Тарировка тензометрических измерителей силовых параметров
Для того чтобыиметь возможность по показаниям микроамперметра μА определять величину силы или крутящего момента, проводится экспериментальная тарировка системы измерения. На рис. 19, б) приведена структурная схема установки для тарировки системы измерения силы.
Для выполнения тарировки силоизмерительный датчик 2 с наклеенными тензометрическими преобразователями устанавливают в нагружающее устройство 1 так, чтобы при подвешивании тарировочных гирь 4 на подвес 3, упор нагружающего устройства воздействовал на датчик 2 с силой Fд. Допустим, что измерительная система должна обеспечивать измерение силы, в диапазоне от Fmin= 0H, до Fmах= 600H. Необходимо определить абсолютную ΔF и относительную d погрешности измерения системы.
Для решения поставленной задачи будем дискретно нагружать измерительный датчик 2 силой Fд, поочередно подвешивая тарировочные гири 4 на подвес 3. Учитывая плечи рычагов, усилие Fд на датчике будет равно:
(2.6)
где Fгр – вес тарировочных гирь.
а) б)
Рис. 19. Тарировочный график и структурная схема установки для тарировки системы измерения силы
В процессе нагружения значения силы Fд и показания Iис измерительного микроамперметра μА будем заносить в таблицу 2.1.
|
|
После окончания нагружения тарировка продолжается в режиме разгружения датчика. При этом последовательно убирают тарировочные гири и заносят полученные результаты в ту же таблицу 2.1.
Таблица 2.1.
Режимнагружениядатчика | |||||||
Усилие на датчике Fд , [H] | 0 | 100 | 200 | 300 | 400 | 500 | 600 |
Показания микроамперметра, Iис [μА] | 0 | 5 | 10 | 15 | 20 | 25 | 30 |
Режим разгружения датчика | |||||||
Усилие на датчике Fд , [H] | 0 | 100 | 200 | 300 | 400 | 500 | 600 |
Показания микроамперметра, Iис [μА] | 0,11 | 6,2 | 11,9 | 16,7 | 21,2 | 26 | 30 |
После полного разгружения датчика строят тарировочный график (см. рис. 19, а). Полученный вид графика в виде петли носит название – петля гистерезиса. Её наличие объясняется трением между элементами измерительной системы. Чем больше трение, тем больше площадь петли гистерезиса, а, следовательно, и погрешность измерений.
Используя результаты тарировки, определяют коэффициент К преобразования измерительной системы:
,
(2.7)
Для приведенного выше примера тарировки коэффициент преобразования имеет значение: = 20
.
Далее определяют погрешности измерения. Так абсолютная погрешность измерения ΔF системы измерения силы может быть определена как максимальное значение разности:
|
|
(2.8)
где Iнагр - показания прибора в режиме нагружения датчика, Iразгр - показания прибора в режиме разгружения датчика. При этом оба показания Iнагр и Iразгр берутся при одинаковых значениях нагрузки на измерительный датчик.
Для приведенного выше примера тарировки максимальное значение абсолютной погрешности наблюдается при нагрузке на датчик 200 Н (см. таблицу 2.1). Его величина равна:
×20 = 1,9×20 = 38 Н.
Относительная погрешностьd измерения силы определяется исходя из выражения:
(2.9)
Для приведенного выше примера тарировки относительная погрешность измерения имеет значение: = 6,3%
Тарировка тензометрических измерителей крутящего момента выполняется аналогично, по вышеприведенной методике. Для этого собирают установку, внешний вид которой представлен на рис. 20. Устанавливают в неё тензометрический вал 1, с наклеенными на него тензометрическими преобразователями. Один конец тензовала 1 жестко закрепляется в точке 3. С противоположного конца к тензовалу прикрепляют тарировочный рычаг 2 с подвесом 4. В процессе тарировки на подвес 4 крепят тарировочные грузы 5, имеющие эталонные массы.
|
|
Рис. 20. Установка для тарировки тензометрического вала
В процессе тарировки дискретно нагружают тензовал 1 крутящим моментом Мкр, поочередно подвешивая тарировочные гири 5 на подвес 4. Учитывая плечо L рычага 2, крутящий момент Мкр, будет равен:
Мкр = Fгр × L (2.10)
В ходе последовательного нагружения, а затем и разгружения тензовала все значения крутящего момента Мкр и показания измерительного микроамперметра Iис заносят в таблицу, аналогичную таблице 1.1.
Используя результаты тарировки, строят график зависимости тока измерительной системы Iисот величины приложенного к тензовалу крутящего момента Мкр (аналогичный, представленному на рис. 20, а). Затем определяют коэффициент К преобразования измерительной системы по формуле:
,
(2.11)
Далее определяют погрешности измерения. Абсолютная погрешность измерения системы крутящего момента ΔМ определяется по формуле:
, [Н×м]. (2.12)
Оба показания Iнагр и Iразгр берутся при одинаковых значениях крутящего момента на тензовалу, при максимальном модуле разности (Iнагр - Iразгр).
|
|
И в заключении определяется относительная погрешность системы измерения крутящего момента - по формуле:
(2.13)
Измерение давления
Измерение давления газа и жидкости в агрегатах и системах автомобиля осуществляется, как правило, при помощи измерительных систем, состоящих из первичных преобразователей – датчиков, а также усилителей сигналов датчиков (электронных усилителей).
