Закалка стали токами высокой частоты
Поверхностная закалка при нагреве токами высокой частоты.Нагрев токами высокой частоты (т.в.ч.), предложенный и разработанный проф. В.П.Вологдиным, является наиболее производительным и прогрессивным способом. При нагреве т.в.ч. можно закаливать детали разнообразных конфигураций, полностью автоматизировать процесс закалки.
Сущность нагрева т.в.ч. заключается в следующем. Если в переменное электромагнитное поле поместить замкнутый проводник электрического тока, то в проводнике возникают переменные, так называемые вихревые токи. Характерным является распределение тока по сечению проводника. Если постоянный ток распределяется при прохождении по проводнику равномерно по всему сечению, то распределение переменного тока по сечению проводника неравномерно. Плотность протекающего переменного тока значительно больше у поверхности, чем во внутренних слоях проводника. Такое неравномерное распределение переменного тока в проводнике называется поверхностным эффектом. Вследствие поверхностного эффекта проводник нагревается на определенную глубину от поверхности.
Нагрев т.в.ч. принципиально отличается от других способов нагрева – тепло возникает в самой детали, а при нагреве в печах, соляных ваннах и газовым пламенем тепло распространяется от поверхности к сердцевине путем теплопроводности.
В связи с большой скоростью нагрева (в течение нескольких секунд) для завершения всех превращений в стали необходима температура, значительно (на 100-200°С) превышающая нормальную температуру закалки при нагреве в печах. Но в связи с отсутствием выдержки при температуре закалки такая высокая температура не вызывает роста зерна стали.
|
|
По сравнению с обычной закалкой сталь, закаленная при нагреве т.в.ч., имеет следующие преимущества: более высокая твердость, более мелкая микроструктура, более высокая износостойкость, более высокая прочность при относительно меньшем понижении вязкости, более высокий предел выносливости.
Поверхностную закалку нагревом т.в.ч. проводят различными способами – в зависимости от размера и формы детали и предъявляемых к ней требований.
При закалке небольших деталей применяют одновременный нагрев и охлаждение всей обрабатываемой поверхности. Наибольшее применение имеет душевое охлаждение. Для этого на внутренней поверхности индуктора имеются многочисленные отверстия, через которые, после окончания нагрева, на поверхность детали поступает вода.
Закалку деталей значительной длины проводят непрерывно – последовательным способом. Непрерывно – последовательно нагревается и охлаждается вся поверхность детали.
|
|
Если необходимо закалить отдельные части детали, то целесообразно применять способ последовательной закалки, при котором обрабатываемая поверхность нагревается и охлаждается по частям.
После закалки для уменьшения возникающих внутренних напряжений детали подвергают низкому отпуску (160 - 200°С).
Для точной установки детали в индукторе и обеспечения определенного одинакового нагрева и охлаждения каждой нагреваемой детали, от чего зависит качество закалки, применяют специальные приспособления, установки, станки-полуавтоматы и автоматы различных конструкций.
Поверхностная закалка при нагреве пламенем.При этом способе закалки нагрев поверхности детали осуществляют пламенем. Наиболее часто используют ацетилено - кислородное пламя, температура которого 3150°С.
43. Цементация стали.
Под цементацией понимают процесс насыщения поверхности углеродом. Ее целью является получение твердой и износостойкой поверхности.
Цементации обычно подвергают низкоуглеродистые стали, содержащие 0,1…0,18 (иногда до 0,30) % С. После обработки поверхностные слои содержат 0,8…1,0 % С, а сердцевина изделий остается вязкой. На цементацию детали обычно поступают после механической обработки. Если цементации следует подвергать часть поверхности детали, то нецементируемые участки защищают тонким слоем меди или изолируют специальными обмазками, состоящими из смеси огнеупорной глины, песка и асбеста, замешанных на жидком стекле или других связках.
|
|
Цементацию проводят в области существования аустенита из-за малой растворимости углерода в феррите. Как правило, цементацию осуществляют при температурах 920…950 °С. Когда активность углерода в газовой фазе велика, концентрация растворенного углерода в аустените достигает предела насыщения (определяемого на диаграмме линией SE) и на поверхности изделий образуется слой цементита. В реальных условиях слой цементита на поверхности образуется очень редко и обычно цементованный слой состоит из аустенита почти насыщенного углеродом при температуре цементации. При охлаждении он распадается на феррит и цементит. Практически всегда в цементованном слое концентрация углерода убывает от поверхности к сердцевине изделия. У поверхности имеется заэвтектоидная зона, состоящая из перлита и вторичного цементита. Эта зона постепенно переходит в эвтектоидную - состоящую из пластинчатого перлита и, наконец, в доэвтектоидную зону, состоящую из перлита и феррита. В этой зоне доля феррита возрастает по мере приближения к сердцевине.
