Расчет технологических режимов напыления
Министерство образования и науки РФ
Казанский национальный исследовательский технический университет им. А.Н.Туполева
==========================================================
Институт Радиоэлектроники и Телекоммуникаций
Кафедра ТРЭС
Курсовой проект
по дисциплине
"Технология микросхем"
Тема проекта:
Технологический процесс изготовления платы интегральной микросхемы – зарядного устройства.
Выполнила:
студентка группы 5406
Корчагина М. О.
Руководитель:
Гайнуллина Н. Р.
Казань 2012
Аннотация
Выполнена технологическая разработка платы зарядного устройства в гибридном тонкопленочном варианте. Произведен контроль конструкторской документации, расчет технологических параметров, исследована точность тонкопленочных резисторов, определение параметров технологического режима. Разработан технологический процесс изготовления платы.
Содержание
Задание на курсовой проект…………………………………………………..
Аннотация……………………………………………………………………...
Содержание…………………………………………………………………….
Введение……………………………………………………………………….
Анализ задания, технологический контроль документации……………….
Выбор технологического процесса ………………………………………….
Схема технологического процесса ………………………………………….
Выбор установки для напыления ……………………………………………
|
|
Характеристики материалов………………………………………………….
Технологические расчеты…………………………………………………….
Характеристика детали технологического приспособления……………….
Список литературы……………………………………………………………
Приложение:
Разработанный процесс на технологических картах Топологический чертёж
Введение
Микроэлектроника как современное направление проектирования и производства электронной аппаратуры различного назначения является катализатором научно-технического прогресса. Автоматизация производства, создание гибких перестраиваемых роботизированных микросхем, систем, развитие автономных систем немыслимо без применения интегральных микросхем, микропроцессоров и микросборок. Технология изготовления изделий микроэлектроники обеспечивает в первую очередь высокий уровень производительности труда, комплексную микроминиатюризацию электронной аппаратуры связи, автоматики, вычислительной техники и вбирает в себя передовой опыт и достижения многих отраслей и науки и техники: от физики взаимодействия атомных и ядерных частиц веществом до микрометаллургии и прецизионной химической технологии.
|
|
Наиболее перспективной в конструктивном и технологическом отношениях является радиоэлектронная аппаратура, основой которой служат функциональные микроэлектронные узлы – интегральные микросхемы.
Интегральной микросхемой (ИМС) называется микроэлектронное изделие, имеющее высокую плотность упаковки элементов соединений между ними, при этом все элементы выполнены нераздельно и электрически соединены между собой таким образом, чтобы с точки зрения испытаний, поставки и эксплуатации изделие рассматривалось как единое целое. Интегральная микросхема имеет малую массу, габариты и потребляемую мощность РЭА.
Гибридная пленочная интегральная микросхема – ИМС, которая наряду с пленочными элементами, полученными с помощью интегральной технологии, содержит компоненты, имеющие самостоятельное конструктивное оформление. В зависимости от метода нанесения пленочных элементов на подложку различают тонкопленочные (напыление в вакууме) и толстопленочные (трафаретная печать) гибридные ИМС. Гибридные ИМС имеют худшие технические показатели (размеры, массу, быстродействие, надежность), чем полупроводниковые ИМС. В то же время они позволяют реализовать широкий класс функциональных электронных схем, являясь при этом экономически целесообразными в условиях серийного и даже мелкосерийного производства. Это объясняет менее жесткими требованиями к фотошаблонам и трафаретам, с помощью которых формируют пленочные элементы, а также применением менее дорогостоящего оборудования. В составе пленочных ИМС возможно получить резисторы с точностью 5%, а с применением подгонки – до десятых долей процента. Гибридно-пленочная технология позволяет реализовать практически любые функциональные схемы.
|
|
Анализ задания
(технологический контроль документации)
В результате анализа топологического чертежа платы ошибки в построении контактной платы были выявлены (несоответствие размеров). Выбранное сопротивление квадрата пленки не соответствует номиналам резисторов. С точки зрения необходимого сопротивления квадрата пленок материалы пленок подобраны не верно.
