Объемная и листовая штамповка
При горячей объемной штамповке материал заготовки, деформируясь под давлением заполняет полость штампа (рис. 3.1,д). Течение металла ограничивается поверхностями полостей и выступов в штампе. По сравнению с ковкой штамповка имеет ряд преимуществ: возможность получения сложных поковок без напусков и в три четыре раза меньшими допусками; высокая производительность и более низкая трудоемкость процесса.
Однако штампы являются дорогим инструментом, поэтому штамповку применяют в серийном и массовом производстве. Наиболее рационально штамповкой получать поковки массой 20-30кг.
В зависимости от конструкции штампов штамповка делится на открытую и закрытую. При открытой штамповке образуются переменный зазор между нижней и верхней половинками штампа. В этот зазор вытесняется заусенец (облой), при этом полость штампа целиков заполняется металлом. Открытой штамповкой получают поковки всех типов.
При закрытой штамповке полость штампа в процессе деформирования остается закрытой, заусенец при этом не образуется. Объемы заготовки и поковки должны быть строго равны. При закрытой штамповке металл деформируется в условиях всестороннего неравномерного сжатия. Это позволяет получать большие степени деформации и штамповать малопластические сплавы. К закрытой штамповке относятся штамповка выдавливанием и прошивкой. Технологический процесс штамповки определяется конфигурацией и размерами деталей. Разработку чертежа поковки выполняют в следующей последовательности:
|
|
– выбор поверхности (плоскости, разъема штампа);
– установление припусков и допусков;
– установление штамповочных уклонов на вертикальной стенки;
– установление радиусов закруглений на пересекающиеся поверхности;
– проверка возможности изготовления изделия из нескольких частей с последующей их сваркой;
В целом при конструировании поковок стараются обеспечить наиболее простой разъем в штампах, удобства извлечения поковки, минимальные припуски и допуски. При этом пользуются справочными данными, нормалями и ГОСТами.
Исходной заготовкой для штамповки в большинстве случаев является прокат (сортовой, профильный, периодический).
Массу заготовки определяют: Gзаг=Gпок+GЗ + Gуг, где GЗ – масса заусенца : GЗ = (0,75 – 0,8)fзкPп, Pп – периметр поковки в плоскости разъема; fзк – площадь поперечного сечения заусенечной канавки. Массу угара берут Gу=0,5-2%. При закрытой штамповке массу заусенца не учитывают. Размеры заготовок рассчитываются в зависимости от способа штамповки и вида ручьев.
Штамповка выполняется на штамповочных паровоздушных молотах, кривошипно-горячештамповочных прессах (ГКШП) и горизонтально-ковочных машинах (ГКМ). При штамповке на молотах поковки простой формы получают в штампах с одной полостью, т.е. в одноручьевом штампе. Для получения поковок сложной формы используют заготовки из профильного и периодического проката или предварительно подготовленные ковкой, вальцовкой в ковочных вальцах.
|
|
Однако чаще всего сложные поковки получают в многоручьевых штампах. Ручьи таких штампов подразделяют на заготовительные и штамповочные. К первым относятся протяжной, подкатной, пережимной, формовочный, гибочный и т.д. Ко вторым – предварительный (черновой) и окончательный (чистовой).
При выборе ручьёв и переходов при открытой штамповке на КГШМ необходимо учитывать следующие особенности:
- применение подкатных и протяжных ручьёв на прессе нерационально из-за постоянства хода ползуна пресса;
- при штамповке на прессе металл хуже, чем на молоте заполняет рельеф формы по высоте. Поэтому для обеспечения формования процесс штамповки проводят в два-три перехода, например в осадочном, формовочном окончательном ручьях.
На КГШП широко применяется штамповка выдавливанием (клапаны, тонкостенные чашки). Штамповка в закрытых штампах ведется в два-три перехода. Конструкция закрытых штампов исключает образование облоя. Такие штампы бывают весьма сложной конструкции.
|
|
При штамповке на ГКМ основными операциями является высадка и прошивка. Высадкой получают поковки болтов, рычагов и др. Во избежание продольного изгиба заготовки берутся при определенном соотношении L/D. При высадке в одном ручье L ≤ (2,5-3)D. При многопереходной высадке L ≤ 12D. Прошивкой на КГМ получают кольца, фланцы и др. При этом применяют различные ручьи: прошивочные, формовочные, отрезные и т.д. Основные параметры и размеры штамповочных молотов, КГШП, ГКМ определяются ГОСТами.
Наряду с обычной штамповкой применяют специализированные процессы получения поковок:
- штамповка в ковочных вальцах и ротационноковочнных машинах;
- раскатка и накатка колец, шестерён и др.;
- высадка на электровысадочных автоматах.
Для получения поковок из высоколегированных и труднодеформируемых сплавов применяют подогреваемые и изотермические закрытые штампы.
После штамповки поковки подвергаются отделочным операциям: обрезке заусенцев, правке, очистке от окалины, термообработке, калибровке, контролю качества. В последние годы уделяется большое внимание автоматизации и механизации штамповки. Созданы установки с программным управлением, автоматизированные комплексные линии и роботокомплексы.
|
|
Холодную объёмную штамповку ведут без нагрева заготовок. Разновидностью объёмной штамповки является выдавливание, высадка, формовка.