Первичные преобразователи – датчики преобразующие изменение давления рабочего тела в изменение сопротивления. Датчики давления обычно бывают тензометрического или реохордного типа. Несколько реже встречаются датчики давления емкостного типа. На рис. 21 приведены функциональные схемы датчиков реохордного и тензометрического типа.
Датчик давления реохордного типа (рис. 21, а) состоит из корпуса 1, внутри которого расположена диафрагма 2, соединенная штоком 3 с реохордом 6. Датчик давления реохордного типа работает следующим образом. При подаче на вход датчика рабочего тела, его давление Рw воздействует на диафрагму 2, посредством чего она прогибается и через шток 3 передвигает подвижный контакт реохорда 6 изменяя его сопротивление. В результате в любой момент времени сопротивление реохорда прямо пропорционально величине давления рабочего тела Рw.
Датчик давления тензометрического типа (рис. 21, б) состоит из корпуса 1, внутри которого расположена диафрагма 2, соединенная штоком 3 с тензометрической балкой 4. На тензометрической балке 4 наклеены и соединены по мостовой схеме тензометрические датчики 5.
Датчик давления тензометрического типа работает следующим образом. При подаче на вход датчика рабочего тела, его давление Рw воздействует на диафрагму 2, посредством чего она прогибается и через шток 3 изгибает тензобалку 4 изменяя сопротивление тензометрического моста.
а) б)
Рис. 21. Структурные схемы датчиков давления:
а) – реохордного; б) – тензометрического; 1 – корпус датчика, 2 – диафрагма, 3 – соединительный шток, 4 – тензометрическая балка, 5 – тензометрические датчики, 6 – реохорд
Тензометрический мост запитан от стабилизированного источника тока. В результате в любой момент времени ток разбаланса тензометрического моста прямо пропорционален величине давления рабочего тела Рw.
В качестве примера рассмотрим устройство промышленных датчиков давления, модели КАРАТ-ДИ–13/16–УХЛ31–0,5–1МПа–05В–IP54Р с диапазоном измерения давления от 0 до 1,0 МПа.
Датчик давления КАРАТ-ДИ предназначен для работы в системах измерений, контроля, регулирования и управления технологическими процессами. Он обеспечивают непрерывное преобразование избыточного давления, а при смещении настройки датчика, преобразование избыточного давления-разрежения жидких и газообразных сред в нормированный выходной сигнал постоянного напряжения. Датчик работает от постоянного тока, напряжением Uп=12÷24 В.
Технические характеристики датчика давления КАРАТ-ДИ:
1. Диапазон измерения давления .......................................................0÷1,0 МПа
2. Допустимая перегрузка подавлению ……………………..…………1,5 МПа
3. Выходной сигнал…………………………………………………..........0÷5 В
4. Относительная погрешность ………......................................................0,5%
5. Напряжение питания ……………………………………………..…… ±12 В
6. Сопротивление нагрузки Rн на выходе датчика …… Rн ≤ (Un-12)/0,02 [Ом]
7. Климатическое исполнение ……………………………………...… УХЛ3,1
8. Диапазон рабочих температур окружающей среды ………..... .(+5 ÷ +50)°С
В корпусе датчика КАРАТ – ДИ встроена схема усиления и преобразователя сигнала, (рис. 22).
Рис. 22. Схема преобразователя сигнала датчика КАРАТ – ДИ
Uп «+», Uп «-» – напряжение внешнего (первичного) питания схемы; Uc, Ic, Fc – сигнал напряжения, токовый и частотный, соответственно; «+Uвп», «-Uвп» – напряжение вторичного питания элементов схемы; Uоп– опорное напряжение; ВИП – вторичный источник питания; ТМ – тензомост; ДУ – дифференциальный инструментальный усилитель; ПНТ и ПНЧ – преобразователи напряжения в ток и частоту, соответственно; ТКН, ТКЧ – цепи термокомпенсации «нуля» и «чувствительности» (диапазона), соответственно; Лин – цепь линеаризации; Rд – резисторкорректор диапазона; Rо – резистор корректор «нуля»; ПД – узел переключения диапазонов; УСН – узел смещения нуля.
Напряжение на выходе датчика КАРАТ-ДИ прямо пропорционально величине давления рабочего тела Рw на его входе.
