Figure 1.2 Typical flow diagram for LNG liquefaction
The gas then passes to a fractionating unit where the NGLs are removed and further split into propane and butane. Finally, the main gas flow, now mostly methane, is liquefied into the end product, liquefied natural gas (LNG).
To lower the temperature of the methane gas to about -162°C (its atmospheric boiling point) there are three basic liquefaction processes in current use. These are outlined below:—
• Pure refrigerant cascade process — this is similar in principle to the cascade reliquefaction cycle described in 4.5 but in order to reach the low temperature required, three stages are involved, each having its own refrigerant, compressor and heat exchangers. The first cooling stage utilises propane,
the second is a condensation stage utilising ethylene and, finally, a sub-cooling stage utilising methane is involved. The cascade process is used in plants commissioned before 1970.
• Mixed refrigerant process — whereas with pure refrigerant process (as described above) a series of separate cycles are involved, with the mixed refrigerant process (usually methane, ethane, propane and nitrogen), the entire process is achieved in one cycle. The equipment is less complex than the pure refrigerant cascade process but power consumption is substantially greater and for this reason its use is not widespread.
• Pre-cooled mixed refrigerant process — this process is generally known as the MCR process (Multi-Component Refrigerant) and is a combination of the pure refrigerant cascade and mixed refrigerant cycles. It is by far the most common process in use today.
Fuel for the plant is provided mainly by flash-off gas from the reliquefaction process but boil-off from LNG storage tanks can also be used. If necessary, additional fuel may be taken from raw feed gas or from extracted condensates. Depending upon the characteristics of the LNG to be produced and the requirements of the trade, some of the extracted NGLs may be re-injected into the LNG stream.
1.2.2 LPG production
Liquefied petroleum gas (LPG) is the general name given for propane, butane and mixtures of the two. These products can be obtained from the refining of crude oil. When produced in this way they are usually manufactured in pressurised form.
However, the main production of LPG is found within petroleum producing countries. At these locations, LPG is extracted from natural gas or crude oil streams coming from underground reservoirs. In the case of a natural gas well, the raw product consists mainly of methane. However, as shown in Figure 1.2, in this process it is normal for NGLs to be produced and LPG may be extracted from them as a by-product.
|
|
A simple flow diagram which illustrates the production of propane and butane from oil and gas reservoirs is shown in Figure 1.3. In this example the methane and ethane which have been removed are used by the terminal's power station, and the LPGs, after fractionation and chill-down, are pumped to terminal storage tanks prior to shipment for export.
Figure 1.3 Typical oil/gas flow diagram
1.2.3 Production of chemical gases
A simplified diagram for the production of the chemical gases, vinyl chloride, ethylene and ammonia is shown in Figure 1.4. These three chemical gases can be produced indirectly from propane. The propane is first cracked catalytically into methane and ethylene. The ethylene stream can then be synthesised with chlorine to manufacture vinyl chloride. In the case of the methane stream, this is first reformed with steam into hydrogen. By combining this with nitrogen under high pressure and temperature, in the presence of a catalyst, ammonia is produced.
Дата добавления: 2018-02-28; просмотров: 661; Мы поможем в написании вашей работы! |
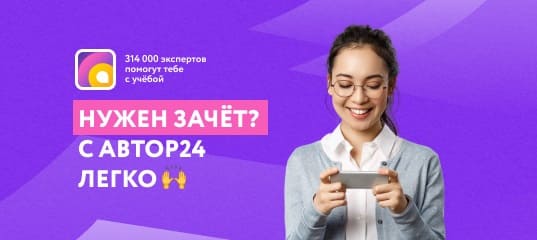
Мы поможем в написании ваших работ!