Футеровка реакторов и огнеупорные материалы
РЕАКЦИОННОЕ ОБОРУДОВАНИЕ ПОЛУЧЕНИЯ ТЕХНИЧЕСКОГО УГЛЕРОДА
1.1. ОСНОВНЫЕ СПОСОБЫ ПОЛУЧЕНИЯ ТЕХУГЛЕРОДА
1.2. ТЕХНОЛОГИЯ ПОЛУЧЕНИЯ ПЕЧНОГО ТЕХУГЛЕРОДА
Технический углерод (ТУ) вырабатывается путём термоокислительного разложения углеводородов под действием высокой температуры при недостатке воздуха. Процесс разложения осуществляют сжиганием в печи или реакторе какого-либо вспомогательного горючего или сжиганием части того сырья, из которого вырабатывают ТУ. Сырьё вводят в печь в виде капель, образованных при распылении его форсунками пневматического или механического действия.
В печи происходит одновременно несколько различных процессов:
- сгорание вспомогательного горючего или части сырья для получения тепла, необходимого для термического разложения углеводородов;
- испарение капель сырья;
- частичное неполное сгорание сырья с образованием вследствие недостатка кислорода окиси углерода и паров воды;
- термическое разложение углеводородов сырья с получением частиц ТУ (начало сажеобразования);
- взаимодействие между полученными частицами и газообразными продуктами процесса.
Каждый из этих процессов зависит от ряда условий, которые можно регулировать.
Создание необходимой температуры для разложения углеводородов зависит от количества сжигаемого вспомогательного топлива (или части сырья), его теплотворной способности, от количества и температуры воздуха, подаваемого в печь. С повышением температуры интенсивность процессов, протекающих в печи возрастает.
|
|
Скорость испарения и частичного сгорания капель сырья зависит от степени его распыленности. Чем меньше размеры капель, тем быстрее протекают эти процессы. Степень распылённости сырья (при одной и той же конструкции форсунки) в свою очередь зависит от температуры сырья (чем выше температура, тем меньше размеры капель), а при пневматических форсунках – от количества распыливающего воздуха (размеры капель уменьшаются с увеличением количества воздуха).
Образование окиси углерода и паров воды при термическом разложении сырья предшествует образованию ТУ. Последнее начинается лишь тогда, когда содержание кислорода в зоне реакции снижается до 1,5–2 объёмн. %. Выход ТУ зависит от количества воздуха, поступающего в печь: с уменьшением подачи воздуха на единицу массы сырья и вспомогательного горючего выход ТУ увеличивается. Однако сокращать подачу воздуха можно до строго определённого предела, превышение которого может вызвать снижение степени дисперсности ТУ.
Увеличение интенсивности процессов в печи за счёт повышения температуры и сокращения размеров капель сырья приводит к повышению дисперсности получаемого ТУ.
|
|
Степень структурности ТУ можно регулировать, изменяя содержание ароматических углеводородов в сырье и время пребывания ТУ в зоне высоких температур.
При производстве печного ТУ часть сырья иногда не успевает разложиться и неразложившиеся углеводороды адсорбируются поверхностью сажевых частиц, что резко ухудшает качество ТУ. Этого можно избежать, повышая температуру процесса и степень распыления сырья.
Для получения ТУ с определённой степенью дисперсности и структурности необходимо регулировать время пребывания её в зоне реакций; это достигается быстрым охлаждением саже-газовой смеси путём впрыскивания в реактор воды (испаряясь, вода понижает температуру сажи и газов). Быстрое охлаждение саже-газовой смеси до 700–750° С приостанавливает рост сажевых частиц и прекращает взаимодействие сажи с газообразными продуктами, выделяемыми в процессе сажеобразования.
Влияние изменения основных параметров процесса на свойства ТУ и на его выход показано в таблице 18.
