Гибкие производственные системы
Общие сведения. Термины и определения.
По ГОСТ 26228 — 90 основополагающее понятие гибкая производственная система (ГПС) - это управляемая средствами вычислительной техники совокупность технологического оборудования, состоящая из разных сочетаний гибких производственных модулей и (или) гибких производственных ячеек, автоматизированной системы технологической подготовки производства и системы обеспечения функционирования, обладающая свойством автоматизированной переналадки при изменении программы производства изделий, разновидности которых ограничены технологическими возможностями оборудования.
ГПС представляют собой наиболее важное технологическое достижение XX века после появления сборочного конвейера. Их внедрение имеет для промышленности поистине революционное значение, поскольку вызывает резкое сокращение себестоимости продукции, изготовляемой в условиях массового, серийного и мелкосерийного производства. В то же время результатом внедрения ГПС является значительное повышение требований к квалификации обслуживающего персонала.
Именно ГПС знаменуют собой начало этапа научно-технической революции, позволившего в машиностроении достичь уровня автоматизации, на который давно вышли перерабатывающие отрасли массового производства.
Составными частями ГПС являются: гибкий производственный модуль (ГПМ); гибкая производственная ячейка (ГПЯ); гибкий производственный участок (ГПУ); система обеспечения функционирования ГПС и ГПЯ.
|
|
ГПМ — это единица технологического оборудования, управляемая средствами вычислительной техники, автоматически осуществляющая технологические операции в пределах своих технических характеристик, способная работать автономно и (или) в составе ГПС или ГПЯ. В средства автоматизации ГПМ в общем случае могут входить:
Устройства ЧПУ для автоматизации последовательности действий рабочих органов технологического оборудования (включая смену заготовок, изделий, инструмента, подачу СОЖ, удаление отходов, переналадку);
Устройства адаптивного управления для автоматизации регулирования параметров технологического процесса;
Устройства контроля и измерения изделия во время или после обработки;
Устройства диагностирования оборудования и т.д.
Основные свойства ГПМ: способность работать автономно и без участия человека в течение ограниченного времени; автоматическое выполнение всех основных и вспомогательных операций; максимально полная обработка деталей с одного установа, на одной операции; гибкость, удовлетворяющая требованиям мелкосерийного производства; легкость наладки и устранения отказов, а также удобство управления; возможность легко встраиваться в традиционное и гибкое производство; экономическая эффективность.
|
|
ГПЯ, управляемая средствами вычислительной техники, представляет собой совокупность нескольких ГПМ (а следовательно, и нескольких единиц технологического оборудования) и системы обеспечения функционирования. ГПЯ осуществляет комплекс технологических операций, способна работать автономно и в составе ГПС при изготовлении изделий в пределах подготовленного запаса заготовок инструмента.
Примечание: Отмеченное мелким курсивом * для расширения общих понятий о производственных процессах в машиностроении.
Система обеспечения функционирования (СОФ), предназначенная для ГПС — это совокупность взаимосвязанных автоматизированных систем, обеспечивающих управление технологическим процессом, перемещением предметов производства и оснастки*. В состав этой системы входят: автоматизированная система инструментального обеспечения (АСИО), автоматизированная транс-портно-складская система (АТСС), система автоматизированного контроля (САК), автоматизированная система удаления отходов (АСУО), автоматизированная система управления технологическим оборудованием (АСУТО) и др.
|
|
Примечание: Обратите внимание на терминологию из других дисциплин ФГОС.
Таким образом:
Гибкая производственная система – это несколько единиц технологического оборудования, снабженного средствами и системами, обеспечивающими функционирование в автоматическом режиме.
ГПС представляет собой совокупность (в различных сочетаниях) оборудование с ЧПУ, роботизированных технологических комплексов, гибких производственных модулей и систем обеспечения их функционирования в автоматическом режиме.
При этом ГПС должна обладать свойством автоматизированной переналадки при переходе на производство новых изделий в пределах заданной номенклатуры.
