Контроль собранной передачи«на краску» (по пятну контакта)
1. Наносим на поверхность зубьев ведущего колеса тонкий слой краски.
2. Проворачиваем несколько раз собранную передачу.
3. Делаем вывод о качестве сборки передачи по характеру расположения пятен контакта на ведомом зубчатом колесе (рис. 4).
Рисунок 4 — Контроль параллельности и межцентрового расстояния
прямозубых цилиндрических колес по расположению пятна контакта
а — все правильно | б — перекос осей |
в — увеличенный радиальный зазор | г — недостаточный радиальный зазор |
H, В — высота и длина зуба | А,hср — длина и высота пятна контакта |
С — расстояние между пятнами контакта |
Контроль бокового зазора
1. Стопорим ведущее колесо, а ведомое колесо поворачиваем на максимально возможный угол, который соответствует величине бокового зазора.
2. Измеряем щупом расстояние между боковыми поверхностями зубьев зубчатых колес (боковой зазор) и сравниваем полученные данные с требованиями технических условий на сборку.
3. Установливаем между зубьями колес свинцовую проволочку, диаметр которой должен быть немного больше величины бокового зазора, и проворачиваем передачу. Измеряем толщину проволочки после ее деформирования и сравните полученный результат с требованиями технических условий на сборку.
Зубчатые передачи могут быть цилиндрическими, коническими и червячными.
Сборка цилиндрических зубчатых передач
Сборка зубчатых цилиндрических передач включает посадку зубчатых колес на валы, установку валов с колесами в корпусе, регулирование зацепления зубчатых колес. Посадка обычно производится с небольшим натягом на центрирующие поверхности под прессом, с применением специальных приспособлений, которые должны обеспечивать правильное направление напрессовываемого зубчатого колеса и тем самым устранить его перекосы.
|
|
Напрессовывание вручную применяется в условиях мелкосерийного и единичного производства, и то только для колес малых диаметров, как правило, термически не обрабатываемых и устанавливаемых с небольшими натягами.
Сборка также может производиться с нагревом и охлаждением.
Поле установки колесо проверяется на качку при легком обстукивании колеса мягким молотком. Плотность прилегания к упорному буртику обычно контролируется с помощью щупа.
В единичном и серийном производствах контроль радиального биения колес производиться на контрольном приспособлении с базированием опорных шеек вала на призмах.
Между зубьями колеса закладываются цилиндрические калибры и при повороте вала фиксируются показания прибора. Разница в показаниях прибора характеризует радиальное биение начальной окружности. При отклонении больше допустимого производят распрессовку, колесо снимают и вновь напрессовывают, повернув предварительно на некоторый угол.
|
|
В крупносерийном и массовом производствах контроль производится на автоматизированном приспособлении с эталонным колесом. При вращении неточные зацепления вызывают перемещение эталонного колеса, которые отмечаются цифровыми показывающими приборами. Одновременно с проверкой радиального биения можно контролировать и торцевое биение.
Зазоры в зацеплении проверяются щупом, а при большом модуле – путем прокатывания между зубьями свинцовых проволочек с последующим измерением толщины сплющенных проволочек.
При большой длине зубьев таких проволочек устанавливается несколько, 3 – 4 проволочки по длине зуба. По их сплющиванию судят о равномерности зазора по длине. Качество зацепления зубчатых передач может проверяться на краску. При вращении меньшего колеса, покрытого тонким слоем краски, на парном большем колесе пятна краски должны покрыть среднюю часть боковой поверхности зубьев.
Дата добавления: 2018-04-05; просмотров: 476; Мы поможем в написании вашей работы! |
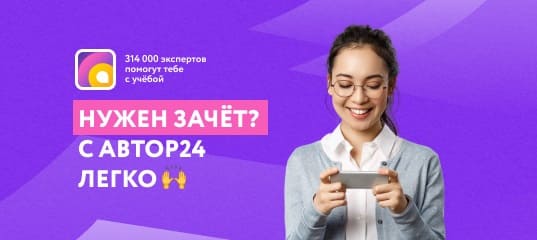
Мы поможем в написании ваших работ!