Утилизация отходящих газов. Очистка газов
Около 2/3 общего количества тепла уходит вместе из рабочего пространства печи месте с дымовыми газами. Температура продуктов сгорания при выходе из рабочего пространства равна примерно 1700 °С. Вследствие подсоса воздуха и потерь тепла при прохождении через вертикальные каналы и шлаковики температура газов при поступлении в регенераторы снижается до 1500-1550 °С. Из-под насадок регенераторов дымовые газы выходят с температурой 500-800 °С. При прохождении через борова и перекидные клапаны эта температура снижается (главным образом в результате подсоса воздуха) еще на 100-200 °С.
Таким образом, перед дымовой трубой температура отходящих газов составляет все еще 400—600 °С, они содержат около 1/3 общего количества тепла, поступающего в печь. Поэтому утилизация этого тепла позволяет существенно повысить показатели работы печи. Температура отходящих газов на двухванных печах, работающих без регенераторов, еще выше.
За всеми мартеновскими и двухванными печами установлены котлы-утилизаторы. Наиболее распространен котел с многократной принудительной циркуляцией воды (рис.9.9 ). В современных котлах-утилизаторах используется 60-70 % тепла отходящих продуктов сгорания и вырабатывается 350-450 кг пара на 1 т выплавляемой стали.
Температура продуктов сгорания в котлах-утилизаторах снижается до 150-230 °С. С такой температурой газы можно отсасывать дымососом прямого действия (котел представляет собой дополнительное значительное сопротивление на пути движения газов, поэтому тяги дымовой трубы не хватает, чтобы протянуть дымовые газы через котел, требуется дополнительный дымосос).
|
|
Снижение температуры дымовых газов при прохождении их через котел-утилизатор позволяет решить также чрезвычайно важную задачу- очистку дыма от плавильной пыли. Количество пыли в дымовых газах, выходящих из печи, колеблется по ходу плавки от 1,0 до 10,0 г/м3, 50—75 % пыли оседает в шлаковиках, 10-25 % в регенераторах и 10-20 % уходит в борова и в трубу.
Рис.9.9. Котел утилизатор вертикального типа: 1-питательный насос; 2- дымосос; 3-футеровка; 4-кожух котла; 5-змеевик водяного экономайзера; 6- испарительный змеевик; 7-барабан; 8-циркуляционный насос; 9-змеевик пароподогревателя.
9.3. «Электросталеплавильное производство»
Виды электросталеплавильных агрегатов
Классификация электропечей
Для выплавки электростали были созданы дуговые печи – агрегаты, в которых тепло, полученное за счет превращения электрической энергии в тепловую, передается расплавляемому материалу.
По способу преобразования подводимой извне к плавильной печи электрической энергии в тепловую, электропечи подразделяются на следующие группы (рис.9.10):
|
|
дуговые; преобразование (превращение) электрической энергии происходит в самой дуге короткого замыкания угольных (графитизированных) электродов о токопроводящую часть шихты (рис.9.1, а);
печи сопротивления; тепло выделяется в специальных элементах или шихтовых материалах в результате прохождения через них электрического тока; по закону Джоуля-Ленца при прохождении электрического тока по проводнику выделяется тепловая энергия:
(1)
где J – величина (сила) электрического тока, А;
R – величина электрического сопротивления проводника, Ом;
t – время прохождения электрического тока по проводнику, с.
Рис. 9.10. Способы плавки стали в электрических печах
а – плавка в ДСП; б – плавка в индукционных печах; в – вакуумная плавка;
г – электрошлаковый переплав; д – плазменно-дуговая плавка.
комбинированные печи (ферросплавные, руднотермические), работающие одновременно как дуговые и как печи сопротивления;
индукционные печи; металл нагревается вихревыми токами, возбуждаемыми в нем электромагнитной индукцией (рис.9.1, б);
электронно-лучевые печи; при помощи электрического тока в вакууме создается строго направленный поток электронов, бомбардирующий и расплавляющий шихту (рис.9.1, в);
|
|
плазменные печи; нагрев и плавление металла осуществляется низкотемпературной плазмой (рис.9.1, д); плазмой называют ионизированный газ с одинаковым количеством (концентрацией) положительно и отрицательно заряженных ионов, т.е. так называемый квазинейтральный газ; для образования плазмы используется аргон, поэтому в печи (плазмотроне) образуется нейтральная атмосфера с небольшим положительным давлением, исключающим подсос атмосферного воздуха в рабочее пространство агрегата; дуга в печи горит стабильно и расплавляет шихту в печи; в состоянии плазмы находится подавляющая часть вещества вселенной: звезды, галактические туманности и межзвездная среда; температура плазмы аргона достигает 30000К;
электрошлаковый переплав (рис.9.1, г); стальной расходуемый в процессе плавки электрод под слоем жидкого электропроводящего шлака, нагреваемого электрическим током до 2000°С, расплавляется и в кристаллизаторе печи формируется новый слиток высококачественной стали; рафинирующий шлак состоит из 70% CaF2 и 30% Al2O3, очищает сталь от серы и неметаллических включений.
Следует особо подчеркнуть, что основное отличие электрических печей от мартеновских и конвертеров, изначально, не связано с тем, что технология электроплавки проводится не на базе протекания в жидком металле экзотермических реакций окисления примесей железосодержащей части шихты, а благодаря тепловой энергии электрических дуг. Для осуществления электросталеплавильного процесса не требуется потребление кислорода (химического окислителя), что позволяет создавать над материалом, расплавленным в рабочем пространстве печи по ходу плавки любую атмосферу (окислительную, восстановительную или нейтральную) в широком диапазоне давлений, обеспечивающих выплавку стали любого химического состава и высокой степени чистоты.
|
|
Относительная простота конструкций электрических плавильных печей создает необходимые условия для механизации и автоматизации процессов, а также для облегчения труда обслуживающего персонала.
Основная доля электростали выплавляется в дуговых электропечах различной емкости (как правило, дуговые печи – трехфазные).
Мощности печей
– малые – (0,5…5)т вместимости;
– средние – (6…50)т вместимости;
– большие – (свыше 50 до 200)т вместимости;
– ультравысокие – (300 и 400)т вместимости.
В отечественных стандартах принято сокращенное обозначение дуговых сталеплавильных печей серий ДСП и ДСВ:
первая буква (Д) означает метод нагрева шихты (дуговой);
вторая буква (С) означает назначение печи (сталеплавильная);
третья буква означает основной конструкционный признак: П – поворотный свод; В – выкатной корпус (из-под стационарного свода). Цифры после букв – вместимость печи по проекту (т).
В обозначении печи могут использоваться аббревиатуры завода-изготовителя и другие, согласованные с заказчиком.
Дата добавления: 2018-04-05; просмотров: 1624; Мы поможем в написании вашей работы! |
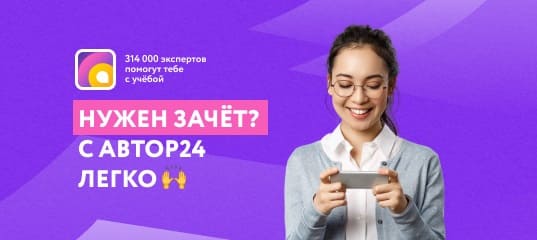
Мы поможем в написании ваших работ!