Направления ускорения оборачиваемости оборотных средств
В целях ускорения оборачиваемости оборотных средств на предприятиях должны разрабатываться организационные и технико-экономические мероприятия по ускорению прохождения каждого этапа движения оборотных производственных фондов и фондов обращения от оплаты поставщикам до получения денежных средств от потребителей. Эффект ускорения выражается в уменьшении потребности в оборотных средствах.
Основными направлениями сокращения длительности цикла на этапе закупок производственных запасов являются:
- оплата предметов труда по факту поставки, т.е. ликвидация транспортного запаса;
- механизация и автоматизация выполнения складских операций;
- компьютеризация складского учета.
Основным путем сокращения объема незавершенного производства является сокращение длительности производственного цикла, достигаемое за счет:
- повышения комплексной механизации и автоматизации производственных процессов;
- сокращение времени внутрисменных и междусменных перерывов;
- сокращение продолжительности естественных процессов.
На этапе обращения основной задачей является уменьшение времени превращения готовой продукции в денежные средства на счетах фирмы. Пути решения этой задачи:
- уменьшение запасов готовой продукции вследствие улучшения планирования сбыта;
- отпуск продукции на условиях предоплаты;
- уменьшение дебиторской задолженности;
|
|
- ускорение расчетов путем применения компьютерных программ «банк-клиент» и т.п.
Длительность одного оборота может быть уменьшена за счет сокращения производственных запасов можно снизить за счет сокращения производственного цикла и времени доставки готовой продукции.
Норму производственных запасов можно снизить благодаря совершенствованию их расхода, замене дефицитного сырья более дешевым, использованию отходов производства, повышению качества используемого материала, увеличению времени на погрузочно-разгрузочые работы, применению тары многократного пользования, унификации деталей и узлов, сокращению номенклатуры запасных частей и т.д. Организационно-технические мероприятия способствуют сокращению среднесуточного расхода материальных ценностей и интервала между поставками, следовательно, и потребности в оборотных средствах.
Сокращение длительности производственного цикла имеет важное значение для ускорения оборота средств в незавершенном производстве и может обеспечиваться повышением уровня интенсификации производственных процессов; уменьшением номенклатуры изготовляемой продукции и сроков освоения вновь вводимых производственных мощностей; улучшением использования основного капитала; снижением трудоемкости выпускаемой продукции; совершенствованием организации производства и т.д.
|
|
Для объекта исследования в целях ускорения процесса оборачиваемости оборотных средств можно рекомендовать следующие мероприятия.
Объекту исследования можно рекомендовать внедрить комплексную систему управления производством «М-3», которая позволяет совершенствовать систему управления оборотными средствами. Она предназначена для управления финансовыми и материальными потоками крупных и средних промышленных предприятий. Система разработана на основе применения мировых стандартов управления в реальных условиях функционирования российских предприятий. Интегрированная система управления предприятием "М-3" полностью соответствует требованиям, предъявляемым к интегрированным системам класса ERP.
Система управления предприятием "М-3" формирует единый информационный контур, объединяющий процессы финансового планирования, учета обязательств и расчетов, материально-технического обеспечения и сбыта, планирования и управления производством и складскими запасами, ведение бухгалтерского и управленческого учета и эффективного контроллинга деятельности предприятия.
|
|
В отличие от традиционной концепции автоматизации, предусматривающей автоматизацию уже существующих управленческих функций и написание АРМов (рабочих мест) без изменения технологии управления, внедрение современной интегрированной системы управления предприятием предполагает автоматизацию бизнес-процессов.
Внедрение системы "М-3" позволяет перейти на современную систему управления, ориентированную на управление по конкретным объектам и центрам ответственности, которая рассматривает предприятие не в виде структуры организационных подразделений, выполняющих отдельные функции, а как совокупность бизнес-процессов. Подобный подход обеспечивает не просто повышение производительности традиционных рабочих мест или отдельных структурных подразделений, а позволяет установить эффективный контроль и ответственность за достижение результатов конкретных бизнес-процессов.