Печной способ получения ТУ является наиболее распространённым, и в настоящее время до 80% ТУ вырабатывают этим способом
|
|
К преимуществам печного способа относятся:
- возможность получения ТУ с разнообразными технологическими свойствами. Так, печным способом можно получить высокодисперсный ТУ с удельной поверхностью до 140 м2/г, ТУ, приближающийся по свойствам к канальной саже и малодисперсный с удельной поверхностью 16 м2/г;
- высокий выход ТУ, вследствие чего себестоимость печного ТУ, как правило, ниже себестоимости ТУ, выработанного другими способами;
- сравнительно несложное управление процессом сажеобразования, что позволяет получать ТУ с заранее заданными свойствами;
- возможность полной автоматизации процесса сажеобразования.
При других способах полностью автоматизировать процесс получения ТУ не удаётся.
1.3. СТАДИЙНОСТЬ ПРОЦЕССА И ОБЩИЕ ЭЛЕМЕНТЫ РЕАКТОРОВ
В настоящее время в производстве ТУ превалирует так называемый «печной» способ его получения из жидкого углеводородного сырья с использованием вспомогательного топлива. Процесс с использованием вспомогательного топлива (газообразного или жидкого) называют комбинированным. Основная масса товарного продукта для шинной промышленности производится именно этим способом. Получение дисперсного технического углерода в реакторах является основным технологическим процессом производства, ответственным за выход и потребительские свойства товарного продукта. Реактор условно рассматривается как аппарат, состоящий из нескольких зон, в которых последовательно протекают и частично накладываются друг на друга стадии процесса:
|
|
- полное горение вспомогательного топлива для получения тепловой энергии и обеспечения температурных условий разложения углеводородного сырья;
- распыливание жидкого сырья, его смешение с газами горение топлива и испарение;
- неполное горение сырья в условиях недостатка кислорода, остающегося после сжигания топлива, для обеспечения дополнительной энергии;
- разложение углеводородного сырья в высокотемпературном газовом потоке с образованием частиц ТУ;
- газификация образовавшихся углеродных частиц при их взаимодействии с окислительными составляющими (O2, H2O, CO2) высокотемпературного газового потока;
- охлаждение углеродного аэрозоля (техуглеродогазовой смеси).
В соответствии с теоретическими предпосылками некоторые из названных стадий процесса можно рассматривать как нежелательные (например, газификация углеродных частиц), и их влияние должно быть в максимальной степени уменьшено.
Желательно обеспечить:
- максимальную температуру газов полного горения топлива (минимальный избыток воздуха);
- минимальное время испарения сырья и смешивание его паров с газами полного горения топлива;
- минимальное время контактирования углеродных частиц с реакционным газом в условиях высоких температур;
- высокую производительность реактора.
Развитие технологии и аппаратурного оформления процесса направлено на достижение вышеуказанных целей. Темпы этого развития связаны с созданием более термостойких огнеупоров, новых конструкций воздухоподогревателей и других элементов реактора, повышением давления воздуха на горение.
Общей чертой всех реакторов является наличие газонепроницаемого стального корпуса, что позволяет строго контролировать все материальные потоки участвующие в процессе. Корпус реактора футерован изнутри несколькими концентрическими слоями огнеупорного материала. Для самого внутреннего слоя используется газонерпоницаемый, наиболее термостойкий материал. Последующие к наружным сторонам слои обладают меньшей термостойкостью и большей пористостью, что обеспечивает постепенное возрастающее изоляционное действие. Футеровка может быть выполнена из кирпичей или фасонных блоков. Внутренняя конфигурация реактора – длина и диаметры обуславливают скорости и время пребывания реакционных потоков в различных зонах по длине реактора. Геометрия реакторов может существенно различаться у разных производителей техуглерода. В большинстве случаев фирмы, производящие ТУ, имеют собственную конструкцию реакторов в большей или меньшей степени отличающуюся от используемых конкурентами. Конструкции реакторов отличаются также в зависимости от марок ТУ, производимого ими. При производстве ТУ для резин (шинная и резинотехническая промышленность) используют два основных типа реакторов. Реакторы для производства активных высокодисперсных марок ТУ – класса 100, 200, 300 по ASTM и реакторы для производства полуактивных марок – класса 500, 600 и 700. В зарубежной литературе их называют реакторами твёрдого техуглерода (реакторами протекторного техуглерода) в первом случае и реакторами мягкого техуглерода (реакторами каркасного техуглерода) – во втором. Марки технического углерода с более мелкими первичными частицами (высокой удельной площадью поверхности) получаются при более высоких температурах реакции, чем марки с более крупными частицами. Очевидно, что в первом случае реакция получения техуглерода протекает быстрее и, следовательно, реакторы разрабатываются для более высоких скоростей реакции и малого времени пребывания. Во втором случае реакция происходит при сравнительно низких температурах и требуется более длительное время пребывания, что может осуществляться в реакторах большого объёма.
