Механическая обработка деталей резанием.
Это процесс удаления слоя металла с поверхности заготовки для обеспечения требуемых геометрической формы, размеров и шероховатости.
Режимы обработки резанием – это совокупность элементов: глубина резания t, подача s и скорость резания v.
Металлорежущие станки: токарные, сверлильные и расточные, шлифовальные и доводочные, зубо- и резьбообрабатывающие (резьбонарезные), фрезерные, строгальные, долбежные, протяжные, разрезные.
Методы обработки резанием:
Точение – технологический метод обработки поверхностей тел вращения резанием токарными резцами (инструмент) на токарных станках (оборудование) при вращении заготовки (главное движение) и перемещения резца (движение подачи).
Разновидности точения: Обтачивание — обработка наружных поверхностей. Растачивание — обработка внутренних поверхностей. Подрезание — обработка плоских торцевых поверхностей. Резка — разделение заготовки на части. Резьбонарезание.
Сверление – метод получения сквозных и глухих отверстий в сплошном материале. Инструмент – сверло. Обработка производится на сверлильных и токарных станках. Главное движение – вращательное вращение инструмента, подача – поступательное движение инструмента вдоль оси отверстия. Зенкерами обрабатывают просверленные отверстия (зенкерование). Развертками окончательно обрабатывают отверстия (развертывание)
Фрезерование - высокопроизводительный и распространенный метод обработки поверхностей заготовок многолезвийным инструментом – фрезой (б ывают цилиндрические и торцевые). Станки горизонтально-фрезерные и вертикально-фрезерные. На фрезерных станках возможна обработка наклонных поверхностей, уступов, пазов различного профиля, зубчатых и других поверхностей.
|
|
Шлифование - процесс обработки заготовок резанием с помощью абразивных инструментов для получения поверхностей высокой точности и низкой шероховатостью. Шлифование часто применяют для чистовой и отделочной обработки после токарных и фрезерных операций. Слой металла, снимаемый при шлифовании менее 0,3 мм.
Абразивные инструменты выпускают в виде кругов, головок, брусков, сегментов, шлифовальной шкурки. Если шлифование осуществляется шлифовальными кругами и шлифовальными головками, то главным движением являются их вращение, а перемещение относительно детали - движением подачи. Используют круглошлифовальные, плоскошлифовальные, бесцентрово-шлифовальные станки, специальные ленточно-шлифовальные и оптико-шлифовальные, координатно-шлифовальные, резьбошлифовальные станки.
Протягивание - высокопроизводительный метод обработки деталей разнообразных форм, обеспечивающий высокую точность формы и размеров обрабатываемой поверхности. Из-за высокой стоимости инструмента - протяжки, протягивание применяют в крупносерийном производстве. В протяжке каждый режущий зуб больше последующего на определенную величину. Процесс резания при протягивании производится на протяжных вертикального и горизонтального исполнений станках при поступательном движении инструмента относительно неподвижной заготовки за один проход.
|
|
Отверстия различной геометрической формы протягивают на горизонтально- протяжных станках для внутреннего протягивания. Цилиндрические отверстия протягивают после сверления, растачивания или зенкерования. Шпоночные и шлицевые пазы протягивают протяжками, форма которых в поперечном сечении соответствует профилю протягиваемого отверстия. Наружные поверхности различной геометрической формы протягивают на вертикально –протяжных станках для наружного протягивания.
Точение. Сущность процесса, назначение и область применения, применяемое оборудование (станок), инструмент, приспособления, точность размеров и шероховатость обрабатываемой поверхности.
Точение является основным способом обработки поверхностей тел вращения. Процесс резания осуществляется на токарных станках при вращении обрабатываемой заготовки (главное движение) и перемещении резца (движение подачи).
|
|
Главным движением при точении является вращательное движение детали. Движение подачи придается режущему инструменту. Движение подачи осуществляется: параллельно оси вращения заготовки (продольная); перпендикулярно оси вращения заготовки (поперечная); под углом к оси вращения заготовки (наклонная).
С помощью точения выполняют операции: обтачивание - обработку наружных поверхностей, растачивание - обработку внутренних поверхностей, подрезание - обработку торцевых поверхностей, резку - разрезание заготовки на части, резьбонарезание - нарезание резьбы.
