Метод определения растяжимости
Сущность метода определения растяжимости (дуктильности) битума заключается в определении максимальной длины, на которую может растянуться без разрыва битум, залитый в специальную форму, раздвигаемую с постоянной скоростью при заданной температуре.
В основу используемого для этих целей прибора лег дуктилометр, предложенный Доу в 1903 году. В 1909 году прибор был усовершенствован Смитом.
Применение дуктилометра при испытаниях битумов было введено в стандарты США в 1926 году, Германии и Англии в 1929 году. В СССР метод был стандартизирован в 1931 году.
Данный метод изложен в ГОСТ 11505 «Битумы нефтяные. Метод определения растяжимости».
Применяемые в настоящее время дуктилометры имеют тот же принцип действия, что и дуктилометр Доу - Смита. Наличию большого количества разновидностей данного прибора способствует то обстоятельство, что в ГОСТ 11505 «Битумы нефтяные. Метод определения растяжимости» дается лишь краткое описание дуктилометра, а нормативный документ на сам дуктилометр отсутствует.
В соответствии с ГОСТ 11505 дуктилометр состоит из пластмассового или деревянного ящика (ванны), выложенного изнутри оцинкованной жестью или эмалью. Внутри ванны через всю длину проходит червячный винт с салазками, поступательное движение которых обеспечивается движением винта. На одной стороне прибора укреплена стойка с тремя штифтами соответственно трем штифтам, имеющимся на салазках. На салазках имеется указатель - стрелка, передвигающаяся при движении салазок вдоль линейки. Червячный винт приводится в движение от мотора. Скорость салазок должна быть 5 см/мин. Общий вид дуктилометра приведен на рис. 4.4.
|
|
Рисунок 4.4
1 – линейка, 2 – подвижная каретка, 3 – неподвижная каретка,
4 – форма «восьмерка»
Помимо дуктилометра при испытании используют следующие аппаратуру и материалы:
- формы латунные для битума – «восьмерки»;
- термометр ртутный стеклянный по ГОСТ 215, с интервалом измеряемых температур 0-50ОС, с ценой деления шкалы 0,5ОС;
- нож для среза битума с прямым лезвием;
- сито с металлической сеткой № 07 по ГОСТ 6613;
- пластинка полированная металлическая или термостойкая стеклянная;
- тальк;
- глицерин по ГОСТ 6823 или по ГОСТ 6259;
- соль поваренная пищевая по ГОСТ 13830;
- декстрин по ГОСТ 6034;
- спирт этиловый ректификованный технический по ГОСТ 18300 или спирт этиловый технический по ГОСТ 17299;
- бумага папиросная по ГОСТ 3479.
Перед испытанием битум обезвоживают осторожным нагреванием без перегрева до температуры на 80 - 100ОС выше температуры размягчения, но не выше 160ОС для дорожных битумов.
Затем битум процеживают через металлическое сито и тщательно перемешивают до полного удаления пузырьков воздуха.
|
|
После этого осуществляют заливку битума в специальную форму – «восьмерку» (рис. 1.5). Перед этим полированную металлическую или стеклянную пластинку и внутренние боковые стенки вкладышей «восьмерки» смазывают смесью талька с глицерином (1: 3) или смесью декстрина с глицерином (1: 2), после чего собирают форму на пластинке.
Битум наливают в три формы тонкой струей от одного конца формы до другого, пока она не наполнится выше краев. После остывания излишек битума срезают горячим острым ножом от середины к краям так, чтобы битум заполнял формы вровень с их краями.
Формы с битумом, не снимая с пластинки, помещают в водяную ванну (можно в ванну дуктилометра), поддерживая в ней температуру испытания добавлением горячей или холодной воды или льда. При определении растяжимости при 25ОС температура должна быть (25 ± 0,5), а при определении растяжимости при 0ОС температура воды поддерживается (0 + 0,5)ОС.
Через 1 час формы с битумом вынимают из воды, снимают с пластинки и закрепляют в дуктилометре. Затем снимают боковые части формы и включают мотор дуктилометра. Скорость растяжения должна быть 5 см/мин.
|
|
Допускается при определении рястяжимости битума при 0ОС устанавливать перегородку в середине ванны дуктилометра. Это делается для уменьшения объема жидкости, который необходимо охладить до 0ОС. Для этой цели используют снег или лед. В летний период возникают проблемы с обеспечением лабораторий необходимым количеством льда, так как получаемого с помощью бытовых холодильников льда для этих целей недостаточно. При установлении перегородки в середине ванны, объем охлаждаемой жидкости уменьшается в два раза. По условиям испытания уменьшение рабочей длины ванны допустимо, так как растяжимость битумов при 0ОС во много раз меньше, чем при 25ОС.
При определении растяжимости битумов, имеющих плотность значительно больше или меньше воды нити битума опускаются до дна или всплывают на поверхность воды, что приводит к искажению результатов испытаний. Для предотвращения этого явления плотность воды изменяют добавлением раствора поваренной соли или глицерина (для увеличения плотности) и этилового спирта (для уменьшения плотности).
