Производство основных видов проката.
Процесс прокатного производства начинается с получения на заготовительных станах полупродуктов: блюмов, слябов, заготовок и сутунок.
Полупродукты можно также получать и на машинах непрерывного литья заготовок.
Схема изготовления проката
Блюмы представляют собой стальной полуфабрикат квадратного сечения, который применяется для производства сортового проката.
![]() |
Блюм имеет сечение 150х150мм - 450х450мм
Длина блюмов 6 - 10м.
Исходная заготовка - слиток весом до 10 тонн
Внешний вид блюмов
Последовательность прокатки полосы, прутка, двутавровой балки и рельсов из блюма
Слябы представляют собой стальной полуфабрикат прямоугольной формы, который применяется для производства листов.
Сляб имеет сечение 50 – 300мм х 500 – 2800мм
длина 1,3-5 м.
Исходная заготовка – слиток весом до 25 тонн
Внешний вид слябов
Прокатку блюмов и слябов производят на обжимных одноклетьевых дуо-реверсивных станах - блюмингах и слябингах. Перед прокаткой слитки нагревают до 1260-1300°С. Если слитки поступают на нагрев в холодном состоянии, то продолжительность нагрева составляет 12-16 часов. Более эффективный, с точки зрения энергосбережения, горячий посад, то есть слитки загружают в печь горячими, не успевшими остыть после разливки (температура 400-1000°С). Их время нагрева в этом случае составляет 4-8 ч.
|
|
Из блюмов получают полупродукты меньших размеров: заготовки – квадратного сечения и сутунку – прямоугольного сечения.
![]() |
Заготовка 50х50мм - 150х150мм
Сутунка 6 – 50мм х 150 -500мм
Далее полупродукты идут на изготовления различного вида проката.
Производство сортового проката
Справка: По размеру профиля сортовой прокат делится на:
· крупный — круглая сталь диаметром 80-250 мм, квадратная сталь со стороной 70-200 мм, периодические арматурные профили № 70-80, угловая сталь с шириной полок 90-250 мм, швеллеры и двутавровые балки обычные и облегченные высотой 360—600 мм, специальные широкополочные двутавры и колонные профили высотой до 1000 мм, шестигранная сталь до № 100, рельсы железнодорожные с массой 1 м длины 43-75 кг, полосовая сталь шириной до 250 мм и др.;
· средний — круглые диаметра 32-75 мм, квадратные со стороной 32-65 мм и шестигранные до № 70, стальной периодический арматурный профиль № 32-60, двутавровые балки высотой до 300 мм, швеллеры высотой от 100—300 мм, рельсы узкой колеи Р18-Р24, штрипсы сечением до 8x145 мм, разнообразные фасонные профили отраслевого назначения и др;
|
|
· мелкий — круглая сталь диаметром 10-30 мм, квадратная сталь со стороной 8-10 мм, периодический арматурный профиль № 6-28, угловая сталь с шириной полок 20-50 мм, швеллеры № 5-8, полосовая сталь шириной до 60 мм, шестигранная сталь до № 30 и разнообразные фасонные профили отраслевого назначения эквивалентных размеров.
Производство бесшовных труб.
I этап – получение толстостенной гильзы (диаметром 60-650мм и толщиной стенки 10-100мм)
Прошивка слитка осуществляется в горячем состоянии на стане поперечно-винтовой прокатки, двумя конусообразными рабочими валками, оси которых скрещиваются под углом 6-12°.
Схема прошивки слитка.
Благодаря косому расположению валков заготовка при прокатке получает одновременно вращательное и поступательное движение. Вследствие этого, каждая точка деформируемой части заготовки совершает винтовое движение. При этом в заготовке возникают радиальные растягивающие напряжения, вызывающие течение металла от ее центра к периферии. В результате металл в центре заготовки 4 доводится до состояния разрыхления, и заготовка сравнительно легко прошивается прошивнем 3 с образованием трубной заготовки – толстостенной гильзы.
|
|
II этап - раскатка толстостенной гильзы на тонкостенную трубу на автоматическом стане
Прокатку производят на неподвижной оправке в круглых калибрах. Толщина стенки трубы зависит от просвета между калибром и оправкой. Прокатку выполняют за два прохода с поворотом трубы на 90° после первого прохода.
Схема раскатки гильзы на автоматическом стане
III этап – отделка и калибровка тонкостенной трубы.
При небольшой степени деформации получают более точные размеры и заданное качество поверхности.
Производство сварных труб
Сварные трубы получают из полосы (штрипса) или листов, ширина которых равна длине окружности трубы.