Рис.1. Точение: а- обтачивание; б-растачивание; в- подрезание;
г- отрезание; д- нарезание резьбы
По технологическим возможностям точение условно подразделяют на черновое, получистовое, чистовое, тонкое. В качестве режущего инструмента при точении используют резцы. Главным принципом классификации резцов является их технологическое назначение. Различают резцы: проходные - для обтачивания наружных цилиндрических и конических поверхностей; расточные- проходные и упорные – для растачивания глухих и сквозных отверстий; отрезные, резьбовые, фасонные, канавочные. По конструкции резцы бывают цельные; с напаянной пластиной или прикрепленной механически пластиной; сварные. Деталь крепится в патрон или центрах.
|
|
Токарный станок — станок для обработки резанием (точением) заготовок из металлов и др. материалов в виде тел вращения. На токарных станках выполняют обточку и расточку цилиндрических, конических и фасонных поверхностей, нарезание резьбы, подрезку и обработку торцов, сверление, зенкерование и развертывание отверстий и т. д. Заготовка получает вращение от шпинделя, резец перемещается вместе с салазками суппорта от ходового вала или ходового винта, получающих вращение от механизма подачи.
Приспособления станка: станина, на которой монтируются все механизмы станка; передняя (шпиндельная) бабка, в которой размещаются коробка скоростей, шпиндель и другие элементы; коробка подач, передающая с необходимым соотношением движение от шпинделя к суппорту (с помощью ходового винта при нарезании резьбы или ходового валика при обработке других поверхностей); фартук, в котором преобразуется вращение винта или валика в поступательное движение суппорта с инструментом; в пиноли задней бабки может быть установлен центр для поддержки обрабатываемой детали или стержневой инструмент (сверло, развертка и т. п.) для обработки центрального отверстия в детали, закрепленной в патроне; суппорт служит для закрепления режущего инструмента и сообщения ему движений подачи.
При обработке на станках нормальной точности шероховатость обработанных поверхностей обычно находится в пределах Rz 80- Rz5. На специальных станках, при применении алмазного инструмента может быть получена шероховатость поверхности до Ra-0,05мкм.
Токарная обработка позволяет достигать точности при обработке на станках нормального класса точности, в экономически оптимальных условиях - 7-14 квалитет. В настоящее время созданы уникальные токарные станки, обеспечивающие точность обработки менее 0,05мкм (1…2 квалитеты), которые применяются для изготовления элементов информационных накопителей вычислительной техники, изготовления прессформ лазерных носителей информации. Шероховатость поверхности во многом определяется выбранной подачей и геометрическими параметрами вершины резца.
Фрезерование. Сущность процесса, назначение и область применения, применяемое оборудование (станок), инструмент, приспособления, точность размеров и шероховатость обрабатываемой поверхности.
Фрезерование – высокопроизводительный и распространенный метод обработки поверхностей заготовок многолезвийным инструментом - фрезой. Каждый режущий зуб при вращении фрезы врезается в обрабатываемую деталь и осуществляет резание с определенной периодичностью. По исполнению фрезы делятся на цилиндрические, когда зубья расположены только на цилиндрической поверхности, и торцевые, у которых режущие зубья располагаются на и торце и цилиндрической поверхности, дисковые,концевые, угловые, шпоночные, фасонные.
Горизонтальные плоскости фрезеруют на горизонтально-фрезерных станках цилиндрическими фрезами и на вертикально-фрезерных станках - торцовыми фрезами и торцовыми фрезерными головками. Вертикальные плоскости фрезеруют на горизонтально-фрезерных станках торцовыми фрезами и на вертикально-фрезерных станках – концевыми фрезами.
Универсальные фрезерные станки имеют вертикальную и горизонтальные бабки. На фрезерных станках возможна обработка наклонных поверхностей, уступов, пазов различного профиля, зубчатых и других поверхностей. Фрезерные станки с программным управлением позволяют обрабатывать сложные профили по трем координатам одним инструментом.
Обрабатываемые детали закрепляют неподвижно на столе станка чаще всего в специальных приспособлениях или тисках. Фрезы получают вращение от шпинделя станка непосредственно или через оправку.
Станки предназначены для обработки наружных и внутренних поверхностей. Горизонтально- и вертикально-фрезерные станки, продольно-фрезерные (для обработки заготовок большой массы и размеров, типа станин, корпусов, коробок передач), карусельно-фрезерные (заготовки устанавливают и снимают без остановки станка; движение круговой подачи стола), барабанно-фрезерные (наличие барабана с горизонтальной осью вращения), копировально-фрезерные (для обработки поверхностей сложного профиля), многоцелевой станок с ЧПУ (для комплексной обработки корпусных деталей с 4 сторон без переустановки).
