Расчет режимов сварки (наплавки) в углекислом газе проволокой сплошного сечения
В основу выбора диаметра электродной проволоки при сварке и наплавке в углекислом газе положены те же принципы, что и при выборе диаметра электрода при ручной дуговой сварке:
Расчет сварочного тока, А, при сварке проволокой сплошного сечения производится по формуле:
где а – плотность тока в электродной проволоке, А/мм 2 (при сварке в СО2 а=110 ÷ 130 А/мм 2 ; dЭ – диаметр электродной проволоки, мм.
Механизированные способы сварки позволяют применять значительно большие плотности тока по сравнению с ручной сваркой. Это объясняется меньшей длиной вылета электрода.
Напряжение дуги и расход углекислого газа выбираются в зависимости от силы сварочного тока по табл. 6.1.
Зависимость напряжения и расхода углекислого газа от силы сварочного тока
При сварочном токе 200 ÷ 250 А длина дуги должна быть в пределах 1,5 ÷ 4,0 мм. Вылет электродной проволоки составляет 8 ÷ 15 мм (уменьшается с повышением сварочного тока).
Реклама
Скорость подачи электродной проволоки, м/ч, расчитывается по формуле:
где αР – коэффициент расплавления проволоки, г/А ч ; ρ – плотность металла электродной проволоки, г/см 3 (для стали ρ =7,8 г/см 3 ).
Значение αР рассчитывается по формуле:
Скорость сварки (наплавки), м/ч, рассчитывается по формуле:
где αН — коэффициент наплавки, г/А ч; αН = αР(1-Ψ), где Ψ — коэффициент потерь металла на угар и разбрызгивание. При сварке в СО2 Ψ = 0,1- 0.15;FB — площадь поперечного сечения одного валика, см 2 . При наплавке в СО2 принимается равным 0,3 — 0,7 см 2 .
|
|
Масса наплавленного металла, г, сварке рассчитывается по следующим формулам:
при наплавочных работах:
где l – длина шва, см; ρ – плотность наплавленного металла (для стали ρ=7,8 г/см 3 ); VН — объем наплавленного металла, см 3 .
Время горения дуги, ч, определяется по формуле:
Полное время сварки (наплавки), ч, определяется по формуле:
где kП – коэффициент использования сварочного поста, ( kП= 0,6 ÷ 0,57).
Расход электродной проволоки, г, рассчитывается по формуле:
где GH – масса наплавленного металла, г; Ψ – коэффициент потерь, (Ψ = 0,1 — 0,15).
Расход электроэнергии, кВт ч, определяется по формуле:
где UД– напряжение дуги, В; η– КПД источника питания: при постоянном токе 0,6÷0,7 , при переменном ,8÷ 0,9; WO–мощность источника питания, работающего на холостом ходе, кВт. На постоянном токе Wо = 2,0÷ 3,0 кВт, на переменном – Wо= 0,2÷ 0,4 кВт.
Режим сварки в СО2 подбирают на основании обобщенных опытных данных, приведенных в табл. 41.
Таблица 41
Режимы сварки в среде СО некоторых видов соединений
Перед началом сварки необходимо отрегулировать расход газа и выждать 20–30 с до полного удаления воздуха из шлангов. Перед зажиганием дуги необходимо следить, чтобы вылет электрода из мундштука не превышал 20–25 мм. Движение горелки должно осуществляться без задержки дуги на сварочной ванне, так как эта задержка вызывает усиленное разбрызгивание металла. Сварка в нижнем положении производится с наклоном горелки под углом 5–15° вперед или назад. Предпочтительнее вести сварку углом назад, так как при этом обеспечивается более надежная защита сварочной ванны. При механизированной сварке металла малой толщины 1–2 мм поперечных колебательных движений не производят. Сварку ведут на максимальной длине дуги, с максимальной скоростью. При достаточной газовой защите избегают прожогов и обеспечивают нормальное формирование шва. Горелку ведут углом назад, при этом угол наклона составляет 30–45°.
|
|
Стыковые соединения при толщине металла 1,5–3 мм сваривают на весу. Более тонкий металл сваривают в вертикальном положении на спуск (сверху вниз), провар достигается за один проход. Сварку соединений внахлестку при толщине металла 0,8–2,0 мм чаще производят на весу и реже – на медной подкладке. При качественной сборке нахлесточных соединений представляется возможным значительно увеличить скорость сварки. Колебательные движения горелкой при сварке больших толщин те же, что и при ручной сварке. При сварке с перекрытием для уменьшения пор применяются продольные колебания горелки вдоль оси шва, что обеспечивает более полное удаление водорода из сварочной ванны.
|
|
Сварка в среде СО2 является высокопроизводительным процессом. В массовом и крупносерийном производстве работают слесари– сборщики, которые освобождают сварщика от сборочных операций. Сварочный пост в этом случае оборудуется кроме сварочной аппаратуры специальными приспособлениями для обеспечения высокой производительности сварочных работ при гарантированном качестве сварных узлов. На рис. 83 показан сварочный пост на одного сварщика и одного слесаря‑сборщика.
Требования к качеству сборки и подготовки деталей под сварку в СО2сварочной проволокой (0,8–2,5 мм) должны соответствовать существующим нормативным документам.
Рис. 83. Сварочный пост для оборонно‑сварочных работ (сварщик, слесарь‑сборщик):
1 – складочное место для заготовок; 2, 7 – сборочно‑сварочные приспособления; 3 – ширма с встроенной вентиляцией; 4 – полуавтомат с консолью; 5 – кран консольно‑поворотный; 6 – стул поворотный; 8 – стол двухпозиционный поворотный
|
|
Дата добавления: 2022-06-11; просмотров: 78; Мы поможем в написании вашей работы! |
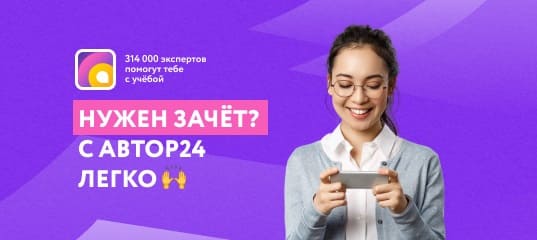
Мы поможем в написании ваших работ!