Система «М-3» сочетает преимущества настраиваемого продукта с индивидуальной разработкой под заказчика, так как поставляется в виде относительно неизменного ядра, достаточно легко модифицируемых модулей и системы разработки приложений.
|
|
Интегрированная система «М-3» позволяет обеспечивать защиту информации от несанкционированного доступа и гарантировать ее целостность.
Внедрение системы «М-3» обеспечит:
- качественное повышение управляемости предприятием за счет оперативного получения учетной и аналитической информации;
- управление полным циклом выполнения заказов клиентов с контролем на каждой стадии, включая контроль обеспеченности материальными ресурсами;
- реализацию современной технологии бюджетирования и обеспечения динамической увязки необходимых ресурсов с утвержденными проектами и направлениями деятельности;
- внедрение системы управленческого учета затрат в разрезе направлений деятельности, отдельных проектов и центров ответственности;
- реализация системы управления рисками.
Как показывает опыт работы российских предприятий, переход на современную систему управления с одновременным внедрением интегрированной системы управления предприятием позволяют добиться существенного снижения уровня производственных расходов при одновременном повышении потребительского качества товаров и услуг, что позволяет говорить о радикальном повышении эффективности работы всего предприятия. Внедрение информационной системы является эффективным средством снижения отрицательного воздействия рисков на деятельность предприятия Расчеты экономической эффективности внедрения интегрированной системы управления показывают, что экономический эффект от снижения потерь окупает все затраты на систему уже через 1-2 квартала после начала ее работы в полном контуре. Общий экономический эффект от внедрения системы составляет не менее 15% от годового объёма продаж, начиная с первого года после окончания внедрения системы.
Блок «Материальные потоки (логистика)» предназначен для контроля за всеми ресурсами на всех стадиях производственного процесса без ограничений по входу и выходу, включая второстепенные и сопутствующие продукты. Блок согласует информацию и оптимизирует материально-производственные запасы по всему предприятию (от торговых подразделений до производственных). С помощью модулей, входящих в данный блок можно осуществлять оперативное и стратегическое планирование в зависимости от имеющихся заказов и потребностей в ресурсах с корректировкой на промежуточные прогнозы. Работа блока направлена на принятие хорошо обоснованных оперативных решений, направленных на снижение затрат, обеспечения календарных графиков, контроля за процессами и качеством продукции, контроля за ресурсами, хранящимися на складах.
Функции модуля "Материально-техническое снабжение":
- ведение реестра поставщиков с фиксированием партий ресурсов и описанием различных условий поставки, ведением историй цен поставки;
- ведение электронного регистра всех поступающих заявок на закупку ресурсов;
- контроль за возможностью прохождения необходимой закупки по бюджету;
- автоматическое оформление заказов поставщикам на сырье, материалы, комплектующие, работы и услуги;
- возможность определения и ведения произвольных характеристик ресурсов с возможностью подбора ресурсов с учетом требуемых характеристик;
- привязка сформированного заказа на поставку к зарегистрированному в системе договору с соответствующим поставщиком;
- автоматический подбор оптимального поставщика различными спосо-бами, в том числе, с помощью произвольно заданными факторами;
- возможность контроля за работой отдела снабжения с помощью агрегированных отчетов, отображающих в табличном и графическом виде состояние заказов;
- контроль и разнесение денежных средств по статьям бюджета;
- возможность разбиения заказа на отдельные поставки;
- контроль за состоянием заказа;
- автоматическое формирование финансовой задолженности перед поставщиком;
- отслеживание расчетов по закупкам;
- возможность автоматической регистрации документов, сопровождаю-щих процесс передачи товарно-материальных ценностей.
Сортировка и фильтрация записей в регистре по сочетанию любых задаваемых пользователем условий.
В системе предусмотрена возможность отображения отчета в графическом виде, что позволяет более наглядно увидеть текущее состояние выполнения заказов.
В системе предусмотрена автоматическая регистрации предъявленного к оплате счета поставщика и документов, сопровождающих процесс передачи товарно-материальных ценностей, что позволяет сократить время обработки информации
Сформированные документы автоматически попадают в регистры системы, которые определены для работы с ними.
Программный комплекс "Интегрированная система управления предприятием "М-3" защищен сертификатом (№ 259 от 05 августа 1999 г.) Государственной технической комиссии при Президенте РФ на соответствие требованиям "Средства вычислительной техники.