При цилиндрическом фрезеровании: 1.Черновое (Ra=50-25мкм; Н14-12), чистовое (Ra=6,3-3,2мкм; Н11-10), тонкое (Ra=1,6-0,8мкм; Н9-8). Режимы резания: V-скорость вращения фрезы, S-подача (величина перемещения заготовки в минуту), t-глубина резания (расстояние между обрабатываемой и обработанной поверхностью), B – ширина фрезерования.
Шлифование. Сущность процесса, назначение и область применения, применяемое оборудование (станок), инструмент, приспособления, точность размеров и шероховатость обрабатываемой поверхности.
Шлифование - процесс обработки заготовок резанием с помощью абразивных инструментов (эльбор, корунд, алмаз) для получения поверхностей высокой точности и низкой шероховатостью. Шлифование часто применяют для чистовой и отделочной обработки после токарных и фрезерных операций. Слой металла, снимаемый при шлифовании менее 0,3 мм.
Абразивные зерна имеют твердость выше обрабатываемого материала. В шлифовальном круге зерна расположены в круге беспорядочно и удерживаются связующим материалом. При вращательном движении круга в зоне его контакта с заготовкой часть зерен срезает материал в виде очень большого числа тонких стружек. Т.к. при обработке сильное тепловое воздействие, то процесс проводят с обильной подачи СОЖ (Смазочная Охлаждающая Жидкость). Шлифование применяют для чистовой и отделочной обработки деталей с высокой точностью (Н=8-6, Ra=1.6-0.8).
Режимы резания: скорость главного движения резания, подача и глубина резания. Если шлифование осуществляется шлифовальными кругами и шлифовальными головками, то главным движением являются их вращение, а перемещение относительно детали - движением подачи.
Инструмент: шлифовальные ленты, круги, головки, шкурки, бруски, диски, сегменты.
Станки: кругло-шлифовальный (для наружного шлифования цилиндрических и конических поверхностей), внутришлифовальный (для получения высокой точности отверстий; возможно шлифование сквозных и глухих, конических отверстий), плоскошлифовальный, бесцентрово-шлифовальный. Для обработки сложных фасонных поверхностей используются специальные ленточно-шлифовальные и оптико-шлифовальные, координатно-шлифовальные, резьбошлифовальные станки.
Различают плоское, круглое и внутреннее шлифование. Плоское шлифование может осуществляться периферией или торцом круга.
Сверление. Сущность процесса, назначение и область применения, применяемое оборудование (станок), инструмент, приспособления, точность размеров и шероховатость обрабатываемой поверхности.
Сверление - основной способ получения сквозных и глухих отверстий в сплошном материале заготовки. В качестве инструмента используется сверло. Обработка производится на сверлильных и токарных станках. На сверлильных станках сверло совершает вращательное движение и продольное вдоль оси отверстия, а заготовка закреплена на столе станка. На токарных станках обрабатываемая деталь закрепляется в патрон и совершает вращательное движение, сверло крепится в заднюю бабку станка и совершает поступательное движение вдоль оси отверстия.
Рис.2. Схемы: а, б - сверления, в – рассверливания,
г-зенкерования, д- развертывания
Диаметр просверливаемого отверстия можно увеличить сверлом большего размера. Такие операции называют рассверливанием. При сверлении обеспечивается сравнительно невысокая точность и качество поверхности.
Для получения отверстий более высокой точности и меньшей шероховатости поверхности выполняются зенкерование и развертывание. Зенкерованием обрабатывают предварительно полученные отверстия многолезвийным инструментом зенкером, который имеет более жесткую рабочую часть. Число зубьев не менее трех.
Развертыванием можно исправить неточности формы отверстия. Развертки - многолезвийный инструмент, срезающий очень тонкие слои с обрабатываемой поверхности.
Назначение сверления: Сверление необходимая операция для получения отверстий в различных материалах при их обработке, целью которой является:
· Изготовление отверстий под нарезание резьбы, зенкерование, развёртывание или растачивание.
· Изготовление отверстий (технологических) для размещения в них электрических кабелей, анкерных болтов, крепёжных элементов и др.
