Назовите способы упрочнения поверхностного слоя
Тема 12. Способы упрочнения поверхности металлов. Химико-термическая обработка сталей.
12.1 Упрочнение поверхности методом пластической деформации. Эффективными способами упрочнения поверхностного слоя являются дробеструйная обработка и обкатка поверхности роликами. При этом происходит наклеп поверхности детали, позволяющий повысить ее усталостную прочность. Наклепу подвергают готовые детали, прошедшие механическую и термическую обработку.
При дробеструйной обработке на поверхность детаей из специальных дробеметов с большой скоростью направляют поток стальной дроби диаметром 0,5-1,5 мм. Удары дроби вызывают пластическую деформацию поверхностного слоя, вследствие чего он становится твердым. В нем создаются остаточные напряжения сжатия, и тем самым повышается усталостная прочность. Если в поверхностном слое присутствует остаточный аустенит, то благодаря наклепу происходит его превращение в мартенсит, что дополнительно увеличивает твердость и износостойкость. Благодаря дробеструйной обработке сглаживаются мелкие поверхностные дефекты, являющиеся концентраторами напряжений. Дробеструйной обработке подвергают поверхность рессор и пружин, зубчатых колес, гильз и поршней. В результате дробеструйной обработке предел выносливости рессор увеличивается в 1,5 раза и в несколько раз возрастает их долговечность.
Обкатку роликами применяют для обработки шеек валов, осей железнодорожных вагонов, коленчатых валов и других деталей. Помимо упрочнения обкатка повышает чистоту обрабатываемой поверхности.
|
|
12.2. Поверхностная закалка.Поверхностная закалка состоит в нагреве поверхностного слоя стали выше Ас3 с последующим охлаждением для получения высокой твердости и прочности в поверхностном слое детали в сочетании с вязкой сердцевиной. Высокая скорость высокочастотного нагрева (сотни градусов в секунду) обусловливает смещение фазовых превращений в область более высоких температур. Следовательно, температура высокочастотной закалки должна быть выше температуры закалки при обычном печном нагреве. (Сталь 40 при печном нагреве закаливают с температуры 840-860 ºC, при индукционном нагреве – 880-920 ºC).
Нагрев под закалку производят токами высокой частоты (ТВЧ), в расплавленных металлах и солях, пламенем газовых горелок, а также лазерным излучением. При нагреве ТВЧ магнитный поток, создаваемый переменным током, проходящим по проводнику (индуктору), инициирует вихревые токи в металле детали, помещенной внутри индуктора. Индуктор представляет собой медные трубки с циркулирующей внутри водой для охлаждения. Форма индуктора соответствует внешней форме изделия. Скорость нагрева зависит от количества выделившейся теплоты, пропорционального квадрату силы тока и сопротивлению металла.
|
|
Плотность тока по сечению детали неравномерна, на поверхности детали она значительно выше, чем в сердцевине, поэтому основное количество теплоты выделяется в тонком поверхностном слое. Глубина проникновения тока в металл зависит от свойств нагреваемого металла и обратно пропорциональна квадратному корню из частоты тока. При использовании машинных генераторов с частотой 500-15000 Гц толщина закаленного слоя составляет 2-10 мм, ламповых с частотой до 106 Гц – от десятых долей миллиметра до 2 мм. После нагрева в индукторе деталь охлаждают с помощью специального охлаждающего устройства. Через имеющиеся в нем отверстия на поверхность детали разбрызгивается охлаждающая жидкость.
Структура закаленного слоя состоит из мартенсита, а переходной зоны – из мартенсита и феррита. Глубинные слои нагреваются до температур ниже критических и при охлаждении не упрочняются.
Для повышения прочности сердцевины перед поверхностной закалкой деталь подвергают улучшению.