За растяжимость битума принимают длину нити битума в сантиметрах, отмеченную указателем в момент ее разрыва. Для каждого образца проводят три определения. За результат принимают среднее арифметическое значение трех параллельных определений.
|
|
При растяжимости битума до 10 см результат округляют до 0,1 см, при значении растяжимости больше 10 см, результат округляют до целого числа.
Требования к сходимости и воспроизводимости метода приведены в таблице 4.21
Таблица 4.21
Растяжимость при 25ОС | Сходимость, % от среднего результата | Воспроизводимость, % от среднего результата |
от 0 до 30 | ||
свыше 30 |
Метод определения температуры хрупкости
Данное испытание нормировано в ГОСТ 11507 «Метод определения температуры хрупкости по Фраасу», который распространяется на нефтяные битумы и устанавливает метод определения температуры хрупкости по Фраасу. Сущность метода заключается в охлаждении и периодическом изгибе образца битума и определении температуры, при которой в образце битума появляются трещины или он ломается. В ходе испытаний применяют следующие аппаратуру, реактивы и материалы:
- аппарат Фрааса, (рис. 4.5) в который входят:
- устройство для сгибания пластинки, состоящее из двух концентрических трубок из теплоизоляционного материала, и приспособления для перемещения внутренней трубки относительно внешней трубки. Зазор между трубками не должен превышать 1 мм. На нижних концах трубок жестко укреплены захваты с пазами. Часть внутренней трубки, находящаяся между захватами, имеет четыре продольные прорези (размером 30 ´ 4 мм), устраняющие экранирование резервуара термометра (или термопары). При перемещении внутренней трубки расстояние между пазами захватов должно равномерно уменьшаться до (36,5 ± 0,1) мм от максимального расстояния 40 ± 0,1 мм за 10 - 12 с;
- приспособление для перемещения внутренней трубки состоит из конуса или двух клиньев, по поверхности которых движется шифт, соединенный с внутренней трубкой. Приспособление приводится в действие вращением рукоятки или автоматически;
- пластинки стальные длиной 41 ± 0,05 мм, шириной (20 ± 0,2) мм и толщиной (0,15 ± 0,02) мм, изготовленные из стальной ленты 65Г-Ш-С-Н-0,15±20 по ГОСТ 2283. В напряженном состоянии пластинки должны быть плоскими. Не допускается применять пластинки со следами коррозии;
- пробирка стеклянная диаметром 37±1 мм, высотой около 210 мм, в которую вставляется изгибающее устройство;
- устройство для охлаждения, состоящее из несеребреного сосуда Дьюара, снабженного резиновой пробкой с прорезями для пробирки с изгибающим устройством для подачи охлаждающего агента (воронка для подачи углекислоты или трубка для подачи газообразного азота), и отводящей трубки. Вместо сосуда Дьюара может быть использована широкая пробирка, которая укрепляется при помощи пробки в стакане. на дно пробирки и стакана помещают небольшое количество хлористого кальция или другого осушителя. Допускается применять аппарат другой конструкции, по основным размерам рабочей части, условиям проведения и результатам испытаний соответствующий аппарату Фрааса.
Рисунок 4.5
1 – сосуд Дьюара, 2 – пластинка, 3 – пробирка,
4 – устройство для сгибания пластинки, 5 – термометр,
а) начальной положение пластинки, б) конечное положение пластинки
Термометр ртутный стеклянный с длиной погружаемой части 250-260 мм, диаметром не более 5 ± 0,5 мм, ртутным резервуаром цилиндрической формы длиной 15-20 мм, с диапазоном измерения от минус 35 до плюс 30ОС, ценой деления 1ОС и погрешностью ±0,5ОС или термопара хромель-копелевая малоинерционная с длиной погружаемой части не менее 250 мм, с потенциометром класса точности 0,5 с диапазоном измерения от минус 50 до плюс 50ОС и ценой деления 1ОС;
Устройство для расплавления битума на пластинке, состоящее из двух металлических плиток любой формы (60´60 мм), расположенных друг над другом на расстоянии примерно 50 мм. Верхняя плитка толщиной 5 мм, нижняя - отражатель толщиной 1 - 2 мм. Устройство закрепляется на штативе горизонтально. Для расплавления битума допускается устройство другой конструкции, обеспечивающей отсутствие перегрева битума и равномерное распределение его на пластинке, например, электрическая плитка с горизонтальной качающейся поверхностью, или магнитный блок, состоящий из плоскошлифиванной магнитной стальной пластины размером 40 ´ 60 ´ 8 мм, обеспечивающей полное соприкосновение всей поверхности пластинки для испытания при расплавлении битума, и электрической плитки с устройством, обеспечивающим горизонтальность поверхности, а также;
- секундомер;
- сито с металлической сеткой № 07 по ГОСТ 6613. Допускается применять импортные сита с аналогичными размерами сетки;
- плитка керамическая размером 100´100´5 мм для выдерживания пластинок после расплавления битума;
- кальций хлористый технический по ГОСТ 450;
- толуол нефтяной по ГОСТ 14710 или толуол каменноугольный по ГОСТ 9880, или керосин осветительный;
- охлаждающая смесь: этиловый технический регенерированный спирт или сырец или технический изооктан с твердой углекислотой; жидкий азот или жидкая углекислота. Допускается использовать другие охлаждающие смеси;
- весы лабораторные 3-го класса точности;
- держатель для помещения пластинок в пазы захватов. Ширина концов держателя не должна превышать 8 мм. Он должен быть снабжен устройством, предотвращающим сближение концов на расстояние менее 38 мм.
