Детонационное напыление покрытий
В последние годы для нагрева и ускорения распыляемых частиц все шире применяют импульсные источники энергии, в частности энергию взрыва (рисунок 1.5). Импульсные методы обработки материалов характеризуются большими энергетическими возможностями, простотой и экономичностью. Технологические устройства импульсного действия имеют высокие удельные мощности, отличаются значительным упрощением преобразования энергии в полезную работу. Наиболее широко применяется напыление покрытий с помощью энергии взрыва газовых смесей – детонационное [13]. Более полную физическую сущность этого метода отражает термин «детонационно-газовое напыление». Детонационно-газовые покрытия успешно используются для упрочнения нагруженных поверхностей деталей, изготовленных из разнообразных материалов. Они отличаются высокими физико-механическими и эксплуатационными свойствами (прочностью, плотностью, износостойкостью и пр.) [3].
![]() |
Рисунок 1.5 - Принципиальная схема устройства для детонационно-газового напыления покрытий: 1 - подвод газа для ввода порошка; 2 - бункер с порошком напыляемого материала и дозирующим устройством: 3 - свеча зажигания: 4 - ствол; 5 - обрабатываемое изделие; 6 - напыленное покрытие; 7 - подвод горючей смеси; 8 - подвод флегматизирующего газа (азота) |
Детонационные покрытия получают с помощью устройств, принципиальная схема которых приведена на рисунке 1.6. Они состоят из открытого с одного конца ствола 5, блоков подачи напыляемого порошка 4 и газов 1, блока инициирования взрыва 3 с воспламенителем 2. С помощью блока 1 ствол заполняется смесью газов, способных детонировать; из блока 4 в ствол подается заданная навеска напыляемого порошка; блок 3 вырабатывает инициирующий импульс, который подается на воспламенитель 2. Вблизи воспламенителя температура поднимается выше критической (Ткр ≈620 К), например, проскакивает искра. Воспламенитель поджигает смесь газов, обычно у закрытого конца ствола. По смеси газов распространяется пламя с увеличивающейся скоростью. Пройдя определенное расстояние, горение переходит в детонацию, т.е. с этого момента по трубе распространяется детонационная волна со скоростью, строго постоянной для данных геометрии ствола и состава газа. Детонационная волна представляет комплекс ударной волны и зоны химической реакции [11].
|
|
![]() |
Рисунок 1.6 – Принципиальная схема детонационных устройств |
В ударной волне газ сжимается до давления несколько десятков атмосфер. При этом температура повышается до нескольких тысяч градусов Цельсия и становится значительно больше критической температуры, при которой газовая смесь вступает в реакцию.
|
|
За зоной химической реакции находятся продукты детонации, имеющие высокие давление и температуру. Они следуют за детонационной волной со скоростью, меньшей скорости детонационной волны D на скорость звука С.
После достижения детонационной волной открытого конца ствола детонационная волна разрушается, так как может перемещаться только по смеси газов, способной детонировать. Затухающая ударная волна может перемещаться вне ствола, но на расстоянии более 100 мм ее амплитуда близка к нулю.
Продукты детонации начинают истекать из ствола в виде сверхзвуковой нерасчетной струи: температура и давление продуктов детонации в стволе уменьшаются; истечение происходит до тех пор, пока давление продуктов на выходе из ствола не сравняется с атмосферным, после чего окружающий воздух засасывается в ствол сначала вблизи стенок, а затем по всему сечению и заполняет большую его часть.
При истечении продукты детонации увлекают напыляемые частицы. Формируется двухфазный поток, состоящий из продуктов детонации и напыляемых частиц. Двухфазный поток неоднороден как по длине, так и по сечению ствола. Неоднородность двухфазного потока обусловлена как нестационарностью процесса истечения, так и различием физико-химических и геометрических характеристик напыляемых частиц. Продукты детонации нагревают и ускоряют напыляемые частицы. При этом могут иметь место процессы их плавления и испарения.
|
|
После выхода двухфазного потока из ствола продукты детонации резко расширяются. Их температура, скорость и плотность уменьшаются при удалении от ствола, но не монотонно. Вблизи поверхности обрабатываемой детали (подложки) поток газа тормозится и затем растекается вдоль преграды. У подложки создается пограничный слой, в котором частицы тормозятся, их скорость может резко падать. Часть частиц может увлекаться продуктами детонации, обтекающими подложку, и уносится.
Процесс формирования детонационных покрытии во многом подобен процессу формирования плазменных покрытий [7], который в основном заключается в растекании и кристаллизации жидких частиц по поверхности подложки или предыдущих слоев покрытия.
При напылении материалов однородного химического состава, например металлов или окислов, покрытие может формироваться из практически полностью расплавленных частиц и из смеси расплавленного и нерасплавленного материалов. При напылении некоторых композиционных материалов, например твердого сплава ВК, напыление осуществляется из смеси расплавленного кобальта и твердых частиц карбида вольфрама.
|
|
Преимущества детонационных покрытий по сравнению с плазменными и газопламенными объясняются существенным отличием механизма формирования. По-видимому, здесь определяющую роль имеет наличие в конце двухфазного потока наиболее крупных непроплавленных частиц, которые взаимодействуют с покрытием сформированным из частиц, входящих в начало и середину двухфазного потока. В результате образуются эффекты абразивного отделения части или всего покрытия и эффект ударного прессования, т. е. увеличивается плотность уже сформированного покрытия. Указанные эффекты, в частности эффект ударного горячего прессования, могут проявляться и при взаимодействии двухфазного потока с покрытием, сформированным в результате предыдущего выстрела.
