Порядок выполнения работ по монтажу днища
Билет №18
Фрезерная обработка деталей. Основные параметры обработки, режущий инструмент. Оборудование, приспособления.
Фрезерование — один из высокопроизводительных и распространенных методов обработки поверхностей заготовок многолезвийным режущим инструментом — фрезой.
Технологический метод формообразования поверхностей фрезерованием характеризуется главным вращательным движением инструмента и обычно поступательным движением подачи. Подачей может быть и вращательное движение заготовки вокруг оси вращающегося стола или барабана (карусельно-фрезерные и барабанно-фрезерные станки).
На фрезерных станках обрабатывают горизонтальные, вертикальные и наклонные плоскости, фасонные поверхности, уступы и пазы различного профиля. Особенность процесса фрезерования — прерывистость резания каждым зубом фрезы. Зуб фрезы находится в контакте с заготовкой и выполняет работу резания только на некоторой части оборота, а затем продолжает движение, не касаясь заготовки, до следующего врезания. На рисунке 1 показаны схемы фрезерования плоскости цилиндрической (а)и торцовой (б)фрезами. При цилиндрическом фрезеровании плоскостей работу выполняют зубья, расположенные на цилиндрической поверхности фрезы. При торцовом фрезеровании плоскостей в работе участвуют зубья, расположенные на цилиндрической и торцовой поверхностях фрезы.
1 — заготовка; 2 — фреза
|
|
Рисунок 1 – Схемы фрезерования цилиндрической (а)и торцовой (б) фрезами, против подачи (б) и по подаче (г):
Цилиндрическое и торцовое фрезерование в зависимости от направления вращения фрезы и направления подачи заготовки можно осуществлять двумя способами[1]:
1) против подачи (встречное фрезерование), когда направление подачи противоположно направлению вращения фрезы (рисунок 1, е);
2) по подаче (попутное фрезерование), когда направления подачи и вращения фрезы совпадают (рисунок 1, г).
При фрезеровании против подачи нагрузка на зуб фрезы возрастает от нуля до максимума, при этом сила, действующая на заготовку, стремится оторвать ее от стола, что приводит к вибрациям и увеличению шероховатости обработанной поверхности. Преимуществом фрезерования против подачи является работа зубьев фрезы «из-под корки», т. е. фреза подходит к твердому поверхностному слою снизу и отрывает стружку при подходе к точке В. Недостатком является наличие начального скольжения зуба по наклепанной поверхности, образованной предыдущим зубом, что вызывает повышенный износ фрезы.
При фрезеровании по подаче зуб фрезы сразу начинает срезать слой максимальной толщины и подвергается максимальной нагрузке. Это исключает начальное проскальзывание зуба, уменьшает износ фрезы и шероховатость обработанной поверхности. Сила, действующая на заготовку, прижимает ее к столу станка, что уменьшает вибрации.
|
|
2 Режимы и силы резания
К режиму резания при фрезеровании относят скорость резания v, подачу s, глубину резания t, ширину фрезерования В.
Скорость резания,т. е. окружная скорость вращения фрезы, м/мин,
v= πDn/1000 , (1)
где D — диаметр фрезы, мм; п — частота вращения фрезы, об/мин.
Подача — величина перемещения обрабатываемой заготовки в минуту (SM, мм/мин) за время углового поворота фрезы на один зуб (SZ, мм/зуб) или за время одного оборота фрезы (S0, мм/об).
Эти подачи связаны между собой зависимостями;
Sм = S0n = Szzn, (2)
где z — число зубьев фрезы. Глубина резания t (мм) и ширина фрезерования В (мм) показаны на рисунке 1.
