Модули реакции 2-го порядка и относительные объемы реакторов смешения в вытеснения
Таблица 2
Степень превращения | Степень незавершенности Реакции | Идеальное вытеснение В=1 | Трехсекционный реактор смешения | Двухсекционный реактор смешения | Односекционный реактор смешения | |||
![]() | ![]() | b | ![]() | b | ![]() | b | ||
0,7 | 0,3 | 2,33 | 3,5 | 1,5 | 4,23 | 1,81 | 7,78 | 3,33 |
0,8 | 0,2 | 4 | 6,75 | 1,69 | 8,8 | 2,2 | 20 | 5 |
0,9 | 0,1 | 9 | 18,8 | 2,09 | 27,2 | 3,02 | 90 | 10 |
0,95 | 0,05 | 19 | 48 | 2,53 | 78,5 | 4,13 | 380 | 20 |
0,99 | 0,01 | 99 | 37,4 | 3,78 | 784 | 7,92 | 9900 | 100 |
Рис.2.1 Схема реактора идеального смешения
Рис.2.2 Схема трехсекционного реактора
Рис.2.3 Схема реактора идеального вытеснения
Вопрос 23. Схемы расположения труб в трубных решетках, способы соединения труб с решеткой. Способы крепления трубных решеток, распределительных камер (крышек) и кожуха между собой в аппаратах различных типов.
Теплообменные трубы и трубные решетки. Теплообменные
трубы кожухотрубчатых стальных аппаратов — это серийно выпускаемые промышленностью трубы из углеродистых, коррозионно-стойких сталей и латуни. Диаметр теплообменных труо значительно влияет на скорость теплоносителя, коэффициент теплоотдачи в трубном пространстве и габариты аппарата; чем меньше диаметр труб, тем большее их число можно разместить
Рис. 1. Схема размещения труб в трубной решетке:
в — по вершинам равностороннего треугольника: б — по вершинам квадратов*, а — по окружностям
|
|
в кожухе данного диаметра. Однако трубы малого диаметра быстрее засоряются при работе с загрязненными теплоносителями, определенные сложности возникают при механической очистке и закреплении таких труб развальцовкой. В связи с этим наиболее употребительны стальные трубы с наружным диаметром 20 и 25 мм. Трубы диаметром 38 и 57 мм применяют при работе с загрязненными или вязкими жидкостями.
С увеличением длины труб и уменьшением диаметра аппарата его стоимость снижается. Наиболее дешевый теплообменный аппарат при длине труб 5—7 м.
Трубные решетки кожухотрубчатых теплообменников изготовляют из цельных стальных листов или поковок. Для аппаратов большого диаметра используют сварные трубные решетки. В эгом случае сварные швы не должны пересекаться, а расстояние от кромки сварного шва до отверстий должно быть не менее 0,8 диаметра отверстия.
Схема расположения труб в трубных решетках и шаг отверстий для труб регламентируются ГОСТ 9929—82. Для теплообменников типов Н и К трубы размещают в трубных решетках по вершинам равносторонних треугольников (рис. 1, а), а для теплообменников типов П, У и ПК — по вершинам квадратов (рис. 1,6) или равносторонних треугольников. При размещении труб диаметром <4Т по вершинам равносторонних треугольников обеспечивается более компактное расположение труб в трубной решетке, чем при размещении их по вершинам квадратов при одинаковом шаге I'. Однако последняя схема имеет важное эксплуатационное преимущество: она позволяет очищать трубы снаружи механическим способом, поскольку между трубами образуются сквозные ряды. При размещении по вершинам треугольников такие ряды можно получить, только увеличив шаг /'. По окружностям (рис. 2, в) трубы располагают лишь в кислородной аппаратуре.
|
|
Рис. 2. Варианты крепления труб в трубных решетках:
а — развальцовка в дву* канавках; 6 — раэвальцов-ка о одной канавке; в — раэвальцоака со сваркой; г, д — сварки; е — развальцовка в гладком отверстии с отбортойкой; ж — пайка; з — склеивание
Шаг отверстий для труб в решетке выбирают с учетом достаточной прочности участка шириной
;для стальных кожухотрубчатых аппаратов шаг принимают по следующим данным:
, мм....... 16 20 25 38 57
, мм....... 21 26 32 48 70
Трубы соединяют с трубной решеткой стальных аппаратов развальцовкой (рис. 2, а, б, е), сваркой (рис. 2, г, д), развальцовкой со сваркой (2, в). Пайку и заливку металлом концов труб в решеткахприменяют при изготовлении теплообменников из меди и ее сплавов, а склеивание — при изготовлении аппаратов из полимерных материалов.
