Прихватки стыков алюминиевых сплавов
Толщина элементов, Мм | Длина прихваток, мм | Расстояние между прихватками, мм |
2…8 | 20…35 | 100…200 |
10…20 | 40…80 | 200…300 |
25…30 | 70…120 | 300…400 |
При толщине элементов до 3 мм прихватки выполняют на всю толщину материала. При длинных соединениях прихватки расплагают от середины соединения к краям. Прихватки в стыковых, многослойных соединениях располагают со стороны, обратной сварке первого слоя шва и при сварке шва их следует удалить. Перед сваркой прихватки необходимо осмотреть, дефектные удалить и выполнить вновь, а затем очистить и обезжирить.
1.5 Сварка алюминия и его сплавов покрытыми электродами.
Сварку покрытыми электродами применяют в основном для малоответственных конструкций из-за невозможности получить шов близкий по механическим свойствам основному металлу. В качестве покрытий электродов применяют смеси из хлористых и фтористых солей. Толщина покрытия не более 0,3…0,5 мм. Для сварки алюминия и его сплавов используют электроды ОЗА-1, АФ-4А, ЭЮ-1, АФ4аКР. Электрод ОЗА-2 предназначен для заварки дефектов литья и наплавки.
Перед сваркой электроды просушивают при температуре 150-200°С в течении 2-х часов. Сварку указанными электродами производят постоянным током обратной полярности, короткой дугой без поперечных колебаний электрода. Возможно, выполнять сварку в вертикальном положении. Диаметр электрода подбирают в зависимости от толщины материала.
|
|
Таблица 2
Диаметр электрода
Толщина материала, мм | до 3 | 3…5 | 5…8 | 10 и более |
Диаметр электрода, мм | 3 | 4 | 5 | 6; 8; 10 |
Сварочный ток принимают (40-50)d электрода, напряжение дуги 30…36 А. Применяют предварительный подогрев при толщине 8-10 мм до 200-240°С, а при толщине 12-20 мм – до 300-350°С с целью снижения скорости охлаждения, удаления из шва водорода и уменьшения пористости шва. Сварку рекомендуется выполнять непрерывно в пределах одного электрода, так как плёнка шлака на кратере и конце электрода препятствует повторному зажиганию дуги.
1.6 Ручная и механизированная дуговая сварка в среде инертных газов получила наибольшее распространение при изготовлении сварных конструкций из легких сплавов. Сварку выполняют неплавящимся (вольфрамовым) и плавящимся электродами. Инертные газы – аргон 1-го и 2-го сортов, гелий повышенной чистоты и смесь аргона с гелием.
Сварка вольфрамовым электродом диаметром 2…6 мм целесообразна для металла толщиной до 12 мм. Присадочный металл выбирают в зависимости от марок сплава: для технического алюминия – проволоку марок АО, АД или АК,
для сплавов типа АМг – проволоку той же марки, нос увеличением (на 1,0 …1,5 %) содержанием магния для компенсации его угара. Диаметр присадочной проволоки 2…5 мм.
|
|
Ручную аргонодуговую сварку вольфрамовым электродом ведут на переменном токе, который хорошо разрушает и удаляет из металла оксидную плёнку, при расходе аргона 6…15 дм3/мин. Сварку можно выполнять и в гелии при его расходе в 1,8 – 2,2 раза выше расхода аргона (табл. 1). Напряжение дуги при сварке в аргоне составляет 15…20 В, при сварке в гелии – 25…30 В.
Режимы ручной дуговой сварки легких сплавов вольфрамовыми электродами в инертных газах Таблица 3
Толщина металла, мм | Диаметр, мм | Сила тока, А | ||
вольфрамового электрода | присадочной проволоки | в аргоне | в гелии | |
1…2 | 2 | 1…3 | 50…70 | 30…40 |
4…6 | 3 | 2…3 | 100…130 | 60…90 |
4…6 | 4 | 3 | 160…180 | 110…130 |
6…10 | 5 | 3…4 | 220…300 | 160…240 |
11…15 | 6 | 4 | 280…360 | 220…300 |
При толщине листов до 3 мм сварку можно вести за один проход на подкладках из металла с малой теплопроводностью (обычно из высоколегированной стали). Они также служат и для защиты обратной стороны шва. С этой точки зрения нахлесточные, угловые и тавровые соединения менее технологичны. Металл толщиной 4…6 мм можно сваривать без скоса кромок за два прохода с двух сторон. При толщине металла свыше 6 мм необходима V- образная разделка кромок и увеличение числа проходов; возможна также Х-образная разделка. Сварку вольфрамовым электродом довольно просто механизировать. Производительность сварки вольфрамовым электродом можно повысить в 3 - 5 раз, если использовать трехфазную дугу.
