Химический состав и свойства бронз
Высокой электропроводности и прочности
Материал | Химический состав (Сu остальное), мас. % | sВ, МПа | δ, % | Электросопротивление, мкОм.см |
Медь | - | 220 | 45 | 1,72 |
БрСр | 0,1Ag | 440 | 14 | 1,85 |
БрКд | 1,0Cd | 420 | 17 | 2,28 |
БрМг0,3 | 0,3Mg | 530 | 3 | 2,0 |
БрМг0,5 | 0,5Mg | 540 | - | 3,0 |
БрМг0,8 | 0,8Mg | 650 | - | 3,7 |
БрХ | 0,7Cr | 450 | 19 | 2,03 |
БрЦр0,4 | 0,4Zr | 480 | 17 | 2,08 |
БрХЦр | 0,7Cr; 0,05Zr | 500 | 24 | 2,04 |
БрНБТ | 1,5Ni; 0,3Be; 0,1Ti | 820 | 5 | 3,97 |
БрНХК | 2,5(Со+Ni); 0,7Сг; 0,7Si | 800 | 17 | 3,72 |
Бронзы высокой электропроводности по типу упрочнения разбивают на две группы:
а) сплавы, упрочняемые холодной деформацией;
б) термически упрочняемые сплавы.
К первой группе принадлежат сплавы систем Сu-Ag, Сu-Сd и Сu-Мg. Бронза БрСр, содержащая 0,07¸0,12 % Аg, однофазна, так как серебро растворяется в меди в больших количествах. Высокой прочностью и электропроводностью отличается кадмиевая бронза, содержащая 0,9¸1,20 % Сd. Растворимость кадмия в меди составляет 3 % при 549 °С и уменьшается до 0,5 % при комнатной температуре. Однако упрочнение кадмиевой бронзы выделениями β-фазы (СdCu2) незначительно. Кадмиевая бронза характеризуется способностью к искрогашению и поэтому применяется для изготовления контактных проводов электрифицированного транспорта, коллекторных шин, электродов сварочных машин, разрывных контактов и т.п. изделий.
|
|
Растворимость магния в меди уменьшается от 2,8 % при эвтектической температуре (722 °С) до 1,2 % при 400 °С. Выделяющаяся при распаде твёрдого раствора фаза Сu2Мg сильно ухудшает деформируемость сплавов при холодной обработке и исключает возможность эффективного наклёпа. Поэтому магниевые бронзы содержат до 1 % Мg (см. табл. 1.7). Магниевую бронзу БрМг0,3 рекомендуют как заменитель кадмиевой бронзы в производстве контактных колец и коллекторных пластин. Бронзы БрМг0,5 и БрМг0,8 применяют для изготовления кабелей и троллейных проводов.
Остальные бронзы, приведенные в табл. 1.7, относят к термически упрочняемым. Хромовые бронзы, содержащие обычно от 0,4 до 1,0 % Сr, обладают высокой электропроводностью после закалки и старения. Хром мало растворим в меди: 0,65 % Сr при 1072 °С и 0,02 % Сr при 400 °С; поэтому после старения структура хромовых бронз представлена почти чистой медью и небольшим количеством выделений хрома. При такой структуре сохраняется высокая электропроводность, составляющая около 80 % от электропроводности меди. Хромовые бронзы имеют высокое сопротивление ползучести, хорошо сопротивляются износу. Они широко применяются для изготовления электродов аппаратов контактной сварки и коллекторов электромоторов.
|
|
Хорошими свойствами обладают сплавы, легированные 0,10¸0,8 % циркония. Ещё более высоким сочетанием свойств отличаются бронзы, одновременно легированные и хромом, и цирконием. Введение сотых долей процента циркония в сплавы меди с 0,1¸1,0 % хрома приводит к существенному повышению температуры рекристаллизации, прочности и жаропрочности. Структура этих сплавов в состаренном состоянии состоит из матрицы, представленной почти чистой медью, и выделений хрома. Находящийся в твердом растворе цирконий уменьшает диффузионную подвижность хрома, что и обусловливает высокую жаропрочность сплавов Сu-Сr-Zr. Благодаря высокой тепло- и электропроводности в сочетании с высокой жаропрочностью хромоциркониевая бронза БрХЦр (см. табл. 1.7) – это наиболее распространенный материал для электродов контактной сварки.