Рассмотрим подробнее функции отдельных элементов реактора – зон горения, смешения, реакции и закалки.
1. Зона горения. Энергия для процесса вырабатывается в камере горения в результате реакции окислителя (обычно воздуха, иногда воздуха, обогащённого кислородом) с газообразным или жидким топливом. Полное горение топлива необходимо для оптимального использования энергии в процессе получения технического углерода.
В практике это достигается правильным выбором конструкции и количества газовых горелок, организации эффективного смешения газа с воздухом, соотношением диаметра и длины камеры горения (объёмом камеры горения). Практика показала, что эта задача наиболее сложно решается для большегрузных реакторов при производстве полуактивных марок технического углерода. У данных реакторов зона реакции должна иметь диаметр, близкий к диаметру камеры горения, что при больших расходах газа и воздуха (высоких скоростях газовоздушного потока) может привести к пролёту в зону реакции продуктов неполного горения.
На рисунке 1.1 и 1.2 представлены конструкции горелочного устройства и камеры горения большегрузного реактора для получения полуактивных марок техуглерода.
Рисунок 1.1 – Горелочное устройство:
1 – прорези в воздушных трубках; 2 – фланец крепления несъёмной колодки сырьевой форсунки; 3 – колодка несъёмная сырьевой форсунки; 4 – колодка съёмная сырьевой форсунки; 5 – сырьевая форсунка; 6 – пневмозатвор; 7 – съёмная колодка газовой горелки; 8 – несъёмная колодка газовой горелки; 9 – воздушная труба камеры; 10 – воздушная камера; 11 – грелка газовая
Рисунок 1.2 – Камера горения большегрузного реактора для получения полуактивных марок техуглерода
Горелочное устройство (см. рисунок 1.1) включает в себя четыре газовые горелки 11, расположенные по осям воздушных труб 9, в которые из воздушной камеры 10, через четыре прорези 1 в каждой, поступает воздух на горение. Гам под давлением 1,5–2,0 атм. подаётся струями перпендикулярно воздушному потоку, чем обеспечивается высокая степень предварительного смешивания. Горелки симметрично расположены по образующей окружности с диаметром большим, чем диаметр входа зоны реакции. Таким образом, газовоздушный поток от горелок направлен на футеровку задней стенки камеры горения. Для выполнения этого условия диаметр камеры горения (см. рисунок 1.2) был значительно увеличен. Опыт эксплуатации показывает, что полное горение природного газа достигается при его расходе до 1300 м3/час.
Проконтролировать полноту сгорания топлива можно по составу газов горения, взяв пробу, например, через канал сырьевой форсунки. Отсутствие окиси углерода подтверждает полноту сгорания топлива.
Известно множество конструкций газовых горелок. В реакторе для производства активных марок ТУ последнее время также применяют одногорелочные устройства.
Воздух на горение предварительно нагревается в рекуперативных подогревателях. Следует отметить, что повышение температуры воздуха приводит к увеличению скорости горения топлива и, как следствие, к упрощению конструкции горелочных устройств.