В целях совершенствования системы планирования оборотных средств возможно также использование графического метода. Например, по данным учета затрат известно, что стоимость подачи одного заказа на металл листовой составляет 200 р., годовая потребность в металле — 15500 листа, цена единицы – листа — 1300 тыс. р., стоимость содержания комплектующего изделия на складе равна 20% его цены. Определить оптимальный размер заказа на комплектующее изделие.
Уровень суммарных издержек графически представлен на рисунке 2.
Затраты (Г) на содержание запасов в определенный период
складываются из следующих элементов:
1) суммарная стоимость подачи заказов (стоимость форм документации, затраты на разработку условий поставки, на каталоги, на контроль исполнения заказа и др.);
2) цена заказываемого комплектующего, изделия;
3) стоимость хранения запаса.
![]() |
.
![]() | |||
|
Рисунок 2 - Суммарные издержки на подачу заказа и хранение запаса:
I — затраты на содержание единицы запаса, руб./шт.; О— размер
заказа, шт.; Q* — оптимальный размер заказа, шт.; S— потребность в
товарно-материальных ценностях за определенный период, шт.;
А — стоимость подачи одного заказа, руб.
Математически можно представить затраты в следующем виде:
Г=AS/Q + SC+IQ/2,
где С — цена единицы заказываемого комплектующего изделия.
Величину затрат необходимо минимизировать:
Г → min.
Дифференцирование по Q дает формулу расчета оптимального
размера заказа (формулу Вильсона):
Q* = √ 2 AS / I
где Q* — оптимальный размер заказа, шт.;
А — стоимость подачи одного заказа, р.;
S — потребность в товарно-материальных ценностях за определенный период, шт.;
I — затраты на содержание единицы запаса, р./шт.
Определяем оптимальный размер заказа по имеющимся исходным данным:
Q* = √ (2*200*15500) / 0,2 * 1300 = 154,4 ≈ 155 листов
Во избежание дефицита можно округлить оптимальный размер заказа в большую сторону. Таким образом, оптимальный размер заказа металл составляет 155 листов.
Обратим внимание, что при годовой потребности в металле 15500 листов и числе рабочих дней в году — 226 дней, оптимальный размер заказа составляет 155 шт., время поставки — 10 дней, при этом возможная задержка поставки составляет 2 дня. Определим параметры системы с фиксированным размером заказа.
Расчет параметров системы управления запасами с фиксированным размером заказа представлен в таблице 4.
Таблица 4 - Расчет параметров системы управления запасами
с фиксированным размером заказа
Показатель | Порядок расчета | Значение |
Потребность, шт. | — | |
Оптимальный размер заказа, шт. | — | |
Время поставки, дни | — | |
Возможная задержка в поставках, дни | — | |
Ожидаемое дневное потребление, шт./день 1 | [1]: [число рабочих дней] | 68,6 |
Срок расходования заказа, дни | [2]: [5] | 2,2 |
Ожидаемое потребление за время поставки, шт. | [3] х [5] | |
Максимальное потребление за время поставки, шт. | ([3]+[4]) x [5] | 823,2 |
Гарантийный запас, шт. | [8] - [7] | 137,2 |
Пороговый уровень запаса, шт. | [9] + [7] | 823,2 |
Максимальный желательный запас, шт. | [9] + [2] | 978,2 |
Срок расходования запаса до порогового уровня, дни2 | ([11] -[10]): [5] | 2,25 |
1 Округление производится в большую сторону.
2 Округление производится по общим правилам.
Учитывая, что далеко не все поставщики добросовестно выполняют свои обязательства необходимо учитывать возможные срыва. Однако, данный способ можно использовать для графического моделирования работы системы управления запасами с фиксированным размером заказа при
наличии сбоев в поставках.
В системе с фиксированным размером заказа последний
выдается в момент, когда текущий запас достигает порогового
уровня. Сбои в поставках могут быть связаны со следующими мо-
ментами:
- задержка в поставках;
- преждевременная поставка;
- неполная поставка;
- поставка завышенного объема.