К сплавам с интерметаллидным упрочнением относятся бронзы БрНБТ, БрКБ, БрКХКо и БрНКХ. У этих бронз самые высокие прочностные характеристики, но вместе с тем и в 1,5¸2раза большее удельное электросопротивление по сравнению с медью, серебряной, кадмиевой и хромциркониевой бронзами (см. табл. 1.7). К этой же группе принадлежат сплавы Мц2 и Мц3 . Высокая жаропрочность сплава Мц2 обусловлена интерметаллидом Ni2Si, а сплава Мц3 – NiВе.
|
|
Все дисперсионно-твердеющие бронзы высокой электропроводности применяют в термически упрочненном состоянии. Их закаливают с температур 930¸1000 °С (выдержка 2 ч в воде), а затем подвергают старению при 440¸500 °С в течение 2¸6 ч. В некоторых случаях используют термомеханическую обработку, вводя между закалкой и старением холодную деформацию.
Принципы выбора режимов отжига меди и её сплавов
При разработке технологии термической обработки меди и её сплавов учитывают две их особенности: высокую теплопроводность и активное взаимодействие с газами при нагреве. При нагреве тонких изделий и полуфабрикатов теплопроводность имеет второстепенное значение. При нагреве массивных изделий высокая теплопроводность меди является причиной более быстрого и равномерного их прогрева по всему сечению по сравнению, например, с титановыми сплавами.
В связи с высокой теплопроводностью при упрочняющей термической обработке медных сплавов не возникает проблемы прокаливаемости. При используемых на практике габаритах полуфабрикатов и изделий они прокаливаются насквозь.
|
|
Медь и сплавы на её основе активно взаимодействуют с кислородом и парами воды при повышенных температурах, по крайней мере, более интенсивно, чем алюминий и его сплавы. В связи с этой особенностью при термической обработке полуфабрикатов и изделий из меди и её сплавов часто применяют защитные атмосферы, в то время как в технологии термической обработки алюминия защитные атмосферы встречаются редко.
Отжиг меди и её сплавов проводят в целях устранения тех отклонений от равновесной структуры, которые возникли в процессе затвердевания или в результате механического воздействия либо предшествующей термической обработки.
Гомогенизационный отжиг, направленный на устранение внутрикристаллической (дендритной) ликвации, заключается в нагреве слитков до максимально возможной температуры, не вызывающей оплавления структурных составляющих сплавов. Ликвационные явления в латунях развиваются незначительно, и нагрев слитков под горячую обработку давлением достаточен для их гомогенизации. Основными сплавами меди, нуждающимися в гомогенизационном отжиге, являются оловянные бронзы, так как составы жидкой и твердой фаз в системе Cu-Sn сильно отличаются, в связи с чем развивается интенсивная дендритная ликвация.
В результате гомогенизацнонного отжига повышается однородность структуры и химического состава слитков (рис. 1.18). Гомогенизационный отжиг – одно из условий получения качественного конечного продукта.
Дата добавления: 2018-04-04; просмотров: 602; Мы поможем в написании вашей работы! |
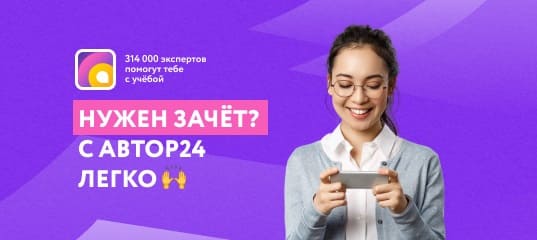
Мы поможем в написании ваших работ!