Методы нанесения покрытий на поверхности деталей
Успешное решение задач повышения эффективности общественного производства и перевода экономики страны на путь преимущественно интенсивного развития тесно связано с ускорением научно-технического прогресса. Необходимо создать принципиально новые виды техники и технологии, существенно повысить производительность труда во всех отраслях народного хозяйства. В этих условиях особое значение приобретают проблемы надежности и долговечности машин и механизмов, экономного использования материалов, энергии и трудовых ресурсов. Их решение неразрывно связано с обеспечением эффективной защиты поверхности деталей и конструкций от коррозии и изнашивания [5]. Применение покрытий создает условия для повышения конструктивной прочности промышленных сталей и сплавов [6].
Использование износостойких, коррозионностойких, жаростойких, химически стойких, электроизоляционных, теплоизоляционных и других видов покрытий позволяет резко сократить потери металлов, расход ресурсов на их возмещение и дает возможность повысить качество, надежность и долговечность машин, оборудования и сооружений [6].
В настоящее время существуют различные методы нанесения покрытий на детали машин, инструменты и конструкции (рисунок 1.1). Существующие методы получения покрытий, с учетом специфики протекания процессов формирования покрытий, можно разделить на четыре основные группы.
|
|
![]() |
Рисунок 1.1 – Классификация методов нанесения покрытий |
К первой группе относятся химико-термические методы образования покрытий (ХТМ), основанные на твердофазовом, жидкофазовом и газофазовом насыщении поверхности детали. ХТМ позволяют получить покрытия толщиной 10-40 мкм. Наиболее популярным представителем химико-технологических методов является способ электроискрового легирования (ЭИЛ). При ЭИЛ можно получить покрытия толщиной от 24-50 мкм до 200-250 мкм, при этом шероховатость поверхностного слоя составляет 3.6-6.3 мкм. Среди ХТМ наибольшим преимуществом обладает ионное азотирование инструментов из углеродистых и быстрорежущих сталей, которые обеспечивают получение покрытий с минимальными деформациями инструмента. К методам первой группы может быть также отнесен метод термодиффузионного насыщения (метод ДТ), разработанный во Всесоюзном НИИ твердых сплавов. Метод термодиффузионного насыщения, основанный на порошковой металлургии, имеет недостатки, связанные: во-первых, с наличием порошковой смеси на рабочих поверхностях инструмента; во-вторых, с необходимостью герметизации контейнера или использования защитных газов; в-третьих, с одноразовым использованием смеси. ХТМ позволяют лишь ограниченно увеличить поверхностные свойства за счет варьирования технологическими параметрами процесс, поэтому эффективность этого метода относительно невысока.
|
|
Ко второй группе методов нанесения покрытий на рабочие поверхности можно отнести методы химического осаждения покрытия (ХОП). Методы этой группы также представляют собой методы формирования покрытий по комплексному методу, но в данном случае большой вклад вносят интердиффузионные реакции между конденсатом и материалом детали. Методы ХОП (химического осаждения покрытий из пароплазменной фазы), имеющие в мировой практике наименование CVD (Chemical Vapor Deposition) получили широкое распространение. Методами ХОП из газовой фазы можно получать однослойные, двухслойные и даже трехслойные покрытия, состоящие последовательно из карбида титана, карбонитрида титана и нитрида титана. Отличительной особенностью покрытий, полученных методами ХОП, является формирование переходной зоны между покрытием и подложкой - твердым сплавом, обычно именуемой г-фазой. Формирование переходной зоны связано с интердиффузионными реакциями между насыщающим тугоплавким металлом из парогазовой смеси и компонентами твердого сплава. Методы ХОП обычно реализуются при температуре около 1000-1200°С.
|
|
К третьей группе методов нанесения покрытий могут быть отнесены методы физического осаждения покрытий (ФОП), основанные на процессах ионно-плазменной обработки в вакууме, применяемых в технологии производства изделий для переноса массы материалов. В одном случае это локальное или повсеместное (по всей поверхности обрабатываемой детали) удаление материала обрабатываемой подложки с целью ее очистки, в другом случае - распыление материала, используемое для получения пленочных покрытий на подложках.
Плазменные способы можно разделить на два вида по различию в применении плазменных явлений. Плазменно-дуговые и плазменно-струйные методы основаны на использовании тепла плазмы для нагрева, размягчения и возможного расплавления напыляемого порошка. В плазменной струе, состоящей из свободных электронов, ионов и частично нейтральных атомов аргона, азота или другого плазмообразующего газа, создается высокая температура, позволяющая расплавить порошок любого состава. Современные плазмотроны дают возможность регулировать тепловые, энергетические и газодинамические параметры процесса струйно-плазменного нанесения покрытий [7].
|
|
Травление распылением в плазме - повсеместное или локальное удаление распылением в плазме инертных газов поверхностных слоев материала с целью очистки его от загрязнений. Бомбардировка ионами осуществляется при подаче на обрабатываемый материал высокого отрицательного электрического потенциала, ускоряющего ионы. Основное практическое применение травления распылением в плазме - очистка подложек перед нанесением на них пленочных износостойких покрытий.