Измерение интервалов времени
Измерение интервалов времени осуществляется цифровой электроникой. Основу любого электронного секундомера составляет генератор опорных частот ГОЧ, который выполняет функцию электронного маятника. В состав ГОЧ входит электрический колебательный контур (рис. 23), включающий
![]() | конденсатор С и катушку индуктивности L, к которым подведено напряжение ±U. Известно, что при этом пластины конденсатора быстро заряжаются. Затем они начинают периодически перезаряжаться через катушку L, меняя заряд конденсатора так, что напряжение на них будет изменяться по закону синуса. |
Период Т собственных незатухающих колебаний в контуре определяется по формуле Томсона:
, [c] (2.14)
Частота собственных колебаний контура будет равна:
, [Гц] (2.15)
Таким образом, частота, с которой будет меняться напряжение ±U на пластинах конденсатора, зависит от его емкости С и величины индуктивности катушки L. Для того чтобы повысить стабильность частоты собственных колебаний контура, сделать её не зависимой от внешних факторов, параллельно колебательному контуру включают кристалл кварца К. Его подбирают так,
![]() | чтобы собственная частота колебаний электронов в кристаллической решетке кварца совпадала с частотой собственных колебаний контура (рис. 24). Как известно, при этом наступает явление резонанса, т.е. резкое возрастание амплитуды колебаний силы тока в колебательном контуре, а |
вместе с ним происходит и стабилизация частоты n колебаний контура.
Теперь познакомимся с работой электронного секундомера, типовая схема которого представлена на рис. 25. Как уже было отмечено выше основой «маятником» электронного секундомера является генератор опорных частот ГОЧ, содержащий кварцевый резонатор с колебательным контуром и кристаллом кварца К. Генератор опорных частот ГОЧ за одну секунду вырабатывает на своем выходе (точка А) 10000 стабильных по времени импульсов. Или другими словами, на своем выходе ГОЧ вырабатывает электрические импульсы с частотой 10000 Гц.
Рис. 25. Функциональная схема электронного секундомера
В состав электронного секундомера входят делительные декады ДД1 – ДД4. Принцип их работы заключается в том, что они циклически считают поступающие на вход импульсы до десяти, и каждый десятый импульс счетная декада отправляет на свой выход. Поэтому, если на вход первой делительной декады ДД1 (в точке А) поступает 10000 импульсов в секунду, то на её выход (в точку Б) отправляется в секунду уже 1000 этих импульсов.
Таким образом, каждая делительная декада делит входящую в неё последовательность электрических импульсов на десять, образуя на выходе второй делительной декады ДД2 (в точке В) частоту следования импульсов 100 Гц, на выходе третьей делительной декады ДД3 (в точке Г) – 10 Гц, и на выходе четвертой делительной декады ДД4 (в точке Д) – 1 Гц.
Еще одним важным элементом любого электронного секундомера являются счетные декады. В нашем примере (рис. 25) их четыре: СчД-1 ¸ СчД-4. Каждая счетная декада имеет вход, на который подаются электрические импульсы, выход, для каждого десятого электрического импульса, а также вход для обнуления счетной декады (показан кружочками в центре каждой счетной декады).
Эти декады соединены последовательно, справа налево, так, что выход каждой предыдущей счетной декады соединен со сходом следующей счетной декады. От делительных декад ДД счетные декады СчД отличаются тем, что они имеют дисплеи, на которых отображается результат счета поступивших в декаду импульсов от 0 до 9. Каждый десятый импульс СчД передается соседней (стоящей слева) счетной декаде, а эта СчД обнуляется и продолжает счет.
Для выполнения измерений интервалов времени необходимо выбрать нужную точность измерения, нажав на одну из кнопок Кн. «1000 Гц» ¸ Кн. «1 Гц» и одновременно нажать на кнопку «Замер». Электрические импульсы начнут поступать от делителей ДД на вход счетных декад СчД.
Для измерения интервалов времени с точностью до 0,001 секунды необходимо нажать кнопку «1000 Гц». В этом случае на интервале времени равном 1 секунде на вход счетных декад поступит ровно одна тысяча импульсов, которая отобразится на дисплеях СчД.
Например, при включенной кнопке «1000 Гц» на дисплее счетных декад отображено число 3782. Это означает, что измеренный интервал времени составляет Т = 3,782 секунды. Если при включенной кнопке «100 Гц» на дисплее счетных декад отображено число 5293. Это означает, что измеренный интервал времени составляет Т = 52,93 секунды.
Абсолютная погрешность измерения интервалов времени зависит от того, какую частоту n импульсов вырабатывает на своем выходе генератор опорных частот ГОЧ и сколько в измеренном интервале времени секунд. В нашем примере, абсолютная погрешность измерения интервала времени равна:
Δt × T = ± = ±0,0001× N с. (2.16)
где T – количество секунд в измеренном интервале времени
Из выражения (2.16) видно, что чем больше тактовая частота n генератора ГОЧ, тем точнее измерение интервала времени.
Относительную погрешность измерения интервала времени Т, [c] определим из формулы:
(2.17)
Обнуление результата измерения осуществляется нажатием кнопки «Сброс». При этом первый же импульс, поданный на вход для обнуления счетной декады (показан кружочками в центре каждой счетной декады), обнулит дисплеи всех счетных декад, подготовив их тем самым для проведения повторных измерений временных интервалов.
ИЗМЕРЕНИЕ СКОРОСТИ ВРАЩЕНИЯ
Измерение скорости вращения валов, шестерен, колес и других элементов, осуществляется, как правило, при помощи электронных тахометров. Типовая схема электронного тахометра приведена на рис. 26.