Произведем проверку резисторов в соответствии с выбранными резистивными слоями.
Сопротивление резисторов
R1=3000 Ом/□*28мм/4мм=21000 Ом
R4=3000 Ом/□*17 мм/6 мм=8500 Ом
R7=3000 Ом/□*10мм/7 мм=4286 Ом
Т.к. сопротивления R1,R4,R7 расчётные данных (сплав РС3710) намного больше сопротивлений R1,R4,R7, нужно взять ρкв много меньше чем 3000Ом/□. Для этого найдём подходящее ρкв.
|
|
R1= ρкв *28мм/4мм=6800Ом
ρкв = 971Ом/□
R4= ρкв*17 мм/6 мм=2700Ом
ρкв =954Ом/□
R7= ρкв*10мм/7 мм=1000Ом
ρкв=629 Ом
Возьмём среднее ρкв=850Ом. Данное сопротивление характерно для другого сплава – РС3001. Так как изначально материал для пленок был выбран неверно, изменяем его на сплав РС3001. И возьмем соответствующее сопротивление квадрата пленки для расчетов ρкв=500Ом.
Выбор технологического процесса изготовления платы зарядного устройства
Любая технология изготовления платы с пленочными элементами включает в себя два основных этапа: нанесение пленки из проводящего, резистивного или диэлектрического материала на подложку и формирование из этих пленок планарной (то есть в плоскости подложки) конфигурации элементов. Процессы нанесения пленки и формирования рисунка можно осуществлять либо последовательно друг за другом, либо одновременно. Выбор того или иного варианта зависит от природы процесса, величины параметров элементов, ограничений на функциональные параметры по точности, надежности, стабильности и т.д.
Напыление тонких пленок может быть выполнено на основе термического вакуумного испарения или ионно-плазменного распыления материалов. Для осуществления процесса обоснованно выбирается подходящее оборудование.
Для формирования конфигурации проводящего, резистивного и диэлектрического слоя используют различные методы:
- масочный: соответствующий материал напыляют на подложку через съемную или контактную маску;
- фотолитографический: пленка наносится на всю поверхность подложки, а затем избирательно стравливается с отдельными (лишними) участками;
- комбинированный: когда совмещаются масочный и фотолитографический метод.
На основе этих методов для изготовления плат гибридных тонкопленочных интегральных схем (ГИС) и функциональных узлов (ФУ) можно выделить несколько характерных технологических процессов (ТП).
ТП1 – все слои наносятся через съемные маски;
ТП2 – последовательно напыляются материалы резистивных пленок, затем проводящие пленки за один вакуумный цикл на всю поверхность подложки;
ТП3 – последовательность напыления слоев как в ТП2;
ТП4 – резистивный слой и конденсаторы напыляются через маску, а рисунок проводящего слоя – фотолитографией;
ТП5 – через маску напыляются проводники и контактные площадки, рисунок резисторов формируют фотолитографией;
ТП6 – рисунок резистивного слоя формируется фотолитографией, а проводники и контактные площадки напыляются через маску.
Резистивный слой напыляется на всю поверхность, затем проводники напыляются через маску, после чего фотолитография резистивного слоя, и фотолитография защитного слоя. Для формирования можно использовать характерный процесс ТП5.
Схема технологического процесса изготовления платы ГИС
Последовательность операций:
Выбор установки напыления
При катодном распылении на установке ИПУ-6 используют простейшую двухэлектродную схему (см. рис), называемую также диодной схемой распыления, которая состоит из катода (распыляемой мишени) и анода. Подложки размещают на аноде. Тлеющий разряд создается в разреженном аргоне при давлении 1—10 Па. В процессе распыления непрерывно работает система откачки, а аргон с определенным расходом поступает в камеру через натекатель, что и обеспечивает заданное давление газа. Катод-мишень наводится под отрицательным потенциалом относительно заземленного анода.
