Краткие теоретические сведения.
Себестоимость продукции машиностроения в значительной степени определяется затратами на материалы. Поэтому рациональный выбор заготовки обусловлен необходимостью экономии материалов.
При выборе вида заготовки для проектируемого технического процесса предпочтение следует отдавать заготовке, характеризующейся лучшим использованием материала и меньшей стоимостью. В случае, когда в технологическом процессе могут быть использованы различные виды заготовок, рациональный тип заготовки может быть выбран только на основе технико-экономических расчетов.
Одним из фактов, обеспечивающих рациональное использование материалов при изготовлении продукции машиностроения является нормирование их расходов.
Сущность нормирования расходов материалов заключается в регламентации использования предметов труда в отраслях народного хозяйства. Нормы расхода материалов служат основной для плановых расчетов потребности в материальных ресурсах, с их помощью обеспечивается необходимое соответствие между плановым объемом выпуска продукции и материальными ресурсами, выделяемыми на ее изготовление. Без норм расхода материалов невозможна разработка сметы производственных затрат. Нормы расхода является средством контроля и учета за рациональным использованием материальных ресурсов.
Основу нормы составляет полезный расход материала на единицу продукции, равный массе готовой детали.
|
|
Второй элемент нормы включает дополнительные затраты материала на отходы и потери, обусловленные несовершенством конкретного технического процесса (угла металла при плавке, образование стружки при обработки резанием и т. д.).
В общем случае определение нормы расходы металла для изготовления отдельной детали определяется как массой отходов, возникающих в процессе разки металла на заготовки, так и отходами, возникающими в процессе их последующей обработки.
Норма расхода металла на изделие массового и крупносерийного производства определяется точным техническим расчетом с учетом потерь металла по элементам. На изделия единичного и мелкосерийного производства норма расхода, как правило, устанавливается по коэффициенту технологических потерь.
Методика расчета норма расхода металла определяется типом заготовки, выбранной для изготовления детали.
В случае выбора в качестве заготовки сортовой прокат норма расхода металла рассчитывается следующим образом.
Устанавливается длина заготовки Lз в мм для одной детали по формуле:
(16)
где - длина детали по чертежу, мм;
a- общий припуск на обработку торца;
b- ширина разреза при резке сортового проката на заготовки, мм.
|
|
Далее устанавливается величина потерь металла на зажим заготовки в патроне, которая зависит от диаметра проката, и определяется числом деталей, изготавливаемых из одного прутка сортового проката по формуле:
(17)
где - длина прутка сортового проката, мм
l – величина потерь на зажим заготовки в патроне, мм
Для дальнейших расчетов применяют целое число деталей n.
Затем определяется длина остатка прутка вследствие некратности используемой длины прутка длине заготовки для одной детали по формуле:
(18)
Норму расхода материала на изготовление одной детали Нр можно определить из условия:
(19)
где Мn.m. – масса погонного метра проката, кг.
В случае выбора в качестве заготовки поковки или штамповки норма расхода металла Нр определяется следующей формулой:
(20)
где Gn – масса поковки (штамповки) с учетом припуска на последующую механическую обработку, кг;
Gо – масса отходов в процессе штамповки и ковки, кг;
Gу – потери металла на угар при нагреве заготовок, кг;
А - отходы металла при расходе листового проката для поковки (штамповки), кг.
Нормирование расхода металла на изготовление отливок имеет свои особенности. Расчет ведется не по каждой отдельной детали, а по группам деталей. При этом основу нормирования расхода металла на изготовление отливок составляет определение массы металлической завалки шихты. Кроме массы отливки, литников и прибылей при расчете металлозавалки определяется процесс брака, угара и прочих потерь. При этом потери подразделяются на возвратные и безвозвратные.
|
|
В связи с ограниченностью учебного времени в настоящей работе норма расхода металла на изготовление отливок будет считаться укрупнено по формуле:
(21)
где Gо – масса отливки с учетом припуска на последующую механическую обработку, кг;
Кn – коэффициент безвозвратных потерь и брака литья, увеличивающих норму расхода металла.
Экономическая целесообразность использования того или иного типа заготовки обусловливается не только меньшей нормой расхода металла при ее изготовлении, но также и меньшей стоимостью изготовления.