|
|
Наиболее распространенный способ крепления труб в решетке — развальцовка. Трубы вставляют в отверстия решетки с некоторым зазором, а затем обкатывают изнутри специальным инструментом, снабженным роликами (вальцовкой). При этом в стенках трубы создаются остаточные пластические деформации, а в трубной решетке — упругие деформации, благодаря чему материал решетки после развальцовки плотно сжимает концы труб. Однако при этом материал труб подвергается наклепу (металл упрочняется с частичной потерей пластичности), что может привести к растрескиванию труб. С уменьшением начального зазора между трубой и отверстием в решетке наклеп уменьшается, поэтому обычно принимают зазор 0,25 мм. Кроме этого для обеспечения качественной развальцовки и возможности замены труб необходимо, чтобы твердость материала трубной решетки превышала твердость материала труб.
Развальцовочное соединение должно быть прочным и герметичным. Прочность соединения оценивают усилием вырыва трубы из гнезда, герметичность — максимальным давлением среды, при котором соединение герметично. При развальцовке конец трубы должен выступать над трубной решеткой на расстояние, равное толщине 5 трубы. Для повышения прочности и герметичности соединения иногда выполняют отбортовку выступающего над решеткой конца трубы (рис.3).
|
|
Рис. 3
Наиболее простой способ — развальцовку (в гладких отверстиях) — применяют при относительно небольших рабочих давлениях (до 0,6 МПа). Прочность и герметичность вальцовочного соединения значительно возрастают при развальцовке в отверстиях с одной или двумя канавками глубиной около 0,5 мм.
Трубы развальцовывают обычно на глубину 1,5 или, если толщина решетки меньше 1,5
на полную толщину решетки. При этом со стороны межтрубного пространства оставляют неразвальцованным поясок шириной 3 мм, чтобы не подрезать трубу кромкой решетки при развальцовке, либо на этой кромке снимают фаску.
В толстых решетках трубу развальцовывают двумя поясками: один шириной 1,5 со стороны распределительной камеры, другой шириной 0,75
со стороны межтрубного пространства. Это позволяет исключить проникновение среды в щель между трубой и решеткой и коррозию.
Крепление труб сваркой с развальцовкой применяют без ограничений давления и температуры теплоносителей. В этом случае сначала выполняют сварку, а затем развальцовку трубы.
Распределительные камеры теплообменного аппарата предназначены для распределения потока теплоносителя по трубам ( и представляют собой обечайку с фланцами, соединенными с трубной решеткой и съемной эллиптической или плоской крышкой. В некоторых конструкциях крышка приварена к цилиндрической обечайке.
Для образования ходов теплоносителя по трубам распределительную камеру снабжают продольной перегородкой.
Для аппаратов небольшого диаметра (до 800 мм) крышку распределительной камеры выполняют плоской, поскольку такие крышки дешевле и проще в изготовлении. В некоторых случаях для удобства обслуживания аппарата распределительные камеры и крышки к ним навешивают в шарнирных устройствах, закрепленных на кожухе.
Толщину стенок распределительной камеры принимают равной толщине стенки кожуха аппарата. Камеру и крышку обычно изготовляют из того же материала, что и кожух аппарата.
Фланцы теплообменных аппаратов выполняют с привалочной поверхностью выступ-впадина или под прокладку восьмиугольного сечения. В стальных кожухотрубчатых теплообменниках используют металлические и асбометаллические прокладки. Во всех случаях прокладку следует изготовлять цельной без сварки, пайки или склеивания. Прокладку в плавающей головке выполняют обычно из стали.
Вопрос 15.Тарельчатые колонны: классификация контактных устройств, колпачковые тарелки, клапанные тарелки,ситчатые тарелки, прямоточно-скоростные и язычковые тарелки. Рекомендации по выбору тарелок стальных колонных аппаратов для процесса масообмена.
Тарельчатые контактные устройства ректификационных и абсорбционных аппаратов классифицируют по числу потоков, типам и конструкции контактных элементов, характеру взаимодействия фаз в зоне контакта, организации перелива жидкости и другим признакам.
По числу потоков (сливов) тарелки выполняют одно-, двух- и многопоточными (рис. 101). Применяют также многосливные тарелки с еделенными по площади сливами и тарелки с каскадным расположением полотна.
Многопоточные и многосливные тарелки используют в колоннах большого диаметра и при значительных расходах жидкости. Такие тарелки обеспечивают более равномерные уровень жидкости и распределение паров по площади контактных устройств. Это связано с уменьшением напряженности слива в гидравлическом отношении и длины пути жидкости на тарелке. В колоннах со значительным изменением по высоте жидкостной нагрузки устанавливают тарелки с различным числом потоков.