Перед началом испытаний образец битума при наличии влаги обезвоживают осторожным нагреванием до температуры на 80 - 100ОС выше температуры размягчения, но не ниже 120ОС и не выше 180ОС. Обезвоженный и расплавленный до подвижного состояния битум процеживают через металлическое сито.
Две стальные пластинки промывают толуолом или керосином, высушивают и взвешивают с погрешностью не более 0,01 г.
Вручную устанавливают, в какую сторону изгибается стальная пластинка и наносят (0,40 ± 0,01) г битума на выпуклую при изгибе сторону пластинки.
Пластинку с навеской битума кладут на верхнюю плитку устройства для расплавления битума и осторожно нагревают, пока битум не растечется равномерно по поверхности пластинки. Время расплавления и распределения битума составляет 5 - 10 мин.
Защищенные от пыли пластинки с битумом выдерживают при комнатной температуре не менее 30 мин.
Затем пластинку вставляют в захваты устройства для сгибания (при расстоянии между пазами захватов 40,0 ± 0,1 мм) таким образом, чтобы битумный слой был расположен наружу. Если при установке пластинки битумный слой треснул, то в устройство для сгибания помещают другую пластинку с битумным покрытием.
Собирают устройство для охлаждения и сосуд Дюара заполняют изоктаном или спиртом, примерно на 1/2 высоты.
Устройство для сгибания пластинки вставляют в стеклянную пробирку с небольшим количеством хлористого кальция. Термометр или термопара устанавливаются так, чтобы ртутный резервуар термометра или рабочий конец термопары находились на уровне середины стальной пластинки. Температура в пробирке к началу испытаний не должна быть ниже 15ОС.
Порциями вводят охлаждающий агент и понижают температуру в пробирке со скоростью 1ОС/мин, при этом допускаемые отклонения не должны превышать ± 1ОС за 10 мин.
Сгибать пластинку начинают при температуре примерно на 10ОС выше ожидаемой температуры хрупкости.
Сгибают и распрямляют пластинку равномерным вращением рукоятки со скоростью около 1 об/сек сначала в одну сторону до достижения максимального прогиба пластинки (при уменьшении расстояния между пазами захватов до (36,5 ± 0,1) мм), а затем в обратную сторону до исходного положения.
Процесс сгибания и распрямления пластинки должен проходить за 20 - 24 с. Операцию повторяют в начале каждой минуты и отмечают температуру, при которой появляется первая трещина.
В ходе испытания устройство для сгибания нельзя вынимать из пробирки.
Аналогичные испытания проводят с другой пластинкой с битумом, начиная сгибать пластинку при температуре на 10ОС выше температуры появления трещины на первой пластинке.
В случае расхождения между двумя испытаниями на величину более 3ОС, проводят третье определение.
Время с момента нанесения битумного покрытия до конца испытания не должно превышать 4 ч.
За температуру хрупкости принимают среднее арифметическое значение двух определений.
Допустимые значения сходимости и воспроизводимости принимают равными 3 и 8ОС соответственно.
Изменение температуры размягчения после прогрева
Определение данной характеристики битумов направлено на оценку его стабильности в ходе длительного хранения при повышенной температуре, т.е. устойчивости к старению.
Отметим, что старение битума, обусловленное необратимыми изменениями в составе и свойствах битума, вызвано следующими факторами [ ]:
- испарением летучих составляющих, происходящим в поверхностном слое битума незначительной толщины и зависящим от содержания в битуме легколетучих компонентов, вязкости битума и температуры;
- полимеризацией, связанной с воздействием тепла, даже в отсутствие кислорода. Степень полимеризации определяется температурой и временем нагрева и ее роль для битумов обычно невелика;
- оксиполимеризацией компонентов битума, происходящей главным образом на внешней поверхности вяжущего, непосредственно подвергнутой воздействию света и ультрафиолетовых лучей;
- полиоксиконденсацией, происходящей под влиянием кислорода, являющейся основным процессом, изменяющим состав и структуру битума при старении.
Оценить количественно протекающие в битуме в ходе старения химические процессы достаточно сложно, а в условиях строительной лаборатории практически невозможно.
Поэтому для установления степени стабильности битума при длительном нагреве был выбран критерий изменения одного из его свойств после теплового воздействия, - температуры размягчения.
В соответствии с п. 3.3 ГОСТ 22245 «Битумы нефтяные дорожные вязкие. Технические условия» изменение температуры размягчения после прогрева вычисляют как разность температур размягчения, определенных по ГОСТ 11506 «Битумы нефтяные. Метод определения температуры размягчения по кольцу и шару» до и после испытания на прогрев по ГОСТ 18180 «Битумы нефтяные. Метод определения изменения массы после прогрева».
