Автоматизация конвертерного производства
Новые конвертерные цехи оборудуют автоматизированной системой управления (АСУ), которая должна обеспечить управление как отдельными технологическими процессами и агрегатами, так и производством цеха в целом. Составной частью такой АСУ является автоматизированная система управления технологическим процессом плавки в кислородном конвертере (АСУ ТП "Плавка"); подобные АСУ ТП созданы во многих ранее построенных цехах.
Основными задачами такой АСУ являются расчет расхода шихтовых материалов и кислорода; выработка, по возможности, управляющих воздействий для регулирования хода продувки и, что особенно важно, точное определение момента окончания продувки при заданном содержании углерода в металле.
Важность последнего объясняется тем, что из-за быстротечности и краткости продувки нельзя применять обычный для других сталеплавильных процессов метод контроля содержания углерода, заключающийся в периодическом отборе проб металла и их последующем анализе. Поэтому обычно применяют следующий метод окончания плавки. По количеству израсходованного кислорода, длительности продувки, показаниям ЭВМ определяют момент окончания продувки, примерно соответствующий требуемому содержанию углерода. Далее конвертер наклоняют, отбирают пробу металла для экспресс-анализа и измеряют температуру металла термопарой погружения. Затем на основании результатов анализа и замера температуры проводят корректировку состава и температуры ванны методами, описанными ранее.
|
|
При таком методе работы велики непроизводительные простои конвертера, так как длительность корректировочных операций достигает 3-5 мин, увеличиваются теплопотери, снижается стойкость футеровки конвертера.
Существующие АСУ ТП работают в статическом или динамическом режиме управления процессом. В первом случае ЭВМ выполняет расчеты по статической математической модели процесса. Ока построена на использовании только известной до начала плавки информации: в ЭВМ вводят данные о составе и температуре чугуна, составе шлакообразующих материалов, чистоте кислорода, состоянии и температуре футеровки, требуемых составе и температуре стали, основности шлака и др. На основании этих данных по заданной программе ЭВМ рассчитывает параметры плавки, не являющиеся функцией времени,- расход чугуна и стального лома, расход шлакообразующих и кислорода, программу изменения расхода кислорода и положения фурмы, длительность продувки и момент ее окончания. Однако точность выдаваемых ЭВМ рекомендаций невелика, так как в реальных условиях ход продувки отличается от стандартного, заложенного в математическую модель процесса.
|
|
При работе в динамическом режиме управления ЭВМ выполняет расчеты по динамической модели процесса, которая учитывает как исходные данные, так и получаемую по ходу продувки текущую информацию о параметрах процесса (составе и температуре металла и др.). С учетом этих дополнительных данных ЭВМ вырабатывает динамические управляющие воздействия, выполнение которых обеспечивает полную автоматизацию управления ходом плавки. В этом случае при наличии надежно работающих при высоких температурах датчиков будет обеспечиваться остановка продувки с точным получением заданных содержания углерода в металле и его температуры.
Однако проблема создания надежных датчиков для контроля всех необходимых параметров конвертерной плавки пока не решена. Не представляет проблемы контроль при низких температурах множества параметров с помощью серийно выпускаемых приборов (контроль массы материалов, давления и расхода воды, кислорода и других газов, расхода сыпучих материалов и др.). В то же время непрерывный контроль параметров высокотемпературной конвертерной ванны, и в первую очередь, состава и температуры металла, пока не освоен, хотя работы в этом направлении ведутся много лет. Основной трудностью при этом является создание датчиков, способных длительное время работать в условиях разрушающего воздействия высокотемпературных сред - шлаковой и газовой фаз. Поэтому предложено и опробовано много косвенных методов контроля, например непрерывного определения содержания углерода по количеству и составу отходящих газов, уровню шума в конвертере, интенсивности излучения конвертерных газов, данным о вибрации конвертера и др. Однако все они не вышли пока из стадии промышленной отработки.