Изготовление трубы из листа с продольным швом
1 вариант - листы свертываются в холодном состоянии в трубу на трехвалковых вальцах
I, II, III — этапы процесса гибки; 1 — валки; 2 — трубная заготовка;
2 – вариант - штамповка заготовки электросварных труб на прессах
|
|
а — заготовка; б — предварительное формование; в — окончательное формование; 1 — штампы; 2 — трубная заготовка
3 вариант - иготовление трубы из полосы с продольным швом
Продольный стык трубы соединяется с помощью сварки. Способы сварки: контактная стыковая, высокочастотная, дуговая сварка под флюсом и дуговая сварка в углекислом газе.
Схема дуговой сварки стальных труб под флюсом
1 — заготовка; 2 — электроды; 3 — флюс; 4 — шлаковая корка; 5 — шов; б — медная пластина; 7—откос флюса; 8 — бункер подачи флюс
Схема сварки трубных заготовок током высокой частоты
а — контактным; б — индукционным; 1 — заготовка; 2 — контакты; 3 — точка схождения кромок; 4 — сварочные валки; 5 — индукционная катушка
При высокочастотном нагреве в поверхностных слоях можно получить высокие плотности тока и тем самым обеспечить быстрый нагрев металла. Токоподводящие контакты, скользящие или вращающиеся, подводят ток высокой частоты к кромкам сформированной трубной заготовки. Вследствие поверхностного эффекта и эффекта близости ток сосредоточивается на поверхностях сходящихся кромок. Трубная заготовка с разогретыми до необходимой температуры кромками поступает в обжимные валки, где и происходит сварка.
Изготовление труб из полосы (штрипса) на многовалковых вальцах.
1 — валки; 2 — трубная заготовка; А — точка сварки; Dт — диаметр трубы; B — ширина стальной полосы
Сварка труб со спиральным швом имеет то преимущество, что позволяет получать из полосы одной ширины трубы различного диаметра. Трубы, изготовленные этим способом, имеют большую жесткость вследствие наличия сварного шва, расположенного по спирали. Подаваемую полосу в рулонах устанавливают в разматыватель, после которого подвергают правке на правильной машине. Для обеспечения надежной, плотной и точной сварки концов полосы встык после правильной машины осуществляют обрезку концов полосы. Далее полосы сваривают между собой, и таким образом получают полосу бесконечной длины.
Стан для дуговой сварки под слоем флюса труб со спиральным швом
1 – разматывание полосы; 2 – правка полосы; 3 – обрезка концов; 4 – сварка концов полосы встык; 5 – петлеобразователь (накопитель); 6 – образка кромок полосы; 7 – очистка кромок дробью; 8 – снятие фасок резцами; 9 – правящие ролики; 10 - формовка полосы по спирали; 11 – наружная и внутренняя сварка; 12 – резка трубы на мерные длины
На технологической линии имеется накопитель (аккумулятор) полосы, что необходимо для компенсации длины при сварке концов полосы встык. Далее осуществляют обрезку кромок полосы, очистку их поверхности чугунной дробью. За этим производят снятие фасок резцами, т. е. выполняют такую же форму скоса, как и для сварных труб с прямым швом: скос кромок под углом 35°, снизу сохраняется притупление 1 — 2 мм. После этого полосу подвергают правке и подают к формовочному стану, где осуществляют формовку трубы по спирали. Сформированную трубу далее подвергают сварке по наружному и внутреннему швам. Данный способ производства труб позволяет получать трубы бесконечной длины. После сварки трубы разрезают на мерные длины и выполняют все остальные технологические операции по отделке и испытаниям.
ВОЛОЧЕНИЕ – вид обработки давлением, заключающийся в протягивании заготовки через отверстие в инструменте, называемым волоком или фильерой.
Протягивание осуществляется под действием силы, которая деформирует металл и преодолевает силу трения между заготовкой и инструментом.
А б
Схема волочения профиля сплошного сечения «а» и пустотелого «б)
1 –инструмент (волок); 2 – получаемый профиль; 3 – исходная заготовка; 4 - оправка
При волочение площадь поперечного сечения уменьшается, а длина увеличивается. Формоизменение при волочении характеризуется коэффициентом вытяжки μ.
μ = Fo / F к
Fo – площадь поперечного сечения заготовки;
F к - площадь поперечного сечения получаемого профиля
Производительность процесса определяется силой Р, которая увеличивается с увеличением μ и сил трения.
Технологические требования:
- Усилие волочения Р ограничивается прочностью готового профиля Р < σтх F к
- Коэффициент вытяжки должен иметь оптимальные значения - на первом и последнем проходах μ = 1,2, а на промежуточных μ = 1,4
Продукция волочения:
- профили сплошного сечения: проволока диаметром от несколько микрон;
- калиброванные прутки диаметром до 150мм;
Виды поперечного сечения
- пустотелые профили. Пустотелые профили получают путем волочения пустотелой заготовки на оправке.
Виды поперечного сечения
Материал заготовок: углеродистые и легированные стали, цветные металлы и сплавы
Инструмент – волок, изготавливается из высокопрочного материала: инструментальная сталь; твердый сплав ВК3, ВК6; искусственные и природные алмазы (отверстия получают лазером, электроэррозионной обработкой)
Оборудование.