· Отделение (отрезка) заготовок из листов материала.
· Ослабление разрушаемых конструкций.
· Закладка заряда взрывчатого вещества при добыче природного камня.
Операции сверления производятся на следующих станках:
· Вертикально-сверлильные станки.
· Горизонтально-сверлильные станки.
· Вертикально-расточные станки.
· Горизонтально-расточные станки.
· Вертикально-фрезерные станки.
· Горизонтально-фрезерные станки.
· Универсально-фрезерные станки.
· Токарные станки (сверло неподвижно а обрабатываемая заготовка вращается).
· Токарно-затыловочные станки (сверление вспомогательная операция, сверло неподвижно).
Для облегчения процессов резания материалов применяют следующее:
· Охлаждение (вода, эмульсии, олеиновая кислота, углекислый газ, графит).
· Ультразвук (ультразвуковые вибрации сверла увеличивают производительность и дробление стружки).
· Подогрев (ослабляет твёрдость труднообрабатываемых материалов).
· Удар (при ударно-поворотном сверлении (бурении) камня, бетона).
Протягивание. Сущность процесса, назначение и область применения, применяемое оборудование (станок), инструмент, приспособления, точность размеров и шероховатость обрабатываемой поверхности.
Протягивание - высокопроизводительный метод обработки деталей разнообразных форм, обеспечивающим высокую точность формы и размеров обрабатываемой поверхности. Из-за высокой стоимости инструмента - протяжки, протягивание применяют в крупносерийном производстве. В протяжке каждый режущий зуб больше последующего на определенную величину. Процесс резания при протягивании производится на протяжных вертикального и горизонтального исполнений станках при поступательном движении инструмента относительно неподвижной заготовки за один проход.
Отверстия различной геометрической формы протягивают на горизонтально-протяжных станках для внутреннего протягивания. Размеры отверстий от 5 до 250 мм.
Рис. 6. Схемы протягирания: 1-обрабатываемая деталь,2 – протяжка;
а…д- внутреннее протягивание;
з…ж- наружнее протягивание
Цилиндрические отверстия протягивают после сверления, растачивания или зенкерования. Шпоночные и шлицевые пазы протягивают протяжками, форма которых в поперечном сечении соответствует профилю протягиваемого отверстия.
Наружные поверхности различной геометрической формы протягивают на вертикально-протяжных станках для наружного протягивания.
Протягивание применяется в крупносерийном и массовом производстве металлоизделий, и редко в мелкосерийном и единичном. Протяжки различных конструкций — наружные, внутренние, и дорны, являются одними из наиболее дорогих инструментов для выполнения металлообработки. Подчас каждая протяжка при своем изготовлении требует наивысшей точности и правильного расчета. Это обусловлено тем, что инструмент при протягивании работает в наиболее тяжёлых и суровых условиях огромных нагрузок (растяжение, сжатие, изгиб, абразивное и адгезионное выкрашивание лезвий протяжки). Протягиванию предшествуют подготовительные операции металлообработки, такие как сверление, зенкерование, развертывание, вырубка (т. е. для проведения протягивания требуется достаточно точно обработанная поверхность заготовки).
Дорнование (дорнирование) – вид обработки заготовок без снятия стружки. Сущность дорнования сводится к перемещению в отверстии заготовки с натягом жёсткого инструмента – дорна. Размеры поперечного сечения инструмента больше размеров поперечного сечения отверстия заготовки на величину натяга.
Станки для протягивания:
· Горизонтально-протяжные станки: Все виды внутреннего и наружного протягивания заготовок.
· Пресса: Обработка отверстий дорнами (прошивка, формообразование, калибровка).
Виды протягивания:
Внутреннее протягивание. Наружное протягивание. Дорнование. Накаливание.
Дата добавления: 2015-12-18; просмотров: 15; Мы поможем в написании вашей работы! |
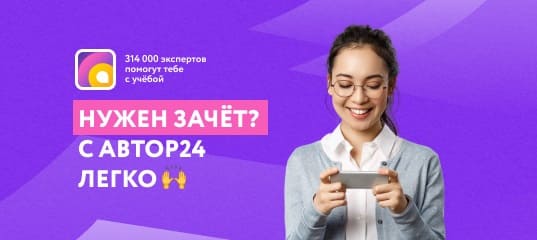
Мы поможем в написании ваших работ!