Выдавливание осуществляется на кривошипных или гидравлических прессах в штампах, имеющих пуансон и матрицу. Исходной заготовкой является часть прутка или листа. Существуют различные схемы выдавливания: прямое (получают болты, клапаны и т.п.), обратное (получают полые детали), боковое (получают тройники, крестовины и т.д.), комбинированное (сложные изделия).
Основной особенностью выдавливания является возможность получения высоких степеней деформации без разрушения заготовки, которые можно характеризовать показателем К = F0/F1. Для мягких металлов К>100.
Возможность получения больших деформаций объясняется тем, что при выдавливании имеет место всестороннее неравномерное сжатие, при котором скользящие относительно друг друга атомные слои дополнительно прижимаются друг к другу, что затрудняет развитие трещин. Усилие деформирования при выдавливании определяют как произведение удельного усилия на площадь поперечного сечения. Приближённо удельное усилие р выдавливания определяют по формуле:
р = а∙σв∙lnК,
где а – коэффициент, равный 3-5, зависит от свойств, условий деформирования. Для уменьшения усилия применяют смазки, выбирают схему формования, при которой исключается образование застойных зон и уменьшается влияние трения.
Холодная высадка выполняется на высадочных автоматах. Исходным материалом является пруток или проволока. Штампуют заготовки диаметром 0,5-40 мм и различные детали с местным утолщением (заклёпки, болты, винты, гвозди, шарики, ролики, накидные гайки, звёздочки и т.д.). При этом резьбу получают на автоматах накаткой. Высадочные автоматы имеют производительность 20-400 дет/мин. Средний коэффициент использования металла 95%.
Холодная формовка производится аналогично горячей штамповке. Однако при холодной штамповке возникают более высокие усилия, материал имеет низкую формуемость, вследствие его упрочнения и действия сил трения. Применяется холодная штамповка для получения в основном деталей из цветных металлов.
Волочение,прессование.
Волочение – вид обработки металлов давлением, при котором заготовка в холодном состоянии протягивается через сужающееся отверстие – волоку (рис. 13.4). Выполняют операцию волочения через ряд волок с постепенно сужающимися отверстиями. На каждом технологическом этапе волочения происходит наклеп металла, поэтому между переходами для снятия упрочнения делают термическую операцию отжига материала с последующим травлением окалины. Волочением обрабатывают сталь, цветные металлы и их сплавы. Изготавливают проволоку, калиброванные прутки и тонкостенные трубы различного профиля. Получаемые изделия имеют точные размеры и высокую чистоту поверхности.
Волоки, работающие в жестких условиях, изготавливают из инструментальных сталей или твердого металлокерамического сплава, а для волочения тонкой проволоки – из технических алмазов. С целью уменьшения трения, повышения стойкости инструмента и улучшения отвода тепла при волочении применяют жидкие и твёрдые смазки (минеральное масло, эмульсии, мыло, порошки графита, меди, молибдена).
Волочильные станы состоят из станины с держателем для волоки и тянущего устройства. При волочении протягиваемый металл движется прямолинейно (цепной, реечный стан) или наматывается на барабан.
Прессование – вид обработки давлением, при котором нагретый металл выдавливается из замкнутой полости через отверстие в матрице 2 в условиях всестороннего сжатия (рис. 13.5), позволяющих деформировать материалы с низкой пластичностью (специальные стали, чугун, некоторые цветные металлы и сплавы). Прессуемый металл принимает форму прутка простого или сложного сечения копирующего форму отверстия в матрице. Прессование проводится при температурах соответствующих горячей обработки давлением.
Метод прямого прессования – металл выдавливается в направлении движения пуансона 4 (рис. 13.5,а), обратное прессование – металл движется навстречу движению пуансона (рис. 13.5,б). Из заготовки 3 прутки 1, сплошного сечения получают любым методом прессования, трубы – только прямым прессованием.
Инструмент (матрица (пресс-шайба) 2, пуансон 4, камера прессования) работает в жестких условиях (большое давление, высокая температура). Поэтому изготовляют его из дорогостоящих инструментальных жаропрочных сталей и сплавов. Для снижения износа и увеличения срока службы прессового инструмента обязательно применяют смазку: минеральные масла, графит, канифоль; при прессовании трудно деформируемых материалов жидкое стекло.
Дата добавления: 2018-04-04; просмотров: 1834; Мы поможем в написании вашей работы! |
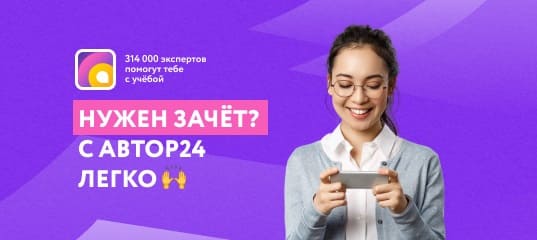
Мы поможем в написании ваших работ!