|
|
В настоящее время наиболее надежным методом остановки продувки при заданном содержании углерода считают применение в сочетании с ЭВМ измерительной фурмы-зонда, вводимой в ванну сверху за 2-3 мин до окончания продувки. Фурма-зонд подобна продувочной фурме, на ее конце крепится сменный измерительный блок, а внутри проложен кабель, соединяющий блок с ЭВМ. В сменном керамическом блоке имеется термопара для замера температуры металла; снабженная термопарой полость, куда затекает металл и при его затвердевании по температуре ликвидус определяют содержание углерода; полость для отбора пробы металла, которую анализируют после вывода зонда из конвертера. В момент погружения зонда в ванну данные о содержании углерода в металле и его температуре поступают в ЭВМ, что позволяет точно рассчитать расход кислорода, необходимого при окислении углерода до заданного содержания, обеспечивая остановку продувки точно при нужном содержании углерода. При повышенной температуре в конвертер вводят охладители, при дефиците тепла вводят теплоноситель (например, уголь, ферросилиций), что позволяет за оставшиеся 2-3 мин продувки получить требуемую перед выпуском температуру металла.
|
|
9.2. «Мартеновское производство»
Сущность мартеновского процесса заключается в ведении плавки на поду пламенной отражательной печи, оборудованной регенераторами для предварительного подогрева воздуха (иногда и газа). Идея получения литой стали на поду отражательной печи высказывалась многими учеными (например, в 1722г. Реомюром), но осуществить это долгое время не удавалось, так как температура факела обычного в то время топлива - генераторного газа - была недостаточной для нагрева металла выше 1500 °С (т.е. недостаточна для получения жидкой стали). В 1856г. братья Сименс предложили использовать для подогрева воздуха тепло горячих отходящих газов, устанавливая для этого регенераторы. Принцип регенерации тепла был использован Пьером Мартеном для плавки стали. Началом существования мартеновского процесса можно считать 8 апреля 1864 г., когда П.Мартен на одном из заводов Франции выпустил первую плавку.
В мартеновскую печь загружают шихту (чугун, скрап, металлический лом и др.), которая под действием тепла от факела сжигаемого топлива постепенно плавится. После расплавления в ванну вводят различные добавки для получения металла заданного состава и температуры; затем готовый металл выпускают в ковши и разливают. Благодаря своим качествам и невысокой стоимости мартеновская сталь нашла широкое применение. Уже в начале XX в. в мартеновских печах выплавляли половину общего мирового производства стали.
В России первая мартеновская печь была построена С.И.Мальцевым в 1866-1867 гг. на Ивано-Сергиевском железоделательном заводе (бывш. Калужской губернии) Мальцевского фабрично-заводского округа. В 1870г. первые плавки проведены в печи вместимостью 2,5т, построенной известными металлургами А.А.Износковым и Н.Н.Кузнецовым на Сормовском заводе. Эта печь хорошо работала и стала образцом для печей большой вместимости, построенных позже на других русских заводах. Мартеновский процесс стал основным в отечественной металлургии. Огромную роль сыграли мартеновские печи в суровые годы Великой Отечественной войны. Советским металлургам впервые в мировой практике удалось удвоить садку мартеновских печей без существенной их перестройки (ММК, КМК), удалось наладить производство высококачественной стали (броневой, подшипниковой и т.п.) на действовавших в то время мартеновских печах. В настоящее время наиболее крупные и высокопроизводительные мартеновские печи работают в России и Украине. По мере расширения конвертерного и электросталеплавильного производств масштабы производства мартеновской стали сокращаются.
Топливо мартеновской плавки
В течение всех периодов в печь подают топливо. Под действием тепла факела нагреваются кладка печи и шихта. Около 85-90 % тепла от факела к ванне передается излучением и 5-15%- конвекцией.
В соответствии с известной формулой Стефана-Больцмана, количество тепла, переданного холодной шихте излучением, может быть выражено следующей формулой:
Q= δεп[(Тгор/100)4 - (Тхол/100)4],
где δ — коэффициент, учитывающий оптические свойства кладки и форму рабочего пространства; εп- степень черноты пламени; Тгор и Тхол — температуры факела (горячего) и шихты (холодной), К.