Система с фиксированным размером заказа не ориентирована
на учет сбоев в объеме поставок. В ней не предусмотрены парамет-
ры, поддерживающие в таких случаях систему в бездефицитном
состоянии.
Если начальный объем запаса соответствует максимальному желательному запасу.
При оптимальном размере заказа запас пополняется до максимального желательного уровня.
Первая поставка производится с задержкой, равной
максимально возможной. Это приводит к использованию гарантийного запаса, и возникает необходимость в его пополнении. Первый поступивший заказ пополняет запас до уровня меньше порогового. Это требует введения в рассматриваемую систему дополнительного условия выдачи заказа: если поступивший заказ не пополняет систему до порогового уровня, то новый заказ производится в день поступления заказа. В противном случае система с данными расчетными параметрами не может работать при наличии задержки в
поставках.
Данная ситуация возникает из-за несоответствия конкретных значений оптимального размера заказа и временных параметров поставки (время поставки и возможная задержка поставки).
При неоднократных задержках в поставках система с фиксированным размером заказа (при данных исходных значениях) может перейти в дефицитное состояние, которое может усугубляться задержкой следующих поставок.
Для исправления ситуации необходимо потребовать от поставщика одноразового увеличения объема поставки, что позволит пополнить запас до желательного максимального уровня.
Если интервал времени между заказами фиксирован, но имеют место сбои в поставках, то использование графического метода будет иметь следующий вид.
Прежде всего, отметим, что в системе с фиксированным интервалом времени между заказами последний выдается в фиксированный момент времени. Размер заказа должен быть пересчитан таким образом, чтобы поступивший заказ пополнил запас до максимального желательного уровня:
РЗ = МЖЗ - ТЗ + ОП.
где РЗ — размер заказа, шт.;
МЖЗ — максимальный желательный запас, шт.;
ТЗ — текущий запас, шт.;
ОП — ожидаемое потребление за время поставки, шт.
Система с фиксированным интервалом времени между заказа-
ми не ориентирована на учет сбоев в объеме поставок. В ней не
предусмотрены параметры, в таких случаях поддерживающие си-
стему в бездефицитном состоянии.
Начальный объем запаса соответствует максимальному желательному запасу. Как видно из рисунка 6, при отсутствии сбоев в поставках поступление заказа происходит в момент, когда достигается гарантийный уровень запасов. Рассчитанный по формуле (15) размер заказа пополняет запас до максимального желательного уровня.
Максимальный желательный запас, шт.
Рисунок 6 - Графическая модель работы системы управления запасами
с фиксированным интервалом времени между заказами при отсутствии сбоев в поставках
На рисунке 7 первая поставка производится с задержкой, равной
максимально возможной. Это приводит к использованию гаран-
тийного запаса, и возникает необходимость в его пополнении. Первый
поступивший заказ пополняет запас до уровня меньше порогово-
го. При расчете размера второго заказа учет текущего запаса и
размера не поступившего еще первого заказа позволяет при по-
ступлении второго заказа без задержек пополнить запас до мак-
симального желательного уровня.
Максимальный желательный запас, шт.
Рисунок 7 - Графическая модель работы системы управления запасами с фиксированным интервалом времени между заказами при наличии одной задержки в поставках
При наличии задержек в поставках, как видно из рисунка 7, система с фиксированным интервалом времени между заказами всегда находится в бездефицитном состоянии. При отсутствии сбоев в потреблении каждый вновь поступивший заказ пополняет запас до максимального желательного уровня
Существенно облегчить работу в области планирования и нормирования оборотных средств может оказать система планирования потребностей в материалах (система MRP I). В узком смысле она состоит из ряда логически связанных процедур, решающих правил и требований, переводящих производственное расписание в «цепочку требований», синхронизированных во времени, и запланированных «покрытий» этих требований для каждой единицы запаса компонентов, необходимых для выполнения расписания.
Основными целями системы MRP I являются:
- удовлетворение потребности в материалах, компонентах и продукции для планирования производства и доставки потребителям;
- поддержание низкого уровня запасов материальных ресурсов (МР), незавершенного производства (НП) и готовой продукции (ГП);
- планирование производственных операций, расписаний доставки, закупочных операций.