Тахометры измеряют скорость вращения n с размерностью [обороты/мин]. Уже первый взгляд на эту размерность позволяет понять, что тахометр должен выполнять два вида измерений одновременно. Во-первых, измерять количество оборотов (вала, шестерни, колеса и т.п.). Во-вторых, измерять время. Для выполнения таких измерений электронный тахометр (рис. 26) содержат электронный секундомер, фотоэлектрический датчик и логическое устройство ЛУ.
С устройством и работой электронного секундомера мы познакомились в предыдущем разделе. Теперь познакомимся с устройством и работой фотоэлектрического датчика. Он состоит из светодиода – излучателя СД, фотодиода – приемника ФД и формирователя электрических импульсов ФС1. Светодиод СД излучает свет на фоточувствительную поверхность фотодиода приемника ФД. При этом сопротивление фотодиода падает. Если на линии светового потока между светодиодом СД и фотодиодом ФД поместить непрозрачный материал, то сопротивление фотодиода ФД резко возрастет.
Рис. 26. Функциональная схема электронного тахометра
Это свойство фотоэлектрического датчика широко используется в технике и в измерениях. Для измерения скорости вращения между оптопарой – (светодиодом излучателем и фотодиодом приемником), помещают диск 1 с отверстиями, вращающийся на валу 2 (рис. 26). В процессе вращения вала 2 отверстия в диске будут прерывать световой поток между светодиодом СД и фотодиодом ФД. При этом сопротивление фотодиода ФД будет непрерывно изменяться синхронно с частотой вращения вала. Формирователь импульсов ФС1 реагирует на изменения сопротивления фотодиода, преобразуя каждое из их в стандартные по напряжению и длительности прямоугольные электрические импульсы на своем выходе (см. рис. 27, (а). Чем быстрее вращается диск 2, тем больше частота следования импульсов на выходе формирователя ФС1.
Теперь познакомимся с работой логического устройства ЛУ (рис. 26). Логическое устройство имеет два входа и один выход. Принцип его работы можно сформулировать как «2-И». То есть, если и на первый и на второй входы логического устройства ЛУ подано напряжение (условие «2-И» выполняется), то и на его выходе тоже будет напряжение. Если хотя бы на одном из входов ЛУ напряжения нет (условие два «И» не выполняется), то и на его выходе напряжения не будет.Данный принцип работы ЛУ хорошо иллюстрируют графики, представленные на рис. 27.
Рис. 27. Графики электрических импульсов при работе схемы электронного тахометра, (А) – импульсы на выходе формирователя ФС1 в точке А; (Б) – импульсы периодов времени счета (с выхода делительной декады ДД4); (В) – импульсы на выходе логического устройства (на входе в СчД1); (Г) – импульсы, обнуляющие счетные декады в момент начала нового периода счета
В процессе измерения тахометром скорости вращения вала 2 (рис. 26) на выходе формирователя ФС1 в точке (А) вырабатываются электрические импульсы с частотой следования отверстий в диске 1. Эти импульсы подаются на первый вход логического устройства ЛУ. Одновременно с этим на второй вход ЛУ в точку (Б) от выхода делительной декады ДД4 поступают импульсы периодов времени счета.
Глядя на рис. 27. не трудно видеть, что условие «2-И» может периодически выполняться только в момент, когда на второй вход ЛУ в точку (Б) в течение 1 секунды подается напряжение 5 вольт. В это же время с выхода формирователя ФС1 на первый вход ЛУ в точку (А) поступают электрические импульсы, вызванные вращением диска 2. Таким образом, на выходе логического устройства ЛУ в точке (В) формируются прямоугольные электрические импульсы, которые по внешнему виду повторяют импульсы, поступающие от формирователя ФС1. Они поступают на счетные декады СчД, поэтому этот режим называется «счет».
После периода счета импульсов, в течение следующего периода времени продолжительностью в 1 секунду, напряжение на втором входе ЛУ становится равным нулю. На выходе ЛУ напряжение тоже становится равным нулю, поскольку принцип «2-И» не выполняется. Счет не возможен. На счетных декадах в течение одной секунды отображается результат счета. Этот режим называется «индикация».
После режима «индикация» автоматическое устройство управления сбросом УУС (рис. 26) вырабатывает на своем выходе в точке (Г) короткий электрический импульс, который подается одновременно на входы обнуления всех счетных декад. Счетные декады обнуляются, и начинается новый режим счета. Таким образом, режимы «счет» и «индикация» циклически повторяются.
Чтобы по показаниям электронного тахометра определить скорость вращения вала, шестерни и пр., используют формулу:
(2.18)
где: N – результат счета на дисплеях счетных декад; k – количество отверстий в диске датчика; t – период времени счета.
Например, на дисплеях счетных декад электронного тахометра отобразилось число 2400. В диске датчика 80 отверстий. Период времени счета равен 1 секунде. В этом случае:
об/сек.
Если в окружности диска сделать 60 отверстий, а период времени счета будет равен 1 секунде, то с учетом того, что в 1 минуте 60 секунд, электронный тахометр будут показывать скорость вращения в размерности [об/мин].