По организационным признакам ГПС подразделяются на следующие виды:
Гибкая автоматизированная линия – ГАЛ;
Гибкий автоматизированный участок - ГАУ;
Гибкий автоматизированный цех.
ГАЛ и ГАУ состоят из гибких производственных модулей или отдельных единиц технологического оборудования, управляемые от устройств ЧПУ.
Таким образом:
Под ГПМ понимается единица технологического оборудования, оснащенного системой ЧПУ или каким-либо другим устройством программного управления и функционирующая как самостоятельно, так и в составе ГПС; при этом все функции, связанные с изготовлением изделия, должны осуществляться автоматически.
|
|
ГАЛ - это ГПС, состоящая из ГПМ, РТК или другого технологического оборудования, объединенного АСУ.
ГАУ – это ГПС, состоящая из ГПМ, РТК или другого технологического оборудования, объединенных АСУ, в которой в от ГАЛ предусмотрена возможность изменения последовательности использования технологического оборудования, что обеспечивает оптимальную загрузку последнего и позволяет изготовлять детали в комплекте, необходимой для сборки изделия.
ГАЦ – это ГПС, представляющая собой совокупность ГАЛ и ГАУ, предназначенных для изготовления изделий заданной номенклатуры.
ГАЗ представляет собой ГПС, состоящую из ГАЦ и обеспечивающую выпуск готовых изделий в соответствии с планом основного производства.
В общем случае средства автоматизации ГПМ включает: накопители заготовок, режущего и мерительного инструмента, технологическую оснастку, устройства загрузки – выгрузки обрабатываемых изделий, устройства удаления отходов, устройства автоматизированного контроля, устройства диагностики технического состояния оборудования и инструмента, устройства обеспечения точности обработки и др.
Следует отметить, что каждый конкретный ГПМ оснащается только тем из указанных устройств, которые необходимы для его работы*
Совокупность единицы технологического оборудования, промышленного робота и средств оснащения, функционирующая автономно и осуществляющая многократные рабочие циклы, называется робототехническим (роботизированным технологическим) комплексом, сокращенно РТК.
Рассмотрим обобщенную комплектно-структурную схему элементов и подсистем ГПС, выбрав из нее отдельные элементы, выполняющие или обеспечивающие выполнение условий автоматизации управления.
Рис.1.Обобщенная схема элементов и подсистем ГПС.
Не рассматривая детально состав отдельных элементов МРС, в том числе в составе ГПС, отметим, что все главные и вспомогательные механизмы:
Модуль ГПМ,
Специальное оборудование,
МРС,
КПО,
Вспомогательное технологическое оборудование,
КИМ,
Транспортно – складские системы,
АСУ,
Подготовка и обеспечение производства- все эти элементы имеют
4. СИСТЕМЫ УПРАВЛЕНИЯ.
Здесь уместно напомнить:
Системы управления – это комплекс различного оборудования.
Управление предусматривает наличие технических средств управления и математических средств управления.
А это все не что иное, как специальное обеспечение. Иными словами: понятие современных систем управления технологическими процессами на примере МРС или ГПМ включает:
1. Станочно – технологическую часть;
2. Электронно – приводческую часть;
3. Вычислительно – управляющую часть.
Системы управления. Основные понятия и определения.*
Рассмотрим основной понятийный аппарат о системах управления МРС, применяемый в источниках информации при изучении вопросов данного раздела.
Управление
Технические средства управления
Математические средства управления
Алгоритм управления
Управляющее воздействие
Задающее воздействие
Возмущающее воздействие
Датчик обратной связи и др.
Определения указанных терминов смотри терминологический словарь.
Технические устройства (рабочие механизмы МРС), в которых процессы подлежат управлению или регулированию, называются объектами управления или регулирования.
Физические величины, подлежащие управлению или регулированию называются регулируемыми или управляемыми параметрами (величинами).
Внешнее воздействие, вызывающее отклонение регулируемой величины от её заданного значения, называются возмущающими воздействиями.
Технические устройства, предназначены для автоматического регулирования (управления) величин (параметров) называются автоматическими регуляторами.
*Примечание.
1.Обратите внимание на терминологию, выделенную жирным шрифтом.
