Выбор марки материала и способа его обработки для конкретных деталей
Цель работы:
1.Ознакомиться с методикой выбора материалов для конкретных изделий
Порядок выполнения работы
1. Перед выполнением практической работы необходимо ознакомиться с основными теоретическими положениями.
2.Произвести выбор марки стали
Выбор материала и режима термической обработки
Краткая теоретическая часть
Рациональный выбор материалов и режимов технологических процессов их обработки обеспечивает надежность изделий и конструкций, снижает себестоимость, повышает производительность труда, уменьшает металлоемкость оборудования.
При выборе материала для конкретного изделия конструктор должен учитывать совокупность свойств данного материала (физических, химических, механических, технологических), отдавая предпочтение той группе свойств, которая в данных условиях работы имеет решающее значение.
Так, для изделий, работающих в агрессивных средах, решающее значение имеют химические свойства материала. Для изделий, работающих в обычных средах под механической нагрузкой, выбор материала производится по механическим свойствам с учетом технологических свойств и стоимости материала.
При выборе материала по его механическим свойствам необходимо учитывать, что численные значения таких механических характеристик, как ударная вязкость, твердость и пластичность, не могут быть использованы конструктором для расчета подобно численным значениям прочности, однако, они являются весьма важными характеристиками, которые дают возможность оценить качество материала. Каждая из этих характеристик имеет свое особое значение при оценке качества материала, применяемого для изделий, работающих в различных условиях.
|
|
Так, качество инструментов оценивают преимущественно по твердости и прочности.
Пластичность является важнейшей характеристикой материала, применяемого для строительных конструкций. В строительстве принято считать пластичность удовлетворительной, если относительное удлинение не менее 15 %, а относительное сужение не менее 45 %.
Вязкость является одной из важнейших характеристик качества материала, применяемого для различных деталей машин, работающих в условиях динамических нагрузок. Причем необходимо иметь в виду, что недостаточная прочность или жесткость материала в ряде случаев может быть компенсирована увеличением размера изделия, а недостаточную вязкость материала нельзя ничем компенсировать. С увеличением размеров конструкции вязкость не только не увеличивается, а в отдельных случаях может даже уменьшаться.
Для определения ударной вязкости применяют образцы с различными надрезами. Характер надреза сильно влияет на ударную вязкость. Поэтому при оценке ударной вязкости материала по справочной литературе необходимо обязательно устанавливать, какому типу надреза она соответствует.
|
|
Обычно материал считают пригодным, если его ударная вязкость, определенная на образцах размером 10´10´55 мм с V-образным надрезом не ниже 30 Дж/кв. см.
Повышение прочности обычно сопровождается снижением пластичности и вязкости (металл охрупчивается). В общем случае считают, что надежность металла при работе возрастает с повышением его пластичности и вязкости. Охрупчивание металла может явиться причиной внезапного хрупкого разрушения изделия. Нередко это происходит при сравнительно небольших напряжениях (меньше предела текучести этого металла).
Пластичность и вязкость зависят от многих факторов: от вида напряженного состояния, наличия концентраторов напряжения, скорости приложения нагрузки и др. Концентраторы напряжений особенно нежелательны для металлов с низкой пластичностью и вязкостью.
Если для существенного повышения прочности или твердости стали изделие необходимо закаливать, то выбирать сталь для такого изделия необходимо с учетом сквозной прокаливаемости. Следовательно, углеродистые стали можно применять для изделий сечением не более 15 мм. Причем в сталях с низким содержанием углерода (меньше 0,25 %) не удается существенно увеличить закалкой твердость и прочность стали, обычно применяют стали с содержанием углерода, превышающим или равным 0,3 %. В том случае, когда необходимо обеспечить сочетание высокой износостойкости и достаточно высокой пластичности, применяют либо стали с низким содержанием углерода и обязательной химико-термической обработкой, либо среднеуглеродистые стали с поверхностной закалкой изделий.
|
|
Важным фактором для выбора марки стали является сложность геометрической формы изделия. Это имеет первостепенное значение, если изделие необходимо подвергать закалке.
В процессе быстрого охлаждения при закалке возникают большие внутренние напряжения, которые в некоторых случаях могут вызывать очень сильную деформацию изделия и даже трещины. Это особенно характерно для изделий сложной формы с наличием конструктивных концентраторов напряжений. Поэтому такие изделия (сечением более 5 мм) рекомендуется изготовлять из легированных сталей, допускающих при закалке более медленное охлаждение (в масле) по сравнению с углеродистыми, которые при закалке необходимо быстро охлаждать (в воде).
|
|
Достоинство легированной стали заключается не только в большей прокаливаемости и возможности более медленного охлаждения при закалке. Легированная сталь после закалки и соответствующего отпуска имеет лучшее сочетание механических свойств (прочности и пластичности) по сравнению с углеродистой. Следует иметь в виду, что легированная машиностроительная сталь имеет существенное преимущество по механическим свойствам по сравнению с углеродистой только после упрочняющей термической обработки (закалки и отпуска). В «сыром» состоянии она имеет небольшие преимущества и поэтому применяется, как правило, в термически обработанном состоянии.
