Принципиально новые конструкции реакторов, используемые ОАО «ЯТУ»
Реактор для получения активных марок техуглерода. Практическим результатом множества проведённых исследований является создание и внедрение в промышленную эксплуатацию реакторов с двух-, четырёх- и шестиканальной зоной реакции. Принципиальная конструкция таких реакторов представлена на рисунке 1.13.
Рисунок 1.13 – Принципиальная конструкция реактора с многоканальной зоной реакции:
а – двухканальный; б – четырёхканальный; в – шестиканальный
Диаметры каналов выбирались исходя из условия сохранения равенства их суммарного сечения эквивалентному сечению канала диаметром 0,3 м (Dэкв). Тогда диаметр п-го канала Dn будет равен:
а суммарная длина окружности каналов:
Если в качестве эквивалентного принять диаметр 0,3 м, то диаметр одного канала двухканального реактора будет равен 0,22 м, для четырёхканального 0,15 м, для шестиканального – 0.125 м.
В настоящее время двухканальные реакторы заменены шестиканальными, что и подтверждает исходную концепцию. Весь производимый объём активного техуглерода выпускается на 4- и 6-канальных реакторах.
Приведённые выше конструкции реакторов постоянно находятся в стадии совершенствования в направлении создания более термостойкой и газоплотной футеровки, точного определения длин и диаметров канала, мест ввода сырья и закалочной воды и т.д.
Реактор для получения полуактивных марок техуглерода. Рассмотренные выше конструкции реакторов с многоканальной зоной реакции предназначены исключительно для производства активных марок технического углерода. Получение полуактивных марок характеризуется меньшими скоростями реакции и более длительным временем пребывания продуктов реакции до их охлаждения, что обуславливается сравнительно низкими температурами в зоне реакции и её большим объёмом (диаметром и протяжённостью).
|
|
Конструкция большегрузного реактора производства полуактивных марок техуглерода в общем случае должна обеспечивать:
- полное сгорание природного газа в камере горения;
- низкую удельную площадь поверхности (по любому методу её определения);
- требуемое значение показателя «светопропускания толуольного экстракта», который является оценкой количества неразложившихся углеводородов на поверхности частиц;
- требуемую чистоту продукта (минимальное коксование реактора).
Многолетний опыт создания реакторов для получения полуактивных марок технического углерода в производстве привёл к конструкции реакторов, представленной на рисунке 1.14.
Рисунок 1.14 – Принципиальная конструкция реактора для получения полуактивных марок техуглерода
|
|
Данная конструкция наиболее полно на данный момент отвечает высказанным выше требованиям. Конструкция камеры горения и горелочного устройства реактора, обеспечивающие полное горение газа, подробно были рассмотрены ранее. Предусмотрен ввод сырья аксиальной пневматической форсункой или четырьмя радиальными механическими форсунками. Возможна и подача сырья аксиальной и радиальной форсунками одновременно. Время пребывания продуктов реакции до их закалки водой может достигать одной секунды, что обеспечивает нормированное значение показателя «светопропускание толуольного экстракта». Вертикальная часть реактора большого диаметра выполняет функцию гравитационного уловителя частиц кокса и футеровки. На реакторе данной конструкции получают технический углерод марок N660, N650, N539, N550, П514.
1.5. РАСЧЁТ ПРОЦЕССОВ САЖЕОБРАЗОВАНИЯ
Для расчёта процессов сажеобразования составляют материальный и тепловой балансы. Необходимыми данными для этого являются:
- количество газа и сырья, подаваемых в реакторы, печи или другие аппараты;
- химический состав газа и сырья;
- состав технического углерода и газообразных продуктов процесса сажеобразования;
|
|
- количество образуемого нагара или кокса.
Из материального баланса определяют количество воздуха, необходимого для процесса, а также выход технического углерода и газообразных продуктов при сажеобразовании.
Тепловой баланс сажеобразования составляют по данным материального баланса.
При составлении материального баланса исходят из того, что масса продуктов, получаемых в результате процесса сажеобразования. Таким образом, масса сажи, отходящих газов и нагара должна равняться массе сырья и воздуха, поступающих в печь.