ГОСТ 18180 «Битумы нефтяные. Метод определения изменения массы после прогрева» регламентирует процедуру длительного прогрева битума и определения после этого изменения в его массе.
Обсуждая непосредственно определение изменения массы битума после прогрева, отметим, что после прогрева масса образца может как уменьшаться, так и возрастать в зависимости от того, какие факторы будут преобладать, - уменьшения массы вследствие испарения летучих компонентов или ее увеличения за счет окисления воздухом.
Поэтому данное испытание нельзя считать напрямую однозначно характеризующим устойчивость битума к старению. Скорее его можно характеризовать как подготовительное для определения изменения после прогрева других характеристик битума. Так, для вязких дорожных битумов нормируется допустимая величина изменения температуры размягчения после прогрева по ГОСТ 18180.
Метод изменения массы после прогрева
В соответствии с ГОСТ 18180 «Битумы нефтяные. Метод определения изменения массы после прогрева» для испытаний применяют следующую аппаратуру:
- чашки металлические цилиндрические с плоским дном, внутренним диаметром (128 ± 1) мм, высотой (15 ± 0,5) мм или чашки стеклянные типа ЧБН по ГОСТ 10973-75 с наружным диаметром (100 ± 1) мм;
- шкаф сушильный с терморегулятором, поддерживающим температуру с погрешностью не более ±1ОС;
- сито металлическое с сеткой № 07 по ГОСТ 3584;
- термометр стеклянный технический исполнения П с ценой деления 1ОС, до 200ОС по ГОСТ 2823 или лабораторный ТЛ - 2 с ценой деления 1ОС, до 250ОС по ГОСТ 215;
- эксикатор по ГОСТ 6371;
- весы лабораторные технические с погрешностью взвешивания не более 0,01г.
Испытания проводятся следующим образом.
Пробу битума обезвоживают нагреванием до температуры на 80 - 100ОС выше температуры размягчения, но не ниже 125ОС и не выше 180ОС, перемешивая стеклянной палочкой. После этого его процеживают через металлическое сито и перемешивают до полного удаления пузырьков воздуха.
Тщательно вымытые чашки не менее чем на 30 мин помещают в сушильный шкаф при (105 ± 1)ОС. Затем чашки охлаждают в эксикаторе до комнатной температуры и взвешивают с погрешностью не более 0,01 г.
Битум наливают не менее чем в две чашки (в металлические по (50 ± 0,1) г, в стеклянные по (28 ± 0,1) г в каждую) и при осторожном наклоне чашки распределяют его по дну равномерным слоем (около 4 мм).
После охлаждения битума до комнатной температуры в эксикаторе пробы взвешивают с погрешностью не более 0,01 г. Затем пробы горизонтально устанавливают в сушильный шкаф предварительно нагретый до (163 ± 1)ОС. Во время испытаний сушильный шкаф не открывают. Прогрев битума продолжается 5 часов.
После истечения 5 ч прогрева чашки с битумом вынимают из сушильного шкафа, устанавливают в эксикаторе и после охлаждения до комнатной температуры взвешивают с погрешностью не более 0,1 г.
Для определения изменения свойств битума после прогрева содержимое чашек расплавляют в сушильном шкафу при 163ОС и после перемешивания определяют показатели, предусмотренные в технических требованиях.
Изменение массы битума после прогрева (Х) в процентах вычисляют по формуле:
(m - m1) · 100
х = ------------------
m
где m - масса битума до прогрева, г;
m1 - масса битума после прогрева, г.
За результат испытания принимают среднее арифметическое значение двух параллельных определений.
Требования к сходимости и воспроизводимости метода приведены в таблице 4.21:
Таблица 4.21
Изменение массы, % | Сходимость, % | Воспроизводимость, % |
До 0,2 | 0,05 | 0,10 |
свыше 0,2 до 1,0 | 0,10 | 0,15 |
свыше 1,0 | 0,15 | 0,30 |
Индекс пенетрации
Индекс пенетрации является величиной, рассчитываемой по значениям глубины проникания иглы при 25ОС и температуры размягчения.
Для удобства в приложении 2 ГОСТ 22245 «Битумы нефтяные дорожные вязкие. Технические условия» приведена таблица, по которой определяют значения индекса пенетрации (табл. 4.22).