В процессе реализации этих целей система MRP I обеспечивает поток плановых количеств материальных ресурсов и запасов продукции за время, используемое для планирования. По системе MRP I сначала определяется, сколько и в какие сроки необходимо произвести конечной продукции. Затем рассчитывается время и необходимые количества материальных ресурсов для удовлетворения потребностей производственного расписания. На рисунке 8 представлена блок-схема системы MRP I.
![]() |
![]() |
Производственное ра
расписание
MRP
Программный
комплес
комплекс
Рисунок 8 – Блок-схема системы MRP I
Рассмотрим примеры.
ОАО «Нефтемаслозавод» использует в технологических процессах металлорежущий инструмент (резцы и сверла). Производственная программа основной продукции, производимой заводом, на планируемый год составляет 300 тыс. изделий. Необходимо рассчитать потребность завода в металлорежущем инструменте на планируемый год. При этом предполагается, что в плановом году за счет восстановления работоспособности части инструмента (величина внутренних резервов предприятия) будет покрыто 20% потребности в нем.
Для расчета стойкости инструмента, определения его срока службы, нормы расхода каждого наименования инструмента на определенное количество изделий (в данном случае — на 1000 изделий), переходных запасов инструмента и расчета потребностив нем на планируемый год следует использовать исходные данные, приведенные в таблице 5. Кроме приведенной выше исходной основной информации для расчета потребности в металлорежущем инструменте необходимы дополнительные данные, которые представлены в таблице 7.
Отметим, что в плановом году потребность в металлорежущем инструменте на ремонтно-эксплуатационные нужды устанавливается в размере 5% от потребности в нем для выполнения основной производственной программы (по всем трем наименованиям инструмента). Потребность завода в инструменте по кварталам распределяется равномерно.
Таблица 6 - Исходные данные для проведения расчетов
Направления расчета и необходимые параметры | Резец | Сверло | Резец расточной |
А. Для расчета стойкости и срока службы инструмента | |||
Длина рабочей части инструмента, мм | |||
Величина слоя рабочей части, стачиваемая за одну переточку, мм | 0,5 | 0,7 | 0,5 |
Время работы инструмента между переточками, час. | 0,5 | 1,0 | 1,5 |
Б. Для расчета переходящих запасов инструмента | |||
Величина максимального текущего запаса, дней | |||
Величина страхового запаса, дней | |||
В. Для расчета потребности в инструменте | |||
Остаток инструмента на 1 января, шт. | |||
Ожидаемый расход инструмента, шт. |
Таблица 7 - Дополнительные данные для проведения расчетов
Наименование инструмента | Наименование детали | Кол-во деталей в изделии, шт. | Машинное время на одну деталь, мин. |
Резец | 1П244 | ||
Резец | 1П252 | ||
Сверло | 2К343 | ||
Резец расточной | 4Н101 |
Результаты расчета потребности машиностроительного завода в металлорежущем инструменте должны быть представлены в логической последовательности и состоять из следующих позиций: наименование инструмента; единица измерения; остаток на 1 января; ожидаемый расход; потребность для выпуска товарной продукции; потребность на ремонтно-эксплуатационные нужды; величина переходящих/запасов (количество, дни); ожидаемый остаток; внутренние резервы, восполняющие потребность; распределение потребности по кварталам планируемого года.
Ремонтному цеху машиностроительного завода для проведения капитального ремонта в июне необходимы материалы девяти наименований. Номенклатура материалов, используемых для ремонта, их остаток к началу планового периода, цена за единицу материала и их удельный вес в общей стоимости материалов, используемых в капитальном ремонте, приведены в таблице 8.
Необходимо установить лимит на материалы для ремонтного цеха на июнь, получаемые со склада отдела материально-технического снабжения машиностроительного завода. Для проведения расчета предлагаются следующие дополнительные исходные данные.