Абсолютная погрешность Δn измерения числа оборотов электронным тахометром вычисляется по следующей формуле:
, [об/мин] (2.19)
где: Δtизм – абсолютная погрешность длительности импульса времени (от нестабильности генератора опорных частот); nх – измеренная скорость вращения; tизм – длительность импульса времени (в нашем примере он равен 1 секунде).
Относительную погрешность измерения числа оборотов электронным тахометром определим по формуле:
(2.20)
Например, необходимо определить абсолютную и относительную погрешности измерения числа оборотов электронным тахометром, если он показывает величину измеренной скорости вращения nх = 1000 об/мин, а абсолютная погрешность длительности импульса времени Δtизм = 0,0001 с. Используя формулу (2.19) определим абсолютную погрешность измерения числа оборотов электронным тахометром:
Δn = ±(0.0001 × 1000 + 1) = ±1,1 об/мин.
Используя формулу (2.20) определим относительную погрешность измерения числа оборотов электронным тахометром:
.
Измерение угла поворота вала
Наиболее распространенным является измерение угла поворота коленчатого вала в процессе работы микропроцессорной системы управления двигателя. При этом используют индуктивные датчики, структурная схема и внешний вид которого представлены на рис. 28.
![]() |
![]() |
а) | б) |
Рис. 28. Индуктивный датчик: а) структурная схема; б) внешний вид;
1 – металлический стержень; 2 – провод, намотанный в виде катушки; 3 – металлический кронштейн крепления датчика; 4 – магнит; 5 – металлическая экранирующая оплетка проводов; 6 – выводы для подключения катушки датчика; 7 – вывод, для подключения экранирующей оплетки
Индуктивный датчик состоит из катушки провода 2, намотанного на металлический стержень 1. В верхней части датчика закреплен магнит 4. Катушка 2 имеет два вывода 6, которые помещены в экранирующую оплетку 5. Для подключения датчика используют два вывода 6 катушки 2 и провод от экранирующей оплетки 7.
Индуктивный датчик (ИД) устанавливают в кожухе сцепления двигателя
так, чтобы нижний конец его металлического стержня 2 находился на расстоянии 0,5¸1,0 мм от поверхности зубьев венца 1 маховика двигателя (рис. 29, а).
Магнит создает магнитное поле вокруг катушки датчика. При вращении маховика, зубья его венца движутся относительно стержня индуктивного датчика. При прохождении вершины зуба мимо стержня магнитное поле вокруг датчика увеличивается, поскольку зазор между ними минимален. При прохождении впадины зуба, зазор между стержнем датчика и маховиком сильно увеличивается и магнитное поле датчика резко снижается. Таким образом, на катушку индуктивного датчика действует переменное магнитное поле и в ней возникает переменный ток, с напряжением ±Uд которое можно снять с контактов датчика. Форма сигнала индуктивного датчика представлена на верхнем графике рисунка 29, б. Максимальная амплитуда его сигнала Uд мах зависит от скорости прохождения зубьев относительно стержня датчика и может достигать от долей до нескольких десятков вольт.
![]() | ![]() |
а) | б) |
Рис. 29. Измерение угла поворота коленчатого вала
а) блок-схема микропроцессорного измерителя; б) - осциллограммы сигналов; 1 – зубчатый венец маховика; 2 – индуктивный датчик; 3 – полупроводниковый диод; 4 – жидкокристаллический дисплей
Для измерения угла поворота коленчатого вала, сигнал ±Uд индуктивного датчика фильтруют, пропуская его через полупроводниковый диод 3 (рис. 29, а). Поскольку диод 3 попускает ток только в одну сторону и не пропускает его в другую, то на его выходе останутся только положительные полупериоды сигнала датчика с напряжением +Uд (их форма представлена на среднем графике рис. 29, б).
Положительные полупериоды сигнала индуктивного датчика напряжением +Uд поступают на вход формирователя ФИ стандартных (по форме и длительности) прямоугольных импульсов. В моменты времени t1, t2, и т.д., когда зубья маховика начинают проходить мимо стержня индуктивного датчика, формирователь импульсов ФИбудет вырабатывать на своем выходе по одному стандартному прямоугольному импульсу, напряжением +5В (см. нижний график рис. 29, б).
Чтобы, используя стандартные импульсы, определить величину угла поворота коленчатого вала необходимо знать количество зубьев Z на венце его маховика. Величина угла jv поворота коленчатого вала будет равна:
, [град] (2.21)
где nz – количество стандартных импульсов, на выходе формирователя ФИ за период поворота коленчатого вала на угол jv.
Для решения этого уравнения используют микропроцессор МК. Стандартные импульсы формирователя ФИ поступают на вход микропроцессора МК. Программа микропроцессора считывает с его входа стандартные импульсы (считает nz) и, решая уравнение (2.21), определяет величину угла поворота коленчатого вала jv.
Измерение скорости вращения коленчатого вала.Используя схему, представленную на рис. 2.21, а) можно измерять скорость ne вращения коленчатого вала двигателя. Для этого в схеме с микропроцессором установлен кварцевый генератор, генерирующий стандартные импульсы времени, длительностью tt =1,0 секунду. Чтобы определить скорость ne вращения коленчатого вала двигателя микропроцессор решает уравнение вида:
, [об/сек] (2.22)
где nt – количество стандартных импульсов, поступивших в микропроцессор МКот формирователя ФИ за время tt = 1,0 с.