При выборе марки материала необходимо учитывать не только прокаливаемость, но и другие технологические свойства, которые могут играть существенную роль при выборе технологии изготовления. Так, для изделий сложной формы, которые целесообразно изготавливать литьем необходимо выбирать материал с хорошими литейными свойствами, например, чугун или соответствующие цветные сплавы. В некоторых случаях применяют литейные стали. Для изделий, изготавливаемых пластической деформацией, необходимо применять пластичные материалы, например, низкоуглеродистые стали. Для деталей машин, изготавливаемых глубокой вытяжкой, пластичность имеет особое значение, поэтому для них применяют стали с низким содержанием углерода и лучше кипящие.
Важнейшими характеристиками материала для инструментов является твердость и прочность.
Однако для режущих инструментов, применяемых на металлорежущих станках, не менее важной характеристикой является теплостойкость.
Наименьшей теплостойкостью обладают углеродистые стали (нагрев не должен превышать 200 градусов С). Поэтому их применяют в тех случаях, когда инструмент при работе не нагревается более 200 градусов С (ручной инструмент или станочный для обработки дерева и др.).
Низколегированные инструментальные стали по теплостойкости не отличаются существенно от углеродистых, однако, они имеют более высокую прокаливаемость и позволяют применять при закалке масло. По этим причинам инструменты сравнительно больших размеров или сложной формы, которые при работе не нагреваются более 250 градусов С, изготавливают из низколегированных инструментальных сталей.
Высокопроизводительные металлорежущие инструменты изготавливают из быстрорежущих сталей (нагрев не должен превышать 600 градусов С) или твердых сплавов (при нагреве до 800–1000 градусов С).
Общие принципы, которыми следует руководствоваться при выборе материала для конкретного изделия, заключается в следующем:
1. Для различных строительных сооружений, большинства изделий ширпотреба и неответственных слабонагруженных деталей машин и механизмов целесообразно применять строительные стали и серые чугуны. Обычно термическая обработка для таких изделий не применяется. Иногда применяют отжиг (для снятия внутренних напряжений) или нормализацию (для некоторого улучшения механических свойств вместо закалки). Применение легированных строительных сталей может быть оправдано их более высокой прочностью, что приведет к уменьшению металлоемкости изделий и, следовательно, экономии материала.
2. Для ответственных сильно нагруженных деталей машин, работающих при ударной нагрузке, применяют машиностроительные стали. В зависимости от условий работы детали, ее формы и размеров, а также необходимости применения упрочняющей термической обработки выбирают углеродистую или легированную сталь с низким или средним содержанием углерода. При использовании легированной стали обязательно применяется упрочняющая термическая обработка. При использовании углеродистой стали упрочняющая термическая обработка применяется не всегда. Для упрочнения, как правило, применяют закалку с последующим высоким отпуском (улучшение).
3. Для деталей типа пружин или рессор применяют специальные рессорно-пружинные стали с повышенным содержанием углерода (не менее 0,5 %). В зависимости от размеров и формы пружины могут применяться как углеродистые, так и легированные стали. Пружины обычно подвергаются закалке с последующим средним отпуском.
4. Для всевозможных инструментов (режущих, измерительных и др.) применяют инструментальные стали и сплавы. В зависимости от назначения инструмента, его размеров, формы, условий работы выбирают материал из соответствующей группы.
Все инструменты, изготовленные из стали, обязательно проходят термическую обработку для повышения их твердости и прочности. При решении вопроса о термической обработке изделия необходимо учитывать, что термическая обработка приводит к изменению структуры сплава, за счет которой изменяются его свойства. Поэтому при термической обработке изменяются только те свойства, которые зависят от структуры (к ним относится большинство свойств). Свойства, которые зависят от состава и не зависят от структуры, при термической обработке почти не изменяются. К таким свойствам относятся характеристики жесткости – модуль нормальной упругости Е, модуль сдвига G. В тех случаях, когда от изделия требуется большая жесткость, конструктор обеспечивает ее за счет надлежащей площади и формы поперечного сечения. При этом обычно оказывается, что действующие в детали напряжения значительно меньше предела текучести сплава в «сыром» состоянии. В этом случае надобность в упрочняющей термической обработке отпадает. В тех случаях, когда прочность металла в «сыром» состоянии недостаточна, изделие подвергают упрочняющей обработке.
На выбор режима термической обработки оказывают влияние многие факторы. В зависимости от сочетания этих факторов может применяться сквозная или поверхностная, общая или местная термическая обработка.
Например, местная закалка может производиться различными способами в зависимости от конкретных условий. Для мелких деталей удобнее делать общий нагрев всей детали и быстро охлаждать отдельные ее части. Для длинных деталей иногда бывает удобнее делать местный нагрев и охлаждение. При местной закалке с нагревом всей детали и быстрым охлаждением отдельной ее части иногда проводят отпуск за счет запаса теплоты в незакаленной части, которая медленно охлаждается и при этом нагревается закаленная часть. Такой отпуск называют самоотпуском. Температуру при самоотпуске определяют по цвету побежалости.