|
|
Хотя обычно средняя концентрация углерода в поверхностном слое и составляет 0,8…1,0 % С, иногда для повышения сопротивления контактной усталости ее по-вышают до 1,1…1,2 %. Более высокое содержание углерода нецелесообразно, так как при этом повышается хрупкость цементованного слоя.
Если цементируют стали, легированные карбидообразующими элементами, то может образовываться двухфазный слой, состоящий из аустенита и глобулярных карбидов. Несмотря на то, что концентрация углерода в легированном аустените ниже, чем в обычном, средняя концентрация углерода в сталях, легированных хромом, марганцем, вольфрамом, молибденом и ванадием достигает 1,8…2 %. На скорость диффузии легирующие элементы влияют неодинаково. Так, например, вольфрам и хром ее уменьшают, а никель - увеличивает.
44 Азотирование.
Азотированием называют процесс диффузионного насыщения поверхностного слоя стальных изделий азотом (N2). Осуществляется азотирование путем нагрева деталей в потоке аммиака (NH3) при 480-6500С. Тонкий азотированный слой очень тверд, износостоек и хорошо сопротивляется коррозии.
Кроме того, азотирование создает на поверхности изделий остаточные напряжения сжатия, повышающие предел выносливости и долговечность.
Сущность процесса азотирования заключается в разложении NH3 на N2 и H2: 2NH3 =2N+3H2. Активные (в момент выделения) атомы азота проникают в решетку a-Fe и диффундирует в ней. В результате получается ряд структурных составляющих и переходных структур. В начале при азотировании получается a -фаза, т.е. твердый раствор N2 в феррите, который при температуре 5910С растворяет до 0,42% N, а при атмосферной температуре – только до 0,015%N.
При повышении содержания N образуется g´- фаза, содержащая 5,7-6,1% N и представляющая собой твердый раствор на основе нитрида Fe (Fe4N).
Наконец, при дальнейшем повышении содержания азота образуется ε - фаза – твердый раствор на базе нитрида Fe (Fe3N), содержащая 8,0-11,2% азота. Наибольшее содержание в ней азоту отвечает нитриду Fe2N (11,2%).
При температурах выше 5910С образуется g - фаза, представляющая собой твердый раствор азота в g-Fe. Понижение температуры приводит к эвтектоидному распаду. Азотистый эвтектоид состоит из a и g '- фаз и содержит 2,35% N.
Твердость азотированного слоя простой углеродистой стали невелика, поэтому азотированию подвергают среднеуглеродистые легированные стали.
При азотировании легированных сталей образуются нитриды специальных элементов: Al, Ti, V, Cr, Mo, W и Mn: AlN, TiN, VN и т.д., которые придают азотированному слою очень высокую твердость.
Хорошие результаты дает азотирование нержавеющей и жароупорной стали. Замечательные антифрикционные свойства обнаруживает азотированная поверхность графитизированной стали, т.е. стали, имеющей в структуре графит. Она отличается высокой твердостью и износостойкостью; вместе с тем, графит удерживает смазку и понижает коэффициент трения, что очень важно для гильз, цилиндров, втулок и подшипников.
Азотированные детали обладают хорошей сопротивляемостью действию переменных напряжений и обладают высоким пределом выносливости, коррозионной стойкостью. Недостатком процесса азотирования является чрезмерная длительность процесса – 50-100 часов и необходимость применения легированных сталей.
Цианирование.
Процесс азотирования включает несколько последовательно выполняемых операций. Сначала проводят операцию улучшения, состоящую в закалке и высоком отпуске. Как правило, закалку проводят при температурах 800…850 °С с охлаждением в воде или масле. Отпуск проводят при температуре, превышающей температуру последующего азотирования. Структура стали после такого отпуска - сорбит. Применяют отпуск не только для устранения коробления, но и для получения твердости, допускающей обработку резанием. После улучшения проводят механическую обработку детали резанием и ее шлифование для придания необходимых размеров.