Таблица 4.22
Темп. | Индекс пенетрации при глубине проникания иглы при 25ОС | |||||||||||||||||
разм. ОС | ||||||||||||||||||
-2,6 | -2,7 | -2,8 | -2,9 | -3,0 | - | - | - | - | - | - | - | - | - | - | - | - | - | |
-1,8 | -1,9 | -2,0 | -2,1 | -2,2 | -2,3 | -2,4 | -2,5 | -2,6 | -2,7 | -2,8 | -2,9 | -3,0 | - | - | - | - | ||
-1,1 | -1,2 | -1,3 | -1,4 | -1,5 | -1,6 | -1,7 | -1,8 | -1,9 | -2,0 | -2,1 | -2,2 | -2,3 | -2,4 | -2,5 | -2,6 | -2,7 | -2,8 | |
-0,4 | -0,5 | -0,6 | -0,7 | -0,8 | -1,0 | -1,1 | -1,2 | -1,3 | -1,4 | -1,5 | -1,6 | -1,7 | -1,8 | -1,9 | -2,0 | -2,1 | -2,2 | |
+0,2 | +0,1 | 0,0 | -0,1 | -0,2 | -0,3 | -0,4 | -0,6 | -0,7 | -0,8 | -0,9 | -1,0 | -1,1 | -1,2 | -1,3 | -1,4 | -1,5 | -1,6 | |
+0,8 | +0,7 | +0,6 | +0,5 | +0,3 | +0,2 | +0,1 | 0,0 | -0,1 | -0,2 | -0,3 | -0,4 | -0,6 | -0,7 | -0,8 | -0,9 | -1,0 | -1,1 | |
+1,4 | +1,2 | +1,1 | +1,0 | +0,9 | +0,8 | +0,6 | +0,5 | +0,4 | +0,3 | +0,2 | +0,1 | 0,0 | -0,2 | -0,3 | -0,4 | -0,5 | -0,6 | |
+2,0 | +1,8 | +1,7 | +1,5 | +1,4 | +1,3 | +1,2 | +1,1 | +0,9 | +0,8 | +0,7 | +0,6 | +0,5 | +0,3 | +0,2 | +0,1 | 0,0 | -0,1 | |
+2,4 | +2,3 | +2,2 | +2,1 | +1,9 | +1,8 | +1,7 | +1,5 | +1,4 | +1,3 | +1,2 | +1,1 | +1,0 | +0,8 | +0,7 | +0,6 | +0,5 | +0,3 | |
+2,9 | +2,8 | +2,6 | +2,5 | +2,4 | +2,3 | +2,2 | +2,0 | +1,9 | +1,8 | +1,6 | +1,5 | +1,4 | +1,3 | +1,2 | +1,0 | +0,9 | +0,8 | |
- | - | - | +2,9 | +2,8 | +2,7 | +2,6 | +2,5 | +2,3 | +2,2 | +2,1 | +2,0 | +1,8 | +1,7 | +1,6 | +1,5 | +1,3 | +1,2 | |
- | - | - | - | - | - | - | +2,9 | +2,7 | +2,6 | +2,5 | +2,4 | +2,3 | +2,1 | +2,0 | +1,9 | +1,7 | +1,6 | |
- | - | - | - | - | - | - | - | - | - | +2,9 | +2,8 | +2,6 | +2,5 | +2,4 | +2,2 | +2,1 | +2,0 | |
- | - | - | - | - | - | - | - | - | - | - | - | - | +2,9 | +2,8 | +2,6 | +2,5 | +2,4 | |
- | - | - | - | - | - | - | - | - | - | - | - | - | - | - | -- | +2,8 | +2,7 | |
Темп. | Индекс пенетрации при глубине проникания иглы при 25ОС | |||||||||||||||||
разм. ОС | ||||||||||||||||||
-2,3 | -2,4 | -2,5 | -2,6 | - | - | - | - | - | - | - | - | - | - | - | - | - | - | |
-1,8 | -1,9 | -2,0 | -2,1 | -2,2 | -2,3 | -2,4 | -2,5 | -2,6 | - | - | - | - | - | - | - | - | - | |
-1,2 | -1,3 | -1,4 | -1,5 | -1,7 | -1,8 | -1,9 | -2,0 | -2,1 | -2,2 | -2,3 | -2,4 | - | - | - | - | - | - | |
-0,7 | -0,8 | -1,0 | -1,1 | -1,2 | -1,3 | -1,4 | -1,5 | -1,6 | -1,7 | -1,9 | -2,0 | -2,1 | -2,2 | -2,3 | -2,4 | - | - | |
-0,2 | -0,4 | -0,5 | -0,6 | -0,7 | -0,8 | -0,9 | -1,1 | -1,2 | -1,3 | -1,4 | -1,5 | -1,7 | -1,8 | -1,9 | -2,0 | -2,1 | -2,3 | |
+0,2 | +0,1 | 0,0 | -0,1 | -0,3 | -0,4 | -0,5 | -0,6 | -0,7 | -0,9 | -1,0 | -1,1 | -1,2 | -1,4 | -1,5 | -1,6 | -1,7 | -1,9 | |
+0,6 | +0,5 | +0,4 | +0,3 | +0,2 | 0,0 | -0,1 | -0,2 | -0,3 | -0,4 | -0,6 | -0,7 | -0,8 | -1,0 | -1,1 | -1,2 | -1,3 | -1,5 | |
+1,1 | +0,9 | +0,8 | +0,7 | +0,6 | +0,5 | +0,3 | +0,2 | +0,1 | -0,1 | -0,2 | -0,3 | -0,4 | -0,6 | -0,7 | -0,8 | -1,0 | -1,1 | |
+1,5 | +1,4 | +1,2 | +1,1 | +1,0 | +0,8 | +0,7 | +0,6 | +0,5 | +0,3 | +0,2 | +0,1 | -0,1 | -0,2 | -0,3 | -0,5 | -0,6 | -0,7 | |
+1,9 | +1,7 | +1,6 | +1,5 | +1,4 | +1,2 | +1,1 | +0,9 | +0,8 | +0,7 | +0,6 | +0,4 | +0,3 | +0,2 | 0,0 | -1,0 | -0,3 | -0,4 | |