Для волочения используют волочильные станы:
- волочильный стал цепного типа. На данных станах изготавливают прутки, трубы длиной до 50 метров.
Схема цепного волочильного стана
1– заготовка, 2 – волока, 3 – клещи, 4 – волочильная каретка, 5 – крюк, 6 – цепь,
7 – ведущая звездочка, 8 – станина, 9 – электродвигатель
- барабанные волочильные станы
Схема барабанного волочильного стана
1– не приводной барабан, 2 – волока, 3 – приводной барабан, 4 – зубчатая передача.
Технологические особенности волочения.
Волочение осуществляется в условиях холодной пластической деформации и как результат – высокая точность готового изделия и хорошее качество поверхности (точность ±0,01 при диаметре 1,0 мм). Данное обстоятельство позволяет исключить в большинстве случаев последующую механическую обработку, за исключением разрезки на мерные длины.
Исходная заготовка – продукция проката.
Последовательность операций: отжиг (увеличение пластичности) – удаление окалины
(травление – промывка – сушка) – один конец заготовки заостряется и просовывается в отверстие волока – нанесение смазки для уменьшения сил трения (мыльный порошок, растительное и минеральное масло, воск или парафин) - волочение.
ПРЕССОВАНИЕ – вид обработки давлением, при котором заготовка 2 выдавливается под действием пуансона 4 из замкнутого пространства (контейнера) 1 через отверстие в инструменте – матрице 3.
При прессовании получаем профиль 5, вид поперечного сечения которого соответствует форме отверстия в инструменте.
Схема прямого «а» и обратного «б» способа прессования
При прямом способе прессования направление движения металла и пуансона совпадают. При обратном - металл выдавливается в матрицу, установленную на пуансоне.
При обратном способе прессования усилие на 25-30% меньше, чем при прямом. Объясняется это тем, что при прямом способе перемещается вся заготовка и приходится преодолевать силы трения между заготовкой и контейнером, тогда как при обратном способе заготовка неподвижна и силы трения возникают только на поверхности матрицы.
При прессовании невозможно выдавить из контейнера весь металл заготовки. В связи с этим всегда имеется отход в виде прессостатка, толщиной 30% от диаметра заготовки.
Пустотелые профили, в частности трубы, получают прямым способом с помощью пуансона 1 с иглой 4.
Схема прессования пустотелого профиля
Заготовка 2 в этом случае сначала прошивается иглой 4, а затем выдавливается из контейнера в зазор между матрицей 3 и иглой.
Продукция прессования – сложные профили со многими отверстиями и ребрами:
- профили сплошного сечения диаметром до 250мм
- пустотелые, диаметром до 400мм
Материал заготовок: цветные металлы и сплавы, легированные и инструментальные сплавы, малопластичные труднодеформируемые сплавы на основе никеля и титана. Возможность деформирования малопластичных металлов при прессовании объясняется тем, что металл в контейнере находится в состоянии всестороннего неравномерного сжатия – увеличение фактической пластичности металла.
Инструмент – матрица, контейнер, игла и пуансон. Наиболее нагруженные – матрица и игла. Они изготавливаются из жаропрочных сплавов, причем для увеличения работоспособности изготавливаются со специальными отверстиями для охлаждения водой.
Оборудование – гидравлический пресс как вертикального, так и горизонтального исполнения. Вертикальный пресс используется при производстве профилей небольшой длины, горизонтальный – для изготовления профилей длиной до 25 метров.
Технологические особенности прессования
Прессование осуществляется в условиях горячей пластической деформации.
Исходная заготовка либо слиток, либо продукция проката в виде прутков мерной длины.
Последовательность операций: зачистка поверхности от раковин и трещин – нагрев заготовки (в электропечах) – удаление окалины (пневмосбив – воздействие воздуха при давлении 6 атм в течение 0,1 сек – температура не изменяется) – нанесение графитовой смазки (или стеклянный порошок) на поверхность заготовки и инструмента (для уменьшения сил трения в контейнере и матрице, а также для увеличения стойкости инструмента и повышения качества поверхности профиля) – прессование – термообработка – разрезка на мерные длины.
Дата добавления: 2022-06-11; просмотров: 154; Мы поможем в написании вашей работы! |
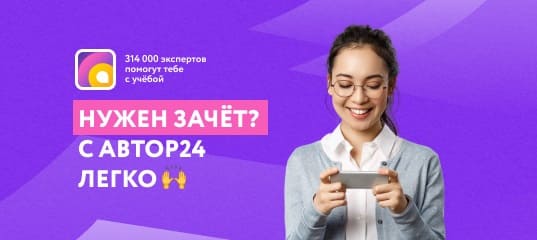
Мы поможем в написании ваших работ!