Преимуществами поверхностной закалки ТВЧ являются регулируемая глубина закаленного слоя; высокая производительность и возможность автоматизации; отсутствия обезуглероживания и окалинообразования; минимальное коробление детали. К недостаткам относятся высокая стоимость индуктора (индивидуального для каждой детали) и, следовательно, малая применимость ТВЧ в условиях единичного производства.
|
|
Для поверхностной закалки применяют обычно углеродистые стали, содержащие около 0,4% С. После закалки проводят низкий отпуск при 200 ºC. После закалки и отпуска твердость стали 45-55 НRС на поверхности и 25-30 HRC в сердцевине.
Высокочастотной закалке подвергают шейки коленчатых валов, кулачковых валов, гильзы цилиндров, поршневые пальцы, рессоры и т. д.
12.3. Химико-термическая обработка стали. Химико-термической обработкой (ХТО) называют процесс, сочетающий в себе поверхностное насыщение стали тем или иным элементом при высокой температуре и термическое воздействие, в результате которых происходит изменение химического состава, микроструктуры и свойств поверхностных слоев деталей.
Химико-термическая обработка включает в себя цементацию, азотирование, цианирование, алитирование, силицирование и т. д. Насыщение поверхностного слоя происходит при нагреве детали до определенной
|
|
температуры в среде, легко выделяющей насыщающий элемент в активном состоянии, и выдержке при этой
температуре. Среды, выделяющие насыщающий элемент, могут быть газообразными, жидкими и твердыми.
В отличие от поверхностной закалки при ХТО разница в свойствах достигается изменением не только структуры металла, но и его химического состава.
Основные элементарные процессы химико-термической обработки следующие:
1. Диссоциация – выделение насыщающего элемента в активном атомарном состоянии в результате разложения исходных веществ: 2СО→СО2+С; 2NH3 →3Н2+2N и т.д.
2. Абсорбция – захват поверхностью металла свободных атомов насыщающего элемента. Развитию процесса абсорбции способствует возможность диффундирующего элемента образовывать с основным металлом твердые растворы и химические соединения.
3. Диффузия – проникновение насыщающего элемента в глубь металла. В результате абсорбции химический состав поверхностного слоя меняется, при этом создается градиент концентраций насыщающего элемента в поверхностных и нижележащих слоях. Диффузия протекает легче при образовании твердых растворов внедрения (С, N), чем твердых растворов замещения (Al, Cr, Si). Поэтому при диффузионной металлизации процесс ведут при более высоких температурах.
12.3.1 Цементация стали. Цементацией называют процесс диффузионного насыщения поверхностного слоя стальных деталей углеродом. Цель цементации – достижение высокой твердости и износостойкости поверхности детали в сочетании с вязкой сердцевиной. На цементацию поступают механически обработанные детали с припуском на шлифование. В тех случаях, когда цементации подвергается только часть детали, остальные участки защищают либо большим припуском, который после цементации снимают, либо специальными огнеупорными обмазками, либо тонким слоем меди, нанесенным электролитическим путем.
Цементации подвергают стали с низким содержанием углерода (0,1-0,2%). После цементации на поверхности концентрация углерода достигает 1,0%. Глубина цементированного слоя обычно лежит в пределах 0,5-2,5 мм. Для достижения высокой поверхностной твердости и вязкой сердцевины после цементации всегда проводят закалку с низким отпуском.
Различают два основных вида цементации: в твердой и газовой средах. Твердая цементация проводится в специальных стальных ящиках, в которых детали укладывают попеременно с твердым карбюризатором. В качестве карбюризатора – твердой средой, поставляющей углерод к поверхности детали, используют дубовый и березовый древесный уголь и активизаторы BaCO3 или Na2CО3. Ящики закрывают крышками и замазывают огнеупорной глиной для предотвращения утечки газов.
Процесс цементации проводят выше Ас3 (обычно 910-930 ºC), когда сталь находится в аустенитном состоянии, которое характеризуется высокой растворимостью углерода. При нагреве идут реакции:
2С+О2 → 2СО; BaCO3+С→BaO+2CO; 2СО→СО2+С.
