Литейные свойства сплавов.
1)Жидкотекучесть – это способность сплава в жидком состоянии заполнять литейную форму и воспроизводить размеры и формы литейной формы и стержней. Она увеличивается с увеличением температуры перегрева сплава. Углерод и фосфор улучшают жидкотекучесть.
2)Усадка - общее уменьшение объема и размеров отливок при охлаждении и затвердевании. Для предотвращения устанавливаются прибыли, для дополнительной подачи металла при его затвердевании.
3) Внутренние литейные напряжения- при охлаждении и затвердевании металла отливки в следствии усадки возникают внутренние усадочные напряжения если , то возникает деформация. Если
то происходит разрыв- образование трещины. Предотвратить это можно увеличением жидкотекучести и медленным охлаждением сплава в области высоких температур.
4)ЛИКВАЦИЯ (???)- это неоднородность сплава по химическому составу, как в отдельных частях отливки(зональная), так и в кристаллоидах(???) стали ликвидируют углерод, фосфор, сера, образуя неоднородность сплава. Предотвращается хорошим перемешиванием сплава при заливке.
5)Поглощение газов? Металлы и сплавы при плавке способны поглощать газы(водород, метан) из ржавчины, влаги, топлива и изменяется качество сплава. Понижение поглощение газов может быть достаточно пропусканием через сплав других газов, не поглощаемых этими сплавами, но убирающие растворенные газы, или применение плавки в вакуумных печах.
|
|
Требования предъявляемые к литейным сплавам:
1)Они должны по возможности хорошо заполнять литейную форму т.е. иметь высокую. Жидкотекучесть.
2)Они должны иметь низкую температуру плавления.
3)Они должны обладать незначительной усадкой при охлаждении.
4)Они должны обладать незначительной способностью поглощать газы.
5)Они должны обладать хорошей структурой.
6) Они должны обладать незначительной способностью ликвации, которая в некоторых местах сплав.
7)Они должны иметь наименьшую стоимость.
8)Они должны легко обрабатываться резанием, иметь достаточно хорошую свариваемость.
7. Литьё в песчано-глинистые формы: сущность технологического процесса, технологические возможности, область применения и оснастка.
1,2 – рёбра;
3 – модель;
4 – стержень;
5 – форма;
6 – стояк;
На долю этого способы приходится до 70% отливок материалов – для изготовления литейных форм служат формировочные смеси из песка и глины. С добавлением добавок:
1)отходы целлюлозно-бумажной промышленности не дают осыпаться.2)каменноугольные пыли не дают пригорать смеси.3)отходы мазута не дают пригорать смеси для цветных металлов. Технологический процесс:
1)Приготовление формовочной смеси:-сушка песка и глины в печах
|
|
-размалывание глины на мельницах и бегунах до мелкодисперсного состояния
-перемешивание смеси-вылеживание смеси-подача на формовку
2) Формовка (обеспечивает получение литейной формы) Для её обеспечения необходимо следующие: опоки, литейные модели и стрежни. Литейная модель - копия очертаний отливаемой детали с учетом припуска на механическую обработку. Материалом для изготовления литейных форм служит дерево (орех, бук, береза, липа, сосна, ель). Часто модель склеивают из отдельных кусочков с различным направлением волокон (для большей прочности) Она выдерживает 5-500 отливок. Иногда изготавливают из чугуна, латуни.
Для получения полостей и отверстий изготавливают стрежни.
Опоки - это ящики, имеющие только стенки (РИС)
3) Заливка- способ подвода расплава в форме зависит от конфигурации, толщины стенок и металла.При заливке чугуна металл подводится к тонким стенкам, чтобы обеспечить равномерное охлаждение. При заливке стали металл подводится к утолщенным элементам, т.е. характерна большая усадка. Также применяется дождевая литниковая система, сифонная(???)литниковая система.4) После заливки выдержка до затвердевания5) Выбивка6)Очистка осуществляется от стрежней. Применяется гидроочистка во вращающихся барабана; электрогидравлическим ударом, электрохимическая.7)Литники и прибыли отрезаются пилами8)Контроль: внешние дефекты, замеры, химический состав, электрохимическим или электрографическим способом; внутренние дефекты(рентген, магнофлокс(???))В последнее время применяется машинная формовка, что повышает точность отливки. Нормы литья регламентированы ГОСТ.Классы точности отливок:
|
|
-размерной до 100 кг 7-13 классы(7 для маленьких отливок в массовом производстве; 13 для крупногабаритных отливок в единичном производстве)
-допуски 9-14 квалитеты-шероховатость 0,2 -40 мкм-припуски 2.5 – 10 мкм на сторону Достоинства: - выполнение для различных условий производства
-сложность конфигурации-различные масса и габариты
Недостатки: -высокая трудоемкость-длительность-низкая производительность при ручной формовке- низкое качество-высокие припуски-отрицательное воздействие на окружающую среду
9. Литьё в оболочковые формы: сущность технологического процесса, технологические возможности, область применения и оснастка.
