Диагностика потенциально опасных объектов и производств
(Агеев)
1. Сложные технические системы. Особенности диагностики сложных технических система
Сложная техническая система (СТС) - техническая система (объект), представляющая собой совокупность взаимодействующих, функционально самостоятельных подсистем, предназначенных для достижения общей (конкретной) цели, в том числе технических устройств с измерительными функциями
Основными признаками сложной технической системы (или устройства) являются:
1) обладание определенным единством цели и способствование выработке оптимальных выходов из имеющегося множества входов. Оптимальность выходов должна оцениваться по заранее разработанному критерию эффективности;
2) выполнение большого количества различных функций, которые осуществляются множеством входящих в систему частей или элементов;
3) сложность функционирования ( изменение одной переменной влечет за собой изменение многих переменных и, как правило, нелинейным образом);
4) высокая степень автоматизации;
5) возможность статистического описания поступающего в систему возмущения. Это означает, что невозможно предсказать точное значение внешних нагрузок, а применение альтернативных методов определения пиковых нагрузок в производственных условиях затруднительно. Входные возмущения могут быть множественными и, как правило, различных типов.
К сложным техническим системам, созданных в настоящее время человеком, относятся радиоэлектронные системы устройства, служащие для передачи и преобразования информации; автомобили ;котлы, в состав которых входит несколько тысяч деталей и узлов, имеющих как групповые, так и индивидуальные технические и технологические признаки; промысловые нефтепроводы; магистральные трубопроводы; буровые установки.
|
|
Диагностический параметр (ДП) – параметр (признак) объекта диагностирования, используемый в установ-ленном порядке для определения технического состояния объекта. Большинство ДП по своему назначению могут иметь двойственную природу, являясь одновременно диагностическими и техническими (или параметрами функционального использования). Именно такие параметры чаще всего поддаются непосредственному измерению, и для них проще всего установить нормы и допуски, выход за пределы которых характеризует отказ или дефект в функционировании системы.
Таким образом, отказ характеризуется выходом за пределы установленного допуска одного из ДП. Решение о работоспособном состоянии технической системы или объекта принимается на основе измерения совокупности ДП, причем эта совокупность тем больше, чем сложнее система.
|
|
В случае, когда значения диагностических параметров не поддаются непосредственному измерению, эти значения могут быть найдены путем обработки других параметров, связанных с искомыми прямыми функциональными зависимостями.
Вся совокупность диагностических параметров предназначается для определения работоспособности – , поиска места отказа (дефекта) и прогнозирования технического состояния .
Как правило, в большинстве своем представленные три подмножества совокупностей ДП являются пересекающимися.
Выбранная совокупность ДП должна характеризоваться и определять: всю полноту контроля, возможности поиска дефектов и оптимизацию алгоритмов поиска; возможности прогнозирования возникновения повреждения (отказа) и, самое главное, чувствительность к изменению состояния отдельных элементов и подсистем объекта, к ходу течения деградационных процессов . Сам выбор совокупности ДП для реализации одной или нескольких операций диагностирования представляет собой многоальтернативную задачу и может осуществляться на двух стадиях жизненного цикла объекта:
1) на стадии проектирования, когда производится первичное определение целей и задач проектируемого объекта;
|
|
2) на стадии технической эксплуатации, когда возникает проблема совершенствования функционального использования, или улучшения показателей технического обслуживания (ТО), или необходимость повышения надежности в условиях эксплуатации.
2. Методы технической диагностики. Назначение, задачи, классификация
Тестовое техническое диагностирование - это диагностирование, при котором на объект подаются тестовые воздействия (например, определение степени износа изоляции электрических машин по изменению тангенса угла диэлектрических потерь при подаче напряжения па обмотку двигателя от моста переменного тока).
Функциональное техническое диагностирование - это диагностирование, при котором измеряются и анализируются параметры объекта при его функционировании но прямому назначению или в специальном режиме, например определение технического состояния подшипников качения по изменению вибрации во время работы электрических машин.
Диагностические признаки - это определенные внешне выраженные признаки объекта диагностики, которые оказываются информативными для отнесения обследуемого объекта к определенной диагностической категории. Косвенными диагностическими признаками могут служить акустические сигналы, изменение температуры изделия, давления в системе, наличие в смазке продуктов износа
|
|
Виды технического состояния объекта:
Исправное техническое состояние
Объект, удовлетворяющий всем требованиям нормативно-технической документации (НТД), находится в исправном техническом состоянии (является исправным).
Работоспособное техническое состояние
Объект работоспособен, если он может выполнять все заданные функции с сохранением значений заданных параметров в требуемых пределах.
Функционирующее состояние
Значение всех параметров, характеризующих способность
выполнять заданные функции на проверенных режимах,
соответствуют требованиям НТД.
Предельное состояние - это состояние объекта, при котором его дальнейшая эксплуатация недопустима или нецелесообразна либо восстановление его работоспособного состояния невозможно или нецелесообразно.