2.Материал данной главы включен для расширения общепрофессиональной подготовки при изучении принципа работы принципиальных схем электроавтоматики МРС.
В состав автоматического регулятора технических систем входят:
Измерительный элемент (датчик).
Элемент сравнения – устройство, предназначенное для сравнения фактического значения регулирования величины с его заданным значением.
Исполнительное устройство, и другие элементы, изучаемые в дисциплине «Элементы и устройства автоматики».
Таким образом, понятие Система управления – это комплекс технических средств, объекта управления, автоматического измеряющего устройства, совокупность упорядоченных приёмов управления, взаимодействие которых приводит к достижению поставленной цели управления.
5.1.Классификация систем управления..
Существует большое разнообразие систем управления. Не ставя задачу дать полную классификацию систем управления, рассмотрим наиболее характерные классификационные признаки, знание которых позволит более осмысленно изучать не только блок-схемы, структурные и принципиальные схемы управления конкретных систем управления технологическими процессами.
По виду задач, связных с управлением объектами, в том числе рабочими механизмами МРС, системы управления подразделяют на:
Системы автоматического контроля;
Системы автоматического регулирования;
Системы автоматического управления;
Системы адаптивного управления;
Системы обработки данных;
Системы автоматического управления производства и др.
В свою очередь системы САР или САУ так же могут иметь разное назначение, что позволяет так же рассматривать их классификации, как подсистемы. Например, изучая самостоятельно конкретные системы управления МРС, следует отметить, что функциональное назначение систем (или подсистем управления) может быть совместимым. Например, САР представляет собой совокупность систем автоматического контроля регулируемого параметра (например, скорость подачи инструмента, диаметр обрабатываемого изделия) и системы управления скоростью вращения приводного электрического двигателя (например, привода шпинделя или суппорта).
5.2.Понятия о типовых замкнутых и разомкнутых структурах систем управления рабочими механизмами технологического оборудования.
По наличию или отсутствию обратной связи системы управления МРС бывают:
5. 2.1. Разомкнутые.
5. 2.2. Замкнутые.
Системы управления, работающие по разомкнутому циклу, используют как составные части более сложных систем. В свою очередь замкнутые системы могут иметь главную обратную связь, например при регулировании какого-либо параметра системы (скорости двигателя), а так же другие обратные связи, предназначенные для улучшения динамических свойств системы (для улучшения работы системы в переходных режимах работы).
Обратная связь называется положительной, если сигнал обратной связи (например Uос какого-либо датчика) суммируется с сигналом задания. Обратная связь называется отрицательной, если сигнал обратной связи вычитается из основного (задающего сигнала).
5.3. По закону изменения регулируемой величины системы делятся на:
5. 3.1. Системы стабилизации или поддержания постоянства регулирования.
5.3.2. Системы программного управления.
5.3.3. Следящие системы.
Системы стабилизации предназначены для поддержания постоянного значения регулируемого параметра.
Системы программного управления предназначены для управления регулируемой величиной по заранее известному закону, заложенному (запрограммированному) в управляющей программе.
Следящие системы предназначены для изменения регулируемой величины (управляемого параметра) по заранее неизвестному значению.
5. 4. По функциональной связи между входящими и выходящими величинами элементов, входящих в состав системы управления системы подразделяются (бывают):
5. 4.1. Непрерывные.
5.4.2. Дискретные.
Непрерывными системами называют систему, в которой непрерывному изменению величин элементов соответствуют непрерывные изменения выходных величин этих элементов.
Дискретной системой управления называют систему, в которой непрерывному изменению входной величины хотя бы одного элемента, входящего в состав системы, соответствует дискретное изменение выходной величины этого элемента.
Не останавливаясь на других классификационных признаках, отметим, что системы управления бывают линейные и нелинейные, адаптивные и неадаптивные, прямого или косвенного действия и др.
5.5.Функциональные схемы систем управления.
Не рассматривая общие вопросы управляющих систем технологическими процессами в машиностроении, необходимо познакомиться с понятиями блок-схема и назначением линий связи.
