Влияние температуры на коррозию бетона
Бетон легко адсорбирует влагу из воздуха. От влажности бетонной массы зависит интенсивность коррозионных процессов. Но влажность воздуха связана с его температурой, т.е. речь идет о термовлажностном воздействии на бетон. При неизменном термовлажностном режиме устанавливается равновесие между окружающей средой и бетонной массой.
Бетонные конструкции практически всегда эксплуатируются в условиях, допускающих колебания температуры: сезонные (зима — лето), суточные (день — ночь) и технологические (например, периодическое заполнение емкости горячим раствором).
Кроме изменения линейных размеров конструкции, зависящего от коэффициента термического расширения бетонной массы, в бетоне при колебаниях температуры может происходить испарение влаги, ее замерзание при понижении температуры или конденсации паров воды. Все это приведет к появлению нестационарных потоков паров воды и поровой жидкости, что может сопровождаться фазовыми и химическими превращениями в системе.
При повышении температуры (Т) будет происходить и постепенное повышение температуры в толще бетона. Это приведет к увеличению упругости паров воды, так как начнется ее испарение из поровой жидкости. Движущей силой этого процесса будет градиент парциональных давлений водяного пара. Этот процесс должен сопровождаться появлением в бетоне растягивающих напряжений. Однако на первых порах это не вызывает заметных деформаций в бетоне, так как одновременно с испарением воды происходит и некоторое расширение твердого скелета бетонной массы, поэтому заметного роста давления в системе не наблюдается.
|
|
Удаление воды приводит к повышению концентрации солей в поровой жидкости, что вызывает нарушение равновесия между поровой жидкостью и стенками пор. При достижении предельной концентрации солей, содержащих в поровой жидкости, начнется их кристаллизация в бетонной массе. Значит, при этом будет развиваться коррозии III вида.
Следующий этап процесса разрушения начнется тогда, когда будет удалена не только свободная вода, но и химически связанная. Интенсивное сжатие геля приведет к развитию в бетоне усадочных явлений. Значит, при длительном воздействии повышенных Т из системы фактически удаляется одна из составляющих цементного камня — гель кремневой кислоты. Это приводит к механическому изменению системы — сжатию, сопровождающемуся растрескиванием массы.
При понижении Т влажность бетона увеличивается, что может привести к развитию деформации набухания. Однако по абсолютной величине деформации набухания в бетоне значительно меньше, чем деформация усадки. Значит, понижение температуры до некоторых пределов (Т= 00) не может вызвать значительных изменений в бетоне. Понижение Т до отрицательных значений вызовет уже весьма существенные изменения, связанные с фазовым превращением воды. Наиболее опасны при этом циклические знакопеременные колебания Т.
|
|
Объем воды при замерзании увеличивается примерно на 9%. При этом в капиллярах и порах будет возникать значительное давление на их стенки. Многократные теплосхемы приведут к расшатыванию структуры цементного камня, появлению трещин и снижению прочности бетона.
Общий уровень напряжения будет зависеть от пористости бетонной массы. Чем меньше пористость, тем меньше величина разрывающих напряжений. Разрушающее действие попеременного замораживания и оттаивания усиливается, если вода содержит значительное количество растворенных солей, например, морская или артезианская. При вымораживании воды возможна кристаллизация солей порах, приводящая к появлению дополнительных напряжений, усиливающих разрушение.
Установлено, что значительную роль в развитии процессов разрушения под действием отрицательных температур играет не только абсолютная пористость материала, но и размер пор капилляров.
|
|
Вода, заполняющая поры цементного камня, начинает переходить в лед в первую очередь в крупных порах и полостях при Т 0...-10С. При дальнейшем понижении Т лед образуется в капиллярах значительно меньших размеров. В наиболее тонких капиллярах вода замерзала только при Т
-250С, что соответствовало состоянию переохлажденной жидкости при отсутствии центров кристаллизации.
Морозостойкость бетона зависит не только от общей пористости, но и от размеров капилляров и пор. Т.о. повысить морозостойкость бетона можно уменьшением его пористости, что достигается уменьшением В/Ц отношения при его изготовлении, а также снижением индивидуального размера пор. Достигается это введением в состав бетонной массы добавок — микропорообразователей обеспечивающих появление равномерно распределенных мелких пор.
Повысить устойчивость конструкций к воздействию низких Т можно увеличением промежутка времени между изготовлением бетонной конструкции и моментом начала воздействия низких Т. Бетонные работы рекомендуется возводить в теплое время года, чтобы до начала заморозков прошел как можно больший промежуток времени.
При невозможности выполнения этого требования следует воспользоваться «прогревным» методом бетонирования, заключающемся в прогревании всего сооружения до положительных температур, не допускающих замерзание воды.
|
|
Однако из-за значительных энергозатрат «прогревный» способ зимнего бетонирования в последнее время не находит широкого применения. Чаще применяется беспрогревный способ, заключающийся в добавке к бетонной смеси противоморозных компонентов, понижающих температуру замерзания жидкой фазы бетона, что обеспечивает условия затвердевания бетона при отрицательных Т. Метод более прост и экономичен, но не лишен недостатков. Основной недостаток - замедленный темп твердения, т.к. скорость всех физико-химических процессов падает при уменьшении Т.