Таким образом, чем выше температура факела и степень черноты пламени, тем интенсивнее нагревается шихта и тем меньше времени затрачивается на плавку. Повышения температуры факела достигают улучшением степени нагрева воздуха и газа в регенераторах и обогащением воздуха кислородом; повышения степени черноты факела — карбюрацией пламени.
Двухатомные газы (О3, N2, Н2) практически лучепрозрачны для волн всех длин, трехатомные (СО2, Н2О, SО2) обладают некоторой излучательной способностью, однако степень черноты пламени горячего чистого газа составляет всего 0,1-0,2. Чтобы повысить степень черноты пламени, необходимо обеспечить в нем содержание твердых "черных" частичек (в первую очередь углеродистых).
Углеродистые частицы могут появиться в пламени в результате разложения углеводородов: Сx Нy = xСТВ + yНгаз, а также при добавке к подаваемому в печь газу различных жидких или твердых топлив, богатых углеродом и сложными углеводородами (мазут, каменноугольный пек). Практически степень черноты пламени εп не должна быть ниже 0,5; в большинстве случаев она составляет 0,55—0,75.
При одной и той же характеристике факела разность (TГОР/100)4-(TXОЛ/100)4 тем выше, чем холоднее шихта. Наиболее низкая температура шихты наблюдается во время завалки и в начале периода плавления. Степень черноты холодной твердой шихты близка к единице (0,92—0,95). Поэтому в этот период передача тепла от факела к шихте максимальна, она настолько велика, что практически нет опасности оплавить огнеупоры, и в печь подают максимальное количество топлива.
По мере нагрева шихты температура ее Тхол возрастает, шихта раскаляется, покрывается шлаком и сама начинает отражать тепловые лучи, в результате чего условия поглощения тепла шихтой ухудшаются. Во избежание нагрева и оплавления огнеупора необходимо уменьшать подачу топлива.
Таким образом, подача топлива по ходу плавки меняется. Максимальной величины расход топлива достигает во время завалки и в начале периода плавления. Подаваемое в это время количество тепла называют максимальной нагрузкой. По мере прогрева шихты подачу топлива уменьшают и тепловая нагрузка падает. Частное от деления общего расхода тепла топлива для одной плавки на время плавки называют средней тепловой нагрузкой или тепловой мощностью печи, т.е.
= тепловая мощность 106кДж.
Средняя тепловая нагрузка в зависимости от тоннажа печи возрастает от 23,2 для 125-т печи до 69,9 МВт (252 кДж/ч) для 900-т печи. Максимальная тепловая нагрузка на 20-40 % выше средней.
Для характеристики топлива и условий его сжигания применяют коэффициент использования топлива (к.и.т.)
η=(QT-Qyx)-тепло уходящих газов,
где Qт - теплота сгорания топлива; Qyx –тепло уходящих газов.
Для мартеновских печей к.и.т. составляет 0,50-0,55.
Удельный расход тепла (расход тепла топлива на 1т стали) зависит от многих факторов, и прежде всего от емкости печи. По мере увеличения садки печи уменьшаются относительные потери тепла на нагрев футеровки, на отвод тепла с охлаждающей водой и другие потери; в результате удельный расход тепла снижается с 840 для 10-20-т печей до 210МДж/т для 900-т печей.
Применяемое для отопления мартеновских печей топливо различают: а) по физическому состоянию: жидкое (мазут, смола), газообразное (доменный, коксовый, природный газы), твердое (каменноугольная пыль);
6) по теплоте сгорания: низкокалорийное (доменный газ, теплота сгорании 3,78— 4,2 МДж/мэ) и высококалорийное (мазут 39,9-42 МДж/кг, коксовый газ 16,8— 18,0 МДж/мэ, сухой природный газ типа саратовского 33,6—35,2 МДж/м3, жирный природный газ типа грозненского 63 МДж/мэ).
Для успешного проведения мартеновской плавки недостаточно подать в печь определенное количество тепла, необходимо еще, чтобы температура факела при сгорании топлива была достаточно высокой. Температура поверхности шлака в конце плавки составляет примерно 1650 °С. Чтобы тепло пламени достаточно интенсивно передавалось металлу, температура факела должна быть не ниже 1750 °С.
