Определение величины скорости резания
Nbsp; Федеральное государственное бюджетное образовательное учреждение высшего образования «Саратовский государственный технический университет имени Гагарина Ю.А.» Кафедра «Технология машиностроения» Методические указания и задания к выполнению контрольной самостоятельной работы по дисциплине “Операции и процессы формообразования” для студентов направления КТОП Одобрено редакционно-издательским советом Саратовского государственного технического университета Саратов 2016 Целью выполнения работы является приобретение навыков пользования технической справочной литературой, регламентирующей порядок выбора инструментов и расчета или назначения режимов резания на операции обработки на токарно-винторезном станке. В данной работе рассматривается станок самой распространенной модели 16К20 и примеры обработки на станке поверхностей деталей типа «Вал» и «Вал-втулка». Переходы токарной операции по обработке поверхностей одной из рассматриваемых деталей могут быть: подрезка торца, сверление отверстия, расточка просверленного отверстия резцом или обработка зенкером, расточка канавки в отверстии под выход резьбового резца, нарезание наружной или внутренней резьбы резцом, обточка наружного диаметра, обработка фаски.
|
|
ИСХОДНЫЕ ДАННЫЕ К ВЫПОЛНЕНИЮ РАБОТЫ
Эскизы деталей, на примере обработки которых производится выполнение работы, приведены в табл. 1, а размеры заготовки и исходные данные к обработке - в табл. 2, 3 и 4 приложения.
Вариант, предлагаемый к выполнению, следует выбирать по двум цифрам полученным от преподавателя. Последняя цифра этой комбинации соответствует номеру рисунка из табл. 1. Одновременно эта цифра задает номер варианта табл. 3, в которой указаны окончательные размеры обрабатываемых диаметров.
Предпоследняя цифра комбинации задает номер варианта табл. 2, в которой указаны длины соответствующих обрабатываемых диаметров, а также номер строки табл. 4, регламентирующей условия обработки.
Последовательность обработки детали типа «Вал» заключается в следующем:
1) закрепить деталь в трехкулачковом патроне;
2) подрезать торец последовательно с двух сторон;
3) зацентровать торец с двух сторон;
|
|
4) перезакрепить деталь в центрах и поводковом патроне;
5) обточить наружные диаметры (ступени шеек) в несколько проходов;
6) проточить канавки;
7) снять фаску;
8) нарезать нестандартную резьбу резцом в несколько проходов.
Последовательность обработки детали типа «Вал-втулка» заключается в следующем:
1) подрезать торец с двух сторон;
2) обточить наружные диаметры (ступени шеек) в несколько проходов;
3) зацентровать отверстие для направления спирального сверла;
4) сверлить отверстие;
5) раззенковать и расточить отверстие под резьбу;
6) расточить канавку под выход резьбового резца;
7) нарезать нестандартную резьбу резцом в несколько проходов;
8) снять фаску.
Если видом заготовки для заданного варианта детали является прокат, то следует предусмотреть, что заготовку требуемой длины предварительно, до обработки торцов, необходимо отрезать от круга (прутка), соблюдая ту же величину припуска на длину, что и заданный в таблице припуск на диаметр.
ПОРЯДОК ВЫПОЛНЕНИЯ РАБОТЫ
При выполнении задания по обработке деталей типа «Вал» и «Вал-втулка» необходимо:
1. Выбрать режущий инструмент для обрабатываемых поверхностей, выбрать одну из рекомендуемых марок инструментального материала для выбранных инструментов, сделать эскизы всех инструментов с указанием размеров и геометрических параметров режущей части.
|
|
2. Установить или рассчитать глубину резания для обрабатываемых поверхностей для каждого из проходов.
3. Для обработки одной из наружных поверхностей рассчитать по нижеприведенным формулам, с учетом технологических ограничений, режимы резания: S, V, Pz , Nрез.ф., Mкр. Эти же величины следует определить по любым доступным студенту таблицам нормативов и сделать вывод о соответствии полученных результатов, определив разницу в значениях в процентах. Рассчитать машинное время для обработки этой поверхности.