С другой стороны, противоморозные добавки отрицательно влияют и на структуру бетона. Рекомендуется применять комплексные добавки, состоящие из противоморозного компонента и пластификатора, позволяющего снизить содержание воды при изготовлении бетона без увеличения жесткости бетонной массы.
Противоморозными добавками чаще всего бывают: нитрит кальция, смесь нитрита натрия с хлоридом кальция или даже хлорид натрия. Однако хлориды, присутствующие в бетонной массе, могут стимулировать питтинговое поражение стальной арматуры, поэтому их применение целесообразно только для бетонных, а не железобетонных конструкций.
Еще одним способом повышения морозостойкости бетона является его гидрофобизация, то есть придание бетонной массе водоотталкивающих, гидрофобных свойств. Гидрофобизация поверхности стенок капилляров и пор приводит к ухудшению смачиваемости бетона водой и водными растворами. При этом возрастает величина поверхностного натяжения на границе вода — бетон. Вместо вогнутого мениска при смачивании стенок капилляра (а) возникает выпуклый мениск (б) в гидрофобизированном капилляре (рисунок 2).
Выпуклый мениск препятствует проникновению жидкости в толщу бетона в отличие от вогнутого, способствующего подсосу жидкости в капилляре, и увеличению её количества в бетонной массе.
Рисунок 2 ─ Влияние гидрофобизации на смачивание бетона
Гидрофобизация бетонной массы достигается обработкой растворами веществ, которые после удаления растворителя остаются на поверхности пор и капилляров, адсорбируясь на ней или даже вступая с ней в химическое взаимодействия.
Используемые гидрофобизаторы весьма разнообразны. Чаще других используют добавки полигидросилоксана, растворенного в органических растворителях — ксилоле, толуоле или уайт-спирите.
Гидрофобизация может быть объемной, выполняемой еще на стадии изготовления бетонной смеси, и поверхностной, заключающейся в обработке поверхности готовой конструкции. Можно использовать и оба способа одновременно. Наилучший эффект дает объемная гидрофобизация, так как под действием солнечной радиации гидрофобизаторы сравнительно быстро теряют свои водоотталкивающие свойства в поверхностных слоях, более глубокие слои, не облучаемые солнцем, сохраняют гидрофобные свойства еще длительное время и обеспечивают защитный эффект.
Способ гидрофобизации хорош тем, что он обеспечивает беспрепятственный обмен влагой внутренних слоев бетона с внешней атмосферой, одновременно препятствуя проникновению больших количеств воды в толщу бетона, что не может быть достигнуто при защите непроницаемыми покрытиями на поверхности сооружения.
Однако способ гидрофобизации не универсален. Например, его не следует применять при защите напорных сооружений, работающих под давлением, а также в сильноагрессивных средах, так как в этом случае может протекать химические реакции, приводящие к послойному разрушению бетонной массы.
1.7 Особенности коррозии других минеральных материалов
К группе минеральных относятся природные каменные материалы. Из них наибольшее применение находят гранит, базальт, кварцит, песчаник и другие. Природными их называют потому, что их обработка сводится только к приданию им определенной формы.
Физико-химические свойства этих материалов определяются составом горных пород, из которых они образованы. Основными минералами, входящими в их состав, являются кварц, полевой шпат, слюда и другие сложные силикаты и алюмосиликаты.
В зависимости от условий образования различают изверженные и осадочные природные каменные материалы. Изверженные материалы образованы из расплавов. Они могут иметь как стекловидную (аморфную), так и кристаллическую структуру. Эти породы обладают высокой плотностью, малой пористостью, а значит. И высоким химическим сопротивлением агрессивному воздействию. Они имеют также хорошую теплопроводность и морозостойкость, высокую твердость и механическую прочность. Однако эти материалы весьма чувствительны к резким колебаниям температуры, что связаны с различием термических коэффициентов расширения минералов, входящих их в состав. В результате воздействия циклических колебаний температуры они могут растрескиваться.
Осадочные породы образовались в результате протекания вторичных процессов – выветривания, кристаллизации из растворов и т.п. Они значительно более пористы и обладают пониженным сопротивлением разрушению по сравнению с изверженными породами.
Осадочные породы легко разрушаются кислыми растворами. Наиболее низкой кислотостойкостью обладают такие осадочные карбонатные породы, как известняки (СаСО3) и магнезиты (MgCO3). Несколько медленнее разлагаются кислотами доломиты (двойная соль CaMg(CO3)2) и кремнистые известняки (CaSiO2), гипсовый камень ( ) и ангидриты (CaSO4).
Промежуточное положение между изверженными и осадочными породами занимают так называемые обломочные породы – гравий, песок. Эти породы претерпели дробление на макроуровне, поэтому сохранили свойства первичных пород, из которых они образовались. Они имеют более высокое химическое сопротивление разрушению, чем осадочные породы.
