Технология и техника сварки покрытыми электродами
План
1. ПОДГОТОВКА МЕТАЛЛА ПОД СВАРКУ
2. РЕЖИМ СВАРКИ
ПОДГОТОВКА МЕТАЛЛА ПОД СВАРКУ
Подготовка металла под сварку заключается в правке, разметке, резке, обработке кромок, гибке и очистке металла, а также сборке деталей.
Правка производится для устранения деформаций прокатных материалов. Листовой и сортовой металл правят в холодном состоянии на листоправильных вальцах и прессах. Сильно деформированный металл правят в горячем состоянии.
Разметка - нанесение размеров детали на металл. Она может быть выполнена индивидуально, по шаблонам, а также оптическим и машинным методами. Индивидуальная разметка — очень трудоемкий процесс. Шаблоны обычно изготавливают из алюминиевого листа. Для разметки используют линейку, угольник, рулетку.
Оптическим называют метод разметки по чертежу, проецируемому на размечаемую поверхность металла. Разметочно-маркировочные машины выполняют разметку со скоростью до 8-10 м/мин при погрешности ± 1 мм.
Резка металла бывает механической и термической. Механическая резка выполняется на различном механическом оборудовании: ножницах, отрезных станках и прессах. Термическая разделительная резка металла менее производительна, чем резка на ножницах, но более универсальна и применяется для получения заготовок разных толщин как прямолинейного, так и криволинейного профиля.
Обработка кромок производится для улучшения условий сварки. Кромки подготавливают термическим и механическим способами. Кромки с односторонним или двухсторонним скосом можно получить, используя одновременно два или три резака, расположенных под соответствующими углами. Механическая обработка кромок на станках выполняется для обеспечения требуемой точности сборки, образования фасок, имеющих заданное очертание, в случаях, когда по техническим условиям необходимо удаление металла с поверхности кромок после резки.
|
|
Форма разделки кромок характеризуется углом их скоса, размером притупления и зазором между свариваемыми кромками. Она зависит от типа сварного соединение, толщины свариваемых элементов и применяемого способа сварки.
При толщине свариваемых элементов до 6 мм скоса кромок не требуется. В элементах толщиной 5-30 мм и более применяют V-образную разделку с суммарным углом скоса 60-80°. Притупление при этом составляет 2-8 мм. Если толщина свариваемых элементов 20 мм и более, в стыковых соединениях применяют криволинейный скос кромок (U-образную разделку).
Свариваемые кромки устанавливаются с зазором 2-4 мм (в зависимости от толщины свариваемых элементов). Сварные соединения ответственного назначения с V-образной разделкой свариваются с двух сторон (с подваркой).
|
|
Элементы толщиной более 12 мм сваривают встык с двух сторон, применяя Х-образную разделку. Соединения такого типа сваривают только в тех случаях, когда имеется доступ с обеих сторон. Х-образную разделку используют, например, в стыковых сварных соединениях сосудов высокого давления, толщина свариваемых элементов которых 50-100 мм и более.
Соединения с плоскими наклонными кромками (V-образная разделка) трудно провариваются в вершине и имеют большую ширину на наружной поверхности. Соединения с U-образной разделкой свободны от этих недостатков. Недостаток соединений с V- и U-образными разделками заключается в том, что при одинаковой толщине свариваемых элементов для их заполнения требуется больше электродов, чем для заполнения Х-образной разделки. Объем наплавленного металла вV-образном шве примерно в два раза больше, чем в Х-образном. Следовательно, соединения с Х-образной разделкой более экономичны, чем соединения с V-образной разделкой.
Гибка металла производится на листогибочных вальцах для изготовления цилиндрических и конических поверхностей. Чтобы получить заготовки с поверхностью сложной формы, широко используется холодная штамповка из листового материала толщиной до 10 мм.
|
|
Очистка металла под сварку- это удаление с его поверхности загрязнений, смазочно-охлаждающих жидкостей, ржавчины, окалины, заусенцев и шлака. Для очистки проката, деталей и заготовок используют механические и химические методы.
К механическим методам относятся зачистка металлическими щетками, иглофрезами, шлифовальными кругами и лентами.
Химическими методами очистки обезжиривают и травят поверхности свариваемых деталей. Различают ванный и струйный методы. В первом случае детали опускают в ванны с различными растворами и выдерживают их там определенное время. Во втором случае поверхность деталей обрабатывается струями раствора, в результате чего происходит непрерывный процесс очистки. Химические методы достаточно эффективны, однако в производстве сварных конструкций используются главным образом для очистки цветных металлов.
Сборка деталей под сварку выполняется с целью установления взаимного пространственного положения элементов сварной конструкции. Для уменьшения времени сборки, а также повышения ее точности применяют различные приспособления: установочные детали, прижимные механизмы, стенды, и др.
|
|
Сварные узлы и конструкции часто собирают в сборочно-сварочных приспособлениях с помощью сварочных прихваток, т. е. коротких сварных швов (15-50 мм в зависимости от толщины свариваемых элементов и длины шва). Для фиксации подлежащих сварке деталей сечение прихваток должно составлять примерно 1/3 сечения основного шва. Расстояние между прихватками - обычно от 100 мм до 1 м.
РЕЖИМ СВАРКИ
Под режимом сварки понимают совокупность основных контролируемых параметров, определяющих условия сварки. К параметрам режима ручной дуговой сварки плавящимся электродом относят диаметр электрода, сварочный ток, напряжение дуги, скорость сварки, род и полярность тока, покрытие электрода, положение электрода и положение изделия при сварке.