Практическая температура факела tпр=кtкал, где tкал - калориметрическая температура горения топлива; k -пирометрический коэффициент, зависящий от отдачи тепла нагреваемым предметом, от потерь тепла в окружающую среду и от степени диссоциации продуктов сгорания.
Величина коэффициента k близка к 0,7. Следовательно, калориметрическая температура горения топлива в мартеновской печи должна быть не ниже 2400 °С (1700 : 0,7 ~ 2430 °С). При этом следует иметь в виду, что для обеспечения полноты сгорания воздух для сжигания топлива подают с некоторым избытком, равным обычно 10—20% (так называемый "коэффициент избытка воздуха" α. = 1,1+1,2).
Калориметрическая температура горения доменного газа низка (~2250 °С), температура факела нагретого доменного газа в горячем воздухе ниже 1600 °С, следовательно, нагреть ванну до нужной температуры при отоплении мартеновской печи одним только доменным газом невозможно. Повысить температуру можно, заменяя воздух кислородом.
Обычно доменный газ применяют в качестве топлива для мартеновских печей только в смеси с другими, более калорийными видами топлива (коксовым газом, мазутом, природным газом).
Наиболее распространены в качестве топлива для мартеновских печей природный газ, мазут и смешанный газ (смесь коксового и доменного газов).
Смешанный газ содержит, %: 16-20 СО, 7-9 СО2, 20-30 Н2, 8—12 СН4, 30—40 N2; состав газа и его теплота сгорания меняются в зависимости от соотношения долей, входящих в состав смеси доменного и коксового газов. Для улучшения светимости факела к смешанному газу обычно добавляют небольшое количество карбюратора (мазута или смолы). Калориметрическая температура горения нагретого смешанного газа в нагретом воздухе составляет около 2600 °С, что обеспечивает получение высокотемпературного факела.
Смешанным газом отапливают печи заводов, имеющих в своем составе доменный и коксохимический цехи. В тех случаях, когда доменного и коксового газов для отопления всех мартеновских и других печей завода не хватает, используют природный газ и мазут.
Природным газом или мазутом отапливают также печи заводов, в составе которых нет доменных и коксохимических цехов. Мазут - первоклассное топливо для мартеновских печей, он дает яркосветящийся настильный высокотемпературный факел (калориметрическая температура горения мазута 2650 °С). Обычно мазут содержит 83-85 % С и 10-11 % Н3, остальное - влага, зола и сера. Содержание серы в мартеновских мазутах колеблется в пределах 0,5—0,7 %. Сернистые мазуты (3 % 8 и более) в мартеновском производстве применяют редко, так как сера из топлива переходит в металл и ухудшает его качество.
Перед подачей к форсункам мазут нагревают до 70-800 С. Распыление мазута осуществляют сжатым воздухом, подаваемым под избыточным давлением 0,5-0,7 МПа, или перегретым до 300-350 °С паром под избыточным давлением 1,1-1,2 МПа.
По мере развития газовой промышленности большое число печей в нашей стране было переведено на отопление природным газом. Природные газы основных месторождений СНГ примерно на 95% состоят из метана СН4. Факел природного газа малосветящийся, и для повышения его светимости одновременно с газом в печь вводят некоторое количество (до 30-40%) мазута. Добавка мазута не только повышает светимость факела, но и утяжеляет его, делает факел более настильным.
Повышать светимость факела пламени природного газа можно также конвертированием, нагревая часть его при недостатке воздуха. Метан при нагревании разлагается ("реформируется") с выделением большого количества сажистых частиц (СН4 = С + 2Н2), что обеспечивает получение светящегося факела.
Природный газ - "удобное" топливо: не содержит ядовитых веществ, вредных примесей, дешев, легко транспортируется. Ряд мартеновских печей оборудован газо-кислородными горелками, при помощи которых газ вводят в печь через свод, и высокотемпературный факел природного газа, горящего в кислороде, направляют непосредственно на шихту. Скорость плавления шихты при этом значительно возрастает.