В процессе фрезерования каждый зуб фрезы преодолевает силу сопротивления металла резанию. Фреза должна преодолеть суммарные силы резания, которые складываются из сил, действующих на зубья, находящиеся в контакте с заготовкой. При фрезеровании цилиндрической фрезой с прямыми зубьями равнодействующую сил резания R, приложенную к фрезе в некоторой точке A, можно разложить на окружную составляющую силу Р, касательную к траектории движения точки режущей кромки, и радиальную составляющую силу Ру, направленную по радиусу. Силу R можно. также разложить на горизонтальную Рн и вертикальную Рv составляющие (рисунок 2, а). У фрез с винтовыми зубьями в осевом направлении действует еще осевая сила Р0 (рисунок 2, б). Чем больше угол наклона винтовых канавок ω, тем больше сила Р0. При больших значениях силы Р0 применяют две фрезы с разными направлениями наклона зубьев. В этом случае осевые силы направлены в разные стороны и взаимно уравновешиваются [1].
|
|
Рисунок 2 – Силы резания при работе цилиндрической фрезой
По окружной составляющей силе Р определяют эффективную мощность Nв и производят расчет механизма коробки скоростей на прочность. Радиальная составляющая сила Ру действует на опоры шпинделя станка и изгибает оправку, на которой крепят фрезу. Горизонтальная составляющая сила Рн действует на механизм подачи станка и элементы крепления заготовки; осевая сила Р0 — на подшипники шпинделя станка и механизм поперечной подачи стола; вертикальная составляющая сила Рv, — на механизм вертикальной подачи стола. В зависимости от способа фрезерования (против подачи или по подаче) направление и величина сил изменяются.
|
|
Сила резания, Н
, (3)
где — постоянный коэффициент, зависящий от свойств обрабатываемого материала, типа фрезы и ее геометрии;
,
и
— показатели степени, также зависящие от механических характеристик обрабатываемого материала, типа и геометрии фрезы. Значения
,
,
и
приводятся в справочниках по выбору параметров режимов резания.
Зная крутящий момент фрезы и частоту ее вращения, можно определить мощность
, (4)
В целях обеспечения эффективной мощности на шпинделе необходимо, чтобы электродвигатель станка обладал большей мощностью, так как часть ее расходуется на трение в подшипниках, зубчатых передачах, направляющих и др.
Потери на трение характеризуются коэффициентом полезного действия станка . Для фрезерных станков общего назначения
. Таким образом, на полезную работу, т.е. на работу фрезерования расходуется 75—85 % мощности электродвигателя.
Для определения эффективной мощности , которую можно использовать на резание, следует мощность электродвигателя
умножить на КПД станка, т. е.
. (5)
Для расчета потребной мощности электродвигателя станка по эффективной мощности необходимо эффективную мощность
разделить на КПД станка, т. е.
. (6)
3 Типы фрез
В зависимости от назначения и вида обрабатываемых поверхностей различают следующие типы фрез: цилиндрические (рисунок 3, а), торцовые (рисунок 3, б, з), дисковые (рисунок 3, в), концевые (рисунок 3, г), угловые (рисунок 3, д), шпоночные (рисунок 3, е), фасонные (рисунок 3, ж).
Фрезы изготовляют цельными (рисунок 3, б—ж) или сборными (рисунок 3, а, з). Режущие кромки могут быть прямыми (рисунок 3, д)или винтовыми (рисунок 3, а). Фрезы имеют остроконечную (рисунок 3, и)или затылованную (рисунок 3, к)форму зуба. У фрез с остроконечными зубьями передняя и задняя поверхности плоские. У фрез с затылованными зубьями передняя поверхность плоская, а задняя выполнена по спирали Архимеда; при переточке по передней поверхности профиль зуба фрезы сохраняется.
Цельные фрезы изготовляют из инструментальных сталей. У сборных фрез зубья (ножи) выполняют из быстрорежущих сталей или оснащают пластинками из твердых сплавов и закрепляют в корпусе фрезы пайкой или механически.
Рисунок 3 – Типы фрез
На рисунке 4, а показана цилиндрическая фреза с винтовыми зубьями. Она состоит из корпуса 1 и режущих зубьев 2. Зуб фрезы имеет следующие элементы: переднюю поверхность 3, заднюю поверхность 6, спинку зуба 7, ленточку 5 и режущую кромку 4.
D — диаметр фрезы; L — ширина фрезы
Рисунок 4 –Элементы и геометрия фрезы
У цилиндрических фрез различают передний угол γ, измеренный в плоскости А—A, перпендикулярной к главной режущей кромке; главный задний угол α, измеренный в плоскости, перпендикулярной к оси фрезы; угол наклона зубьев ω. Передний угол γ облегчает образование и сход стружки. Главный задний угол α обеспечивает благоприятные условия перемещения задней поверхности зуба относительно поверхности резания и уменьшает трение на этих поверхностях. Угол наклона зубьев со обеспечивает более спокойные условия резания по сравнению с прямым зубом и придает направление сходящей стружке.