|
|
Число вольфрамовых включений в сварном соединении можно уменьшить путем повышения стойкости вольфрамового электрода. Благодаря высокой эмиссионной способности вольфрам с оксидом лантана (ВЛ) или оксидом иттрия (ВИ-20, ВИ-30, СВИ-1) более долговечен в эксплуатации. Для
уменьшения перегрева электрода нормируют продолжительность выполнения сварки. Следует избегать коротких замыканий электрода при сварке. Вольфрамовый электрод обладает наибольшей стойкостью при сварке на постоянном токе прямой полярности, меньшей – на переменном токе и минимальной – на постоянном токе обратной полярности. Оптимальный расход газа обеспечивает стабильный процесс горения дуги и эффективную защиту вольфрама от воздействия окружающего воздуха.
Сварка плавящимся электродом в защитных газах возможна в чистом аргоне, либо смеси аргона с гелием (до 70 % Не) на постоянном токе обратной
|
|
полярности проволокой диаметром 1,5 …2,5 мм. Разделка кромок V-образная и Х-образная с углом раскрытия 70…900, либо U-образная с углом раскрытия 300, притупление составляет 6 мм. Такое раскрытие кромок необходимо для размещения в разделке наконечника горелки. Угловые швы сваривают проволокой диаметром 1,5 …2,0 мм при силе сварочного тока 200…300 А, напряжении дуги 16…24 В и расходе аргона 15 л/мин.
Скорость сварки определяется сечением шва и может достигать 30…40 м/ч, скорость подачи проволоки – 400 м/ч. При использовании газовой смеси, содержащей 30 % Аr и 70 % Не, удается за один проход (на подкладке) сваривать металл толщиной до 16 мм, за два прохода – до 30 мм, так как при этом составе смеси увеличиваются и ширина, и глубина проплавления.
Для ручной и механизированной сварки применяют специализированные установки УДГ-301, УДГ-501.
Недостатком аргонодуговой сварки является возможность появления пористости швов из-за дефектов очистки и насыщения шва водородом. Для борьбы с водородом иногда применяют аргон с добавкой кислорода, который окисляет водород и этим уменьшает пористость.
1.8 Плазменная сварка алюминиевых сплавов. Плазменная сварка является перспективной. Она разработана с питанием током переменной полярности от двух объединённых источников питания постоянного тока, что позволило обеспечить качественную сварку алюминия толщиной 6 мм без разделки кромок. Для ручной плазменной сварки алюминия используют установку УСП-301, позволяющую сваривать металл толщиной 1-8 мм постоянным током обратной полярности.
После сварки алюминия и его сплавов любым способом необходимо немедленно очистить шов от шлаков и окислов для предупреждения коррозии металла.
Контрольные вопросы.
1.На какие категории делят деформируемые алюминиевые сплавы?
2. Почему затруднено визуальное наблюдение за процессом сварки алюминиевых сплавов?
3. Какова нормативная длительность хранения подготовленных материалов из алюминиевых сплавов перед сваркой (основных и сварочных)?
4. В каких соединениях при сборке конструкций под сварку прихватки ставят без присадочного материала?
5. Назначение электрода ОЗА-2.
6. Род тока и полярность при сварке алюминиевых сплавов плавящимся электродом в защитных газах.
7.Почему ручную аргонодуговую сварку вольфрамовым электродом ведут на переменном токе?
8. Какой металл выбирают для формирующих подкладок?
9. Как уменьшить число вольфрамовых включений в сварном соединении из алюминиевых сплавов?
10.Какие меры применяют для борьбы с водородом при сварке алюминиевых сплавов?
11.Какое требование необходимо выполнять незамедлительно после сварки алюминия и его сплавов любым способом сварки?
Лекция 2. СВАРКА ТИТАНА И ЕГО СПЛАВОВ.
План лекции.
1.Титан и его сплавы.
2.Подготовка титана и его сплавов к сварке.
3.Сварка титана.