+2,3 | +2,1 | +2,0 | +1,9 | +1,7 | +1,6 | +1,5 | +1,3 | +1,2 | +1,1 | +0,9 | +0,8 | +0,6 | +0,5 | +0,4 | +0,2 | +0,1 | -0,1 | |
+2,6 | +2,5 | +2,4 | +2,2 | +2,1 | +2,0 | +1,8 | +1,7 | +1,5 | +1,4 | +1,2 | +1,1 | +1,0 | +0,8 | +0,7 | +0,6 | +0,4 | +0,3 | |
- | +2,8 | +2,7 | +2,6 | +2,4 | +2,3 | +2,2 | +2,0 | +1,9 | +1,7 | +1,6 | +1,5 | +1,3 | +1,2 | +1,0 | +0,9 | +0,8 | +0,6 | |
- | - | - | - | +2,7 | +2,6 | +2,5 | +2,3 | +2,2 | +2,0 | +1,9 | +1,8 | +1,6 | +1,5 | +1,3 | +1,2 | +1,0 | +0,9 | |
- | - | - | - | - | - | +2,8 | +2,6 | +2,5 | +2,3 | +2,2 | +2,0 | +1,9 | +1,8 | +1,6 | +1,5 | +1,3 | +1,2 | |
- | - | - | - | - | - | - | - | +2,8 | +2,7 | +2,5 | +2,3 | +2,2 | +2,1 | +2,0 | +1,8 | +1,6 | +1,5 | |
- | - | - | - | - | - | - | - | - | - | +2,8 | +2,7 | +2,5 | +2,3 | +2,2 | +2,1 | +1,9 | +1,8 | |
- | - | - | - | - | - | - | - | - | - | - | - | - | +2,7 | +2,5 | +2,4 | +2,2 | +2,1 | |
Темп. | Индекс пенетрации при глубине проникания иглы при 25ОС | |||||||||||||||||
разм. ОС | ||||||||||||||||||
-2,4 | - | - | - | - | - | - | - | - | - | - | - | - | - | - | - | - | ||
-2,0 | -2,1 | -2,2 | -2,4 | - | - | - | - | - | - | - | - | - | - | - | - | - | ||
-1,6 | -1,7 | -1,8 | -2,0 | -2,1 | -2,3 | - | - | - | - | - | - | - | - | - | - | - | ||
-1,2 | -1,4 | -1,5 | -1,6 | -1,8 | -1,9 | -2,1 | -2,2 | - | - | - | - | - | - | - | - | - | ||
-0,9 | -1,0 | -1,1 | -1,3 | -1,4 | -1,6 | -1,7 | -1,9 | -2,1 | -2,2 | - | - | - | - | - | - | - | ||
-0,5 | -0,7 | -0,8 | -1,0 | -1,1 | -1,3 | -1,4 | -1,6 | -1,7 | -1,9 | -2,1 | - | - | - | - | - | - | ||
-0,2 | -0,3 | -0,4 | -0,6 | -0,8 | -1,0 | -1,1 | -1,2 | -1,4 | -1,6 | -1,8 | -2,0 | -2,1 | - | - | - | - | ||
+0,1 | 0,0 | -0,1 | -0,3 | -0,5 | -0,6 | -0,8 | -1,0 | -1,1 | -1,3 | -1,5 | -1,7 | -1,8 | -2,0 | - | - | - | ||
+0,5 | +0,3 | +0,2 | 0,0 | -0,2 | -0,3 | -0,5 | -0,6 | -0,8 | -1,0 | -1,2 | -1,4 | -1,6 | -1,8 | -2,0 | - | - | ||
+0,8 | +0,6 | +0,5 | +0,3 | +0,1 | 0,0 | -0,2 | -0,4 | -0,5 | -0,7 | -0,9 | -1,1 | -1,3 | -1,5 | -1,7 | -1,9 | - | ||
+1,0 | +0,9 | +0,8 | +0,6 | +0,4 | +0,2 | 0,0 | -0,1 | -0,3 | -0,4 | -0,6 | -0,8 | -1,0 | -1,2 | -1,4 | -1,7 | -1,9 | ||
+1,3 | +1,2 | +1,1 | +0,9 | +0,7 | +0,5 | +0,3 | +0,2 | 0,0 | -0,2 | -0,4 | -0,6 | -0,8 | -1,0 | -1,2 | -1,4 | -1,7 | ||
+1,7 | +1,5 | +1,4 | +1,1 | +1,0 | +0,8 | +0,6 | +0,5 | 0,3 | +0,1 | -0,1 | -0,3 | -0,5 | -0,7 | -0,9 | -1,2 | -1,4 | ||
+1,9 | +1,7 | +1,6 | +1,4 | +1,2 | +1,0 | +0,9 | +0,7 | +0,5 | +0,3 | +0,1 | -0,1 | -0,2 | -0,5 | -0,7 | -1,0 | -1,2 | ||
- | - | - | +1,7 | +1,5 | +1,3 | +1,2 | +1,0 | +0,8 | +0,6 | +0,4 | +0,2 | 0,0 | -0,3 | -0,5 | -0,7 | -0,9 | ||
- | - | - | - | - | +1,5 | +1,4 | +1,2 | +1,0 | +0,8 | +0,6 | +0,4 | +0,2 | 0,0 | -0,2 | -0,5 | -0,7 | ||
- | - | - | - | - | - | - | +1,5 | +1,2 | +1,1 | +0,9 | +0,6 | +0,4 | +0,2 | 0,0 | -0,3 | -0,5 | ||
- | - | - | - | - | - | - | - | +1,5 | +1,3 | +1,1 | +0,9 | +0,7 | +0,4 | +0,2 | -0,1 | -0,3 | ||
- | - | - | - | - | - | - | - | - | +1,5 | +1,3 | +1,1 | +0,9 | +0,6 | +0,4 | +0,2 | -0,1 | ||
- | - | - | - | - | - | - | - | - | - | - | +1,3 | +1,1 | +0,9 | +0,6 | +0,4 | +0,1 | ||