Во всех расчётах, связанных с материальным балансом, объём всех газообразных продуктов, участвующих в процессе, приводят к нормальным физическим условиям. Фактический объём газов V (м3) при температуре и давлении, при которых они участвуют в процессе, может быть найден по формуле
где V0 – объём газов, м3 при 0 °С и 101325 Па; t – фактическая температура газов, °С; Р – давление газов, Па; Р0 – атмосферное давление, Па.
Содержание углерода, водорода, кислорода и азота в газах (кг/м3) определяют по данным о составе этих газов:
Где СН4, С2Н4, С3Н6, С3Н8, СО2, СО, Н2, О2 и N2 означают содержание в газах метана, этилена, этана, пропилена, пропана, двуокиси углерода, окиси углерода, водорода, кислорода и азота в объёмн. %. Состав высших углеводородов процесса можно условно считать С2Н4.
|
|
1.6. РЕКУПЕРАТИВНЫЙ ПОДОГРЕВ ВОЗДУХА
Подогрев воздуха за счёт тепла реакционных газов является одним из самых эффективных приёмов возвращения энергии в процесс (рекуперация тепла). Возвращения тепла с воздухом на горение позволяет снизить расход топлива, повысить нагрузку, а также снизить расход воды на охлаждение, что повышает калорийность отходящего газа, используемого далее в котельных или сушилках.
Впервые рекуперативный подогреватель воздуха фирмы «RECUPERATOR» был использован в 1957 году на одном из заводов Германии. Он обеспечивал предварительный нагрев воздуха до 400 °С.
На новых отечественных производствах 1960-х годов циклонные реакторы также оснащались рекуперативными подогревателями ПВ-35 (рисунок 1.15).
Кожухотрубный подогреватель ПВ-35 состоит из восходящей 1 и исходящей 6 ветвей, соединённых в верхней части воздушным коллектором 7 и коллектором углеродогазовой смеси 4. Внутри каждой ветви расположен трубный пучок 2 из семи труб, по которым проходит техуглеродогазовая смесь. Воздух поступает в межтрубное пространство ветви (секция 3), а затем по коллектору 7 в межтрубное пространство нисходящей ветви 6. Углеродогазовая смесь из одной ветви в другую подаётся по коллектору 4, снабжённому предохранительным клапаном 5. Подогрев воздуха в данном аппарате мог достигать значений 350–400 °С при температуре техуглеродгазовой смеси 650–750 °С.
Для цилиндрических реакторов производительностью по сырью 1500 кг/час был создан воздухоподогреватель с большей поверхностью теплообмена ПВ-88 (здесь и далее цифры в обозначении типа подогревателя указывают на величину поверхности теплообмена в м2).
Кожухотрубный прямоточный подогреватель ПВ-88 показан на рисунке 1.16.
Подогреватель ПВ-88 включает в себя цилиндрический корпус 8 с компенсатором 7 и трубными досками 1 и 5, в которых закрепляется трубный пучок 2. Воздух движется по межтрубному пространству, направление движения которого изменяется перегородками 3 и 4. Для снижения потерь тепла в окружающую среду подогреватель снабжён теплоизоляцией 6. Температура подогрева воздуха достигала 450–460 °С на реакторах с нагрузкой по сырью 1500–1700 кг/час. Опыт эксплуатации данных аппаратов выявил их низкую надёжность. Основная причина выхода из строя аппарата – отрыв труб от трубных решёток вследствие отсутствия их компенсации.
![]() | ![]() |
Рисунок 1.15 – Рекуперативный подогреватель воздуха ПВ-35: 1 – восходящая ветвь; 2 – трубный пучок; 3 – компенсаторы; 4 – коллектор углеродогазовой смеси; 5 – предохранительный клапан; 6 – нисходящая ветвь; 7 – воздушный коллектор | Рисунок 1.16 – Рекуперативный подогреватель ПВ-88: 1 – нижняя трубная доска; 2 – трубный пучок; 3, 4 – перегородка; 5 – верхняя трубная решётка; 6 – изоляция; 7 – компенсатор; 8 - корпус |
Вопросы дальнейшего повышения температуры подогрева потребовали обеспечения более высокой эксплуатационной надёжности аппарата.