2. Зона смешения. В зоне смешения в горячие газы, выходящие из камеры горения, вводится сырьё. Эта область характеризуется высокими усилиями сдвига, создаваемыми изменениями площадей поперечных сечений при значительной турбулентности потока за счёт высокой его скорости. Сырьё вводится форсунками, которые конструируются таким образом, чтобы достичь наилучшего распыла и более равномерного распределения капель в газовом потоке. В общем случае, чем меньше размер капель, тем быстрее они испаряются и тем легче получить более мелкие частицы технического углерода. От степени распыла сырья в определённой степени зависит структурность технического углерода, а также вероятность образования грита.
Применяются сырьевые форсунки двух видов – пневматического распыла и механического распыла. На рисунке 1.3 представлена конструкция пневматической форсунки, которая широко использовалась на отечественных заводах технического углерода и, возможно, сохранилась ещё до настоящего времени.
На рисунке 1.4 показан вариант пневматической форсунки в собранном виде. Форсунки данной конструкции широко использовались в производстве при получении активных марок технического углерода и ограниченно используются в настоящее время при получении полуактивного технического углерода при аксиальной подаче сырья. Эту конструкцию можно отнести к классическому упрощённому варианту пневматической форсунки.
Рисунок 1.3 – Пневматическая ультразвуковая форсунка:
1 – воздушная труба; 2 – сырьевая труба; 3 – переходная муфта; 4 – корпус форсунки; 5 – корпус сырьевой улитки; 6 – сопло; 7 – вихревая (воздушная) камера; 8 – улитка; 9 – корпус сырьевой улитки
Рисунок 1.4 – Пневматическая форсунка:
1 – рукоятка зажимного устройства; 2 – зажимной винт; 3 – сырьевой канал в съёмной и несъёмной колодках; 4 – воздушный канал в съёмной и несъёмной колодках; 5 – ручка форсунки со съёмной колодкой; 6 – съёмная колодка; 7 – прокладка; 8 – несъёмная колодка; 9 – воздушная труба; 10 – сырьевая труба; 11 – корпус наконечника; 12 – распылитель; 13 – завихритель воздуха; 14 – завихритель сырья
При радиальной подаче сырья, когда скорости газов горения в смесительном канале достигают значений порядка 400–500 м/с, требования к форсункам снижаются. Дробление капель происходит за счёт высоких скоростей газового потока. Поэтому распыливание сырья при его радиальной подаче преимущественно осуществляют механическими форсунками, без жёстких требований к степени распыла. Иногда такой ввод сырья называют «мультиструйным». Во избежание коксования сырья на стенках скорость струи сырья при заданных режимах должна быть такой, чтобы она не достигала противоположной стенки и не сносилась потоком газа на ближайшую стенку. Однако требования к точности изготовления и чистоте обработки остаются высокими.
В качестве примера на рисунке 1.5 показана принципиальная конструкция наконечника-распылителя сырьевых форсунок, используемых при получении активных марок технического углерода.
На рисунке 1.6 представлена сырьевая форсунка механического распыла, используемая для радиального ввода сырья при производстве полуактивных марок техуглерода.
Рисунок 1.5 – Наконечники-распылители механической форсунки:
а – прямой; б - угловой
Рисунок 1.6 – Сырьевая форсунка механического распыла с завихрителем сырья
В отличие от представленных выше она снабжена завихрителем сырья с центральным отверстием, которое обеспечивает более равномерную заполненность факела.
Зона смешения – одна из основных определяющих частей реактора, т.к. её геометрия непосредственно влияет на свойства получаемого технического углерода.
Площадь поперечного сечения этой зоны определяет пропускную способность реактора при фиксированном давлении воздуха, подаваемого на горение. В различных конструкциях реакторов сырьё подаётся аксиально, радиально, или комбинированным способом – аксиальными и радиальными форсунками одновременно в заданном соотношении.
Известны различные конструкции зоны смешения, в которых её вход и выход могут быть ступенчатыми или коническими. Совершенно необычна и оригинальна конструкция зоны смешения в реакторах ОАО «Ярославский технический углерод» для получения активных марок техуглерода. При сохранении эквивалентной площади сечения она выполнена в виде нескольких (от двух до шести) изолированных друг от друга каналов (сопел) равного диаметра, в каждый из которых вводится равная доля общего расхода сырья. В такой многоканальной зоне осуществляется не только эффективное смешение сырья с горячими газами, но и его испарение. Поэтому в данных реакторах зона смешения становится как бы начальной частью зоны реакции.