У зуба торцовой фрезы (рисунок 4, б)режущая кромка имеет более сложную форму. Она состоит из главной режущей кромки 8, переходной кромки 9 и вспомогательной кромки 10. Зуб торцовой фрезы имеет главный угол в плане φ1 и вспомогательный угол в плане. Чем меньше угол φ1, тем меньше шероховатость обработанной поверхности.
2. Электрический привод буровых установок. Электродвигатели постоянного тока. Достоинства и недостатки.
3. Ленточный тормоз лебёдок подъемных агрегатов. Устройство, принцип действия, неисправности в процессе работы
4. Последовательность проведения работ при монтаже стальных резервуаров
Вертикальные стальные резервуары объёмом до 10 000 м «Правилами безопасности в нефтяной и газовой промышленности» разрешается монтировать из заводских рулонных заготовок. Плоские сварные полотнища резервуаров изготавливаются на заводах на специальных двухярусных стендах с одновременным контролем сварных швов. По мере готовности полотнищ их сворачивают в рулон на шахтной лестнице или на специальных каркасах. Количество рулонов определяется объёмом резервуара.
В частности резервуар РВС-5000 объёмом 5000м имеет следующую техническую характеристику:
- диаметр 20,92 метра
- высота корпуса 14,9 метра
- вес днища 14,4 кН
- вес стенки 470 кН
- вес покрытия (кровли) 190 кН
- максимальная высота налива 14,37 метра
Резервуар поставляется на монтажную площадку в следующем виде: днище и стенка – полотнищами, свернутыми в рулон, остальные металлические конструкции – сварными в соответствии с транспортабельными габаритами.
Рисунок 48 - Вертикальный стальной резервуар
Общая технологическая схема монтажа резервуара заключается в выполнениии следующих основных операций:
1. монтаж днища;
2. монтаж стенки;
2.1. подъём рулона стенки в вертикальное положение;
2.2. установка монтажной стойки;
2.3. развёртывание и испытание стенки;
2.4. по мере развёртывание стенки установка щитов покрытия;
2.5. формообразование, замыкание и сварка вертикального монтажного стыка;
3. демонтаж монтажной стойки.
Резервуар монтируют на основании, верхняя часть которого состоит из песка толщиною 80…100 мм. Для защиты днища резервуара от воздействия грунтовых вод, поверхность основания, сопрягающаяся с днищем утрамбовывается катками и покрывается смесью песка с вяжущим веществом (мазут, жидкий битум). Разность высотных отметок основания не должно превышать: диаметрально противоположных точек +/- 5 см, по периметру на расстоянии 6 метров +/- 2 см.
Порядок выполнения работ по монтажу днища.
Перед основанием устраивается пандус для закатывания рулона днища на основание. Затем производится строповка рулона и рулон накатывается на основание положение 1. При этом начальный участок полотнища должен быть прижат к днищу рулона. Затем развёртывается полотнище 1. Срезание стопорных планок следует производить по мере развёртывания полотнища при натянутых канатах приспособления для разворачивания. После чего рулон перекатывается в положение 4. На развёрнутом полотнище наносят две параллельные риски, обеспечивающих правильность стыковки полотнищ. Для удобства укладки полотнища 2 на полотнище 1 приваривают уголки ограничители нахлёста. После разворачивания полотнища 2 оно укладывается в проектное положение и производится сварка стыка. Затем производится разметка днища для установки по центру монтажной стойки, приварки ограничительных уголков по периметру и контроля вертикальности стенки.
Рисунок 48
Дата добавления: 2018-04-04; просмотров: 220; Мы поможем в написании вашей работы! |
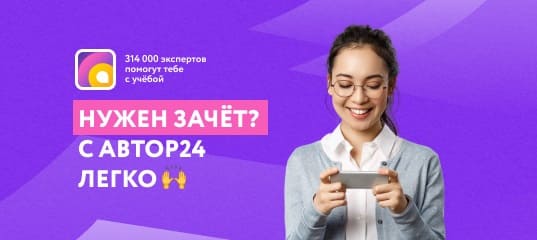
Мы поможем в написании ваших работ!