При необходимости, скорость ne вращения коленчатого вала двигателя можно отображать на жидкокристаллическом дисплее 4 (рис. 2.21, а).
Абсолютная погрешностьсистемы измерения угла jv поворота определяется по формуле:
, [град]. (2.23)
Относительная погрешность системы измерения скорости ne вращения определяется по формуле:
(2.24)
ИЗМЕРЕНИЕ ТЕМПЕРАТУРЫ
Измерение температуры выполняют несколькими средствами, наиболее распространенными из которых являются термопреобразователи сопротивления и термоэлектрические преобразователи. Их выпускают в разных исполнениях в зависимости от способа контакта с окружающей средой (погружаемые, поверхностные), условий эксплуатации (стационарные, переносные), защищенности от воздействия окружающей среды (обыкновенные, пылезащищенные, водозащищенные, взрывозащищенные), герметичности, инерционности, устойчивости к механическим воздействиям (обыкновенные, виброустойчивые). Они различаются по количеству чувствительных элементов для измерения температуры в одной зоне (одинарные, двойные), числу зон (одно- и многозонные) и выводных проводников (два, три, четыре).
ТЕРМОПРЕОБРАЗОВАТЕЛИ СОПРОТИВЛЕНИЯ
Принцип действия термопреобразователей сопротивления основан на использовании свойства чувствительного элемента менять свое сопротивление при изменении температуры. Они могут быть проволочными и полупроводниковыми.
Термопреобразователи сопротивления ПРОВОЛОЧНЫЕ. Материалом проволочных термопреобразователей является, как правило, медь или платина (см. табл.).
В диапазоне температур от - 50 до +180 °С сопротивление меди находится в линейной зависимости от температуры:
Rt = Ro [1 + α (t – to)] ,
где Rt - сопротивление при температуре t, α = 0,00428 1/°С.
Сопротивление платины:
Rt = Ro [1 + αп (t – to) + βп (t – to)2] ,
где αп = 3,94∙10-3 1/°С; βп = 5,8∙10-7 1/°С.
Конструкции термопреобразователей сопротивления весьма разнообразны. Чувствительный элемент большинства из них представляет собой спираль, намотанную без механических натяжений на каркас из изоляционного материала. Каркас со спиралью помещен в защитный кожух, представляющий собой металлическую или стеклянную гильзу, заполняемую гелием или порошком окиси алюминия.
По точности измерения температуры термопреобразователи сопротивления делят на пять классов (см. таблицу).
Основные параметры термопреобразователей сопротивления
Тип термопреобразователя (материал проволоки) | Номинальная статическая характеристика преобразования | Диапазон измеряемых температур, °С | Номинальное сопротивление при 0 °С, Ом |
ТП (платина) | 1 П 5 П 10 П 100 П 500 П | От -50 до 1100 » -100 > 1100 » -260 » 1000 » -260 » 1000 » -260 » 300 | 1 5 10 50 100 500 |
ТП (медь) | 5 М 50 М 100 М | От -50 до 200 » -50 » 200 » -200 » 200 | 10 50 100 |
Наибольшее применение в научных исследованиях получили серийные преобразователи ТСП-5071 с температурным диапазоном от -200 до +600 °С. Температурный коэффициент полупроводниковых термопреобразователей (термисторов) более высокий (3÷6 % на 1 °С),по сравнению с проволочными (0,4 % на 1 °С). Они отличаются большим внутренним сопротивлением, малыми габаритами, высокой механической прочностью, длительным сроком службы и низкой стоимостью.
Для измерения температуры термопреобразователи сопротивлений R1, R2, R3, и R4 включают в мостовую схему с балансировочным резистором и усилителем (см. рис. 29-1).
Рис. 29-1. Мостовая схема включения термопреобразователей сопротивлений с балансировочным резистором и усилителем.
Причем, если необходимо измерить разность температур между двумя средами, то термопреобразователи сопротивлений R1 и R2 располагают в одной среде, а термопреобразователи сопротивлений R3 и R4 – в другой. Включение термопреобразователей сопротивлений R1 и R2, а также R3, и R4 в мостовую схему[1] следует выполнять попарно, в диагонали моста. В этом случае при нагревании (или охлаждении) любой пары резисторов разность потенциалов между точками А и С будет изменяться пропорционально изменению температуры.
Перед измерением схему сначала прогревают (дав поработать 10÷15 минут) а затем балансируют и тарируют. Балансировку схемы выполняют при нахождении всех термопреобразователей сопротивлений R1, R2, R3, и R4, в одинаковой температуре. Её производят резистором R7 до тех пор, пока разность потенциалов между точками А и С не будет равна «нулю». Показание измерительного прибора mA при этом установится на отметке «ноль».