Образующиеся активные атомы углерода диффундируют в решетку γ-железа.
В процессе газовой цементации стальные детали нагревают в газовых смесях, содержащих СО, СH4 и др. Газовая цементация проходит быстро, так как не требует времени на прогрев ящика и карбюризатора. Слой толщиной 1 мм образуется за 6-7 ч.
Цементации подвергают стали с низким содержанием углерода (0,1-0,2%). Глубина цементированного слоя обычно лежит в пределах 0,5-2,5 мм. Полученный в результате цементации наружный слой содержит более более 0,8% углерода и имеет структуру заэвтектоидных сталей –перлит и вторичный цементит. Глубже лежит слой эвтектоидного состава с перлитной структурой, а далее – слой с феррито-перлитной структурой. Для достижения высокой поверхностной твердости и вязкой сердцевины после цементации проводят закалку с низким отпуском. После такой термообработки поверхностный заэвтектоидный слой имеет структуру отпущенного мартенсита, а сердцевина из-за низкой прокаливаемости имеет феррито-перлитную структуру.
12.3.2. Азотирование стали. Азотированием называется процесс насыщения поверхности сталей азотом. Целью азотирования является создание поверхностного слоя с особо высокой твердостью, износостойкостью, повышенной усталостной прочностью и высоким сопротивлением коррозии.
Процесс азотирования состоит в выдержке деталей в течение длительного времени (до 60 ч) в атмосфере аммиака при 500-600 ºC. При более высокой температуре образуются более крупные нитриды, и твердость уменьшается.
Азотирование проводят в стальных герметически закрытых ретортах, в которые поступает аммиак. Реторту помещают в нагревательную печь. Поступающий из баллонов аммиак разлагается на азот и водород: NH3 →3H+N. Активные атомы азота проникают в решетку α-железа и диффундируют в ней. Высокую твердость азотированному слою придают нитриды легирующих элементов: хрома, молибдена, алюминия. При легировании стали этими элементами твердость по Виккерсу достигает 1200HV, в то время
как после цементации и закалки твердость составляет 900HV.
Азотированию обычно подвергают стали 38Х2МЮА, 35ХМА, а также некоторые штамповые стали 5ХНМ, 3Х2В8. Азотированию обычно подвергают готовые изделия, прошедшие механическую и окончательную термическую обработку (закалку с высоким отпуском, температура которого выше температуры азотирования). После такой термической обработки металл приобретает структуру сорбита, имеющую высокую прочность и вязкость. Эта структура сохраняется в сердцевине детали и после азотирования. Высокая твердость при азотировании достигается сразу и не требует последующей термической обработки. Участки, не подлежащие азотированию, защищают нанесением тонкого слоя олова электролитическим методом. Глубина азотированного слоя достигает 0,3-0,6 мм.
По сравнению с цементацией азотирование имеет ряд преимуществ и недостатков. Преимуществами являются более высокая твердость и износостойкость поверхностного слоя и высокая коррозионная стойкость. Азотирование не требует, что позволяет избежать сопутствующих закалке дефектов.
К недостаткам азотирования относятся: более высокая длительность процесса и необходимость применения дорогостоящих легированных сталей. Азотирование применяют для изготовления мерительного инструмента, зубчатых колес, втулок, коленчатых валов и др.
12.3.3. Цианирование сталей. Цианированием (нитроцементацией) называется процесс совместного насыщения поверхности стальных деталей азотом и углеродом. Цель цианирования состоит в повышении твердости и износостойкости деталей.
При цианировании нагрев осуществляется либо в расплавленных солях, содержащих цианистые соли NaCN или KCN, либо в газовой среде, состоящей из смеси CH4 и NH2. В зависимости от температуры процесса различают высокотемпературное (850-950 ºC) и низкотемпературное (500-600 ºC) цианирование. Чем выше температура, тем меньше насыщение поверхностного слоя азотом и больше углеродом. Низкотемпературному цианированию подвергают окончательно изготовленный и заточенный режущий инструмент из быстрорежущих марок стали с целью повышения их износостойкости и красностойкости. Глубина цианированного слоя 0,01-0,04 мм с твердостью 1000HV.