- | - | - | - | - | - | - | - | - | - | - | +1,5 | +1,3 | +1,1 | +0,8 | +0,6 | +0,3 | ||
- | - | - | - | - | - | - | - | - | - | - | +1,7 | +1,5 | +1,3 | +1,0 | +0,8 | +0,5 |
При промежуточных значениях глубины проникания иглы при 25ОС индекс пенетрации определяют интерполяцией или по формуле:
30
И.П. = ------------- - 10
1 + 50 А
2,9031 - logП
где А = ----------------
Т - 25
П - глубина проникания иглы при 25ОС, 0,1 мм
Т - температура размягчения, ОС.
4.3.2 Испытания жидких битумов
Как уже отмечалось в п. 1.1 главным отличием в методиках оценки свойств жидких и вязких битумов являются принципиально разные методы определения их вязкости.
Метод определения условной вязкости
Сущность метода заключается в измерении времени, в течение которого определенное количество битума протекает через калиброванное отверстие цилиндра при заданной температуре.
Метод регламентирован ГОСТ 11503 «Битумы нефтяные. Метод определения условной вязкости», распространяется на нефтяные жидкие битумы, сырье для битумного производства и другие битуминозные продукты (далее битумы).
Наиболее часто для проведения испытания используют аппарат ВУБ -1 (рис. 4.6).
Рисунок 4.6
а) общий вид, б) стакан вискозиметра, в) сменное донышко,
г) шаровидная пробка, 1 – водяная баня, 2 – крышка, 3 – стакан вискозиметра, 4 – штифт пробки, 5 – крыльчатка для перемешивания воды, 6 – кран, 7 – сменное донышко, 8 – шарик пробки, 9 – мерный цилиндр, 10 – газовая горелка, 11 – подогреваемый отросток водяной бани
Перед испытанием пробу жидкого битума, нагретого до подвижного состояния (но не выше 60ОС), при необходимости обезвоживают фильтрованием через слой толщиной 15 - 20 мм крупнокристаллической свежепрокаленной поваренной соли или хлористого кальция.
Затем продукт процеживают через сито и тщательно перемешивают до полного удаления пузырьков воздуха.
Аппарат устанавливают горизонтально с помощью установочных винтов.
Внутреннюю поверхность цилиндра аппарата и затвора тщательно промывают бензином или другим растворителем и просушивают.
Сточное отверстие рабочего цилиндра закрывают затвором и подставляют под него мерный цилиндр. Баню аппарата наполняют водой, нагретой на 1 - 2ОС выше температуры испытания. Температуру воды поддерживают нагреванием ее с помощью мешалки.
Битум, нагретый на 2 - 3ОС выше температуры испытания, заливают в рабочий цилиндр аппарата при закрытом затворе до уровня отметки на затворе.
При достижении температуры испытания с погрешностью не более 0,5ОС из рабочего цилиндра аппарата вынимают термометр и поднимают затвор. При сливе продукт не должен разбрызгиваться по стенкам мерного цилиндра.
Для удобства работы допускается в мерный цилиндр перед определением наливать 20 см3 мыльного раствора с массовой долей 1% или легкого минерального масла. При этом уровень меток истечения 25 см3 и последующих 50 см3 смещается на соответствующую величину.
В момент, когда уровень битума достигнет в мерном цилиндре метки 25 см3, включают секундомер. Когда уровень продукта достигнет метки 75 см3, секундомер останавливают и определяют время испытаний.