Для тарировки схемы термопреобразователи сопротивлений R1 и R2 постепенно нагревают до максимальных рабочих температур, а затем также постепенно охлаждают их, одновременно регистрируя температуру и показания прибора mA. При этом термопреобразователи сопротивлений R3 и R4 должны находиться при постоянной начальной температуре. По результатам тарировки строят тарировочный график функции A=f(ToC), по которому рассчитывают величину абсолютной и приведенной погрешности измерения.
Абсолютная погрешностьсистемы измерения температуры определяется как максимальная разность, по формуле:
max, [oC]
где Тн – температура, измеренная схемой в режиме её повышения;
То – температура, измеренная схемой в режиме её понижения.
Относительная погрешность системы измерения температуры определяется по формуле:
Важным параметром преобразователя является показатель тепловой инерции или постоянная времени, определяемая как время, в течение которого тело, помещенное в среду с постоянной температурой, нагревается до 63,2 % значения температуры среды. По этому параметру термопреобразователи сопротивления выпускают с малой тепловой инерцией (не более 10 с), со средней (не более 60 с) и с большой (более 60 с), что определяется их конструкцией.
К недостаткам термисторов относят нелинейность и низкую воспроизводимость градиуровочной характеристики, что приводит к необходимости их индивидуальной градуировки.
Допускаемые отклонения параметров термопреобразователей сопротивлений
Допускаемые отклонения | Класс термопреобразователя | Тип термопреобразователя | |
ТП (платина) | ТП (медь) | ||
Номинального сопротивления при 0 °С, % | I II III IV V | ±0,05 ±0,1 ±0,2 ±0,4 ±0,8 | — ±0,1 ±0,2 ±0,5 ±1,0 |
Отношения 1,3910 (ТСП) W100 = 1,4280 (ТСМ) | I II III IV V | +0,0015 -0,0005 + 0,0015 - 0,0010 + 0,0015 - 0,0020 + 0,0015 - 0,0030 +0,0015 -0,0050 | — ±0,0010 ±0,0020 ±0, 0030 + 0,0030 - 0,0050 |
ТЕРМОЭЛЕКТРИЧЕСКИЕ ПРЕОБРАЗОВАТЕЛИ. Чувствительным элементом (датчиком) термоэлектрическогопреобразователя является термопара.
![]() | Термопары изготавливают из двух разнородных электродов в виде проволоки, (например: хромели – 1 и алюмели – 2) соединенных (обычно, сваренных электродуговым способом) в одной точке – 3 (рабочий конец термопары). При неравенстве температур рабочего и свободных концов термопары на последних возникает, сигнал (термо-ЭДС), пропорциональный разности температур рабочего и свободных концов. В качестве прибора, регистрирующего ЭДС, обычно используют милливольтметры и миллиамперметры. |
Низкие температуры (до -200 °О измеряют медь-копелевыми, хромель-копелевыми, хромель-алюмелевыми, железо-константановыми и медь-кон-стантановыми термопреобразователями, из которых последние получили наибольшее применение. Для измерения более низких температур термоэлектрические преобразователи применяют редко вследствие их невысокой чувствительности, а также значительных погрешностей, обусловленных паразитными ЭДС.
Преобразователи типа ТВР используют в вакууме или в инертных средах, так как при высоких температурах на воздухе они окисляются.
Ниже в таблице приведены основные параметры термоэлектрических преобразователей и формулы для вычисления пределов допускаемых отклонений термо-ЭДС термопар от градуировочных таблиц.
Основные параметры термоэлектрических преобразователей
Тип преобразователя | Номинальная статическая характеристика преобразования | Материал термоэлектродов | Измеряемые температуры при длительном применении, оС | Предельная температура при кратковременном применении, оС | Допускаемые отклонения термоЭДС термопар преобразователей, мВ |
ТПР ТПП ТХА ТХК ТВР | ПР-30/668 ПП68 ХА68 ХК68 ВР 5/2068-1 ВР 5/2068-2 ВР 5/2068-3 | Платинородий (30 % родия) Платинородий (10 % родия) - платина Хромель-алюмель Хромель-копель Вольфрамрений (5 % рения) — вольфрамрений (20 % рения) | 300÷1600 0 ÷ 1300 От -50 до +1000 От -50 до +600 0 ÷ 1800 | 1800 1600 1300 800 2500 | 0,01+3.3∙10-5(t-300) 0,01+2.5∙10-5(t-300) 0,16+2,0∙10-4(t-300) 0,2 + 6,0∙10-4(t-300) 0,08+4,0∙10-6(t-1000) |
Термоэлектрический преобразователь как элемент системы регулирования в значительной степени определяет характеристики температурного устройства испытательной машины. Тепловая инерция термопреобразователя зависит от его конструктивного исполнения, уровня температуры и диаметра термоэлектродов.
Выпускают термопреобразователи малой, средней, большой и, ненормированной инерционности с показателем тепловой инерции соответственно не более 5, 60, 180 и свыше 180 с для погружаемых, и не более 10, 120, 300 и свыше 300 с для поверхностных термопреобразователей.
АНАЛИЗ ТЕМПЕРАТУРНЫХ ПОЛЕЙ
Пирометрические методы находят все более широкое применение для получения видимого изображения и регистрации температурного поля поверхности материальных объектов. Приборы для наблюдения и исследования объектов по их тепловому излучению называются тепловизорами.