В начале 1980-х годов ВНИИТУ разработал серию «самокомпенсирующихся» воздухоподогревателей различной производительности. Особенность конструкции такого аппарата состоит в том, что его трубный пучок выполнен в виде прямого угла (рисунок 1.17).
Схема движения воздуха в аппарате показана на рисунке 1.18.
В первой зоне подогревателя (на выходе высокотемпературного аэрозоля в трубное пространство) схема движения теплоносителя является прямоточной с перекрёстным ходом, а во второй зоне (на выходе отдающего теплоагента из трубного пространства) – противоточной с перекрёстным ходом. Принятая схема движения позволяет защитить входную трубную решётку от перегрева и в то же время эффективно использовать теплообменную поверхность.
Серийно изготавливаются три типоразмера подобных аппаратов ПВ-53, ПВ-85, ПВ-185, рассчитанных на различную производительность и имеющих поверхность теплообмена 53 м2, 85 м2 и 185 м2 соответственно.
При температуре технического углерода на входе 800–850 °С достигается подогрев воздуха до значений 500–550 °С.
Рассмотренные воздухоподогреватели в настоящее время являются самыми распространёнными на отечественных заводах технического углерода. Они зарекомендовали себя как наиболее надёжные в эксплуатации. Следует отметить, что не всегда удаётся поддерживать температуру на входе аппарата порядка 800–850 °С, а соответственно и указанную выше степень подогрева воздуха. Такие температуры на входе по аэрозолю возможны лишь тогда, когда организована футеровка хвостовой части реактора до самой нижней трубной доски, что выполнимо не всегда. Поэтому на большинстве предприятий температуру на входе аэрозоля поддерживают в пределах 700–750 °С и соответственно достигают подогрева воздуха в пределах 460–480 °С.
В зависимости от требуемой производительности реактора используют несколько параллельно установленных подогревателей. На ОАО «Ярославский техуглерод» имеется опыт эксплуатации реакторов для производства активных марок технического углерода с установкой трёх параллельно собранных подогревателей типа ПВ-85 и даже пяти подогревателей типа ПВ-53. На реакторах для производства полуактивных марок технического углерода установлены по два воздухоподогревателя ПВ-85.
При переходе на рыночную экономику и прекращении централизованного финансирования отраслевой науки дальнейшие разработки по созданию рекуперативных подогревателей воздуха в 90-х годах были полностью прекращены. Некоторые предприятия всё же предпринимали попытки повышения эффективности рекуперации тепла процесса. Так, в производстве технического углерода ОАО «Ярославский техуглерод» был создан аппарат предварительного подогрева воздуха на базе газоохладителя, получивший название «подогреватель воздуха 1-й ступени» (см. рисунок 22).
Аппарат представляет собой две вертикально расположенные секции 1, соединённые между собой коллекторами по аэрозолю 2 технического углерода и воздуху 3 (см. рисунок 22). Каждая секция представляет собой трёхтрубный теплообменный аппарат. Аэрозоль технического углерода после воздухоподогревателей проходит в межтрубном пространстве, образованном внутренней 4 и средней 5 трубами. Воздух проходит в пространстве, образованном средней 5 и наружной 6 трубами. Средняя труба имеет оребрение своей внешней поверхности. Суммарная площадь теплообмена средней трубы совместно с рёбрами составляет порядка 300 м2. Воздух проходит через параллельные ветви аппарата и направляется для дальнейшего подогрева в воздухоподогреватели. По внутренней трубе 4 последовательно через обе ветви просасывается воздух, который далее поступает к горелкам камеры обогрева сушильного барабана БСК-40. Аппарат обеспечивает подогрев воздуха, подаваемого к реактору, до температуры порядка 200 °С, а воздуха к сушильному барабану до температуры порядка 150–160 °С. При этом температура аэрозоля технического углерода снижается на 100–120 °С, что позволило уменьшить расход воды на холодильник-ороситель на 1500–2000 кг/час. В целом при производстве активных марок технического углерода температура нагрева воздуха подогревателем первой ступени в совокупности со стандартным подогревателем типа ПВ-85 достигает порядка 510–550 °С при температуре в зоне закалки реактора ~700 °С. Очевидно, что есть ещё существенный резерв по подогреву за счёт повышения температуры в зоне закалки до значений 800–880 °С.