На следующем этапе обработки участки, не подлежащие азотированию, защищают тонким слоем олова или жидкого стекла и лишь затем проводят азотирование в течение 24…96 ч. После азотирования осуществляют окончательное шлифование и доводку изделия.
Иногда для ускорения применяют двухступенчатый процесс; сначала азотируют при 500…520 °С, а затем при 540…600 °С.
Применение двухступенчатого азотирования уменьшает длительность обработки, но не приводит к снижению твердости. Охлаждение деталей после азотирования проводят вместе с печью в потоке аммиака.
Значительное сокращение времени азотирования (в 2…3 раза) получается при азотировании в «тлеющем разряде», т. е. когда обрабатываемую деталь, находящу-юся в разреженной атмосфере, содержащей азот, подключают к отрицательному электроду - катоду. В качестве анода служит контейнер. Между катодом и анодом возникает тлеющий разряд. В рабочем пространстве увеличивается концентрация атомарного азота, деталь нагревается до температуры насыщения в результате бом-бардировки ионами газа.
Еще более быстрым является азотирование в жидких средах - расплавленных цианистых солях (тенифер-процесс).
Как и при газовом азотировании, так и при тенифер-процессе твердость азотированного слоя составляет 300…350 HV для углеродистых сталей, а для легированных может меняться от 600 до 1100 HV. При жидкостном азотировании не происходит ни коробления деталей, ни заметного изменения их размеров. Недостатками этого процесса являются токсичность и высокая стоимость цианистых солей.
Диффузионное легирование.
Диффузионное легирование может проводиться одновременно одним легирующим элементом ( аналогия с цементацией и азотированием), двумя ( аналогия с цианированием), тремя и более элементами. Степень насыщения в основном зависит от температуры процесса легирования, активности окружающей среды и времени выдержки. [2]
Процесс диффузионного легирования аналогичен цементации, азотированию и цианированию. Он заключается в том, что в сталь или чугун при высоких температурах внедряются атомы одного или другого металла, в результате чего изменяется химический состав верхних слоев изделия или детали. [3]
Процесс диффузионного легирования протекает, как и процесс цементации, в трех самостоятельных, но и взаимосвязанных между собой областях: 1-я область - среда, окружающая деталь; 2-я - граница раздела окружающей среды и металла и 3-я - верхние слои металла. [4]
При диффузионном легировании возникают трудности в получении тонких легированных слоев и достаточно резких р-и-пере-ходов. [5]
При диффузионном легировании GaAs литием удельное сопротивление кристалла n - типа возрастает до десятка ом см. В результате термообработки при высоких температурах удельное сопротивление снижается до 0 2 ом см и кристалл становится р-типа. Предполагается, что литий может входить в решетку как по междоузлиям, так и путем замещения атомов галлия. Эти два вида дефектов могут образовать комплекс LijLiQa, обладающий акцепторными свойствами. [6]
Медь и ее сплавы
Медь - химический элемент I группы побочной подгруппы периодической системы, порядковый номер 29, атомный вес 63,54. Химический знак - Сu. Она носит латинское название «купрум», которое происходит от наименования острова Кипр, богатого залежами медьсодержащих ископаемых. Это один из древнейших химических элементов-металлов. Он совместно с золотом и серебром был известен в 7 - 6 тысячелетии до нашей эры.
Массовая доля данного элемента в земной коре составляет 0,01 %. Медь содержится во многих сульфидных рудах: халькопирите (медный колчедан) CuFeS2, халькозине (медный блеск) Cu2S, ковеллине CuS. Существуют оксидные медные руды, например, куприт Сu2О, и гидрокарбонатные, такие как малахит СuСО3∙Сu(ОН)2.
Медь кристаллизуется в гранецентрированной кубической решетке. Она имеет розовато-красный цвет. Это тяжелый и высокоплавкий металл, так плотность меди составляет 8,9 г/см3; а температура плавления - 1084,5 °С. Важнейшимифизико-механическимисвойствами данного металла являются значительные электро- и теплопроводность, по которым он после серебра занимает второе место. Так удельное сопротивление меди равно 0,0178 Ом×м, а теплопроводность l = 340ккал/м×град×ч, Медь высокопластична и способна подвергаться пластической деформации в холодном и нагретом состояниях, хорошо сопротивляется коррозии. Чистый металл диамагнитен. Медь легко образует сплавы со многими металлами с широким диапазоном различных свойств.