Первые приборы, разработанные для ночного видения, основанные на применении электронно-оптических методов усиления и визуализации фотоэлектронов, имели спектральный диапазон чувствительности до 1,3 мкм и позволяли наблюдать распределение температур только выше 400 °С.
Телевизионные приемные трубки - видиконы с фоторезистивным слоем из пленки оксида свинца или сульфида оксида свинца чувствительны к излучению до 2 мкм. Чувствительные телекамеры, снабженные такими видиконами, дают возможность определять температурное поле при температурах выше 250 °С.
Создание чувствительных приемников инфракрасного излучения, спектральная чувствительность которых простирается далеко в инфракрасную область спектра, открыло широкие возможности для развития термографии и тепловидения объектов с более низкими температурами. Применение в качестве приемников излучения пироэлектрических элементов дает возможность получать видимое изображение температурного поля объектов с температурой от -20 до +2000 °С.
Телевизионные приемники инфракрасного излучения, в которых видикон выполнен со сканируемой поверхностью из пироэлектрического кристалла три-глицилсульфата, позволяют создавать чувствительные пироэлектрические тепловизоры, известные под названием пиротронов, пироконов или видиконов пироэлектрических, которые обеспечивают прием инфракрасного излучения вплоть до 40 мкм.
Структурная схема тепловизора показана на рис. 29-2. Приемно-оптическая система 7, управляемая сканирующей системой УСкС, производит обзор объекта и разлагает его изображение в ряд точек, излучение от которых воспринимается приемником излучения 6, выходной сигнал которого подается на усилитель УВО. Сигналы с усилителя УВО и устройств развертки и синхронизации ГПНсоздают на экране электронно-лучевой трубки[2] 5видимое изображение температурного поля поверхности исследуемого объекта.
Обзор происходит в пределах поля зрения, определяемого углами α и β, за время t, называемое временем кадра. В качестве приемников излучения применяются фоторезисторы из антимонида индия, охлаждаемые жидким азотом до -196°С. Такие приемники имеют постоянную времени 1 мкс, что позволяет в зависимости от требуемого геометрического разрешения получать кадры с частотой 0,5÷60 Гц. Низкая частота кадров пока ограничивает применение тепловизоров при исследовании динамики тепловых процессов и наблюдении быстродвижущихся объектов.
Рис. 29-2. Структурная схема тепловизора, 1 – электронно-лучевая трубка; 2 – электронная пушка; 3 – вертикально отклоняющие пластины; 4 – горизонтально отклоняющие пластины; 5 - экран электронно-лучевой трубки; 6 - приемник излучения; 7 - приемно-оптическая система; УВО – усилитель вертикального отклонения луча; УГО – усилитель горизонтального отклонения луча; ГПН – генератор пилообразного напряжения; УСкС - управляющая сканирующая система
Можно увеличить геометрическое разрешение и частоту кадров применением нескольких приемников, соединенных в строку или детекторную матрицу.
Важной характеристикой тепловизоров является их порог чувствительности - минимально определяемая разность температур ΔТмин на поверхности АЧТ (e=1) с температурой 25°С, при которой отношение сигнала к собственным шумам тепловизора должно быть равно 1. У серийно выпускаемых тепловизоров ΔТмин = 0,1÷ 0,3 °С.
![]() | ![]() |
а) | б) |
Рис. 29-3. Внешний вид тепловизора – а) и изображение температурных полей двигателя на экране тепловизора – б)
Для исследования температурных полей малых объектов разработаны тепловизорные микроскопы и микрорадиометры, применяемые, например, для исследования температурного поля микросхем с целью обнаружения скрытых дефектов. В таких приборах используется микроскопная оптика с увеличением от 3 до 125. Известны микрорадиометры, имеющие пространственное разрешение 10 мкм и температурное разрешение ΔТ=0,06°С в диапазоне температур от -30 до +850°С.
Тепловидение и термография широко применяются при геологических и климатологических исследованиях земной поверхности, в медицинской практике для диагностики, в строительстве для проверки теплоизоляции зданий, для обнаружения мест перегрева в электрических цепях и у различного рода энергетического оборудования, для измерения механических напряжений и деформаций. Для температурного зондирования атмосферы применяются спутниковые радиометры, а для поисков залежей полезных ископаемых - спектрорадиометры. Такие приборы обычно градуируются непосредственно в единицах температуры или в единицах энергетической яркости.
Дата добавления: 2018-04-05; просмотров: 1756; Мы поможем в написании вашей работы! |
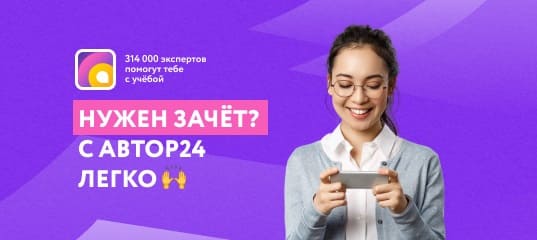
Мы поможем в написании ваших работ!