При высокотемпературном цианировании на глубину 0,6-1,8 мм в течение 3-10 часов детали подвергают закалке и низкому отпуску. Твердость после термообработки составляет 59-62 HRC.
По сравнению с цементованным цианированный слой имеет более высокую твердость и износостойкость, а также более высокое сопротивление коррозии.
Недостатком цианирования является более высокая стоимость процесса, связанная с необходимостью строгого соблюдения правил техники безопасности из-за высокой токсичности цианистых солей.
12.3.4. Диффузионная металлизация. Диффузионной металлизацией называется процесс диффузионного насыщения поверхностных слоев стали различными металлами. Металлизация бывает твердая, жидкостная и газовая. При жидкостной металлизации стальную деталь погружают в расплав металла. При твердой и газовой металлизации насыщение происходит с помощью летучих соединений хлора с металлом AlCl3, CrCl3, SiCl4, которые при температуре 1000-1100 ºC вступают в реакцию с железом с образованием диффундирующего элемента в активном состоянии.
При алитировании детали приобретают повышенную коррозионную стойкость благодаря образованию плотной пленки Al2O3, предохраняющей металл от окисления. Толщина слоя составляет 0,2-0,5 мм.
При хромировании обеспечивается высокая стойкость против газовой коррозии до 800 ºC, а также стойкость против коррозии в морской воде и кислотах. Толщина слоя до 0,2 мм.
Силицирование (насыщение кремнием) придает высокую кислотоупорность в соляной, серной и азотной кислотах, и применяется для деталей, используемых в химической и нефтяной промышленности. Толщина слоя - 0,3-1,0 мм. Борирование придает поверхностному слою исключительно высокую твердость (до 1800-2000 HV), износостойкость и устойчивость против коррозии в различных средах.
Вопросы к теме 12. Способы упрочнения поверхности металлов. Химико-термическая обработка сталей.
1. Назовите способы упрочнения поверхностного слоя.
2. Какие процессы обеспечивают упрочнение поверхностного слоя?
3. На какой стадии изготовления производят упрочнение поверхностного слоя?
4. Охарактеризуйте дробеструйную обработку поверхности.
5. Охарактеризуйте обкатку роликами.
6. Охарактеризуйте поверхностную закалку ТВЧ.
7. Что представляет собой химико-термическая обработка?
8. Какие процессы ХТО вы знаете?
9. Охарактеризуйте процесс насыщения поверхностного слоя?
10. В чем отличие ХТО от поверхностной закалки?
11. Охарактеризуйте цементацию.
12. Какие виды цементации различают? Охарактеризуйте их.
13. Какие стали подвергают цементации? Какова структура цементированного слоя?
14. Охарактеризуйте азотирование.
15.Каковы достоинства и недостатки азотирования и цементации?
16. Охарактеризуйте цианирование.
17.Охарактеризуйте диффузионную металлизацию.
Вопросы к теме 12. Способы упрочнения поверхности металлов. Химико-термическая обработка сталей.
Назовите способы упрочнения поверхностного слоя.
Эффективными способами упрочнения поверхностного слоя являются дробеструйная обработка и обкатка поверхности роликами.
Дата добавления: 2018-04-05; просмотров: 667; Мы поможем в написании вашей работы! |
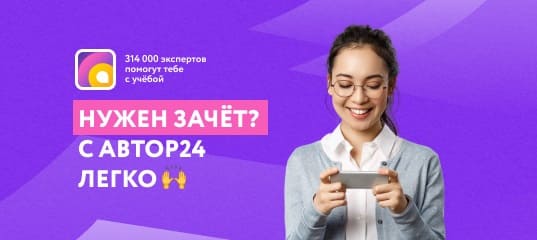
Мы поможем в написании ваших работ!