Еще одним существенным отличием детонационно-газового напыления является значительно большая концентрация частиц в момент формирования покрытия по сравнению с плазменным, что, в частности, усиливает проявление эффектов ударного прессования и абразивного отделения. Более высокие скорости частиц, чем при плазменном напылении, делают возможным при ударе выделение значительной энергии; из-за этого происходит увеличение температуры частиц и температуры в зоне контакта. Благодаря высокой скорости и сравнительно малой температуре становится возможным напыление мелкодисперсного порошка (~1 мкм).
Механизм формирования покрытий при напылении изучен крайне недостаточно. В случае детонационного напыления имеются весьма большие расхождения взглядов по этому вопросу. Рассмотрим механизм формирования покрытий при детонационном напылении, используя имеющиеся экспериментальные данные.
Покрытие может формироваться из частиц: 1) жидких; 2) имеющих жидкую оболочку и твердый керн; 3) из смеси жидких и твердых частиц; 4) из смеси жидких, твердых и расплавленных с поверхности частиц, т.е. имеющих твердый керн.
Если напыляемый материал не расплавлен, но имеет температуру, значительно превосходящую температуру плавления подложки, то контактная температура может быть выше температуры плавления подложки. При этом отдельные частицы закрепляются на подложке, однако формирование следующих слоев покрытия при указанных условиях невозможно.
Детонационное напыление является импульсным процессом. В результате единичного цикла, как правило, формируется покрытие толщиной ~5 мкм, т. е. покрытие толщиной более 40 мкм практически всегда является многослойным.
Рассмотрим формирование первого слоя детонационного покрытия. Как показали металлографические исследования, указанный слой характеризуется прежде всего плотным прилеганием к поверхности. На границе с подложкой очень редко можно обнаружить дефекты в виде пор. По размытости изображения границ переходной зоны можно косвенно судить об оплавлении поверхности. Было зафиксировано частичное подплавление подложек из нержавеющей стали и алюминиевого сплава при напылении окиси алюминия и твердого сплава типа ВК. Оплавление сопровождается перемешиванием материала подложки с покрытием, что благоприятствует образованию прочной связи. В зоне излома образца с покрытием отслоения покрытия в оплавленных зонах не наблюдается.
Адгезию между первым слоем покрытия и подложкой могут обеспечивать химическое взаимодействие, механическое зацепление и Ван-дер-Ваальсовы силы. При напылении на отпескоструенную подложку благодаря высокой скорости частиц напыляемый материал затекает в неровности подложки.
Высокая адгезия детонационных покрытий показывает, что происходит и химическое взаимодействие частиц и подложки. Она обеспечивается пескоструйной обработкой напыляемых деталей непосредственно перед напылением, что приводит к увеличению в несколько раз контактной площади и активации поверхности.
За счет высокой концентрации частиц контактная температура между частицами при формировании единичного слоя близка к температуре плавления, поэтому границы между отдельными частицами стираются. Единичный слой при микроскопических исследованиях выглядит монолитным, в то время как границы между слоями фиксируются достаточно четко.
Напыление последующих слоев покрытия (II, III на рисунке 1.7) существенно отличается от формирования слоя I. Как отмечается в работе [4], контактная температура при этом будет значительно выше. Так, при напылении окиси алюминия даже без учета перегрева частиц выше температуры плавления А12О3, перехода кинетической энергии в тепло и наличия микровыступов . Можно предположить, что указанные выше причины приведут к тому, что контактная температура на границах слоев покрытия 2, 3 и т. д. (рисунок 1.7) будет лежать в интервале от 1870 К до 2320 К, т. е. достигать в некоторых точках температуры плавления.
![]() |
Рисунок 1.7 – Схема строения покрытия |
Слой I, имеющий толщину 5-10 мкм, при формировании слоя II нагревается до температуры, достигающей 1770 К, причем и на границе 1 с подложкой температура может достигать 1270 К [4], т.е. там возможны дополнительные процессы, увеличивающие прочность сцепления. Слой II формируется из высокоскоростных частиц, которые развивают высокие давления, в результате чего слой I может деформироваться. При этом улучшается контакт на границе покрытие - подложка.
Слой покрытия, ближайший к внешней поверхности, наиболее слабо связан с предыдущими из-за отсутствия дополнительного упрочнения при напылении следующих слоев. Во многих случаях при исследовании излома наблюдалось отслоение верхнего слоя. Исследование износостойкости покрытий при высоких контактных давлениях показало, что верхние слои (10-30 мкм) сравнительно быстро истирались, после чего износ уже был минимальным.
Определяющую роль при детонационном напылении, как правило, играют процессы взаимного влияния частиц друг на друга, а также эффекты абразивного отделения и ударного горячего прессования. Таким образом, отличия характеристик детонационных покрытий от плазменных и газоплазменных объясняется большей величиной скорости частиц при детонационном напылении.
Дата добавления: 2015-12-21; просмотров: 58; Мы поможем в написании вашей работы! |
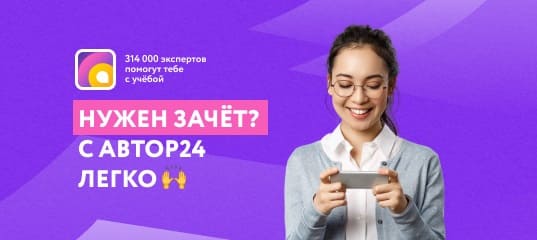
Мы поможем в написании ваших работ!