Калориметрическая температура горения холодных мазута и природного газа в нагретом воздухе составляет 2600-2650 °С.
Таким образом, такие высококалорийные виды топлива, как мазут и природный газ дают высокотемпературный факел без подогрева топлива (но с подогревом воздуха).
Вид топлива, следовательно, оказывает влияние на конструкцию печи, которая при отоплении высококалорийным топливом становится значительно проще: вместо двух пар регенераторов (для подогрева газа и воздуха) достаточно иметь только одну пару регенераторов (для подогрева воздуха), соответственно вдвое уменьшается число шлаковиков, отсутствуют газовые вертикальные каналы, упрощается конструкция головки и система перекидки клапанов, легче осуществить автоматизацию печи.
Периоды мартеновской плавки
Мартеновскую плавку можно условно разделить на несколько периодов: 1)заправка печи; 2)завалка шихты; 3)плавление шихты; 4) кипение ванны (доводка), раскисление и легирование; 5) выпуск плавки.
Заправка. После выпуска плавки печь осматривают и исправляют замеченные неполадки. Особенно внимательно осматривают подину печи. За время плавки те части задней и передней стенок, а также откосов печи, которые соприкасались со шлаком, подвергаются определенному воздействию этого шлака и поэтому обычно нуждаются в профилактическом ремонте. При помощи заправочных машин на эти места набрасывают заправочные материалы (обычно доломит или магнезит). Эту операцию называют заправкой печи и проводят обязательно после каждой плавки. Операция заправки печи в зависимости от состояния подины, размеров печи и условий проведения операции продолжается от 10 до 30 мин.
Завалка и плавление шихты. Эти операции решающим образом влияют на производительность печи ( 2/3—3/4 продолжительности всей плавки), поэтому в зависимости от конкретных условий производства принимают необходимые меры для ускорения процесса завалки, рационального размещения на подине заваливаемых твердых составляющих (стального лома, чушкового чугуна, железной руды, известняка и т. п.), заливки жидкого чугуна и обеспечения необходимого теплового режима печи.
Кипение, раскисление и легирование. Этот период часто называют также периодом рафинирования. Момент начала периода определяется на основании следующих признаков: 1) металл должен быть полностью расплавлен и нагрет до температуры, предусмотренной технологической инструкцией для данной марки стали; 2) шлак должен быть сформирован. В зависимости от содержания углерода принимают решение о вводе в ванну порции железной руды или о продувке ванны. Стадию плавки, в процессе которой в результате введения железной руды или продувки происходит интенсивное кипение ванны, часто называют полировкой. В результате скачивания шлака из ванны удаляется фосфор, по ходу полировки вследствие подсадок извести постепенно формируется высокоосновной шлак (основность возрастает - 1,5—2,0 до 2,5—4,0) и повышается температура ванны. Это создает благоприятные условия для удаления серы. Через некоторое время содержание углерода приближается к требуемому, начинается следующая стадия плавки, называемая доводкой, в процессе которой должны достигаться заданные состав и температура ванны.
Кипение ванны, продолжающееся во время доводки, обеспечивает уменьшение содержания газов и включений в металле, способствует выравниванию его состава и температуры. За 10— 40 мин (в зависимости от марки стали, вместимости печи и др.) до момента раскисления подсадка железной руды или продувка панны прекращаются. Эта небольшая, по продолжительности стадия плавки называется периодом чистого кипения. Кипение ванны прекращается в момент ввода в нее раскислителей и легирующих.
Дата добавления: 2018-04-05; просмотров: 808; Мы поможем в написании вашей работы! |
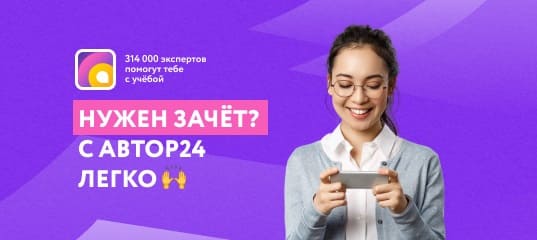
Мы поможем в написании ваших работ!