Изучая общие вопросы оборудования, нужно отметить, что в теории автоматического регулирования основное внимание уделяется не техническим характеристикам или свойствам отдельных элементов, а их функциональным преобразованиям и характеру связи между ними. Наглядное представление об этом дают функциональные схемы систем управления, имеющие в графическом изображении много общего с функциональными схемами. Блок-схема – это условное графическое изображение технической системы, дающее общие представление о составе системы и функциональных связях между элементами или блоками системы.
Функциональные схемы отражают взаимодействие устройств и элементов систем управления в процессе их работы. Графические элементы или отдельные устройства САР изображают в виде прямоугольников, а существующие (рабочие) связи между ними – стрелками, указывающими направление прохождение сигнала. Каждый элемент обозначается буквами, обозначающими функциональное назначение элемента.
5.6. Системы автоматического контроля.
Контроль является одной из действительных форм борьбы за улучшения качества работы МРС.
Рассмотрим принцип работы САК на примере блок-схемы и принципа работы обобщенной системы автоматического контроля.
Типы применяемых датчиков, наличие и разновидности усилителей, преобразующих устройств зависят от требований точности к измерений, видов изменяемых поверхностей и многих других факторов.
В качестве исполнительных органов применяют указывающие, сигнализирующие, регистрирующие или отклоняющие устройства. Кроме того, различают САК с прямым измерением, когда датчик размеров непосредственно контактируется с измеряемой поверхностью и косвенным измерением, когда датчик контактируется с рабочими органами, сложение которых определяет размер.
5.7.Системы автоматического управления
технологическим оборудованием
Под управлением металлорежущим станком понимают совокупность воздействий на его механизмы и устройства в целях выполнения требуемого технологического цикла обработки заготовки с заданной точностью, производительностью и себестоимостью выполненной операции.
Циклом работы оборудования называют совокупность основных и вспомогательных перемещений рабочих органов, осуществляемых в определенной последовательности, необходимой для выполнения оборудованием рабочих функций.
Этап цикла — простейшая не расчленяемая его часть. В течение отработки этапа цикла не происходит никаких изменений (включений или отключений) в состоянии рабочих и вспомогательных органов оборудования. Этап цикла также называют тактом работы схемы (этот термин полностью эквивалентен термину «этап цикла», применяемому в релейных схемах).
Управление станком заключается в получении сведений о результатах
воздействия на его устройства (перемещения рабочих органов, срабатывание различных механизмов), анализе этой информации, выработке решения и в исполнении данного решения. Управление станком может выполняться вручную рабочим или без его непосредственного участия — системой автоматического управления. При управлении вручную рабочий использует свой опыт и сведения о методах обработки, последовательности выполнения технологических переходов, применяемых режимах резания, возможностях и особенностях конструкции используемого станка, режущих инструментах и др. На основе разработанной технологической карты или своего опыта и знаний рабочий выбирает нужный режущий инструмент, зажимные и другие приспособления, мерительный инструмент, выполняет их установку, наладку и подналадку и затем, осуществляя управление процессом обработки, получает соответствующие его квалификации качество продукции и производительность.
При автоматическом программном управлении металлорежущим станком указанные функции выполняет система программного управления (СПУ)*, работающая по заранее составленной управляющей программе, вводимой в систему с помощью соответствующего программоносителя.
Забегая вперед изучения дисциплины, отметим, что одним из основных элементов СПУ является электрический привод станка. Привод состоит из электродвигателя, силового преобразователя, механической системы и блока управления. Электродвигатель «преобразует электрическую энергию в механическую. Силовой преобразователь является источником питания электродвигателя регулируемым напряжением. Механическая система обеспечивает передачу механической энергии от электродвигателя к рабочему органу станка.
* Внимание. Системы программного управления являются одними из главных современных систем управления в машиностроительном производстве.
В станкостроении в большинстве случаев применяют автоматизированный электропривод, т.е. электропривод с автоматическим регулированием параметров.