Титан и его сплавы
Титан– распространённый в природе металл. В земной коре его больше, чем меди, свинца и цинка. Это тускло-серый металл с температурой плавления 16620 С. При плотности 4,51 г/см3 титан имеет прочность 267…337 МПа, а его сплавы – до 1250 МПа. Коррозионностоек при нормальной температуре и даже в сильно агрессивных средах, но очень активен при нагреве выше 4000 С. В кислороде способен к самовозгоранию. Бурно реагирует с азотом. Окисляется водяным паром, углекислым газом, поглощает водород. Теплопроводность титана более чем в два раза ниже, чем у углеродистой стали. Поэтому при сварке титана, несмотря на его высокую температуру плавления, требуется меньше тепла.
Титан может находиться в виде двух основных стабильных фаз, отличающихся строением кристаллической решётки. При нормальной температуре он существует в виде a -фазы с мелкозернистой структурой, не чувствительной к скорости охлаждения. При температуре выше 8820 С образуется b -фаза с крупным зерном и высокой чувствительностью к скорости охлаждения. Легирующие элементы и примеси могут стабилизировать a-фазу (алюминий, кислород, азот) или b-фазу (хром, марганец, ванадий). Поэтому сплавы титана условно разделяются на три группы: a, a+b и b сплавы. Первые (ВТ1, ВТ5-1) термически не упрочняются, пластичны, обладают хорошей свариваемостью. Вторые (ОТ4, ВТ3, ВТ4, ВТ6, ВТ8) при малых добавках b-стабилизаторов также свариваются хорошо. Они термически обрабатываются. Сплавы с b-структурой, например ВТ15, ВТ22, упрочняются термообработкой. Они свариваются хуже, склонны к росту зерна и к холодным трещинам.
При комнатной температуре поверхность титана растворяет кислород, образуется его твёрдый раствор в a-титане. Возникает слой насыщенного раствора, который предохраняет титан от дальнейшего окисления.
Этот слой называют альфированным. При нагреве титан вступает в химическое соединение с кислородом, образуя ряд окислов от Тi6O до TiO2. По мере окисления изменяется окраска оксидной плёнки от золотисто-жёлтой до тёмно-фиолетовой, переходящей в белую. По этим цветам в околошовной зоне можно судить о качестве защиты металла при сварке. При хорошей защите поверхность металла в зоне сварки имеет серебристый цвет. При недостаточной защите появляются цвета побежалости, а при плохой – серые и бурые налёты. С азотом титан, взаимодействуя активно при температуре более 5000 С, образуя нитриды, повышающие прочность, но резко снижающие пластичность металла. Все титановые сплавы не склонны к образованию горячих трещин, т.к. у них малая величина литейной усадки в сочетании с повышенной прочностью и пластичностью в области высоких температур. Но склонны к сильному укрупнению зерна в металле шва и около шовной зоне, что ухудшает свойства металла.
Растворимость водорода в жидком титане больше, чем у стали, но с понижением температуры она резко падает, водород выделяется из раствора. При затвердевании металла это может вызвать пористость и замедленное разрушение сварных швов после сварки. Часто встречается также образование холодных трещин, возникающих при пониженной пластичности вследствие насыщения металла газами, в первую очередь водородом, причём холодные трещины в таких соединениях могут образовываться при хранении сварных конструкций. С целью предупреждения пор при сварке титана и его сплавов используют различные способы, которые можно разделить на три группы:
1)уменьшение количества адсорбированной влаги на кромках свариваемых деталей и поверхности сварочной проволоки, а также создание условий для удаления влаги из зоны сварки до формирования сварочной ванны,
2)использование режимов сварки, обеспечивающих наиболее полное удаление водорода из сварочной ванны,
3)связывание и интенсификация выделение водорода из сварочной ванны с использованием флюсов.
Снижение количества влаги достигается за счёт повышения чистоты обработки, а также регламентации условий и срока хранения подготовленных к сварке деталей.
4.2 Подготовка титана и его сплавов к сварке и сборка деталей должны производиться особенно тщательно. Основной металл и сварочная проволока должны быть очищены от загрязнений, и иметь чистую, без альфированного слоя и окалины поверхность. При необходимости очищают металл дробеструйной обработкой, механическим способом, травлением и обезжириванием.
Сварочную проволоку диаметром 1,2…7 мм обычно поставляют после отжига при температуре 900-10000 С в течении 4 часов для удаления водорода. Резка металла возможна обычными ножницами и плазменными резаками. При кислородной резке окисленные кромки удаляют механическим путём. Проволоку для режут на куски длиной 300-400 мм.