Поскольку прочность литейной формы в песчано-глинистые формы невысока, это требует большое количество формовочной смеси(на 1 т литья используется 4-12 т смеси).Достижения Химии полимеров позволили найти связывающие повышающие прочность смеси в сухом состоянии, т.е. появилась возможность заменить песчано-глинистую форму оболочковой.
|
|
Материалы: -кварцевый песок-термореактивная смола
Предел прочности такой смеси повышается в 15-20 раз, и составляет 5 МПа
РИС.Процесс литья: начинается с того что на подмодельный щиток устанавливается модель (они металлические) они нагреваются до 200-300градусов, смазываются разграничительной смазкой и выдерживаются 10-30 сек. Засыпается формовочная смесь, смола нагревается и связывает песчинки, образуя оболочу 6-15 мм. После удаления смеси оболочка вместе с модельной плитой помещаются в печь, где при 600-700 выдерживаются 3 мин., при этом смола изменяется переходя в твердое состояние. После этого оболочка выталкивается. Если форма состоит из двух, то их склеивают. При необходимости устанавливается стержень и производится заливка металла. После охлаждения отливки оболочка спокойной разрушается, т.к. часть смолы выгорает. Смесь регенерируется(?) т.е. огнеустойчивый наполнитель может быть использован еще раз. Особенности:
-Оболочковые формы можно изготовить по горячей металлической оснастке.
-песчано-смолевые смеси обладают высокой сыпучестью, т.е. повышается точность размеров (8 квалитет Rz=40-80 мкм).-масса отливок 0,5-50 кг.
-эффективность способа, припуски снижаются в 2 раза.
-уменьшается объем механической обработки.
-Уменьшается объем формовочной смеси.
-устраняются трудоёмкие операции выбивки.
Этот способ наиболее рационально применять в условиях серийного производства(не меньше 200 отливок в год)
Недостатки: -работа на горячей оснастке.-утрата точности литейной формы при изготовлении тяжелых заготовок.
10. Литьё по выплавляемым моделям: сущность технологического процесса, технологические возможности, область применения и оснастка.
Сущность метода заключается в использовании неразъемной разовой модели.
При этом перед заливкой расплава, модель удаляется их формы вплавлением, выжиманием, растворением.
Технологический процесс:
Модель или звено модели изготавливают в пресс-форме, рабочая плоскость которой имеет конфигурацию отливки с припуском, на механическую обработку модель изготавливают из материалов, имеющего невысокую температуру плавления(воск, парафин), высокую способность растворяться(карбонит), способность выгорать без образования остатков. Собирают в блоки, имеющие модели литниковой системы и прибыли. Далее блок молей с жидкой формовочной смесью (суспензией) для оболочковых форм на поверхности образуется слой менее 1 мм, оболочку наращивают опылением в 3-10 слоёв, каждый слой просушивается на воздухе, либо в аммиаке. После этого модельный состав выплавляется при 100 градусах, дополнительно прокаливают. После охлаждение и затвердевания керамическая форма разрушается.Процесс обеспечивает гладкую чистую поверхность (8-11 квалитет)припуски от 1.4 мм. Этот процесс обеспечивает максимальный КИМ(85-95%) Из-за улучшения формы можно получить отливки 0,8-2 мм.
Достоинства: - возможность получения отливок любых сплавов, любой конфигурации, тонкостенных.-возможность создания сложных конструкций, объединяющих несколько деталей.-возможность организации как в единичном так и в массовом производстве.-уменьшение расходов формовочных материалов.-уменьшение вредных воздействий.
Недостатки: -Трудоемкость и длительность.-Большое количество факторов, оказывающих влияние на качество отливки.-большая номенклатура материалов для получения формы.Повышенный расход металла на литники.
11. Литьё в металлические формы (кокиль): сущность технологического процесса, технологические возможности, область применения и оснастка.