По своей химической природе медь - малоактивный металл. Он легче всего взаимодействует с галогенами при обычной температуре, с кислородом и серой реагирует только при нагревании, образуя оксид и сульфид соответственно. С водородом и углеродом медь не взаимодействует.
Сухой воздух практически не вызывают окислительного разрушения металла. Незначительное влияние на химическую стойкость меди оказывают ряд органических кислот, спирты и фенольные смолы.
Поскольку медь находится в ряду напряжений после водорода, кислоты окисляют ее лишь за счет аниона: она растворяется только в азотной НNО3 (любой концентрации) и концентрированной H2SO4, но не реагирует с хлороводородной (соляной) и разбавленной серной кислотами. Также медь не взаимодействует как с чистой пресной, так и с морской водой и растворами щелочей.
Металл плохо сопротивляется действию аммиака, аммиачных солей и щелочных цианистых соединений. Коррозию меди вызывают также хлористый аммоний и окислительные минеральные кислоты. На воздухе во влажной атмосфере, содержащей диоксид углерода, она покрывается плотной серо-зеленой пленкой основного карбоната - Cu(OH)2∙CuCO3.
Постоянными примесями в меди являются висмут, сурьма, мышьяк и др. Все они понижают ее электропроводность. Температура плавления, плотность, пластичность и другие свойства металла значительно изменяются от присутствия в нем примесей.
Висмут и свинец образуют с медью легкоплавкие твердые растворы с ограниченной растворимостью (эвтектики), которые при кристаллизации затвердевают последними и располагаются по границам ранее выпавших зерен основного метала. При нагревании до температур, превышающих точки плавления эвтектик (270 и 327 °С соответственно), зерна меди разъединяются жидкой эвтектикой. Такой металл является красноломким и при прокатке в горячем состоянии разрушается. Красноломкость меди может вызываться присутствием в ней тысячных долей процента висмута и сотых долей процента свинца. При повышенном их содержании она становится хрупкой и в холодном состоянии.
Сера и кислород образуют с медью тугоплавкие эвтектики с точками плавления выше температур горячей обработки меди (1065 и 1067 °С). Поэтому присутствие небольших количеств серы и кислорода не сопровождается появлением красноломкости. Однако значительное повышение содержания кислорода приводит к заметному понижению механических, технологических и коррозионных свойств меди; она становится красноломкой и хладноломкой.
Медь, содержащая кислород, при отжиге ее в водороде или в атмосфере, содержащей водород, делается хрупкой и растрескивается. Это явление известно под названием «водородной болезни». Растрескивание меди в этом случае происходит в результате образования значительного количества водяных паров при взаимодействии водорода с кислородом меди. Водяные пары при повышенных температурах имеют высокое давление и разрушают медь. Наличие трещин в меди устанавливается путем испытаний на изгиб и кручение, а также микроскопическим методом. В меди, пораженной водородной болезнью, после полировки хорошо видны характерные темные включения пор и трещин.
Сера снижает пластичность меди при холодной и горячей обработке давлением и улучшает обрабатываемость резанием.
Железо растворяется в меди в твердом состоянии весьма незначительно. Под влиянием примесей железа резко снижаются электро- и теплопроводность меди, а также ее коррозионная стойкость. Структура меди под влиянием примесей железа измельчается, что повышает ее прочность и уменьшает пластичность. Под влиянием железа медь становится магнитной.
Алюминий и его сплавы
Алюминий имеет огромное значение в промышленности из-за высокой пластичности, большой тепло и электропроводности, слабой коррозии, т.к. образующая на поверхности пленка Al2O3 защищает металл от окисления. Из него делают тонкий прокат, фольгу, любой профиль прессованием и другими видами обработки давления. Из него изготавливают разного типа провода, применяют в электроаппаратуре.
Как конструкционный материал алюминий чаще всего применяется в сплавах со следующими легирующими элементами: Cu, Zn, Mg, Ni, Fe, Mn, Ti, Si, Cr, которые формируют упрочняющие зоны и фазы.