4. Для обработки остальных поверхностей эти же режимы резания: S, V, Pz (Po), Nрез.ф., Mкр,, Тм - выбрать и назначить с помощью таблиц нормативов [6], [7] или другой справочной технической литературы. Если в используемых справочниках некоторые параметры, например, мощность резания или крутящий момент при сверлении, отсутствуют, то их можно рассчитать по формулам, например, из [2] или [4] .
5. Изобразить схему обработки каждой поверхности детали с указанием окончательных размеров, а также направлений величин V и S. Режущий инструмент на схемах изобразить в конечном положении обработки поверхности.
|
|
Примерный вид эскиза совместного положения з аготовки иинстнрумента приведен в приложении 6.
Инструмент для обработки каждой поверхности заготовки можно выбирать по любому из имеющихся в наличии справочнику технолога-машиностроителя или по иной справочной литературе, например, [1], [2], [4]. При этом, в учебных целях, следует выбирать инструмент с креплением пластинки инструментального материала методом пайки. При выборе одной из рекомендуемых марок инструментального материала, которым может быть оснащена режущая часть инструмента, следует руководствоваться характеристиками заданного материала заготовки и указанными в задании условиями обработки.
Для токарного резца с напаянной пластинкой инструментального материала следует указать и эскизно изобразить форму заточки передней поверхности в соответствии с рекомендациями [4] или [9] с указанием сечения, в котором производится эта заточка, перечислить численные значения всех регламентируемых геометрических параметров режущей части и указать на эскизе их непротиворечивые величины, размеры сечения державки и толщину пластинки инструментального материала, например, по [2], [4], и указать обозначение выбранного резца по [1]. Каждое принятое техническое решение подтверждают ссылками на рекомендации соответствующего справочника с указанием номера страницы и таблицы (карты), в которой приведена данная рекомендация. Нужно оговорить и изобразить на эскизе обработки рассматриваемой поверхности, что установка резца при наружной обработке осуществляется выше оси центров станка на величину +h, так как сила резания отжимает резец в направлении действия силы (вниз) и режущая кромка устанавливается на уровне центров станка.
Аналогично по справочникам выбираются и указываются на эскизах форма режущей части, ее материал и материал державки, размеры сечения державки и значения геометрических параметров режущей части для расточного резца, сверл, зенкера, резьбового резца. Эскиз внешнего вида центровочного сверла, размеры которого должны быть согласованы с размерами спирального сверла, приведен, например, в [9].
Путем распределения припуска на обработку h между переходами устанавливается глубина резания на черновом и чистовом переходах. Принимается, что на предварительном переходе удаляется 2/3 припуска и глубина резания t1 = 2/3 h, а на получистовом (и окончательном в данном случае) проходе - 1/3 припуска и t2 = 1/3 h. Возможны и иные, вынужденные, варианты распределения припуска между большим числом переходов, определяемые после расчета мощности, потребной на резание.
Назначение режимов резания для наружного обтачивания поверхности детали на этих переходах производится в соответствии с рекомендациями, изложенными ниже.
РАСЧЕТ РЕЖИМОВ РЕЗАНИЯ ДЛЯ ПРЕДВАРИТЕЛЬНОГО ПЕРЕХОДА
Определение величины подачи
В общем случае, с целью повышения производительности обработки, величина подачи должна приниматься максимально возможной. Однако ее увеличение ограничивается рядом лимитирующих факторов. Для ознакомления с ними величину подачи следует рассчитывать в следующей последовательности.
Определяется по справочным данным нормативов [2,3] максимальный диапазон рекомендуемых пределов подач Sтабл, используемый в дальнейшем для оценки расчетных величин.
Аналитически определяется подача, допускаемая лимитирующими факторами.