Ионно-плазменное нанесение - получение пленочных покрытий распылением в плазме инертных газов материала мишени при подаче на нее отрицательного электрического потенциала. Разновидности ионно-плазменного нанесения отличаются техническими средствами, обеспечивающими создание плазмы и бомбардировку распыляемой мишени. К ним можно отнести катодное распыление, высокочастотное распыление, магнетронное распыление. Давление газа в процессах ионно-плазменного нанесения покрытий составляет 5x10-2-101 Па. Высокая энергия распыленных частиц при ионно-плазменном нанесении обеспечивает получение плотной пленки материала, имеющей прочное сцепление с подложкой. Возможно получение пленок многокомпонентных материалов без изменения их стехиометрического состава. Ионно-плазменное нанесение используется в технологии для получения пленок практически любых материалов.
Ионно-лучевое нанесение - получение пленочных покрытий распылением материала мишени направленным пучком энергетических ионов инертных газов. Процесс осуществляется при давлениях 10-3-10-2 Па. Распыленные частицы материала мишени достигают подложки без соударения с газом среды и сохраняют свою энергию до конденсации на подложке. Ионно-лучевое распыление осуществляется в значительно более "чистых" вакуумных условиях, и на этапе распыления среда в меньшей степени влияет на энергию бомбардирующих ионов и состояние поверхности мишени.
Реактивное ионно-плазменное нанесение - получение сложных по составу пленочных покрытий распылением мишени в плазме, содержащей химически активный (реактивный) газ. Пленки формируются в результате химического взаимодействия распыленного материала и реактивного газа в основном на поверхности подложки и частично на поверхности распыляемой мишени.
Реактивное ионно-лучевое нанесение - получение сложных по составу пленочных покрытий распылением мишени пучком, содержащим ионы реактивного газа. Реактивное ионно-лучевое нанесение разделяется на: распыление материала мишени пучком ионов инертного газа с одновременной подачей реактивного газа в область конденсации пленки; распыление пучком, состоящим из смеси инертных и реактивных газов; распыление пучком, состоящим только из ионов реактивного газа. Пленка, формируемая в процессе реактивного ионно-лучевого нанесения, - продукт химического взаимодействия реактивного газа и распыляемого материала. Диапазон давлений – 10-3-10-2 Па.
Реактивное ионно-плазменное и реактивное ионно-лучевое нанесение являются разновидностями ионно-плазменного и ионно-лучевого нанесения покрытий. В этих разновидностях процесса к основным различиям можно отнести вид используемого газа и условия осаждения пленок на подложке. Ионно-плазменное и ионно-лучевое нанесение включают в себя процессы создания покрытий - физическое осаждение пленок в вакууме на подложках, в которых необходимый для получения покрытий материал переводится из твердой в газовую фазу распылением мишени энергетическими ионами. Распыленные частицы, осаждающиеся на поверхности подложки, формируют пленку материала.
Среди методов физического осаждения покрытий (ФОП), получивших в мировой практике наименование PVD (Physical Vapor Deposition) можно выделить: метод конденсации покрытий из пароплазменной фазы в вакууме с ионной бомбардировкой поверхностей детали (КИБ); метод реактивного электронно-плазменного осаждения покрытий из пароплазменной фазы в вакууме (РЭП); магнетронно-ионное распыление (МИР) и его разновидность - магнетронно-ионное реактивное распыление (МИРР); ионное плакирование и его разновидность – активированное реактивное распыление (метод ARE). Физические методы нанесения покрытий представляют наиболее прогрессивные направления в области производства. Возможность широкого варьирования температурой в зонах нанесения покрытий позволяет использовать вакуумно-плазменные методы в качестве универсальных методов для нанесения покрытий на инструменты из углеродистых, легированных углеродистых, быстрорежущих сталей и твердых сплавов.
Наиболее характерной особенностью покрытий, получаемых вакуумно-плазменными методами, является отсутствие переходной зоны между покрытием и материалом подложки. Это обусловлено весьма слабым взаимодействием между осаждаемым материалом и субструктурами материала подложки в условиях относительно низких температур последнего. Это обстоятельство является весьма важным, так как создается возможность получения комплекса свойств на рабочих поверхностях инструмента практически без ухудшения его объемных свойств - прочности и вязкости.
Методы ФОП реализуются в широком температурном диапазоне (200-800°С), поэтому они применимы для нанесения покрытий не только на теплостойкий твердосплавный инструмент, но и на инструменты из углеродистых, легированных углеродистых и быстрорежущих сталей с более низкой теплостойкостью.
К четвертой группе методов нанесения износостойких покрытий на формообразующие поверхности инструмента можно отнести плазменные и детонационные (газотермические) методы. Основным недостатком покрытий, напыленных плазменным методом, является высокая пористость, слабая адгезия с материалом подложки. Кроме того, плазменные методы недостаточно производительны, и при их использовании создаются сильные шумы. Несколько более качественные покрытия формируются при использовании детонационного метода – одной из разновидностей газотермического напыления, когда покрытие образуется с помощью энергии взрыва газовых смесей. Детонационные покрытия характеризуются высокой плотностью и хорошей адгезией с материалом основы [6].
Дата добавления: 2015-12-21; просмотров: 66; Мы поможем в написании вашей работы! |
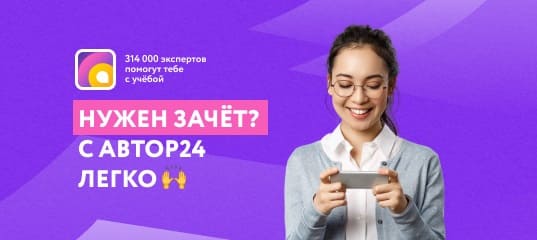
Мы поможем в написании ваших работ!