3. Зона реакции. В зоне закалки заканчивается испарение сырья с кислородом, содержащимся в газах горения. Под воздействием высоких температур происходит разложение углеводородов, находящихся в газообразной фазе, и выделение технического углерода. Температура в зоне реакции в большей мере определяет размер первичных частиц техуглерода и ограничивается термостойкостью футеровки. Размер зоны реакции определяется производительностью реактора и требуемым временем пребывания реакционной смеси для завершения процесса образования техуглерода.
Размер зоны реакции (точнее, её длина) не устанавливается жёстко; он должен регулироваться в зависимости от производимой марки технического углерода.
Это достигается изменением вдоль зоны реакции места ввода воды на охлаждение (закалка продуктов реакции). Вода вводится для уменьшения воздействия химически активных газовых компонентов (O2, CO2 и пары H2O) на поверхности образовавшихся частиц сразу по окончании процессов разложения сырья и формирования технического углерода с требуемыми физико-химическими свойствами. Таким образом, зона реакции заканчивается в точке первого ввода закалочной воды.
4. Зона закалки. Зона закалки (охлаждения) представляет собой конечную часть реактора, в которой осуществляется впрыск воды и её испарение.
Время, необходимое для разложения основной части сырья, образования дисперсной фазы, а также роста и коагуляции частиц до нужных для данной марки продукта размеров, быстро сокращается с увеличением температуры реакции. Значения требуемого времени контакта порядка 0,001 с характерны для получения активных марок технического углерода.
При таких малых значениях времени контакта высокомолекулярные соединения, входящие в состав сырья и (или) продуктов его пиролиза, не успевают разложиться полностью. Во избежание замасливания углеродной поверхности этими соединениями температура по окончании формирования дисперсной фазы может снижаться ступенчато: в начале до значений порядка 1100–1250° С для притормаживания процессов газификации и обеспечения разложения остаточных высокомолекулярных компонентов сырья, а затем до величин 700–950° С в зависимости от конструкции установленных далее рекуперативных подогревателей. Оба потока воды регулируются независимо друг от друга, и каждый может вводится в реактор несколькими форсунками. Таким образом, в общей зоне закалки предусматривается выделение так называемой зоны предзакалки.
Вода в реактор вводится форсунками и, как правило, это форсунки механического распыла весьма несложной конструкции.
Пневматический затвор. Пневматический затвор (отсекатель) используют для обеспечения возможности замены сырьевых и водяных форсунок без снятия режима работы реактора. Он монтируется перед несъёмной колодкой форсунки со стороны корпуса реактора. На рисунке 1.7 показана конструкция пневматического затвора. Он состоит из корпуса 1 и втулки 2, образующих кольцевой зазор, из которого в реактор с большой скоростью истекает воздух высокого давления (ВВД), подводимый патрубком 3.
Рисунок 1.7 – Пневматический затвор:
1 – корпус; 2 – втулка; 3 – патрубок подвода воздуха высокого давления
Направленная кольцевая струя ВВД в канале форсунки препятствует выбросу горячих газов из реактора. Перед заменой форсунки аппаратчик открывает вентиль на ВВД и подаёт его в пневмозатвор. После извлечения форсунки из реактора и замены её другой подача ВВД в пневмозатвор прекращается.