Среди перечисленных показателей только некоторые влияют на процесс сварки. К ним относятся диаметр электрода и сварочный ток. Скорость сварки и напряжение дуги при ручной сварке, как правило, не регламентируются. Эти характеристики устанавливает сам сварщик. Они зависят от вида сварного соединения, свариваемой стали, марки электрода, положения сварного шва в пространстве и др.
Вначале определяют диаметр электрода, в зависимости от которого назначают силу сварочного тока. Диаметр электрода зависит от толщины свариваемых элементов, типа сварного соединения в пространстве, марки (состава) свариваемого металла. Тип и марка электрода зависят от требуемой прочности сварного соединения, а род и полярность тока - от марки и толщины свариваемого металла.
Диаметр электрода и толщина свариваемого изделия находятся примерно в следующих соотношениях:
Толщина свариваемых листов, мм 1-2 3 4-5 6-12 13 и более
Диаметр электрода. мм 1,5-2,5 3 3-4 4-5 5 и более
Сила сварочного тока зависит не только от диаметра электрода Оптимальное его значение обусловлено скоростью перемещения электрода.
Если толщина свариваемых элементов s меньше 1,5dэ . сила сварочного тока Iсв уменьшают по сравнению с расчётной на 10-15%; если s >3 dэ, силу сварочного тока увеличивают сравнению с расчетной на 10 - 15%.
При сварке элементов разной толщины диаметр электрода и силу сварочного тока подбирают в соответствии с нижними параметрами режима сварки, которые рекомендуются для элементов сварного соединения большой толщины.
При сварке вертикальных швов силу сварочного уменьшают на 10-15%, а при сварке потолочных швов на 15-20% по сравнению с силой сварочного тока, выбранной для сварки в нижнем положении.
Оптимальную силу сварочного тока корректируют и устанавливают практическим путем. Она зависит от диаметра электрода, а также от длины его рабочей части, состава покрытия, положения, в котором выполняется сварка. Чем и больше сила сварочного тока, тем выше производительность. Однако при чрезмерной для данного диаметра электрода силе сварочного тока электрод быстро нагревается выше допустимого предела, что приводит к снижению качества шва и повышенному разбрызгиванию металла. При недостаточной силе сварочного тока дуга горит неустойчиво, часто обрывается, в шве могут быть непровары.
Силу сварочного тока при сварке конструкционных сталей можно определить по следующим формулам: для электродов диаметром 3-6 мм Iд = (20 + 6dэ) dэ;для электродов диаметром менее3 мм Iд= 30 dэ,где dэ -диаметр электрода, мм.
Сила сварочного тока при ручной дуговой сварке может изменяться в достаточно широких пределах: от 50 до 350 А.
При сварке на малыхсварочных токах у неопытных сварщиков может наблюдаться примерзание электрода — непреднамеренное приваривание электрода к изделию. В таких случаях сварщику нужно потренироваться в умении зажигать и поддерживать сварочную дугу.
Диаметр электрода выбирают в зависимости от толщины свариваемого металла, положения, в котором выполняется сварка, а также от вида соединения и формы подготовленных кромок под сварку. При сварке встык листов стали толщиной до 4 мм в нижнем положении диаметр электрода обычно берется равным толщине свариваемого металла. При сварке стали большей толщины используют электроды диаметром 4-6мм при условии обеспечения полного провара соединяемых деталей и правильного формирования шва. Применение электродов диаметром более 6 мм ограничено возможным непроваром в корне шва, а также большей массой электрода и электрододержателя.
При выполнении многослойных швов дня лучшего провара корня шва рекомендуется сварку первого слоя производить электродами малого диаметра. Это относится как к стыковым, так и к угловым швам.
Изменение скорости сварки влияет на глубину провара и ширину шва. При увеличении скорости сварки уменьшаются глубина провара и ширина шва, и, наоборот, уменьшение скорости сварки вызывает увеличение глубины провара и ширины шва.
Увеличение длины дуги повышает напряжение дуги и снижает силу сварочного тока. В результате уменьшается глубина провара и увеличивается ширина шва.
Положение электрода при сварке характеризуется углом его наклона к оси сварного шва. При наклонном положении электрода хорошо оттесняются расплавленный металл ванны и шлак из кратера, при этом также увеличивается глубина провара. Для получения сварного шва хорошего качества при сварке в нижнем положении угол наклона электрода по отношению к вертикали должен составлять 15° в направлении сварки.
Электрод должен быть наклонен независимо от направления сварки (слева направо, справа налево, от себя, к себе). Только при соблюдении правильного наклона электрода свариваемое изделие проплавляется на наибольшую глубину.
Дата добавления: 2016-01-04; просмотров: 15; Мы поможем в написании вашей работы! |
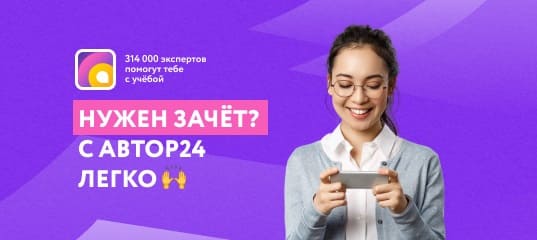
Мы поможем в написании ваших работ!