При коррозии природных каменных материалов протекают такие же химические процессы, как и в бетоне. Однако скорость этих процессов зависит от индивидуальных физико-химических свойств материала, важнейшим из которых является химический состав и происхождение.
К группе минеральных материалов относятся и плавленые силикатные – разного вида стекла, каменное литье, ситаллы и шлакоситаллы. Особенности коррозии этих материалов связаны с их плотной малопористой структурой, так как они получаются из расплавов, поэтому имеют свойства, сходные с изверженными природными каменными материалами. Агрессивная среда действует на них только с поверхности. В кислые растворы при этом переходят из поверхностных слоев растворимые оксиды щелочных металлов, связанные с кремнеземным каркасом, который устойчив во многих средах. В результате этого на поверхности формируется защитный слой SiO2, замедляющий дальнейшее разрушение материала. При воздействии на эти материалы плавиковой кислоты или горячих щелочей кремнезем растворяется, что приводит к нарушению защитного слоя и интенсивной коррозии материала. Аналогично действует на кремнезем фосфорная кислота. При действии на эти материалы H2SO4, HCl, HNO3 скорость коррозии падает с ростом концентрации кислот, т.к. ускоряется процесс образования защитной пленки кремнезема. При воздействии же HF или H3PO4 с ростом их концентрации скорость коррозии возрастает, поскольку слой кремнезема не обладает защитными свойствами и разрушается в этих растворах.
Можно считать, что стойкость плавленых силикатных материалов в химически активных средах определяется не только их составом, но и свойствами образующейся поверхностной пленки.
К материалам минерального происхождения относят и керамику. Это все виды кирпича и различные облицовочные плитки. Их название происходит от греческого «керамон», что значит глина. Наибольшее применение находит кирпич. Это штучный материал, используемый всеми видами строительства. По составу различают кирпич обыкновенный (глиняный) и силикатный (белый).
Обыкновенный кирпич готовят из глины способом пластического или полусухого формования с последующим обжигом. При пластическом формовании в глиняную массу добавляют достаточно большое количество воды и разливают смесь в формы. После этого проводят предварительную сушку свежесформованных изделий для удаления значительной части воды при температуре ниже, чем обжиговая. При полусухом формовании массу лишь увлажняют, а затем прессуют в формах. При этом промежуточной сушки не требуется. Затем кирпичи подвергают обжигу при температуре порядка 900 – 10000С. При этом основной минерал глины – каолинит – подвергается термическому разложению и, взаимодействуя с примесями сырья, образует сложные силикатные и алюминатные соединения. В результате частичного спекания этих компонентов и образуется материал с достаточно высокой механической прочностью. При более высокой температуре обжига ( 12000С) могут образоваться сложные алюмосиликаты ( силлиманит и муллит), обладающие высокой кислото- и щелочестойкостью вследствие более полного спекания. Такой кирпич называют «железняк». Он имеет и более высокую механическую прочность. Основным недостатком обыкновенного кирпича является очень низкая стойкость к воздействию воды и других водных растворов. Он легко разрушается в результате расклинивающего действия воды и кристаллогидратов солей. При насыщении водой всего на 6 % кирпич теряет 20 – 20% первоначальной механической прочности. Не стоек он и к действию кислот как минеральных, так и органических.
Кроме глиняного существует и так называемый силикатный кирпич. Его готовят из смеси кварцевого песка (примерно 90% по объему) и быстрогасящейся извести. После автоклавной обработки при нагревании масса быстро твердеет в результате протекания реакции (1.13).
(1.13)
При взаимодействии с углекислотой воздуха поверхностный слой карбонизируется. Присутствие в силикатном кирпиче извести и карбоната кальция делает его весьма малостойкими даже в слабых растворах кислот как минеральных, так и органических. В щелочных растворах силикатный кирпич стоек, если эти растворы слабой концентрации. Во влажных условиях он также теряет механическую прочность при поглощении воды. Для повышения химического сопротивления кирпича используют различные облицовочные плитки. Их поверхностный слой оплавляют или наносят на него специальные глазуровочные составы. При последующем обжиге этот слой обладает свойствами плавленых материалов – очень низкой пористостью и высоким химическим сопротивлением агрессивному воздействию. Такими плитками облицовывают наружные поверхности кирпичных сооружений. Возможно также оплавление и тех поверхностей кирпича, которые будут контактировать с открытой атмосферой, что приведет к повышению его стойкости.
Дата добавления: 2018-02-28; просмотров: 455; Мы поможем в написании вашей работы! |
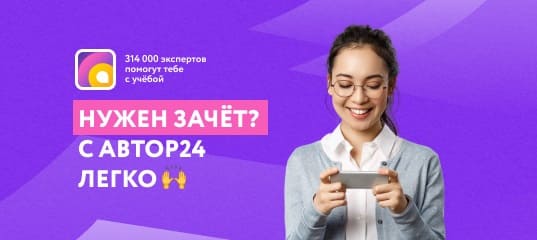
Мы поможем в написании ваших работ!