По типу контактных элементов тарелки разделяются на кол-пачковые с круглыми и прямоугольными колпачками, тарелки из S-образных элементов, клапанные, ситчатые, решетчатые, чешуйчатые или язычковые и др.
В зависимости от направления движения паровой и жидкой фаз в зоне контакта выделяют тарелки с перекрестным током, прямоточные и противоточные. По организации перелива жидкости тарелки разделяют на переливные и беспереливные (провального типа).
В зависимости от диаметра аппарата тарелки выполняют со сплошным полотном и разборной конструкции.
При сравнительно небольших диаметрах аппаратов применяют тарелки неразборной конструкции со сплошным полотном. На таких тарелках для ремонта предусматривают в полотне люки . Люк размещают с учетом схемы расположения контактных элементов. Крышку такого люка изготовляют с контактными элементами и размещают заподлицо с полотном тарелки на опорном кольце .
Тарелки разборной конструкции собирают из отдельных полотен, ширина которых позволяет заносить их в колонну через люки. Полотна размещают на опорных балках. Для соединения полотен используют прижимные планки, струбцины, клиновые соединения . Вертикальная полка уголка и ребро, полученное отгибом одной из кромок полотна, увеличивают жесткость полотна тарелок. Герметичность соединений обеспечивают установкой прокладок.
Колпачковые тарелки.
Круглые или капсульные колпачки стандартной конструкции имеют диаметр 80, 100 и 150 мм. Колпачки меньшего размера применяют в колоннах небольших диаметров.
Колпачки на тарелках располагают по вершинам равносторонних треугольников с шагом от 1,3 до 1,9 диаметра колпачка.
Крепление колпачков на тарелке можно выполнить индивидуальным и групповым способами. При индивидуальном способе в конструкции, показанной на рис. 1, а, колпачок 1 закреплен гайками 4 и 5 на шпильке 3, приваренной к патрубку 2. Прямоугольное отверстие в колпачке под шпильку с двух противоположных сторон имеет отогнутые кромки 2. Положение колпачка по высоте регулируют его вращением, причем одновременно вращается и нижняя гайка 5.
Применяют также варианты крепления колпачка, не позволяющие регулировать его по высоте. При этом колпачок может упираться нижними кромками прорезей в полотно тарелки (рис. 1, б). По другому варианту
Рис.1.
Рис.1.
(рис. 1, б) колпачок 1 установлен на трех опорных ребрах 2 и притягивается к патрубку 3 шпилькой 4 с гайкой 5. При таком креплении неточность установки патрубков приводит к неправильному положению колпачков по высоте или перекосу, что вызывает их неравномерную работу. В связи с этим нужно следить, чтобы верхние торцы патрубков лежали в одной горизонтальной плоскости.
Колпачки тарелки изготовляют штампованными из углеродистой стали толщиной 2—4 мм или легированной стали толщиной 1,5—2,0 мм, а также литыми из чугуна толщиной 5 мм. В некоторых случаях колпачки выполняют из алюминиевых сплавов, пластических масс, керамики. По окружности колпачка для прохода паров имеются 20—40 прорезей высотой 20 или 30 мм. Патрубки для стальных тарелок изготовляют из бесшовных труб.
Клапанные тарелки.
Такие тарелки изготовляют с дисковыми и прямоугольными клапанами. По направлению ввода паров в жидкость различают клапанные тарелки с перекрестным током и прямоточные.
Диаметр дисковых клапанов обычно составляет 50 мм; дилмотр отверстия под клапаном в полотне тарелки 30—40 мм, высота подъема клапана 6—8 мм. При этом площадь проходного сечения щели между полотном тарелки и пластиной клапана при его полном подъеме немного меньше площади отверстия под клапаном. В нижнем положении клапан опирается на выступы, которые получают обычно просечкой и отгибанием краев пластины клапана так, чтобы между пластиной и полотном тарелки оставался зазор 0,5— 1,5 мм. Это позволяет исключить влияние сил поверхностного натяжения на работу клапана.