За условную вязкость, выраженную в секундах, принимают время истечения 50 см3 битума.
За результат испытания принимают среднее арифметическое результатов двух определений, округленное до целого числа.
Требования к точности метода приведены в таблице 4.23
Таблица 4.23
Пределы вязкости, с | Сходимость, с | Воспроизводимость, с |
До 20 включ. | ||
свыше 20 до 40 вкл. | 40% от среднего арифметического результата | |
свыше 40 | 10% от среднего арифметического результата | то же |
Метод определения количества испарившегося разжижителя из жидких битумов.
Данный метод нормирован в ГОСТ 11504 «Битумы нефтяные. Метод определения количества испарившегося разжижителя из жидких битумов», который распространяется на нефтяные жидкие битумы и устанавливает метод определения количества испарившегося разжижителя из жидких битумов при заданной температуре и времени испытания.
В ходе испытаний применяют следующие реактивы и аппаратуру:
- чашка по ГОСТ 25336;
- шкаф сушильный с терморегулятором, поддерживающим температуру с погрешностью до ±1ОС или шкаф сушильный вакуумный (вакуум-термостат) с терморегулятором, поддерживающим температуру с погрешностью до ±1ОС;
- электроплитку;
- термометр ртутный стеклянный по ГОСТ 2045, с ценой деления шкалы 1ОС;
-сито металлическое с сеткой № 07 по ГОСТ 6613;
- эксикатор по ГОСТ 25336;
- весы лабораторные по ГОСТ 24104, класса точности 3 или другие весы такого же класса точности;
- соль поваренную пищевую по ГОСТ 13830 или кальций хлористый технический по ГОСТ 450
Перед испытанием пробу битума, нагретого до 60ОС, при необходимости обезвоживают фильтрацией через слой высотой 15 - 20 мм крупнокристаллической свежепрокаленной поваренной соли или хлористого кальция.
Битум обезвоженный нагретый до подвижного состояния, процеживают через металлическое сито и перемешивают для полного удаления пузырьков воздуха.
Тщательно вымытые чашки помещают в сушильный шкаф при (105 ± 1)ОС не менее чем на 30 мин. Затем их охлаждают в эксикаторе до комнатной температуры и взвешивают с погрешностью не более 0,01 г.
Испытания проводят в двух чашках. В каждую чашку помещают битум, взвешенный с погрешностью не более 0,01 г, толщиной слоя 0,1 см.
Массу битума (m), соответствующую толщине слоя 0,1 см битума, в граммах вычисляют по формуле:
p ´ d2 ´ h ´ r 3,14 ´ d2 ´ 0,1 ´ 1
m = ---------------------- = -------------------------
4 4
где d - диаметр чашки, см;
h - толщина слоя битума, см;
r - плотность битума, г/см3 (условно принята 1).
Чашки с битумом нагревают на электрической плитке, покрытой асбестовым листом, до температуры текучести (около 40 - 60ОС) в течение 1 - 2 мин и при осторожном наклоне чашки битум распределяют равномерным слоем по ее дну.
Чашки с битумом устанавливают на горизонтальную решетку сушильного шкафа, предварительно нагретого до температуры испытания. Контрольный термометр должен находиться на высоте чашек.
Так как при установке чашек в сушильный шкаф температура в нем понижается, то время нахождения в нем чашек с битумом отсчитывают с момента достижения заданной температуры. Время достижения этой температуры после установки чашек и закрытия шкафа не должно превышать 15 мин.
Условия выдерживания чашек с битумом в сушильном шкафу приведены в таблице 4.24:
Таблица 4.24
Аппаратура | Класс битума | Время, ч | Температура, ОС |
Сушильный шкаф | СГ МГ | 100 ± 1 110 ± 1 | |
Вакуум - термостат (остаточное давление не более 4 ´ 103Па (30 мм рт. ст.)) | СГ МГ | 100 ± 1 110 ± 1 |
По истечении времени выдерживания, чашки с битумом вынимают из сушильного шкафа, устанавливают в эксикатор и после охлаждения в течение 30 мин взвешивают с погрешностью не более 0,01 г.
Количество испарившегося разжижителя (х) в процентах вычисляют по формуле:
(m - m1) ´ 100
Х = -----------------------
m
где m - масса жидкого битума до испытания, г;
m1 - масса жидкого битума после испытаний, г.
За результат испытания принимают среднее арифметическое двух параллельных определений. Допускаемые расхождения между определениями не должны превышать 1,5%.
Дата добавления: 2016-01-05; просмотров: 40; Мы поможем в написании вашей работы! |
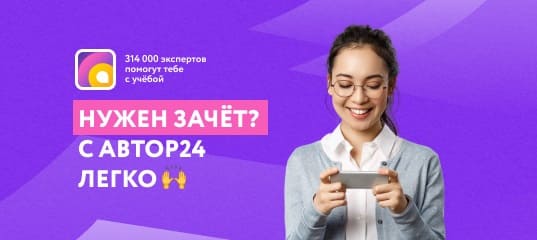
Мы поможем в написании ваших работ!