Футеровка реакторов и огнеупорные материалы
Основным элементом реактора получения техуглерода является огнеупорная футеровка, обеспечивающая условия для проведения высокотемпературных реакций разложения углеводородов. Как правило, футеровка собирается из нескольких слоёв. Для самого внутреннего слоя используется наиболее термопрочный плотный огнеупор с открытой пористостью 15–20%. По направлении к стальному кожуху располагается несколько слоёв, имеющих увеличивающуюся пористость – до 30% и выше. Роль пористых огнеупоров (легковесных) заключается в снижении величины тепловых потерь от корпуса реактора. Обычно невозможно полностью изолировать корпус, более того, к этому и не стремятся, т.к. определённый поток тепла необходим, чтобы поддерживать желаемый температурный профиль в огнеупорной футеровке. Если футеровка разработана правильно, то потеря тепла от корпуса реактора составляет 1–2% вводимой энергии, а температура корпуса в пределах от 130 до 200 °С считается вполне приемлемой.
Используемые в настоящее время конструкции футеровок можно условно разделить на три вида (рисунок 5.30 а, б, в):
а. сборная конструкция из обжиговых стандартных огнеупоров;
б. сборная конструкция из фасонных блочных изделий (обжиговых и безобжиговых) и стандартных огнеупоров;
в. монолитная конструкция из набивных масс и фасонных изделий.
Футеровка реакторов, которую можно отнести к двум первым видам, характерна для отечественных заводов, причём наиболее широко используется комбинированный второй вид.
Монолитная конструкция футеровки применяется на реакторах, состоящих из сборных модулей, и получила распространение на зарубежных заводах технического углерода. Модули изготавливаются автономно и в последующем собираются на соединительных фланцах непосредственно на месте установки реактора. Основным преимуществом данного вида футеровки является возможность замены любого отдельного модуля, состояние которого исключает его дальнейшее использование. При этом монолитный изолирующий слой, изготавливаемый из легковесных огнеупорных бетонов, может сохраняться неоднократно при замене внутренних огнеупорных блоков, что снижает затраты на эксплуатацию реакторов.
Безобжиговые фасонные огнеупоры применяются на ряде отечественных заводов, которые сами их изготавливают по несложной технологии из корундовых набивных масс методом пневматической трамбовки. Обжиг этих огнеупоров производится в процессе сушки реактора и вывода его на рабочий режим эксплуатации.
В течение всего межремонтного периода эксплуатации реактора футеровка должна сохранять газоплотность. С этой целью собранная футеровка выполняется со связующими швами, которые заполняются огнеупорным раствором (мертелем), обладающим временно-подвижной связью. Это позволяет снизить уровень развиваемых термических напряжений, возникающих в огнеупорах в процессе их разогрева.
Обязательное условие компенсационного действия связующего шва в том, чтобы модуль упругости керамического материала шва был меньше модуля упругости соединяемого изделия. Это достигается специальным подбором химико-минералогического состава мертеля, а также фракционным составом использующихся компонентов. Соединительный шов оказывается более жёстким, если зёрна огнеупорного материала, находящегося в мертеле, боле крупные. Для повышения газоплотности футеровки при сборке внутреннего слоя регламентируют толщину связующего шва не более 1 мм.
Монолитная футеровка, изготавливаемая с применением набивных масс, выполняется без связующих и температурных швов. Принято считать, что в огнеупорных бетонах термическое расширение и имеющая место линейная усадка при рабочей температуре имеют примерно равные температурные деформации, что позволяет избежать высокого уровня термических напряжений.
1.4. ТИПИЧНЫЕ ИЗВЕСТНЫЕ И ПРИНЦИПИАЛЬНО НОВЫЕ КОНСТРУКЦИИ РЕАКТОРОВ ПОЛУЧЕНИЯ ТЕХУГЛЕРОДА
Циклонный реактор. Основой создания современных отечественных производств технического углерода в 1962–1965 гг. является циклонный реактор с использованием природного газа в качестве вспомогательного топлива и рекуперативного подогрева воздуха, подаваемого на горение. Своё название реактор получил в соответствии с циклонным характером ввода топливообразующей смеси в зону горения. Топливо и воздух вводятся в реактор двумя тангенциальными потоками при аксиальной подаче сырья. Сырьевой факел в циклонном реакторе (см. рисунок 1.8) увлекается окутывающим его спиральным потоком газов горения.