1.1. Подача, допускаемая прочностью механизма подачи станка, мм/об,
(1)
где | V - скорость резания, м/мин. При предварительных расчетах можно принять значение скорости в диапазоне от 40 до 60 м/мин для инструмента, оснащенного быстрорежущей сталью, и от 70 до 100 м/мин для инструмента, оснащенного твердым сплавом, что примерно соответствует нижнему пределу диапазона скоростей при работе такими инструментами. В дальнейшем это значение будет уточняться;
![]() ![]() ![]() ![]() |
Если в паспортных данных станка (см. табл. 5 приложения) приведено значение только тангенциальной силы Pdop z, допускаемой прочностью станка, то, используя примерную зависимость между этими составляющими, можно принять, что
(2)
1.2. Подача, допускаемая прочностью державки резца, мм/об,
(3)
где | ![]() |
H, (4)
где | B - ширина державки резца, мм;
H - высота державки резца, мм;
lp- длина вылета резца (расстояние от точки крепления до вершины), мм. При наружном точении можно принять lp = 1,5 ![]() ![]() ![]() ![]() ![]() ![]() ![]() |
Показатели степеней и коэффициенты CPz и KPz имеют тот же смысл, что и для осевой составляющей силы резания, и выбираются по тем же справочникам.
1.3. Подача, допускаемая жесткостью державки резца, мм/об,
(5)
где Pdop3 - наибольшее значение тангенциальной составляющей силы реза-
ния, допускаемое жесткостью державки резца, Н:
(6)
где | Еp - модуль упругости материала державки резца, мПа. Для применяемых обычно при изготовлении державок резцов сталей Еp = (2,0 - - 2,2) ![]() ![]() |
1.4. Подача, допускаемая прочностью детали, мм/об,
(7)
где Pdop 4 - наибольшее значение тангенциальной составляющей силы ре-
зания, допускаемое прочностью детали, Н :
(8)
где | L1 - расчетная длина детали;
Qн - коэффициент нагружения при расчете на прочность. При обработке детали в патроне Qн = 1, при обработке детали в центрах Qн = 0,25, при поджиме задним центром детали, закрепленной в патроне, Qн = 0,19;
W - момент сопротивления сечения детали, мм3. Для сплошного круглого сечения обработанной на предварительном переходе поверхности W =( ![]() ![]() ![]() ![]() ![]() ![]() ![]() ![]() |
1.5. Подача, допускаемая жесткостью детали, мм/об,
(9)
где Pdop 5 - наибольшее значение тангенциальной составляющей силы реза-
ния, допускаемое жесткостью детали, Н:
(10)
где | Qg - коэффициент нагружения при расчете на жесткость. При обработке короткой детали, закрепленной в патроне, Qg = 3, при обработке детали, закрепленной в центрах, Qg = 48, при поджиме обрабатываемой детали, закрепленной в патроне задним центром, Qg = 110;
Еd - модуль упругости материала детали. При расчетах можно принять, что для стали Еd = 2 ![]() ![]() ![]() |
1.6. Подача, допускаемая прочностью твердосплавной пластинки, мм/об
Определяется только для инструментов, оснащенных твердым сплавом, из нормативов, например из [2], с учетом вида обрабатываемого металла, главного угла в плане и радиуса при вершине резца, глубины резания и остаточной толщины пластинки инструментального материала после переточки и формирования положительного переднего угла. Остаточная толщина пластины принимается равной (0,2 H), мм.
Из всех найденных по лимитирующим факторам значений подач необходимо выбрать наименьшую Smin, как удовлетворяющую всем ограничениям. Так как станок обеспечивает дискретный ряд значений подач, то выбранное значение Smin корректируется по паспортным данным станка (табл.5 приложения) и принимается ближайшее меньшее значение подачи в качестве Sф.
Во избежание грубых ошибок при расчетах выбранное значение Sф следует сравнить с найденным до расчетов диапазоном значений подач, рекомендуемым нормативами. Величина Sф не должна значительно (более чем в два раза) отличаться от граничных табличных значений. При незначительном превышении верхней границы диапазона следует выбирать расчетное значение, так как оно точнее учитывает условия обработки. Если расчетное значение по критериям жесткости и прочности детали ниже нижней границы диапазона, то выбирается верхнее табличное значение и делается заключение о необходимости проведения обработки в люнете, исключающем прогиб детали, или о необходимости изменения способа закрепления и поджиме свободного конца детали задним центром (в случае зажима детали только в патроне).