Таблица 8 - Исходные данные для проведения расчета
Наименование материала | Остаток на 1 июня | Плановая цена за единицу, усл. ед. | Количество материалов, % к общей потребности |
Чугунное литье, т | 1.5 | 30,0 | |
Стальное литье, т | 0,3 | 10,0 | |
Поковки, т | — | 15,0 | |
Рядовой прокат, т | 1,0 | 27,5 | |
Качественный прокат, т | 0,1 | 5,0 | |
Железо листовое, т | — | 2,0 | |
Баббит и заменители, кг | — | 0,5 | |
Бронза, кг | 2,0 | 3,0 | |
Покупные детали, т | 0,2 | 7,0 |
Программа капитального ремонта на июнь для ремонтного
цеха устанавливается в стоимостном выражении и составляет
100 тыс. условных единиц. Удельный вес стоимости материалов, используемых в процессе проведения капитального ремонта, в общей стоимости ремонта составляет 40%. Плановый остаток материалов на конец июня должен быть
установлен в размере трехдневной потребности в них ремонтного цеха.
Заключение
Для нормального функционирования каждого предприятия необходимы оборотные средства, представляющие собой денежные средства, используемые предприятием для приобретения оборотных фондов и фондов обращения.
Оборотные фонды, т.е. материальные ресурсы в отличие от основных фондов используются в одном производственном цикле, и стоимость их переносится на продукт сразу и полностью.
Рациональное и экономное использование оборотных фондов первоочередная задача предприятий, так как материальные затраты составляют 3/4 себестоимости промышленной продукции. Снижение материалоемкости изделия (расход материальных ресурсов в натуральном и стоимостном выражении на единицу продукции) достигается различными путями, среди которых главными являются внедрение новой техники, технологии, совершенствование организации производства и труда.
Основная черта современного переходного периода нехватка у предприятий оборотных средств. Ускорение оборачиваемости оборотных средств, которое измеряется коэффициентом оборачиваемости и длительностью одного оборота в днях, достигается различными мероприятиям на стадиях создания производственных запасов, незавершенного производства и на стадии обращения.
Список используемой литературы
1. Горемыкин В.А., Бугулов Э.Р., Богомолов А.Ю. Планирование на предприятии: Учебник. – М.: Информационно-издательский дом «Филинъ», 2003, -328 с.
2. Грузинов В.П., Грибов В.Д. Экономика предприятия. Учеб. Пособие - 2-
е изд., доп. - М.: Финансы и статистика, - 2001. - 343 с.
3. Зайцев Н.Л. Экономика организации. - М.: «Экзамен», 2000. - 768 с.
4. Маркин Ю.П. Анализ выявления внутрипроизводственных резервов. – М.: Финансы и статистика, 2001г. – 160с.
5. Организация, планирование и управление деятельностью промышленных предприятий: Учеб. Для экон. Спец. Вузов / Каменицер С.Е., Русинов Ф.М., Мельник М.В. и др.; Под ред. С.Е. Каменицера и Ф.М. Русинова. – 2-е изд., перераб. И доп. – М.: Высшая школа, 1999.– 335 с.
6. Организация предпринимательской деятельности: Учебное пособие /
Под ред Пелиха А.С. Ростовн/Д: издательский центр «МарТ», 2002. - 336 с.
7. Савицкая Г.В. Анализ хозяйственной деятельности: 2-е изд. перераб. и
доп. - М.: ИП «Экоперспектива», - 2001. - 458 с.
8. Смирницкий Е.К. Экономические показатели промышленности: Справочник. 3-е изд., перераб. И доп. – М.: Экономика, 2000. – 335 с.
9. Экономика предприятия. /Под ред. Е.Л. Кантора.-СПб.:Питер, 2003 г. -
352 с.
10. Экономика предприятия (фирмы): Учебник / Под ред. проф. О.И. Волкова и доц. О.В. Девяткина. – 3-е изд., перераб. и доп. – М.: ИНФРА-М, 2003
Дата добавления: 2015-12-20; просмотров: 16; Мы поможем в написании вашей работы! |
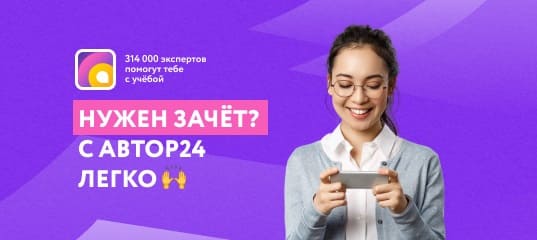
Мы поможем в написании ваших работ!