Рисунок 1.8 – Циклонный реактор:
1 – сырьевая форсунка; 2, 9 – передняя и задняя сферические крышки реактора соответственно; 3 – камера горения; 4 – корпус реактора; 5 – футеровка; 6 – суживающая втулка; 7 – зона реакции; 8 – зона закалки; 10 – каналы для ввода воды на охлаждение; 11 – горелки
Циклонный реактор представляет собой горизонтально расположенный цилиндрический аппарат переменного по длине диаметра с отверстиями для ввода материальных потоков. Стальной корпус 4, снабжённый передней 2 и задней 9 крышками, футерован изнутри огнеупорным материалом 5 (кирпичом или фасонными блоками). Футеровка выполнена в несколько слоёв – внутренние слои из материала с высокой теплостойкостью и огнеупорностью. Наружные слои выполняют роль теплоизоляции. Внутренняя конфигурация реактора образует различной длины и диаметра соосно расположенные зоны – горения 3, реакции 7 (с суживающейся втулкой 6) и закалки 8.
В камеру горения 3 подаётся топливо двумя тангенциально установленными горелками 11. Одновременно в каналы расположения горелок подаётся предварительно нагретый воздух на горение. При сжигании топлива в камере горения создаются вращающиеся потоки пламени, в которые через форсунку 1 впрыскивается нагретое сырьё. Потоки горячего газа и паров сырья поступают в зону реакции 7, где происходит разложение сырья и образование технического углерода. Для интенсификации процессов смешения горячих газов с парами сырья и процесса образования техуглерода в целом, в начале зоны реакции, при производстве активных марок техуглерода, устанавливается смесительная втулка 6. При аксиальной подаче сырья его распыл, как правило, осуществляется воздухом высокого давления (пневматическими форсунками). Для прекращения процесса в зону охлаждения 8 (зону закалки) впрыскивается вода механическими форсунками, установленными в каналах 10.
В циклонных реакторах можно получать активные и полуактивные марки технического углерода.
Рассмотренная выше конструкция реактора в процессе эксплуатации модернизировалась. Наибольшие изменения связаны с организацией радиального ввода сырья механическими форсунками, по принципу уже находившихся в эксплуатации цилиндрических реакторов, при сохранении циклонной камеры горения, что позволило повысить производительность реактора и выход готового продукта. Циклонные реакторы в незначительных количествах ещё сохранились на некоторых заводах.
Цилиндрические реакторы.
Концепция интенсификации процессов получения технического углерода и увеличения единичной мощности оборудования в 1970-е годы уже основывалась на использовании цилиндрических реакторов. В цилиндрическом реакторе ввод сырья в высокоскоростной и высокотемпературный аксиальный поток газов осуществляется радиально. В реакторах для производства полуактивных марок техуглерода возможен комбинированный ввод сырья – радиальный и аксиальный одновременно.
На рисунке 1.9 представлена конструкция цилиндрического большегрузного реактора РС 50/3500 для производства полуактивных марок технического углерода.
Рисунок 1.9 – Цилиндрический реактор для производства полуактивных марок технического углерода:
1 – корпус реактора; 2 – горелка; 3 – прорези в направляющих трубах горелок; 4 – центральная сырьевая форсунка; 5 – воздушная камера; 6 – патрубок подвода воздуха; 7 – камера горения; 8 – футеровка; 9 – реакционная камера; 10 – водяные форсунки; 11 – камера охлаждения (зона закалки); 12 – футерованный переход; 13 – радиальные сырьевые форсунки
Реактор представляет собой горизонтально расположенный аппарат, цилиндрический корпус 1 которого футерован огнеупорным материалом 8. Условно реактор делится на три камеры (зоны) – горения 7, реакции 9 и закалки 11. Топливо в камеру горения 7 вводится горелками 2, установленными на передней крышке параллельно его центральной оси. Воздух на горение через патрубок 6 подаётся в воздушную камеру 5, откуда через прорези 3 в направляющих трубах поступает к горелкам 2. Предварительно подогретый воздух, смешиваясь с топливом, обеспечивает его интенсивное горение. Сырьё в реактор подаётся посредством центральной 4 и двух радиальных форсунок 13. Камера реакции 9 является продолжением камеры горения 7, но имеет меньший диаметр и большую длину. Время пребывания в ней должно быть достаточным для полного разложения углеводородного сырья.