Кокиль - это металлическая литейная форма, заполняемая расплавом; используется многократно. Состоит из двух полуформ,плиты и вставок. Полуформы взаимно центрируются штырями и их соединяют замками. Параметры кокиля Превышают величину отливки на величину усадки сплава. Стрежни извлекаются из отливки после её затвердевания и охлаждения. Расплав заливают через литниковую систему, а питание осуществляется через прибыли. Удаление газов осуществляется через стенки кокиля. Конструкция кокиля может быть сложной (неразъемные, с горизонтальным, вертикальным и несколькими плоскими разъемами)
Технологический процесс: 1)Подготовка кокиля к работе: поверхность разъема тщательно очищается; проверяется легкость перемещения частей, точность центрования; на плоскость кокиля наносится слой огнеупорного покрытия и краска; кокиля нагревается до рабочей температуры (473-623)
2)Заливка расплава
Особенности взаимодействия кокиля с металлом отливки:
Металлический кокиль обладает большей теплопроводностью, теплоемкость, почти нулевой газопроницаемостью.1)Процесс охлаждения материала отливки идет более интенсивно(получается более мелкозернистая и плотная структура)
2)Гидротекучесть материала уменьшается, т.е. наполняемость формы хуже (не получают более тонкостенные отливки)3) Кокиль практически неподатлив, поэтому возможно обеспечение более высокой точности(12-15 квалитет) но в тоже время это способствует образованию значительных внутренних напряжений(трещины, корабление)4) внутренняя поверхность кокиля покрывается облицовочной смесью, поэтому шероховатость поверхности низкая (8-10 мкм)
Преимущества: -повышение производительности труда (в 2-3 раза).
-снижение расходов на капитальные вложения (увеличение съема отливок 1 ).-повышение качества отливок.-улучшение саниатрано-гигиенических условий.-возможность полной автоматизации и механизации.
Недостатки: -высокая стоимость кокиля, сложность его изготовления.
-образование внутренних напряжений.-сложность получения отливок сложной конфигурации.Применяют в серийном и массовом производстве: минимальная партия более 20 крупных и 400 мелких отливок в год (чугун) 400-700 отливок в год (алюминий).
12. Центробежное литьё: сущность технологического процесса, технологические возможности, область применения и оснастка.
Это способ изготовления отливок, при котором залитый в форму металл подвергается воздействию центровых сил. Применяется вращающие литейные формы, т.е. отливки, только тела вращения. По материалу литейной формы, ограничений нет. Поскольку форма вращается, то используют приводы (чаще всего электрической) такие машины называются центробежными; с горизонтальной и вертикальной осью вращения.
В машинах с горизонтальной осью в основном получают трубы, с вертикальной осью невысокие отливки (диаметр намного больше высоты)
А)ковкиБ)форма со шпинделем ЭД.Расплав (3) под действием центр. сил отбрасывается к стенкам литейных форм и затвердевает.Дает 100% водного выхода.Условия формирования отливки, обусловлены материалом отливки. Число оборотов 1500 со стороны наружной поверхности припуски могут быть меньше, а со стороны внутренней больше.
Преимущества: -отливки обладают большой плотностью в следствии малого наличия пустот.-меньший расход металла из-за отсутствия литниковой системы.-исключение затрат на изготовление стрежней.-Исключение влияния жидкотекучести на заполняемость литейной формы.-возможность изготовления отливок из двух различных сплавов: армированные, наварка расплава, последовательная заливка различных сплавов.
Недостатки: неточность диаметра со стороны свободной поверхности(разностенность по выосте)При армировании в литейную форму вначале устанавливается арматура, которая заливается сплавом другого состава, что понижает износ.При наварке сначала устанавливается металлическая втулка, затем заливается сплав.При последовательной заливке сначала заливается один металла, потом когда он затвердевает, остается только не на внутренних поверхностях, заливается другой металл.
Минимальные припуски на отливки устанавливаются для серого чугуна, далее припуски увеличиваются.
Дата добавления: 2015-12-20; просмотров: 89; Мы поможем в написании вашей работы! |
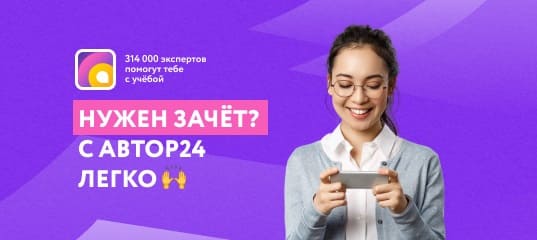
Мы поможем в написании ваших работ!