликами.
6. Охарактеризуйте поверхностную закалку ТВЧ.
8. Что представляет собой химико-термическая обработка?
8. Какие процессы ХТО вы знаете?
14. Охарактеризуйте процесс насыщения поверхностного слоя?
15. В чем отличие ХТО от поверхностной закалки?
16. Охарактеризуйте цементацию.
17. Какие виды цементации различают? Охарактеризуйте их.
18. Какие стали подвергают цементации? Какова структура цементированного слоя?
14. Охарактеризуйте азотирование.
15.Каковы достоинства и недостатки азотирования и цементации?
16. Охарактеризуйте цианирование.
17.Охарактеризуйте диффузионную металлизацию.
Дата добавления: 2018-04-05; просмотров: 1040; Мы поможем в написании вашей работы! |
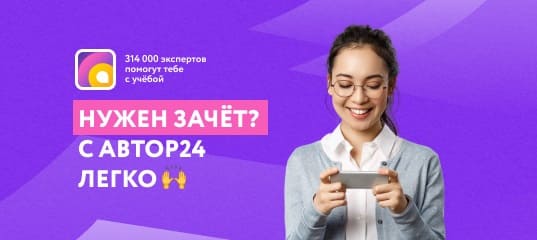
Мы поможем в написании ваших работ!