Для быстрого охлаждения техуглеродгазовой смеси через форсунки 10 вводится вода, которая испаряется в зоне закалки 11, охлаждая поток до заданной температуры.
В хвостовой части реактора направление потока изменяется на 90° и через футерованный стакан 12 аэрозоль техуглерода поступает далее в рекуперативные воздухоподогреватели. В данных реакторах применяют пневматические или пневмомеханические сырьевые форсунки.
В процессе эксплуатации были выявлены основные недостатки конструкции – склонность к коксованию при комбинированном вводе сырья и низкий показатель «светопропускание толуольного экстракта».
Дальнейшее усовершенствование конструкции было связано с определением оптимального положения сырьевых форсунок, увеличения времени пребывания продуктов до их охлаждения, и было направлено на устранение вышеназванных недостатков.
Принципиальная конструкция большегрузного цилиндрического реактора РС 105/3500 для производства активных марок технического углерода представлена на рисунке 1.10.
Рисунок 1.10 – Принципиальная конструкция реактора РС 105/3500:
1 – камера горения; 2 – диафрагма; 3 – воздухоохлаждаемое сопло; 4 – зона реакции; 5 – зона закалки; 6 – зона предзакалки
Высокотемпературный поток газов из камеры горения 1 разгоняется до высоких скоростей в смесительном сопле зоны реакции 4. Сырьё вводится четырьмя механическими форсунками из жаропрочной стали в сопло 3, футерованное изнутри огнеупором, и совместно с диафрагмой 2 охлаждается воздухом. Здесь выделяется зона предзакалки 6, образующая объём между первым поясом ввода охлаждающей воды и последующими поясами её ввода, расположенными в зоне закалки 5, которая переходит и в вертикальную часть реактора.
В настоящее время представленные выше реакторы определённым образом модернизируются (осуществляется перевод на одногорелочное устройство, что сопровождается изменением конструкции передней крышки реактора и футеровки входа зоны горения; уточняются диаметры и объёмы зон реактора и т.д.), но остаются базовыми для большинства отечественных производств.
Конструкции реакторов зарубежных фирм. Обзор зарубежных патентов показывает, что различные фирмы производители технического углерода применяют реакторы, имеющие большое сходство по конфигурации.
В качестве примеров на рисунке 1.11 представлена конструкции реактора по патенту фирмы «Дегусса», а на рисунке 1.12 – конструкция реактора по патенту фирмы «Филипс Петролеум Компании».
![]() | ![]() |
Рисунок 1.11 – Реактор для получения технического углерода фирмы «Phillips Petroleum Company» (США) | Рисунок 1.12 – Реактор для получения технического углерода фирмы «Degussa» (германия) |
Как видно из рисунков, оба реактора очень близки по конструкции. Они оснащены одногорелочным устройством, имеют аналогичные по конструкции камеры горения и зоны реакции, разборные корпуса и практически одинаковую конструкцию футеровки. Различия заключаются, как правило, в расположении мест ввода сырья и количеством этих вводов, а также мест ввода воды на охлаждение.
Дата добавления: 2018-02-28; просмотров: 963; Мы поможем в написании вашей работы! |
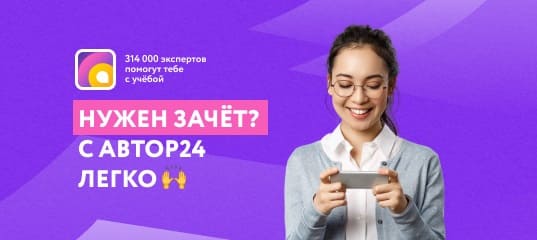
Мы поможем в написании ваших работ!