В отечественной практике широко применяют прямоточные тарелки с дисковыми клапанами. Клапан такой конструкции (рис. 2) имеет три направляющие, расположенные в плане под углом 120°, две из которых имеют большие вес и длину. При работе с возрастающей скоростью паров сначала поднимается легкая часть клапана, обращенная против потока жидкости, а затем клапан принимает положение, при котором пары выходят в направлении движения жидкости. Короткая ножка клапана расположена в вырезе на кромке отверстия полотна тарелки, что обеспечивает Жданное положение клапана в плане при его подъеме. Стандартом предусмотрены тарелки однопоточные диаметром 1000—4000 мм, двухпоточные— 1400—9000 мм и четырехпоточные — 3200—5500 мм. Тарелки выполняют разборными. Тарелку любого из этих диаметров можно изготовлять в трех вариантах с шагом между рядами клапанов 50, 75 и 100 мм, что предопределяет различное число клапанов и соответственно разную площадь свободного сечения тарелки.
Рис.2
Ситчатые тарелки.
Рис. 3
Такие тарелки представляют собой плоский перфорированный лист со сливными устройствами. Перфорацию выполняют в виде круглых отверстий (рис. 3) диаметром d = З-4 мм и более, с шагом t = (3-5) d. Площадь отверстий в зависимости от производительности тарелки по пару составляет от 8 до 30% от площади сечения колонны.
Известны конструкции многосливных тарелок с двумя зонами контакта фаз с ситчатым полотном или контактными элементами другого типа. В этом случае переливное устройство (рис. 4) в нижней части имеет щель, из которой жидкость вытекает в виде пленки, перекрывающей сечение колонны под полотном тарелки. Таким образом образуется вторая зона контакта фаз в пространстве между тарелками
Рис. 4
Анализ работы тарельчатых контактных устройств, выполненный УкрНИИхиммашем, позволил установить для некоторых тарелок описанных конструкций области применения в зависимости от технологического назначения и параметров работы. ~
УкрНИИхиммашем для тарелок шести типов определены области применения (табл.1) и область устойчивой работы (рис. 5).
Установлено, что ситчатые тарелки эффективны в процессах, протекающих при стабильных режимах работы (диапазон устойчивой работы тарелки до 2) и производительности L по жидкости до 40 м3/(м2-ч). Эти тарелки нельзя использовать для обработки жидкостей, вызывающих забивание осадком отверстий тарелок. Ситчатые многосливные тарелки применяют для процессов,-требующих эффективного контакта при большой удельной нагрузке по жидкости L до 180 м3/(м2-ч), ситчато-клапанные— для процессов, .проводимых под вакуумом и при атмосферном давлении, при L < 100 м»/(м*-ч) и F < 2,5 (м/с) (кг/м3) . Эти тарелки в меньшей степени подвержены забиванию твердыми включениями, которые под действием прямоточной составляющей скорости пара, выходящего из-под клапанов, сдуваются с поверхности тарелки.
Клапанные прямоточные тарелки применяют в процессах, протекающих при атмосферном и повышенном давлении, при L < 100 м*/(м"-ч) и F < 2,5 (м/с) (кг/м3) . Диапазон устойчивой работы этих тарелок 3,5.
Таблица 1
Области применения тарелок различных типов
Тарелка | Диаметр, мм | Условия проведения процесса |
Ситчато-клапанная Ситчатая Клапанная Колпачковая | 400—4000 | Вакуум; атмосферное давление Любое давление, стабильный режим Атмосферное и повышенное давление Любое давление, нестабильный режим |
Жалюзийно- клапанная Ситчатая многосливная | 1000—4000 1600—4000 | Атмосферное и повышенное давление
Высокоэффективные процессы, большие удельные нагрузки по жидкости — ДО 180 м3/(м ![]() |
Жалюзийно-клапанные тарелки, обладающие высокой эффективностью, i-имеют несколько более 'высокое гидравлическое сопротивление, чем ситчато-клапанные, и применяются в основном для проведения процессов под давлением, при L < 130 м*(м2-ч) и F< Г<Г 3,75 (м/с) (кг/м3) . Диапазон устойчивой работы достигает 1,5. Колпачковые тарелки применяют в производствах относи-:льно небольшой мощности, а также при небольших нагрузках жидкости. В этих условиях тарелки обеспечивают поддержание изеделенного запаса жидкости в контактной зоне.
Рис.5
Дата добавления: 2018-02-28; просмотров: 513; Мы поможем в написании вашей работы! |
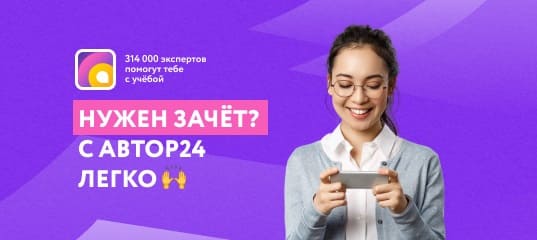
Мы поможем в написании ваших работ!