Определение величины скорости резания
2.1. Ориентировочное значение тангенциальной составляющей силы резания Pz, Н, определяется для глубины резания на предварительном переходе, фактического значения подачи и ориентировочного значения скорости резания, принятого для расчетов в п. 1.1:
(11)
2.2. Величина потребного для резания крутящего момента, развиваемого на обрабатываемом диаметре, Нм,
. (12)
2.3. По найденному значению крутящего момента из паспортных данных станка (табл. 5 приложения) выбирается частота вращения шпинделя nст, соответствующая ближайшему большему допускаемому крутящему моменту на шпинделе станка.
2.4. В соответствии с найденным значением частоты вращения шпинделя определяется максимальное значение скорости резания Vст, допускаемой прочностью механизма главного движения станка, м/мин:
. (13)
2.5. Определяется максимальная величина скорости резания Vи, допускаемой режущими свойствами инструмента, м/мин:
и
, (14)
где | Т -стойкость инструмента, выбирается любое значение из рекомендуемых справочными данными;
СV -постоянный коэффициент, характеризующий материал заготовки и условия ее обработки;
KV -общий поправочный коэффициент, учитывающий все другие конкретные условия обработки по сравнению с теми, для которых приводится в справочнике значение СV. Общий поправочный коэффициент KV представляет собой произведение отдельных частных коэффициентов, каждый из которых отражает влияние определенного фактора на скорость резания. Количество и значения частных коэффициентов определяются полнотой используемого справочника.
m- показатель относительной стойкости;
![]() |
Все перечисленные величины можно выбрать из справочников, например, из [2,4].
2.6. Из двух скоростей резания Vст и Vи выбирают наименьшее значение скорости Vmin, удовлетворяющее обоим ограничениям. Если наименьшей окажется скорость резания Vи, то находят соответствующую ей частоту вращения шпинделя станка на обрабатываемом диаметре:
(15)
и по паспортным данным станка выбирают новое фактическое значение nст. Пересчитывают новое значение фактической скорости резания Vф по формуле, аналогичной (13), при подстановке в нее фактического значения nст.
3. Определение показателей эффективности результатов расчета
3.1. Фактическое значение тангенциальной составляющей силы резания Pzф рассчитывают по формуле (11), подставляя в нее определенные в разделах 1 и 2 значения Sф и Vф.
3.2. Фактическая мощность, затрачиваемая на резание, кВт:
рез.ф.
. (16)
3.3. Коэффициенты использования
инструмента по скорости резания:
, (17)
и станка по мощности:
, (18)
где | N эфф. пр - эффективная мощность шпинделя по приводу, выбирается из паспортных данных станка (табл. 5 приложения) или определяется по формуле: |
Nэфф.пр. = Nпр.эд . пр., (19)
где | Nпр.эд. - мощность двигателя привода главного движения, кВт;
![]() ![]() |
Если расчеты покажут, что коэффициент использования станка по мощности имеет значение большее 1, т. е. мощности станка недостаточно для выполнения операции, следует уменьшить выбранные значения Vф или Sф, при этом уменьшение Vф является более выгодным, так как машинное время будет такое же, как и при уменьшении Sф, но период стойкости инструмента значительно возрастет. Можно также уменьшить глубину резания на каждом из переходов, увеличив их число. После проведенных изменений расчеты следует провести заново.
3.4. Машинное время Т м , мин, на операцию:
(20)
где | L –длина прохода резца: L = l + y + ![]() ![]() ![]() ![]() |
Дата добавления: 2018-04-05; просмотров: 100; Мы поможем в написании вашей работы! |
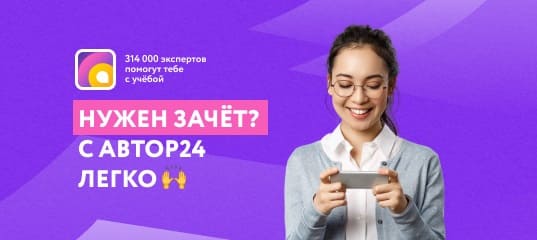
Мы поможем в написании ваших работ!