Сплав алюминия с медью называется дуралюминием (дюраль); сплав с кремнием – силумин – только литейный сплав. Сплав с марганцем – АМц одновременно повышает коррозионную стойкость; Ni, Ti, Cr, Fe повышает жаропрочность сплавов, затормаживая процесс диффузии; литий и бериллий способствуют возрастанию модуля упругости.
Все алюминиевые сплавы можно разделить на деформируемые (получают
лист, трубы, профиль, паковки, штамповки) и литейные – для фасонного литья.
Сплавы алюминия нашли широкое применение прежде всего в авиации,
автомобилестроении, судостроении и др.отраслях народного хозяйства.
Алюминиевые сплавы подразделяются на деформируемые и литейные. Порошковые материалы, композиты деформируются, а иногда льются.
Неупрочняемые сплавы Al – Mn (АМц) и Al – Mg (АМг). Это коррозион-
ностойкие материалы, идущие на изготовление бензо -, маслобаков, корпусов
судов.
Упрочняемые сплавы Al -Mg – Si (АВ, АД31, АД33) идут для изготовления лопастей и деталей кабин вертолетов, барабанов колес гидросамолетов.
Дуралюмины Al – Cu – Mg (Д1, Д16, Д18, Д19, ВД17, В93, В95, В96 и др.).
Дюраль содержит
от 2 до 4,5 Cu и, кроме того, он часто легируется Mg (~0.5%), Mn, Fe, Be, Si, Zn. Перечисленные элементы образуют ряд химических соединений, растворяемых в алюминии – матрице (CuAl2, Mg2Si) и нерастворимых Fe, Mn, Cu. Механические свойства после закалки и старения (отпуска) зависят от температуры закалки и старения, скорости охлаждения.
Высокопрочные сплавы Al – Zn – Mg – Cu (В93, В95, В96Ц) более прочны, чем дюралюминий, обладают лучшей коррозионной стойкостью и применяются для изготовления шпангоутов, лонжеронов, стрингеров. Алюминиевые сплавы часто применяются для изготовления поковок штамповок лопастей винта самолета, рам, поясов лонжеронов, крепежных деталей. Это сплавы АК1, АК6, АК8, АК4.
Жаропрочные алюминиевые сплавы системы Al – Cu – Mn (Д20, Д21) и Al – Cu – Mg – Fe – Ni (АК – 4 – 1) применяют для изготовления поршней, головок цилиндров, дисков, лопаток компрессоров и т.д., работающих при температурах до 300°С. Жаропрочность достигается за счет легирования Ni, Fe, Ti, (Д20, Д21, АК – 4 – 1).
Литейные алюминиевые сплавы применяются для изготовления литых заготовок. Это сплавы Al – Si (силумины), Al – Cu (дюрали), Al – Mg (Амг). К силуминам относятся сплавы Al – Si (AЛ – 2), Al – Si – Mg (АЛ – 4, АЛ – 9, АЛ – 34), которые упрочняются термообработкой. Силумины хорошо льются, обрабатываются резанием, свариваются, анодируются, пропитываются лаками.
Высокопрочные и жаропрочные литейные сплавы систем Аl – Cu – Mn (АЛ – 19), Al – Cu – Mn – Ni (АЛ – 33), Al – Si – Cu – Mg (АЛ – 3, АЛ – 5). Легированные Ti, Cr, Ni, Cl, Zn жаропрочны до 300°С, хорошо термообрабатываются. Из них изготавливают поршни, головки блока, цилиндров и т.п.
Коррозионностойкие литейные алюминиевые сплавы систем Al – Mg (АЛ8, АЛ27) и Al – Mg – Zn (АЛ24) хорошо льются и свариваются. Легирование Be, Ti, Zn вызывает изменение зерна. Они термообрабатываются.
Спеченный алюминиевый порошок (САП) получается прессованием (700 МПа) при температуре 500 – 600°С алюминиевой пудры. САП характеризуется высокой прочностью и жаропрочностью до 500°С.
Спеченные алюминиевые сплавы систем Al-Si-Ni (СОС 1), Al-Si-Fe
(СОС 2) иногда легированные Mn,Cr, Zn, Ti, V закаливаются, стареют, жаро-
прочны до 350°С.
Композиционные алюминиевые сплавы армируются борными волокнами (АД1, АД33, ВКА – 1, ВКА – 2), стальной проволокой (КАС-1, КАС-1А) прочны, гнутся, обладают большой ударной вязкостью, жаропрочностью, усталостью, прочностью.