В системах автоматического управления МРС важным звеном является блок управления, формирующий управляющее воздействие на силовой преобразователь, включает в себя задающие датчики и датчики обратной связи, преобразующие информацию элементов привода и регуляторов, на входах которых эта информация сопоставляется с заданными значениями.
Все элементы систем управления приводами рабочих механизмов взаимосвязаны. Внутренние обратные связи соединяют электродвигатель с управляющим силовым преобразователем. Механические передачи соединяют рабочий орган с электродвигателем.
Поэтому электромеханическую схему привода МРС следует рассматривать только целиком, не расчленяя на части.
Функционирование станка зависит от его структуры и алгоритма управления. При этом структура и технологический процесс станка определяют состав САУ и связь между рабочими органами, вспомогательными механизмами и устройствами. Алгоритм управления, по которому работает САУ, предписывает последовательность выполнения разных функций управления станком.
По функциональному назначению различают следующие виды автоматического управления.
1.Управление повторяющимся автоматическими циклами обработки; примером этого служит управление агрегатным станком, выполняющим фрезерные, сверлильные, расточные резьбонарезные работы. Управление этими циклами работы оборудования традиционно осуществлялось с помощью релейно-контактной автоматики, работающей по жесткой схеме. В последние годы в качестве управляющего устройства в таком случае используются программируемые контроллеры (ПК) или программируемые командоаппараты, программируемые реле.
2. Управление измеряемыми автоматическими циклами (цикловое программное управление), которые задают в виде индивидуальных для каждого цикла материальных моделей-аналогов (копиров, наборов кулачков, системы упоров и т.д.); примерами являются системы управления копировальными токарными и фрезерными станками, многошпиндельными токарными автоматами и др.
3. Числовое программное управление (ЧПУ), при котором программу задают в виде записанного на том или ином носителе массива информации; управляющая информация для систем ЧПУ является дискретной, и ее обработка в процессе управления осуществляется цифровыми методами.
Числовым программным управлением (ЧПУ) металлорежущим станком называют управление обработкой заготовки на станке по УП, в которой данные заданы в цифровой форме.
Системы программного управления могут быть классифицированы по информационным признакам, под которыми понимают число и структуру потоков информации при управлении различными металлорежущими станками. Чем полнее информация, используемая в СПУ, тем выше качество ее работы и шире ее функциональные возможности.
Источником информации, поступающей на вход СПУ, является УП, а в качестве обратной связи могут использоваться потоки информации, характеризующие состояние процесса обработки положение рабочих органов станка, размеры заготовки, уровень вибраций, тепловые деформации); информация о возмущениях, действующих в процессе обработки и не зависящих от процесса травления (например, припуски, твердость материала заготовки, температура окружающей среды и др.).
По способу задания информации САУ подразделяются на четыре-группы:
I — САУ с распределительным валом, где УП задается в аналоговом виде - рабочие и командные кулачки устанавливают на распределительном валу в соответствии с разработанной циклограммой;
II — копировальные САУ, где УП задается также в аналоговом
виде — с помощью копира;
I II — системы циклового программного управления (СЦПУ),
которых размерная информация задается в аналоговом виде с помощью путевых упоров, устанавливаемых на сменных линейках, а цикловая — в цифровом виде набором необходимых данных на пульте управления;
IV— системы ЧПУ (СЧПУ), в которых УП задается в цифровом виде либо вводится с пульта оператором, либо поступает от ЭВМ высокого уровня управления.
Системы автоматического управления могут строиться на механической, гидравлической, пневматической, электрической электрогидравлической и электронной основах.
Дата добавления: 2015-12-20; просмотров: 18; Мы поможем в написании вашей работы! |
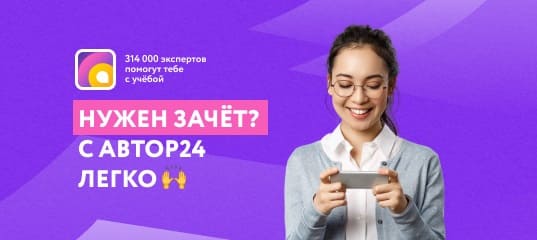
Мы поможем в написании ваших работ!