Конкретную температуру отпуска выбирают в зависимости от заданной твердости, которая указывается на чертеже детали.
Независимо от того, какая задана твердость на чертеже детали, закалкой необходимо обеспечить получение структуры мелкоигольчатого мартенсита. При этом твердость может оказаться значительно выше заданной. При последующем отпуске температура нагрева выбирается такой, которая обеспечила бы снижение твердости до заданной. При этом структуры троостита или сорбита, образовавшиеся из мартенсита при отпуске, будут иметь при равной твердости более высокую пластичность и вязкость по сравнению с аналогичными пластинчатыми структурами, которые образуются из аустенита при закалке.
Приближенно для углеродистых сталей температуру отпуска можно выбрать по нижеприведенным данным (табл. 1, 2).
Таблица 1
Твердость закаленной углеродистой стали в зависимости от содержания углерода
Содержание углерода, % | 0,2 | 0,3 | 0,4 | 0,5 | 0,6 | 0,7 |
HRC (HB) | (340) | 50 | 54 | 58 | 62 | 64 |
Таблица 2
Влияние температуры отпуска на понижение твердости закаленной углеродистой стали
Температура отпуска, градусов С | 200 | 300 | 400 | 500 | 600 | 650 |
Уменьшение твердости в HRC по сравнению с закалкой | 0 | 10 | 17 | 25 | 32 | 36 |
Для изделий, работающих в агрессивных средах, применяют коррозионно-стойкие стали или сплавы на основе цветных металлов.
В слабоагрессивных средах используют наиболее дешевые хромистые стали марок 08Х13, 12Х13, 20Х13 или сплавы на основе алюминия, меди, магния. Изделия из промышленных коррозионно-стойких сталей проходят закалку при температуре 1050 градусов С и высокий отпуск. Для коррозионно-стойких инструментов применяют хромистые коррозионно-стойкие стали с более высоким содержанием углерода марок 30Х13 и 40Х13, которые подвергают закалке и низкому отпуску.
Некоторые сплавы на основе алюминия и магния также подвергают упрочняющей термической обработке.
В сильно агрессивных средах и для изделий, работающих в контакте с пищевыми продуктами, а также для работы в области криогенных температур, обычно применяют хромоникелевые аустенитные коррозионно-стойкие стали типа 12Х18Н10, а для сварных конструкций – стали, дополнительно легированные титаном или ниобием типа 12Х18Н10Т, а также сплавы на основе титана.
При выполнении задания необходимо учитывать изложенное и выбирать не первый попавшийся материал, который удовлетворяет заданным свойствам, а учитывать также экономический фактор. Обилие различных марок материалов, приводимых в справочниках, затрудняет выбор оптимального варианта. Если свойства материала равны или мало превышают указанные в задании, то можно предположить, что вариант близкий к оптимальному. Чем сильнее (в большую сторону) свойства материала отличаются от заданных, тем, как правило, материал дороже и применение его для данной детали менее рационально. В условиях реального производства номенклатура материалов часто ограничивается наличием их на данном предприятии или возможностью их приобретения без особых сложностей.
Задание:Согласно задания своего варианта: 1) изучить условия работы заданной детали и требования, предъявляемые к ней; 2) выбрать марку стали для изготовления заданной детали, изучить ее химический состав и механические свойства; 3) разработать в зависимости от условий работы детали, необходимый вид и режим термической или химико-термической обработки; 4) дать обоснование выбранного вида и режима обработки детали.
№ варианта | № задачи | № варианта | № задачи |
1 | 1,6,15 | 16 | 7,14,5 |
2 | 2,7,14 | 17 | 8,10,3 |
3 | 3,8,13 | 18 | 9,11,7 |
4 | 4,9,12 | 19 | 10,5,13 |
5 | 5,10,15 | 20 | 11,9,1 |
6 | 6,12,2 | 21 | 12,6,4 |
7 | 7,14,5 | 22 | 13,10,5 |
8 | 8,10,3 | 23 | 14,6,9 |
9 | 9,11,7 | 24 | 15,4,10 |
10 | 10,5,13 | 25 | 1,6,15 |
11 | 11,9,1 | 26 | 2,7,14 |
12 | 12,6,4 | 27 | 3,8,13 |
13 | 13,10,5 | 28 | 4,9,12 |
14 | 14,6,9 | 29 | 5,10,15 |
15 | 15,4,10 | 30 | 3,9,14 |
Дата добавления: 2018-02-28; просмотров: 6231; Мы поможем в написании вашей работы! |
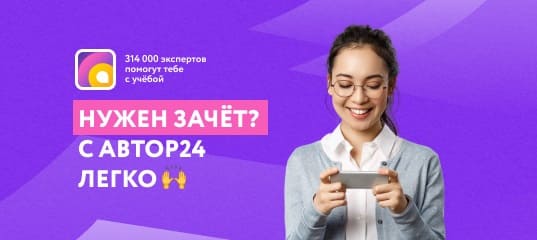
Мы поможем в написании ваших работ!