Однако эффект рекуперативного подогрева воздуха заключается не только в экономии топлива. При ограниченной температуре в камере горения (1700 °С) при повышении температуры воздуха, что позволяет догрузить реактор по сырью. Совершенно очевидно, что охлаждение аэрозоля за счёт отбора сырья в воздухоподогревателе уменьшает расход воды.
1.7. МЕТОДИКА РАСЧЁТА РЕАКТОРА ПОЛУЧЕНИЯ ТЕХУГЛЕРОДА
1.8. КОНТРЛЬ, АВТОМАТИЗАЦИЯ И ОБСЛУЖИВАНИЕ РЕАКТОРНОГО ПРОЦЕССА
Процесс получения технического углерода в реакторе наиболее насыщен параметрами контроля и регулирования в сравнении с другими процессами общей технологической линии точность поддержания заданных значений режимных параметров процесса должна быть достаточно высокой, чтобы получить стабильные показатели качества.
Были попытки создания датчиков качества техуглерода в потоке. Однако до настоящего времени в промышленной практике управление процессом получения технического углерода в реакторе базируется на системах автоматической стабилизации режимных параметров процесса. Так при проведении процесса в реакторе контролируются и регулируются следующие параметры.
- Расход ВСД автоматически поддерживается на заданном уровне указанного расхода путём воздействия на регулирующею заслонку через позиционеры. В системе осуществляется суммирование расходов ВСД, определяется общий расход в реактор. При этом измеренные расходы ВСД корректируются по его действительной температуре, и вычисляется истинный расход. Раздвоение потока ВСД на два потока с отдельными измерениями и вновь объединение связны с необходимостью измерения малых расходов ВСД при розжиге и разогреве реактора. Температура ВСД контролируется на выходе из подогревателей обеих ступеней термопарами, и через преобразователи сигнал поступает в систему управления.
- Расход природного газа измеряется с помощью сужающего устройства с дифманометром и регулируется в соотношении с общим расходом ВСД. На линии газа установлен предохранительный клапан типа ПКН, который отсекает подачу газа при падении давления ВСД ниже предельного значения.
- Контролируется и регулируется расход сырья в каждый реакционный канал. Система управления суммирует расходы сырья по каналам и регистрирует его. При изменении задания общего расхода сырья оператором он автоматически делится на каждый канал с соответствующим автоматическим изменением задания по каждому контуру регулирования.
- Расход химически очищенной воды (ХОВ) в зону предзакалки контролируется и автоматически регулируется диафрагмой с дифманометром.
- Контролируется давление в реакторе, а также температуры техуглеродгазовой смеси после воздухоподогревателей второй и первой ступеней.
- Подробнее рассмотрим организацию и управление системой подачи щелочной присадки. Система включает в себя ёмкость для приготовления добавки, рабочую ёмкость добавки и насос-дозатор. Расход добавки составляет порядка 2–6 л/ч, поэтому непосредственное его инструментальное измерение сложно выполнить. В данной схеме используется дополнительная расходная ёмкость малого объёма, но достаточной высоты, так что и при указанных выше расходах уровень добавки в ней во времени изменяется существенно. Этот уровень измеряется пьезометрическим методом. Регулирование расхода щелочной добавки осуществляется с помощью частотно-регулируемого привода дистанционно. При изменении частоты питающего напряжения электродвигателя насоса-дозатора изменяется его скорость вращения, а значит, и скорость хода плунжера насоса, т.е. его производительность.
Дата добавления: 2018-02-28; просмотров: 460; Мы поможем в написании вашей работы! |
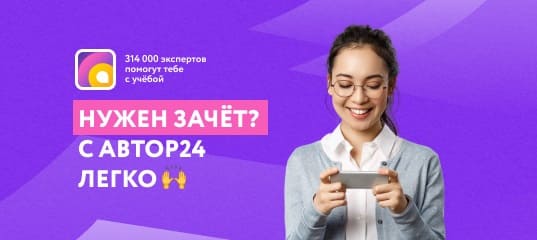
Мы поможем в написании ваших работ!