Получение композитов электрохимическим способом
Комбинированные электрохимические покрытия наиболее часто получают на основе хрома, никеля, железа или меди, реже – на основе благородных или других металлов. К комбинированным покрытиям относят и многослойные осадки, состоящие из двух или нескольких различных металлов. Их называют слоистыми композиционными покрытиями. К этой же группе относят и электрохимические покрытия, содержащие в своем составе различные включения из природных или искусственных химических соединений.
Изменяя температуру, плотность тока, концентрацию компонентов электролита, интенсивность его перемешивания и т. п. можно получать покрытия самых разнообразных свойств и структуры. Эти покрытия совмещают свойства металлов (электропроводность, теплопроводность, износостойкость и др.) со свойствами неметаллов, включенных в осадок при электроосаждении (жаростойкость, твердость, химическую стойкость).
Для возможности включения неметаллических частиц в электролитический осадок их необходимо непрерывно поддерживать во взвешенном состоянии с помощью перемешивания, т. к. эти частицы вводят непосредственно в электролит для осаждения металла.
Выбор способа перемешивания определяется формой изделия, условиями электролиза и экономической целесообразностью. В ваннах малой емкости перемешивание можно вести механическим способом, в более крупных емкостях – с помощью барботажа воздухом или инертным газом.
|
|
В качестве наполнителей в этом случае применяют тугоплавкие бориды, карбиды, силициды и т. п. Используемые суспензии этих веществ чаще всего полидисперсные. Можно получать и монодисперсные вещества фазы наполнителей, однако они значительно дороже. Поэтому их применяют только для моделирования процесса с целью изучения механизма образования композиционного покрытия.
Фазой наполнителя композиционного покрытия могут быть и металлические порошки. Их необходимая дисперсность достигается измельчением крупных частиц в коллоидных мельницах. Эти частицы имеют весьма развитую поверхность и поэтому очень активны, но также склонны к коагуляции, что нежелательно.
Влияние различных факторов на состав и механизм образования комбинированных покрытий
Возможность образования покрытий заданного состава зависит от многих условий. Определяющими из них являются взаимодействие между частицами в составе электролита, взаимодействие частиц с поверхностью, образующегося осадка, а также с выделяющимся на катоде водородом. Поэтому необходимо учитывать заряд частиц дисперсной фазы, адгезию частиц к катоду, смачиваемость частиц второй фазы электролитом и возможность протекания химических реакций в растворе. Иными словами, необходимо знать, существуют ли определенное сродство или несовместимость между катодной поверхностью и заращиваемой частицей. Проявление этих свойств в первую очередь зависит от ионной силы, рН и наличия в электролите поверхностно-активных веществ. Кроме этого существенное влияние оказывают сила тока, потенциал, температура, скорость перемешивания суспензии, природа и размеры заращиваемых частиц.
|
|
Например, при более высоких плотностях тока возможно заращивание не только частиц второй фазы, но и твердых частиц шлама, загрязняющих осадок. Это проводит к увеличению шероховатости покрытия.
Влияние температуры раствора сказывается на вязкости электролита. С ростом температуры вязкость раствора уменьшается и при недостаточно интенсивном перемешивании это может приводить к седиментации частиц второй фазы. При этом будет уменьшаться их содержание в покрытии. Повышение температуры может также снижать адгезию частиц к поверхности катода.
Необходимо принимать во внимание и электропроводность заращиваемых частиц. Наилучшие условия заращивания реализуются для электропроводящих частиц, что способствует повышению их содержания в покрытии. Однако это тоже может увеличивать его шероховатость.
|
|
На качество получаемых композиционных покрытий заметное действие способно оказывать добавление в электролит различных поверхностно-активных веществ. Их действие связано с изменением поверхностного натяжения электролита, что облегчает смачивание заращиваемых частиц и стимулирует их включение в осадок.
Существенную роль играет и размер частиц. Обычно для этого используют частицы размером от 0,01 до 10 мкм. С точки зрения устойчивости суспензии оптимальным должен быть размер частиц 0,1-2 мкм. Грубые частицы размером более 10 мкм труднее заращиваются, легче седиментируют и снижают устойчивость суспензии.
Широкое использование композиционных материалов в виде покрытий объясняется тем, что изделия при эксплуатации контактируют с агрессивной средой именно с поверхности. Композиционные покрытия чаще всего достаточно коррозионностойки, т. к. частицы второй фазы изменяют электрохимические свойства матричного материала. Кроме того, эти частицы сами обладают высокой химической стойкостью и могут защищать металл от коррозии благодаря экранирующему действию.
При использовании композиционных покрытий большую роль играет природа защищаемого металла, подготовка его поверхности и адгезия покрытия к подложке.
Основные закономерности химического взаимодействия пленочных композиционных материалов с агрессивной средой те же, что и в случае монолитного композита того же состава. Однако, определяющим моментом в этом случае, бесспорно, является адгезия покрытия к подложке. Если произошло отслаивание покрытия от подложки из-за недостаточной адгезии, то сохранение химической стойкости композиционного покрытия уже не имеет смысла.
Дата добавления: 2018-02-28; просмотров: 372; Мы поможем в написании вашей работы! |
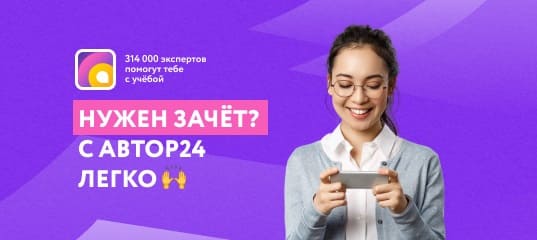
Мы поможем в написании ваших работ!