При распылении сплавов скорость процесса для разных компонентов в общем случае различна. Обеспечить заданный состав пленок при ионном распылении в большинстве случаев проще, чем при термическом вакуумном напылении. Один из приемов заключается в использовании составных (мозаичных) мишеней, причем соотношение площадей компонентов мишени рассчитывают, исходя из заданного состава пленки и коэффициентов распыления.
Условия конденсации распыленных атомов. При ионном распылении (в отличие от термического вакуумного напыления) поток атомов вещества на подложку имеет следующие особенности:
1) энергия и направление удара атомов о поверхность подложки носят случайный характер по поверхности и во времени;
2) плотность потока атомов на подложку приблизительно на порядок ниже, что обусловливает более низкие скорости роста пленок (~0,5 нм/с);
3) средняя энергия атомов, подлетающих к подложке, на 1—2 порядка более высокая;
4) наряду с нейтральными атомами в потоке присутствуют ионы распыляемого вещества и электроны;
5) относительное содержание молекул остаточного газа в потоке и на подложке более высокое.
При катодном распылении легче, чем при термическом вакуумном испарении, достигнуть равномерного распределения конденсата по толщине, так как плоский источник атомов — катод может по размерам быть больше расстояния до подложки (30—80 мм). Так, при диаметре катода 300—350 мм достигается равномерность конденсата по толщине ±2% на площади анода диаметром 150 мм. При планетарном движении подложек на вращающемся аноде равномерность в распределении конденсата улучшается до ±1%.
Упрощённая схема установки ИПУ-6
1—анод; 2—подложка; 3 — изолятор;4—экран; 5 — катод-мишень
Схема технологического процесса изготовления платы ГИС
Последовательность операций:
1 Подготовка(очистка) подложек
2 Подготовка установки к напылению
3 Напыление резистивной плёнки на всю поверхность
3.1 Создание предварительного вакуума
3.2 Создание рабочего вакуума
3.3 Запуск рабочего газа
3.4 Подача напряжения анод - катод
3.5 Напыление
3.6 Отжиг плёнок (выдержка 2 – 2,5 часа)
3.7 Запуск воздуха
3.8 Контроль качества и электрофизических характеристик плёнки
4 Подготовка установки к напылению
5 Напыление через маску проводников (формирование длины резисторов)
5.1 Создание рабочего вакуума
5.2 Запуск рабочего газа
5.3 Подача напряжения анод – катод
5.4 Напыление
5.5 Отжиг плёнок (выдержка 2 – 2,5 часа)
5.6 Запуск воздуха
5.7 Контроль качества и электрофизических характеристик плёнки
6 Фотолитография резистивной плёнки(формирование ширины резисторов)
6.1 Нанесение фоторезиста
6.2 Экспонирование и проявление фоторезиста
6.3 Травление проводникового слоя
6.4 Удаление фоторезиста
7 Фотолитография защитного слоя
7.1 Нанесение фоторезиста
7.2 Совмещение и экспонирование
7.3 Проявление фоторезиста.
8. Контроль качества и электрофизических характеристик плёнки
Характеристика материалов пленочных элементов
Материал подложки.
Наименование материала | Коэффициент теплопроводности, Вт/м ∙ град | Диэлектрическая проницаемость ε | Температурный коэффициент линейного расширения, град-110-6 |
Ситалл Ст50-1 | 2-32 | 8,5 | 5±0,2 |
Материал для тонкопленочных резисторов.
Наименование материала | Удельное поверхностное сопротивление, Ом/□ | Диапазон получаемых сопротивлений, Ом | Температурный коэффициент сопротивления, 10-4град-1 | Допустимая удельная мощность рассеяния Вт/мм2 |
РС3001 | 500-3000 | 100-500000 | -1,6 | 0,02 |
Материал для проводников.