Антифрикционные сплавы.
Антифрикционные сплавы предназначены для повышения долговечности трущихся поверхностей машин и механизмов. Трение происходит в подшипниках скольжения между валом и вкладышем подшипника. Поэтому для вкладыша подшипника подбирают такой материал, который предохраняет вал от износа, сам минимально изнашивается, создает условия для оптимальной смазки и уменьшает коэффициент трения. Исходя из этих требований, антифрикционный материал представляет собой сочетания достаточно прочной и пластичной основы, в которой имеются опорные (твердые) включения. При трении пластичная основа частично изнашивается, а вал опирается на твердые включения. В этом случае трение происходит не по всей поверхности подшипника, а смазка удерживается в изнашивающихся местах пластичной основы.
Антифрикционными сплавами служат сплавы на основе олова, свинца, меди или алюминия, обладающие специальными антифрикционными свойствами (табл. 16). Антифрикционные свойства сплавов проявляются при трении в подшипниках скольжения. Это, в первую очередь, низкий коэффициент трения, хорошая прирабатываемость к сопрягаемой детали, высокая теплопроводность, способность удерживать смазку и др. Из антифрикционных сплавов наиболее широко применяют баббит, бронзу, алюминиевые сплавы, чугун и металлокерамические материалы.
Антифрикционные сплавы хорошо прирабатываются в парах трения благодаря мягкой основе - олову, свинцу или алюминию. Более твердые металлы (цинк, медь, сурьма), вкрапленные в мягкую основу, способны выдерживать большие нагрузки. После приработки и частичной деформации мягкой основы в ней образуются углубления, способные удерживать смазку, необходимую для нормальной работы пары.
Сплавы. Баббиты - антифрикционные материалы на основе олова или свинца. Их применяют для заливки вкладышей подшипников скольжения, работающих при больших окружных скоростях и при переменных и ударных нагрузках. По химическому составу баббиты классифицируют на три группы: оловянные (Б83, Б88), оловянно-свинцовые (БС6, Б16) и свинцовые (БК2, БКА). Последние не имеют в своем составе олова.
Лучшими антифрикционными свойствами обладают оловянные баббиты. Микроструктура оловянносурьмяномедного баббита Б83 (рис. 49) состоит из мягкой основы, представляющей собой твердый раствор на базе олова. Твердыми частицами являются кубические включения SnSb и игольчатые кристаллы включений Cu3Sn.
Баббиты на основе свинца имеют несколько худшие антифрикционные свойства, чем оловянные, но они дешевле и менее дефицитны. Свинцовые баббиты применяют в подшипниках, работающих в легких условиях. В марках баббитов цифра показывает содержание олова. Например, баббит БС6 содержит по 6% олова и сурьмы, остальное - свинец.
Для оловянных и оловянно-фосфористых бронз характерны высокие антифрикционные свойства: низкий коэффициент трения, небольшой износ, высокая теплопроводность, что позволяет подшипникам, изготовленным из этих материалов, работать при высоких окружных скоростях и нагрузках.
Алюминиевые бронзы, используемые в качестве подшипниковых сплавов, отличаются большой износостойкостью, но могут вызвать повышенный износ вала. Их применяют вместо оловянных и свинцовых баббитов и свинцовых бронз.
Свинцовые бронзы в качестве подшипниковых сплавов могут работать в условиях ударной нагрузки.
Латуни по антифрикционным свойствам уступают бронзам. Их используют для подшипников, работающих при малых скоростях и умеренных нагрузках.
Из-за дефицитности олова и свинца применяют сплавы на менее дефицитной основе, например алюминиевые сплавы. Алюминиевые сплавы обладают хорошими антифрикционными свойствами, высокой теплопроводностью, хорошей коррозионной стойкостью в масляных средах и достаточно хорошими механическими и технологическими свойствами. Их применяют в виде тонкого слоя, нанесенного на стальное основание, т. е. в виде биметаллического материала. В зависимости от химического состава различают две группы сплавов.
1. Сплавы алюминия с сурьмой, медью и другими элементами, которые образуют твердые фазы в мягкой алюминиевой основе. Наибольшее распространение получил сплав АСМ, содержащий сурьму (до 6,5%) и магний (0,3-0,7%). Этот сплав хорошо работает при высоких нагрузках и больших скоростях в условиях жидкостного трения. Сплав АСМ широко применяют для изготовления вкладышей подшипников коленчатого вала двигателей тракторов и автомобилей.