Повреждение – это событие, заключающееся в нарушении исправного состояния объекта при сохранении работоспособного состояния. Различают два основных вида повреждений объекта:
1 Допустимые повреждения, возникающие при нормальных условиях эксплуатации (износ режущего инструмента, износ направляющих станка, поломки мелкоразмерного инструмента и деталей предохранительных устройств и т.п.). Полностью устранить этот вид повреждений невозможно, но можно замедлить их проявление.
2 Недопустимые повреждения, возникающие вследствие наличия дефектов или случайных неконтролируемых внешних причин, непосредственно не связанных с техническим состоянием рассматриваемого объекта (аварии, стихийные бедствия и т.п.).
Переход оборудования из одного технического состояния (ТС) в другое обычно происходит вследствие повреждения или отказа.
Степень повреждения:легкая,слабая,средняя,сильная,полная.
При выборе диагностических признаков необходимо учитывать ряд требований, вытекающих из задачи оптимизации диагностической системы. Прежде всего признаки должны быть однозначно связаны с состоянием объекта и образовывать достаточную систему для обеспечения достоверного диагноза. Предпочтительны признаки, которые позволяют обнаружить дефекты на возможно более ранних стадиях их развития. Признаки должны обеспечивать требуемую глубину диагноза, не усложняя процедуры и не увеличивая стоимости средств диагностирования.
3. Методология обнаружения зарождающихся и развитых дефектов. Параметрическая диагностика. Диагностика неисправностей. Диагностика превентивная.
Методология заключается в том, что для разных ситуационных задач требуется различный комплекс диагностики. Диагностика неисправностей проходит при уже развитых дефектах. Диагностика превентивная – для предупреждения дефектов. Параметрическая подходит и туда и туда.
Параметрическая диагностика на основе контрольных измерений осуществляется после введения этой информации вручную. (т.е диагностика на основе каких-либо численных данных: параметрах и перекачиваемой нефти, температура, давление т.д)
Эффективность метода параметрической диагностики зависит от правильности выбора исходных данных, а также от совершенства диагностической логики, используемой для их обработки. Большая часть дефектов и неисправностей может быть установлена методами вибродиагностики, пригодными для обнаружения дефектов практически всех элементов агрегата.
Диагностика неисправностей это диагностика, которая проводится после выхода из стоя одной из деталей оборудование. Пример: Электродвигатель вместе с исполнительным механизмом не вращается при подаче на него напряжения. Возможные причины - сгорела обмотка, двигатель заклинило. Следовательно, нужно проверять обмотку статора и подшипники.
Различают два основных вида поиска отказавших элементов - последовательный и комбинационный.
При использовании первого метода проверки в аппаратуре выполняются в некотором порядке. Результат каждой проверки сразу же анализируется, и если отказавший элемент не определен, то поиск продолжается.
При использовании комбинационного метода состояние объекта определяется путем выполнения заданного числа проверок, порядок выполнения которых безразличен. В качестве критерия для сравнения различных систем поиска неисправностей обычно используется среднее время обнаружения отказа. Могут быть применены и другие показатели - количество проверок, средняя скорость получения информации и пр.
На практике помимо рассматриваемых нередко используется эвристический метод диагноза. Строгие алгоритмы здесь не применяются. Выдвигается определенная гипотеза о предполагаемом месте отказа. Осуществляется поиск.
Диагностика превентивная Основывается на мониторинге и недопущения неисправности. Собираются данные о работе устройства и эти данные сравниваются с правильной работой устройства, без отклонений. Подходят виды неразрушающего контроля.
3.. Методы неразрушающего контроля (виды, приборы)
Неразрушающий контроль – это совокупность таких видов неразрушающего контроля, которые требуют применения специальных веществ, сложных приборов и достаточно наукоемких технологий. Из всех видов неразрушающего контроля, используемых на опасных производственных объектах, лишь один не относится к категории физических – это визуальный и измерительный контроль (ВИК). Таким образом, сочетание этих понятий можно выразить формулой:
Неразрушающий контроль = Неразрушающий физический контроль + ВИК.
По степени проникновения в материал все виды неразрушающего физического контроля условно подразделяют на две категории: поверхностные и объемные.
Поверхностные виды (методы) неразрушающего контроля – это такие, которые позволяют обнаруживать только дефекты, имеющие выход на доступную для контроля поверхность материала объекта.
Объемные виды (методы) неразрушающего контроля – это такие, которые дают возможность обнаруживать преимущественно внутренние дефекты материала, а поверхностные дефекты выявляются, только если они достаточно крупные.