Стоимость заготовки учитывается при расчете технологической себестоимости вариант процесса механической обработки, поэтому предпочтение следует отдавать той заготовке, которая обеспечивает меньшую технологическую себестоимость детали. Если сопоставляемые варианты технологической себестоимости оказываются равноценными, то предпочтительными следует считать вариант заготовки с меньшей нормой расхода материала.
|
|
Если деталь изготавливается из проката, то стоимость заготовки Sз определяется по массе проката, требующегося на ее изготовления, и по массе образующейся в процессе механической обработки стружки:
(22)
где 1,05 – коэффициент, учитывающий затраты на правку, калибровку, разрезку проката на штучные заготовки;
Q – масса заготовки, кг;
S - стоимость 1 т материала заготовки, руб
g- масса готовой детали, кг;
Sотх- стоимость 1 т отходов (стружки), руб.
Оптовые цены на некоторые металлы и сплавы приведены в табл. 1 приложения 2. Заготовительные цены на стружку черных и цветных металлов приведены в табл. 2 приложения 2.
Стоимость заготовок, получаемых методами литья, ковки, штамповки можно с достаточной точностью определить по формуле:
(23)
где С – базовая стоимость 1 т заготовок, руб;
КМ, Кв, Кп, Кс – коэффициенты, зависящие от марки материала, массы заготовки, объема производства, сложности изготовления.
Значения остальных параметров такие же что и в формуле (22).
Базовая стоимость 1 т заготовок, полученных тем или иным методом, приведена в табл. 3 приложения 2.
Для отливок, полученных в песчано-глинистых формах и в кокилях величины коэффициентов материала Км коэффициента массы Кв определяются соответственно из табл. 4 и 5 приложения 2, величина коэффициента объема производства Кn зависит от группы серийности и определяется из табл. 6 на основании данных табл. 7 приложения 2.
Величина коэффициента сложности изготовления Кс определяется из табл. 8 приложения 2.
Определение группы сложности отливок можно произвести по следующим признакам:
1 группа – удлиненные детали типа тел вращения (вкладыш, втулка, гильзы, трубы, цилиндры, валы и пр.) Отношение длины к диаметру у таких деталей больше 1;
2 группа – детали типа дисков (маховики, шкивы, диски корпуса подшипников и т.д.)
3 группа – простые по конфигурации коробчатые плоские детали (крышки, кронштейны, плиты, рычаги и т.д.);
4 группа – закрытые коробчатые детали корпусного типа, внутри которых монтируются механизмы машин (блоки цилиндров, корпуса коробок передач, коробки скоростей и подач и др.);
5 группа – крупные и тяжелое коробчатые детали (рамы, станины, и другие несущие конструкции).
Для отливок, полученных литья по выплавляемым моделям величины коэффициентов материала Км и массы Кв определяются соответственно из табл. 4 и 9 приложения 2. Величина коэффициента объема производства Кn определяется независимо от марки материала отливки в зависимости от серийности производства. Группа серийности, на основании которой выбирается значение коэффициента Кn, приведена в табл. 7 приложения 2.
Значение коэффициента Кn в зависимости от группы серийности составляет:
1 группа – Кn=0,83
2 группа – Кn=1.00
3 группа – Кn=1,23
Величина коэффициента сложности изготовления Кс определяется из табл. 10 приложения 2.
Для отливок, полученных литьем под давлением величины коэффициентов материала Км массы Кв. объема производства Кп, сложности изготовления Кс определяются соответственно из табл. 4, 11, 12, 13.
Для горячештампованных заготовок величины коэффициентов материала Км, массы Кв, определяется из следующего условия: если годовая программа больше значений, указанных в табл. 9, то принимается Кn=1,00.
Таблица 9
Масса Штамповки, кг | ![]() | 0,25…0,63 | 0,63…1,6 | 1,6…2,5 | 2,5…4 | 4…10 | 10…25 |
Объем Производства, тыс. шт. | 15-500 | 8-300 | 5-150 | 4,5-120 | 4-100 | 3,75-75 | 3-50 |
Величина коэффициента Кс определяется из табл. 16 приложения 2.
Экономический эффект для сопоставления способов получения заготовок, при которых технологический процесс механической обработки не меняется, рассчитывается по формуле:
(24)
где - стоимость сопоставляемых заготовок, руб.;
N- годовая программа, шт.
В случае незначительной экономии при использовании заготовки, полученной специальными методами, рекомендуется применение заготовок из проката.
Дата добавления: 2016-01-04; просмотров: 12; Мы поможем в написании вашей работы! |
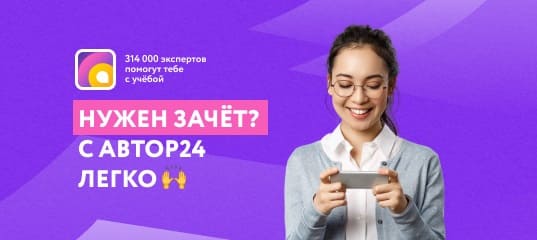
Мы поможем в написании ваших работ!