2. Сплавы алюминия с оловом и медью, например АО20-1 (20% олова и до 1,2% меди) и А09-2 (9% олова и 2% меди). Они хорошо работают в условиях сухого и полужидкого трения и по антифрикционным свойствам близки к баббитам. Их используют для производства подшипников в автомобилестроении, транспортном и общем машиностроении.
Для работы в подшипниковых узлах трения применяют специальные антифрикционные чугуны. Изготовляют три типа антифрикционного чугуна: серый, высокопрочный с шаровидным графитом и ковкий (см. табл. 16). Антифрикционный чугун идет на изготовление червячных зубчатых колес, направляющих для ползунов и т. п. деталей машин, работающих в условиях трения.
Металлокерамические сплавы получают прессованием и спеканием порошков бронзы или железа с графитом (1-4%). Пористость сплава 15-30%. После спекания сплавы пропитывают минеральными маслами, смазками или маслографитовой эмульсией. Сплавы хорошо прирабатываются к валу, а наличие смазки в порах способствует снижению износа подшипника.
Припои.
имеющий температуру плавления ниже, чем соединяемые металлы. Применяют сплавы на основе олова, свинца, кадмия, меди, никеля и другие.
§Описание[править | править вики-текст]
Припои бывают в виде гранул, прутков, проволоки, порошка, фольги и закладных деталей.
Пайку осуществляют или с целью создания механически прочного (иногда герметичного) шва, или для получения электрического контакта с малым переходным сопротивлением. При пайке места соединения и припой нагревают. Так как припой имеет температуру плавления значительно ниже, чем соединяемый металл (или металлы), то он плавится, в то время как основной металл остаётся твёрдым. На границе соприкосновения расплавленного припоя и твёрдого металла происходят различные физико-химические процессы. Припой смачивает металл, растекается по нему и заполняет зазоры между соединяемыми деталями. При этом компоненты припоя диффундируют в основной металл, основной металл растворяется в припое, в результате чего образуется промежуточная прослойка, которая после застывания соединяет детали в одно целое.
Выбирают припой с учётом физико-химических свойств соединяемых металлов (например, по температуре плавления), требуемой механической прочности спая, его коррозионной устойчивости и стоимости. При пайке токоведущих частей необходимо учитывать удельную проводимость припоя. Жидкотекучесть низкотемпературных припоев даёт возможность паять изделия сложной формы.
Вид припоев | Температура плавления Tпл., °C | Предел прочности при растяжении, МПа | Сплавы |
Мягкие | До 300 | 16-100 | оловянно-свинцовые, оловянно-свинцово-кадмиевые, оловянно-цинковые, сурьмянистые, бессвинцовые (Sn+Cu+Ag+Bi+др.) |
Твёрдые | Свыше 300 | 100-500 | медно-цинковые, медно-никелевые, медно-фосфористые, серебряные |
Припои принято делить на две группы:
· мягкие;
· твёрдые.
К мягким относятся припои с температурой плавления до 300 °C, к твёрдым — выше 300 °C. Кроме того, припои существенно различаются по механической прочности. Мягкие припои имеют предел прочности при растяжении 16—100 МПа, а твёрдые — 100—500 МПа.
Мягкими припоями являются оловянно-свинцовые сплавы (ПОС) с содержанием олова от 10 (ПОС 10) до 90 % (ПОС 90), остальное свинец. Проводимость этих припоев составляет 9—15 % чистой меди. Плавление этих припоев начинается при температуре 183 °C (температура плавления эвтектики системы олово-свинец) и заканчивается при следующих температурах:
Дата добавления: 2018-04-04; просмотров: 1771; Мы поможем в написании вашей работы! |
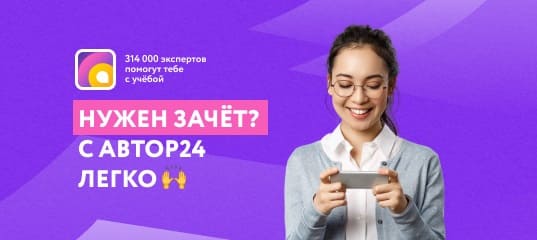
Мы поможем в написании ваших работ!