Основными методами неразрушающего контроля являются:
• магнитный — основанный на анализе взаимодействия магнитного поля с контролируемым объектом. Применяется для выявления дефектов в ферромагнитных металлах (никель, железо, кобальт и ряд сплавов на их основе);
• электрический — основанный на регистрации параметров электрического поля, взаимодействующего с контролируемым объектом или возникающего в контролируемом объекте в результате внешнего воздействия;
• вихретоковый — основанный на анализе взаимодействия электромагнитного поля вихретокового преобразователя с электромагнитным полем вихревых токов, наводимых в контролируемом объекте;
• радиоволновой — основанный на регистрации изменений параметров электромагнитных волн радиодиапазона, взаимодействующих с контролируемым объектом;
• тепловой — основанный на регистрации изменений тепловых или температурных полей контролируемых объектов, вызванных дефектами. Основной параметр в тепловом методе это - распределение температуры по поверхности объекта, так как несет информацию об особенностях процесса теплопередачи, его внутренней структуре, наличии скрытых внутренних дефектов и режиме работы объекта;
• оптический — основанный на регистрации параметров оптического излучения, взаимодействующего с контролируемым объектом;
• радиационный — основанный на регистрации и анализе проникающего ионизирующего излучения после взаимодействия с контролируемым объектом. Слово «радиационный» может заменяться словом, обозначающим конкретный вид ионизирующего излучения, например, рентгеновский, нейтронный и т. д.;
• акустический(ультразвуковой) — основанный на регистрации параметров упругих волн, возбуждаемых или возникающих в контролируемом объекте. При использовании упругих волн ультразвукового диапазона (выше 20 кГц) допустимо применение термина «ультразвуковой» вместо термина «акустический»;
• проникающими веществами — основанный на проникновении веществ в полости дефектов контролируемого объекта. Термин «проникающими веществами» может изменяться на «капиллярный», а при выявлении сквозных дефектов — на «течеискание»;
• виброакустический — основанный на регистрации параметров виброакустического сигнала, возникающего при работе контролируемого объекта.
• визуальный(ВИК) - выявление заусенцев, вмятин, ржавчины, прожогов, наплывов, и других видимых дефектов.
4. Моделирование и методы анализа диагностической информации
Процесс проведения анализа риска включает следующие основные этапы:
планирование и организацию работ;
идентификацию опасностей;
оценку риска;
разработку рекомендаций по уменьшению риска.
При выборе и применении методов анализа риска рекомендуется придерживаться следующих требований:
метод должен быть научно обоснован и соответствовать рассматриваемым опасностям;
метод должен давать результаты в виде, позволяющем лучше понять формы реализации опасностей и наметить пути снижения риска;
метод должен быть повторяемым и проверяемым.
Сбор таких данных возможен только путем применения надежных измерительных систем, использующих современные аппаратные средства, обеспечивающие высокую точность измерений и автоматическую возможность анализа ситуации.
Все виды технического контроля опасных производственных объектов разделяются на 3 группы: разрушающий контроль, повреждающий контроль и неразрушающий контроль
Визуальный и измерительный контроль
Контроль является одним из основных методов, применяемых при диагностировании оборудования. Метод позволяет выявлять поверхностные дефекты металла, такие как трещины, язвенную коррозию, волосовины, а также качество исполнения узлов и элементов оборудования
Ультразвуковой контроль
Ультразвуковой контроль сплошности основного металла и сварных швов производится с целью выявления скрытых дефектов и их оценки. Для этого применяются ультразвуковые дефектоскопы с памятью настроек и результатов измерений, а также автоматизированные сканирующие системы
Ультразвуковое сканирование
Автоматизированная ультразвуковая сканирующая система Canon M500/600, используемая специалистами ОАО «Техдиагностика» при проведении диагностических работ, позволяет обеспечить требуемые качество и достоверность результатов ультразвукового контроля. Хранение параметров и результатов УЗ контроля на сменных носителях информации позволяет проводить периодический контроль оборудования с неизменными настройками с целью мониторинга состояния оборудования
Ультразвуковая толщинометрия
Измерение толщины металла проводится с целью выявления зон коррозионного и эрозионного износа. Полученные результаты служат исходными данными при проведении нормативных и уточненных расчетов прочности и ресурса в экспертизе промышленной безопасности
Магнитопорошковая дефектоскопия
Метод является одним из наиболее эффективных и высокочувствительных к поверхностным и подповерхностным дефектам и позволяет обнаруживать непровары сварных соединений, закаты, волосовины, трещины различного происхождения и другие дефекты и несплошности металла
Капиллярная дефектоскопия
Метод является одним из высокопроизводительных и эффективных при выявлении поверхностных дефектов. Капиллярная дефектоскопия используется с целью уточнения и документирования дефектов, выявленных в процессе визуального и измерительного контроля.
Дата добавления: 2018-02-28; просмотров: 703; Мы поможем в написании вашей работы! |
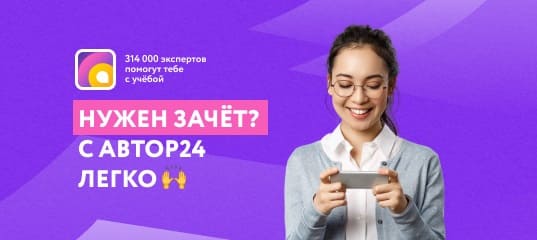
Мы поможем в написании ваших работ!