Материал | Температура плавления, 0С | Атомная масса | Плотность 106 г/м | Условная температура испарения 0С | Коэффици ент теплопро водности, Вт/м К | Температурный коэффици ент сопротивле ния, 10-4К-1 | Удель ное электрическое сопротивление 10-6Ом м | |
Медь | 63,5 | 8,94 | 0,0172 | |||||
Никель | 58,7 | 8,9 | 0,073 | |||||
Технологические расчеты
Расчет технологических режимов напыления
Исходные данные: R=500 Ом, ТКС=-1,6 (104 * град-1)
Уравнение регрессии:
R=594,21 – 26,46 Т*и +61,29 Т*П – 110,04d* – 217,96 Т*и Т*П + 13,21Т*и d*-
-24,86 Т*П d*
ТКС = (-2,06 + 0,405 Т*и – 0,544 Т*П –1,303d*) 104 * град-1
За базовый уровень варьируемых факторов приняты следующие значения:
Тио= 1500°С Тпо=200°С d0=300Å
Интервалы варьирования:
Δ Ти =100°С ΔТп=150°С Δd=100 Å
Кодированные значения соответствующих параметров технологического процесса Ти,Тп и d связаны между собой следующими соотношениями:
Т*и=(Ти – Тио)/ ΔТи Т*П = (Тп – Тпо)/ ΔТп d= (d-do)/ Δd
В результате подстановки (d=0,34) получим следующую систему уравнений:
500=594,21-26,46 Т*и +61,29 Т*П -74,1064+4,4914 Т*и -8,4524 Т*П
-1,6=-2,06+0,405 Т*и -0,544 Т*П -0,44302
Упростим:
-20,1076=-21,9686 Т*и+ 52,8376 Т*П
0,90302=0,405 Т*и -0,544 Т*П
При расчете технологических режимов по системе уравнений регрессии значение одного из варьируемых факторов приходится выбирать в интервале варьирования произвольно (избыток неизвестных). В таком качестве, лучше выбирать фактор с наименьшим коэффициентом влияния на выходной параметр. В уравнении необходимо подставлять его кодированное значение в пределах ±1.
Выберем значение d=0,34, тогда из системы уравнений получим значения параметров Т*и = -0,93 Т*П=0,21
Подставим полученные кодированные значения в уравнения и получим:
Ти=1407°СТп=231,5°Сd=334 Å
Теперь можно рассчитать «коэффициент свидетеля», чтобы рассчитать Roc, которая задается оператору вакуумной установки, а так же рассчитать τ, необходимое для стабилизации сопротивления, т.е. длительности термообработки.
Kсв= 1,144+0,04 Т*и +0,143Т*П –0,072d*-0,045 Т*и Т*П=1,024
Τ= 4769 - 285Т*и - 1837d*- 237Т*иd* - 212 Т*П d*=4469,27c
Зная коэффициент свидетеля можно рассчитать сопротивление осажденной пленки до термообработки: RОм
Roc= R - kсв R=-12 Ом
Задано | Технологические режимы | ||||||
Материал | RОм | ТКС | Ти°С | Тп°С | d Å | RосОм | τ,с |
РС3001 | -1,6 | 231,5 | -12 | 4469,27 |
Дата добавления: 2015-12-21; просмотров: 180; Мы поможем в написании вашей работы! |
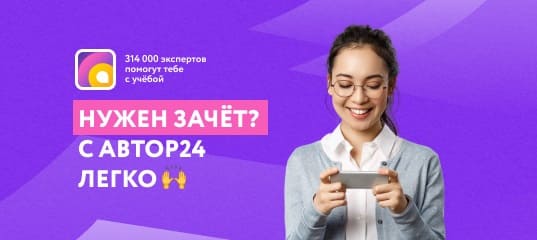
Мы поможем в написании ваших работ!