При толщине металла более 3 мм делают разделку кромок под углом 60-700. Детали собирают под сварку с помощью прижимных или других приспособлений. Возможна сварка на прихватках, при этом детали из легированных сплавов титана прихватывают с применением присадочной проволоки, а детали из технически нелегированного титана – без присадки. Прихватки должны быть длиной 30-50 мм с расстоянием между ними 300 мм. Прихватки выполняют со стороны обратной шву, и обязательно с защитой металла инертными газами с помощью местных или общих камер. В начале и конце стыка прихватывают специальные планки из основного металла, на которых начинают и заканчивают шов. Детали толщиной от 0,5 до 3 мм собирают без зазора.
4.3 Сварка титана покрытыми электродами не обеспечивает требуемых качеств сварного соединения и не применяется. Применяют ручную дуговую сварку вольфрамовыми электродами в аргоне, гелии или их смеси. Обычная защита, применяемая при сварке горелкой с обдувом защитным газом электрода, зоны дуги и ванны, также недостаточна, так как металл реагирует с кислородом уже при нагреве до 4500 С и выше. Для полной защиты при сварке титана и его сплавов неплавящимся электродом применяют защитные камеры нескольких типов. При сварке на воздухе в цехе или на монтажной площадке применяют камеры-насадки.
Для местной защиты зоны сварки и нагретого сварного соединения. При местной защите обратная сторона шва может быть защищена специальной подкладкой с канавкой, куда подают защитный газ.
При сварке трубопроводов применяют поддув защитного газа внутрь трубы.
Для общей защиты свариваемой детали применяют жёсткие и полумягкие герметичные камеры, куда помещают деталь и горелку и наполняют инертным газом под небольшим давлением. Сварщик манипулирует горелкой с помощью гибких или жёстких механических рук и наблюдает процесс сварки через иллюминаторы или через прозрачную оболочку. Для крупных и ответственных деталей применяют обитаемые камеры (рис.4) объёмом до 350 м3, в которых устанавливают сварочные автоматы и манипуляторы. Камеры вакуумируются, затем заполняются аргоном, через шлюзы в них входят сварщики в скафандрах.
Сварку неплавящимся электродом выполняют на постоянном токе прямой полярности. Для повышения стабильности процесса используют лантанированные вольфрамовые электроды.
Сварку плавящимся электродом выполняют на постоянномтоке обратной полярности на режимах обеспечивающих мелкокапельный перенос металла.
Для сварки под флюсом применяют бескислородные фтористые флюсы сухой грануляции серии АНТ. Марку флюса выбирают в зависимости от толщины свариваемого металла. Для толщины 2,5…8,0 мм флюс марки АНТ1 АНТ3, для более толстого материала – АНТ7. Сварку ведут электродной проволокой диаметром 2,0…5,0 мм с вылетом электрода 14...22 мм на медной или флюсовомедной прокладке, либо на флюсовой подушке. Структура металла в результате модифицирующего действия флюса получается более мелкозернистой, чем при сварке в инертных газах.
При электрошлаковой сварке используют пластинчатые электроды из того же титанового сплава, что и свариваемая деталь, толщиной 8…12 мм и шириной, равной толщине свариваемого металла. Используют тугоплавкие фторидные флюсы АНТ2, АНТ4, АНТ6. Чтобы через флюс не проникал кислород, шлаковую ванну дополнительно защищают аргоном. Металл зоны термического влияния защищают, увеличивая ширину формирующих водоохлаждаемых ползунов и продувая в зазор между ними и деталью аргон.. сварные соединения после электрошлаковой сварки имеют крупнокристаллическую структуру. Но свойства их близки к основному металлу. Перед электрошлаковой сваркой, так же как и перед дуговой, флюсы должны быть прокалены при температуре 200…3000 С.
Электронно-лучевая сварка титановых сплавов обеспечивает наилучшую защиту металла от газов и мелкозернистую структуру шва. Требования к сборке по сравнению с другими способами жестче.
При всех способах сварки титановых сплавов нельзя допускать перегрева металла. Нужно применять способы и приёмы, позволяющие получить мелкозернистую структуру шва и высокие свойства сварного соединения.
Контрольные вопросы.
Дата добавления: 2018-04-05; просмотров: 2954; Мы поможем в написании вашей работы! |
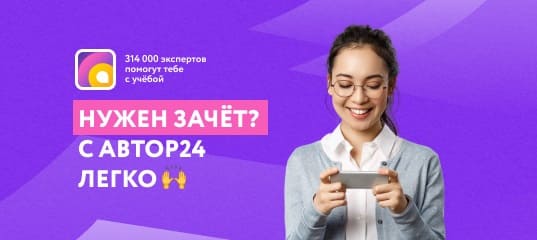
Мы поможем в написании ваших работ!